Внепечное вакуумирование стали
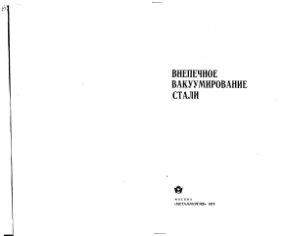
Морозов А.Н. и др.
Металлургия, 1975 г.
СНИЖЕНИЕ СТЕПЕНИ ЗАГРЯЗНЕННОСТИ СТАЛИ ОКСИДНЫМИ ВКЛЮЧЕНИЯМИ
Раскисление стали углеродом в вакууме, сочетающееся с энергичным перемешиванием, позволяет удалить в виде окиси углерода значительную часть растворенного в металле кислорода до введения сильных раскислителей. Тем самым уменьшается количество образующихся продуктов раскисления, загрязняющих сталь. Некоторая часть образующихся после раскисления включений всплывает на заключительной стадии вакуумирования в связи с энергичным перемешиванием металла.
При осуществлении такой технологии из сталеплавильного агрегата выпускают обычно нераскисленный кремнием и алюминием металл. В некоторых cлучаях, особенно при выплавке низкоуглеродистой стали в кислородных конверторах и мартеновских печах, металл раскисляют небольшими добавками кремния (0,05— 0,10%) с целью предотвращения чрезмерно бурной реакции в ковше или вакуум-камере.
Наличие в металле небольшого количества кремния не препятствует раскислению стали углеродом в вакууме.
Процесс раскисления стали углеродом в вакууме проводится обычно до достижения минимального давления в вакуум-камере. При порционном и циркуляционном вакуумировании для этого достаточно 3—5-кратной рециркуляции. Только после проведения раскисления стали углеродом в вакууме вводят раскислители, легкоокисляющиеся легирующие элементы и корректирующие добавки в определенной последовательности, затем металл некоторое время перемешивают для выравнивания химического состава и температуры.
На раскислении металла углеродом преимущественно основана технология внепечного вакуумирования широкого сортамента сталей ответственного назначения, к которым предъявляются повышенные требования по степени загрязненности металла оксидными включениями. К этим сталям относятся прежде всего подшипниковые, легированные конструкционные стали для авиационной и машиностроительной промышленности, приборостроения и судостроения, инструментальные, штамповые и другие стали, к которым предъявляются требования высокой эксплуатационной надежности.
При раскислении стали углеродом содержание последнего снижается, что необходимо учитывать при корректировке химического состава металла.
В некоторых случаях сталь до или в начале вакуумирования полностью раскисляют кремнием и алюминием. В процессе вакуумной обработки при хорошем перемешивании металла находящиеся в нем продукты первичного раскисления всплывают или восстанавливаются углеродом. После обработки в течение определенного времени (на установках порционного и циркуляционного типа при 2—3-кратной рециркуляции) вводят необходимые добавки и перемешивают металл. Раскисление стали до или в начале вакуумирования препятствует обезуглероживанию металла. Такая технология обеспечивает получение достаточно чистого по содержанию кислорода и оксидных включений металла, снижение содержания водорода до достаточно низких значений, высокую степень усвоения легкоокисляющихся элементов и возможность получения стали с заданным в узких пределах содержанием элементов. Однако в большинстве случаев сталь, вакуумированная в раскисленном состоянии, более загрязнена оксидными включениями, чем сталь, раскисленная предварительно углеродом в вакууме. Выбор той или иной технологии вакуумной обработки определяется в каждом конкретном случае, исходя из условий производства и уровня требований, предъявляемых к качеству металла.
Кнюппель с соавторами [104] сообщали о результатах порционного вакуумирования углеродистой мартеновской стали различных марок. Сталь выплавляли в 150-т мартеновских печах с выпуском металла в два ковша. В одном из ковшей сталь раскисляли ферросилицием в обычном порядке. Металл другого ковша раскисляли углеродом в вакууме, а ферросилиций вводили в вакуум-камеру после 3,0—3,5-кратной рециркуляции. Вакуумная обработка заканчивалась перемешиванием металла в течение 5—10 циклов. Содержание кислорода определяли методом горячей экстракции из проб, отобранных по сечению проката из металла обоих ковшей. Результаты анализа проб металла приведены на рис. 45.
Вакуумная обработка привела к значительному уменьшению содержания кислорода (оксидных включений) в готовом прокате. При этом оксидные включения распределялись равномернее по сечению слитка. Эти результаты были подтверждены при металлографическом контроле стали.
Обработка нераскисленной стали в вакууме приводила к заметному (до 0,06%) снижению содержания углерода (рис. 45).
На заводе в Кентоне, США [60] исследовали качество конструкционной легированной стали.
Сталь с различным содержанием углерода выплавляли в 90-т электродуговых печах и вакуумировали в ковше на установке с электромагнитным перемешиванием. При вакуумной обработке нераскисленной стали передвыпуском плавки из печи удаляли шлак, металл обрабатывали в вакууме в течение 15—20 мин. После достижения остаточного давления 0,013 кН/м2 (0,1 мм рт. ст.) присаживали в ковш ферросилиций, алюминий и корректирующие добавки марганца, хрома и углерода и перемешивали металл не менее 2 мин.
При вакуумной обработке спокойной стали ферросилиций и алюминий присаживали в металл при выпуске плавки из печи. Результаты определения содержания кислорода в прокате этих плавок приведены в табл. 8, в которой результаты, полученные при вакуумировании нераскисленных плавок, сопоставлены с данными для тех же сталей, выплавленных в той же электропечи по обычной технологии со сменой окислительного шлака без вакуумирования.
При металлографической оценке площадь поверхности шлифов, приходящаяся на долю оксидных включений, у вакуумированной стали оказалась на 50% ниже, чем в обычной.
