Восстановление железных руд
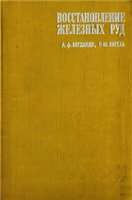
Людвиг фон Богданди, Ганс-Юрген Энгель
Металлургия, 1971 г.
4.1.1. СЫРЫЕ МАТЕРИАЛЫ
4.1.1.1. Руды
Так как в настоящее время имеется много хороших работ (например. [343]), посвященных запасам и свойствам железных руд, подробное изложение этих сведений здесь было бы излишним.
4.1.1.2. Топливо
Рис. 145 дает представление о свойствах твердого топлива. С ростом степени персугливания, т. с. при движении по ряду топлив от дров до кокса, содержание летучих в твердом топливе и его реакционная способность падают. Приведенные значения относятся к безводному и беззольному топливу; в каждом конкретном случае, смотря по необходимости, содержание воды и золы в топливе должно приниматься во внимание. Более подробные сведения читатель может найти в работе [344].
В табл. 26 приведена характеристика наиболее употребительных сортов топливной нефти; в табл. 27 — характеристика различных газов, получаемых из твердого топлива.
В табл. 28 показано несколько анализов природного газа. Содержание отдельных компонентов в природном газе, вообще
4.5.6.2. Производство жидкого чугуна
Б определенных условиях возможно путем повышения температур у разгрузочного конца печи получить при восстановлении руды расплав (способ Бассе и штюрцельбергский способ) [417]. Производительность в этом случае падает, так как в той же печи необходимо провести дополнительные процессы.
Высоких производительностей можно добиться здесь, повышая рабочую температуру во всем объеме шихты почти до 1300° С, как это делается по Stora-способу [421] (рис. 213) и подобным ему методам [433]. Железо получается тогда непосредственно в жидком виде. Возможно довести производительность до 10,8 т чугуна/сутки при очень маленьком объеме шихты в печи.
Если отнести производительность печи к объему твердой шихты, плавающей на поверхности чугуна, возможно достижение удельной производительности до 40 г чугуна/ (м3 объема шихты •сутки) [430], что хорошо согласуется с теорией (см. рис. 200) К
Слабая сторона процессов во вращающихся печах — плохая, в сравнении с шахтными печами, теплопередача — видна здесь, конечно, особенно отчетливо. Отходящий газ покидает печь с температурой по меньшей мере 1500° С; это вынуждает
4.5.6.3. Производство крицы
Между обоими разобранными вариантами стоит производство крицы (крично-рудный способ Круппа) [409, 422, 423]. Рабочая температура шихты у разгрузочного конца печи повышается здесь почти до 1200° С. Металлическое железо коагулирует в крицы и может быть затем легко отделено от пустой породы с помощью магнитной сепарации. Относительно хода процессов-в печи здесь нельзя высказать каких-либо новых точек зрения. Процесс применяется почти исключительно для переработки очень бедных руд с кислой пустой породой (СаО : SiO2 <_2). Из-за большого количества балластной пустой породы процесс теплопередачи играет в этом случае решающую роль [408].
4.5.6.4. Предварительное восстановление
При неполном восстановлении производительность вращающейся печи может возрастать и, кроме того, такая печь разгружает установленный следом плавильный агрегат. Расход топлива во вращающейся печи в расчете на металлическое железо в этом случае не всегда снижается (рис. 215). Для экономии электроэнергии применяют вращающиеся печи предварительного восстановления преимущественно в паре с электровосстановительным и плавильным агрегатом (рис. 216), например с низкошахтной электропечью [424, 428], (рис. 217) (Стратиджик Юди, Оркарб, Электрокемиск-способ и др.).
В связи с процессами электровосстановления эти производственные комбинации будут рассмотрены нами далее (раздел 4.7).
4.6. ВОССТАНОВЛЕНИЕ В ШАХТНЫХ ПЕЧАХ (БЕЗ ПЛАВЛЕНИЯ)
4.6.1. ОБЛАСТЬ ПРИМЕНЕНИЯ
Большие количества восстановительного газа, а также работа по принципу противотока руды и газа дают возможность получить в шахтных печах высокую производительность в расчете на единицу объема при одновременном хорошем использовании восстановительного газа как с термической, так и с химической точек зрения. Впечатляющий пример дает в этом отношении доменная печь, которая служит не только для нагрева и восстановления руды. Наличие кокса в шихте делает возможным проведение двух других важнейших процессов:
4.6.3. ПРОМЫШЛЕННАЯ РЕАЛИЗАЦИЯ ПРИНЦИПА ВОССТАНОВЛЕНИЯ В ПРОТИВОТОКЕ В ШАХТНЫХ ПЕЧАХ
Рис. 227 и 228 показывают примеры реализации этого принципа в шахтных печах в промышленном и полупромышленном масштабе. Согласно процессу Виберга (рис. 228), за счет электроэнергии осуществляется газификация кокса водяным паром и СО2 с получением восстановительного газа, состоящего преимущественно из СО. После обсссеривания газа в башне с доломитом при приблизительно 950° С он вводится в шахту, где восстанавливает руду в режиме противотока. В верхней части шахты имеет место предварительное восстановление до FeO и предварительный нагрев шихты до ~900° С путем сжигания части газа в специально вдуваемой для этой цели в верхнюю часть шахты струе воздуха. Характерная особенность процесса усматривается в том, что главная зона восстановления (FeO-*-Fe) работает приблизительно в изотермических условиях, достигающихся с помощью предварительного подогрева шихты и поддержанием отношения СО: Нг в составе восстановительного газа равным 3: 1, при котором процесс идет почти без затраты тепла, так как постановление с помощью СО слабо экзотермично, с помощью Н2— сильно эндотермично. Восстановление в шахтных печах итальянского металлургического концерна Финсидер проводят при таком же составе восстановительного газа.
По способу Виберга значительная часть (60—75.%) печных газов отсасывается специальным вентилятором из главной зоны восстановления назад в газогенератор, где происходит регенерация газа по схеме:
Н2О + С = СО + Н2, СО2 + С = 2СО.
Напор, создаваемый этим вентилятором, определяет общий расход газа во всей установке, а потому определяет и ее производительность. Из-за тяжелых условий работы (высокое содержание пыли в газе, температура газа около 900° С) достижимый на практике напор такого вентилятора относительно невелик.
Полное и точное предварительное определение производственных показателей доменной плавки сейчас еще невозможно.
Господствующий еще сегодня термодинамический подход к проблеме в состоянии лишь объяснить уже имеющиеся производственные показатели и проверить правильность и полноту результатов опытов.
Предварительное вычисление скорости реакций, производительности печей и удельного расхода кокса на базе материальных и тепловых балансов плавки, т. е. с помощью одной термодинамики, невозможно.
Кинетические исследования скоростей реакций, протекающих в доменной печи, проводятся в больших масштабах начиная с 1950 г. (см. раздел 2) как в лабораториях, так и на доменных печах. Полученный до сих пор материал дает, однако, по многим вопросам и направлениям исследований еще недостаточно полную картину. В особенности слабо исследованы еще процессы, происходящие при размягчении и плавлении компонентов шихты, о которых можно лишь догадываться.
Приближенная предварительная оценка качества руды до сих пор возможна лишь при использовании общих кинетических закономерностей или данных математически-статистической обработки результатов производственных опытов, как например в работах [510, 516]. Точное предварительное определение расчетом производственных показателей независимо от уже имеющихся показателей и от показателей, вычисленных для данного случая, на основе весьма приближенных производственных результатов возможно лишь в том случае, если скорости реакций и коэффициенты теплопередачи для всех компонентов шихты точно известны в широком интервале условий их существования в доменной печи, т. е. когда имеется большое количество данных по кинетике реакций.
Ниже будут охарактеризованы результаты, достигнутые к настоящему времени в области применения данных теоретических расчетов к практике доменного производства, и одновременно будет показано, что проведение дальнейших расчетов и опытов в лабораториях и на производстве оказывается весьма желательным и необходимым.
5.2. ПОДГОТОВКА ШИХТЫ К ПЛАВКЕ
5.2.1. ОСНОВНОЕ НАПРАВЛЕНИЕ В ТЕХНИКЕ ПОДГОТОВКИ ШИХТЫ
Еще в 1932 г. Вагнер, Хольшу и Барт [521] установили, что для достижения оптимальных величин по производительности доменной печи и удельному расходу кокса необходимо сузить интервал крупности кусков руды по верхнему и нижнему пределам перед загрузкой в печь1. В США подобные эксперименты.
привели к хорошим результатам [521а]. Мелкие (—5 мм) фракции в шихте вредны, так как при загрузке в печь они скапливаются в отдельных местах и по-настоящему закупоривают на отдельных участках столб шихты в печи. В разделе 3.1 было уже показано, что уже относительно небольшое содержание мелочи в столбе шихты достаточно для того, чтобы значительно повысить его сопротивление проходу газов. Так же как мелочь, вредны и чрезмерно крупные блоки руды (размер куска >80 мм), так как в печи в них затормаживаются процессы теплопередачи и восстановления. Сужение интервала крупности кусков руды при подготовке шихты к плавке, называемое Вагнером и сотрудниками «физической подготовкой шихты», введено за последние 10 лет в подавляющем большинстве доменных цехов [523—526, 526а], причем значительную помощь в этом деле оказало объяснение происходящих в печи процессов с реакционно-кинетической и газодинамической точек зрения '.
При подготовке шихты различают в основном три группы сооружений, области применения которых зависят от природы руды.
5.2.1.1. Дробильные и сортировочные фабрики
Поступающая кусковая руда измельчается в дробилках до кусков желаемого размера, после чего исходная и образовавшаяся при дроблении мелочь отделяется от руды грохочением [523]. На рис. 256 схематически показана схема цепи аппаратов дробильно-сортировочной фабрики. После разгрузки руда проходит две ступени дробления в конусных и валковых дробилках, которые по мере надобности разгружаются от мелочи путем предварительного грохочения перед дробилками, и затем четыре линии грохотов. Здесь мы не можем останавливаться на деталях, связанных с работой этих фабрик. Достаточно указать, что интервал крупности кусков руды, который в поставляемой руде лежал в пределах от 0 до 200 мм, после дробления и грохочения разбивается на три следующих интервала крупности:
а) мелочь от 0 до 6 мм (на агломерационную фабрику),
б) кусковая руда от 6 до 20 мм (для доменных печей),
в) кусковая руда от 20 до 60 мм (для доменных печей).
Рис. 257 показывает на примере фактический гранулометрический состав грохоченой руды фракций 6—20 и 20—60 мм. На большинстве дробильно-сортировочных фабрик получают только одну фракцию кусковой руды [526].
Преимущества и недостатки этих двух вариантов подготовки шихты будут рассмотрены нами ниже.
При восстановлении пористых руд часто наблюдают игольчатые кристаллы металла, которые врастают в зерна окисла. Так как отнятие кислорода может происходить только на фазовой границе окисел — газ, для их роста требуется диффузия железа в решетке, а также диффузия по границам зерен от поверхности к участкам роста кристаллов металла. Движущей силой диффузионного процесса должна быть активность железа на поверхности окисла. Выделение металла в окисле обусловливает появление напряжений, приводящих к разламыванию зерен и образованию новой поверхности. Образование и рост зародышей могут привести к изменениям объема и поверхности пор и соответственно к изменениям структуры пор [245]. Пересыщение окисла железа как предпосылка для образования металлической фазы влияет на кинетику восстановления, так как активности металла и кислорода в окисле состава Fe,Om связаны между собой отношением Следовательно, повышение активности металла приводит к снижению активности кислорода окисной фазы. Это изменение активности кислорода, согласно формуле (1.62), воздействует на скорость реакции на межфазной границе. При восстановлении высокопористых таблеток гематита Шефер [256] для температуры 350° С установил показанное на рис. 102 изменение скорости отнятия кислорода d(OFe)/dt со степенью восстановления O/Fe. При отношении O/Fe=wl,33 находится минимум скорости восстановления. Рентгенографически было показано, что до минимума таблетки не содержали метал¬лического железа, а после минимума не содержали гематита. Итак, минимум соответствует полному восстановлению образца до магнетита. Шефер объясняет падение скорости восстановления и отсутствие железа перед минимумом предположением, что в таблетке, пока восстанавливается гематит, имеется сравнительно высокое давление водяного пара или высокая активность кислорода. При такой высокой активности кислорода магнетит не пересыщается железом, что требуется для образования зародышей железа. Только после исчезновения гематита давление водяного пара в газе в порах падает столь резко, что активность железа в магнетите становится достаточной для образования зародышей. Медленный подъем скорости восстановления объясняется медленным ростом числа зародышей.