Аналогичные результаты были получены и в наших исследованиях при вакуумировании стали 18Х2Н4ВА в струе при выпуске из 10-т электропечи. В первом случае шлак в печи обрабатывали только молотым коксом (вариант 1), во втором — коксом и ферросилицием (вариант 2). В обоих случаях недостающее количество ферросилиция, а также ферротитан и алюминий помещали на дно ковша в вакууме. При выплавке этой стали без вакуумной обработки (вариант 3) плавку проводили обычным двухшлаковым процессом с диффузионным раскислением металла в печи. Ниже приведены результаты исследования полученного металла. Исследования, проведенные на заводе Хирохата фирмы «Ниппон стил корп» были посвящены сопоставлению степени загрязненности высококачественного толстолистового проката (0,08—0,18% С; 1,3% Мn; 0,25% Si; 0,02—0,04% Аl) после вакуумной обработки раскисленного и нераскисленного металла на установке циркуляционного типа [9]. При полном раскислении металла до вакуумирования все необходимое количество алюминия, кремния и марганца присаживали в ковш во время выпуска плавки; в другом случае в ковш присаживали только ферромарганец, а алюминий и ферросилиций вводили после раскисления стали углеродом в вакууме. Содержание оксидных включений, особенно размером более 200 мкм, в вакуумированной в раскисленном состоянии стали оказалось значительно больше.
В последние годы в результате многочисленных исследований, обобщенных Кнюппелем [105], установлено, что скорость всплывания и полнота удаления продуктов первичного раскисления стали определяется главным образом составом образующихся включений, что в свою очередь зависит от вида и порядка введения рас- кислителей. В частности, продукты раскисления стали
алюминием удаляются из жидкого металла значительно быстрее и полнее, чем кремнистые включения.
Эти представления, подтвержденные результатами производственных исследований, оказали определенное влияние на технологию раскисления стали и, в частности, на последовательность ввода различных раскислителей в процессе вакуумной обработки. Оказалось, что при вакуумировании раскисленных алюминием сталей, особенно низкоуглеродистых, конечное содержание кислорода и оксидных включений мало зависит от времени ввода алюминия при условии, что после раскисления металл энергично перемешивался.
Так, при порционном вакуумировании конструкционной мартеновской стали (0,16% С; 1,0—1,3% Мп; 0,8— 1,10% Сг) на заводе фирмы «Зюдвестфален» (ФРГ) [100] варьировали временем ввода алюминия (до 1 кг/т) в процессе вакуумной обработки. Часть плавок была раскислена алюминием до вакуумирования, на остальных алюминий вводили в вакуум-камеру после 4— 30 циклов обработки. В пробах металла из готового проката (верхней, средней и хвостовой части слитка) среднее содержание кислорода составляло 0,0016—0,0035%. Какой-либо зависимости концентрации остаточного кислорода от продолжительности вакуумной обработки стали до ввода алюминия не было установлено; колебания по содержанию остаточного кислорода были связаны исключительно с расходом алюминия. Авторы работы [100] пришли к заключению, что перемешивание металла после его раскисления алюминием в течение 8 циклов обеспечивало достаточно полное удаление включений глинозема из стали.
Очевидно, было бы неправильным пытаться установить какие-либо определенные нормы (число циклов, продолжительность перемешивания аргоном, коэффициент рециркуляции), гарантирующие достаточно полное удаление включений глинозема в процессе вакуумирования, так как это определяется назначением металла и конкретными условиями производства. Между тем технология, предусматривающая предварительное раскисление стали алюминием до или в начале вакуумирования, получила распространение на многих металлургических предприятиях. Такая технология, обеспечивая получение чистой по оксидным включениям стали, дает
возможность гарантировать узкие пределы по содержанию углерода, сократить продолжительность вакуумной обработки и предотвратить чрезмерно бурное вскипание металла в ковше или в вакуум-камере.
Отдельно следует остановиться на последовательности введения присадок в процессе вакуумирования в тех
случаях, когда в качестве раскислителей используют кремний и алюминий.
Обобщая современный опыт внепечного вакуумирования, Халлемейер и Кутчер [9] представили зависимость между содержанием углерода и кислорода в процессе вакуумной обработки стали (рис. 46). Заштрихованная область 1 на диаграмме характеризует содержание углерода и кислорода в нераскисленном металле при выпуске из печи; область 2 — это же соотношение после раскисления углеродом в вакууме; область 3 — после раскисления металла алюминием в вакууме и удаления продуктов раскисления. Содержание кислорода в металле после раскисления углеродом в вакууме (область 2) при данном содержании углерода ниже, чем в стали, раскисленной кремнием. С этой точки зрения казалось бы безразличным, в какой последовательности следует вводить в металл кремний и алюминий. Однако результаты производственных исследований свидетельствуют, что загрязненность готовой стали оксидными включениями в значительной степени определяется последовательностью раскисления вакуумированного металла. Это, по-видимому, объясняется тем, что при местном обогащении отдельных объемов металла кремнием последний может реагировать с кислородом и после проведения раскисления стали углеродом в вакууме. Образующиеся при этом включения кремнезема удаляются из металла значительно хуже, чем включения глинозема.
Подробные исследования в этом направлении были проведены на заводе в Уиллэнде фирмы «Атлас стал» (США) [106], где выплавляли легированные конструкционные стали ответственного назначения в 35—50-т электропечах с обработкой металла на установке порционного вакуумирования. Выплавляемую сталь тщательно контролировали на загрязненность оксидными включениями.
Всю сталь перед вакуумированием предварительно раскисляли кремнием (до 0,10% Si). Недостающее количество кремния и алюминий вводили в вакуум-камеру в конце обработки. При раскислении металла сначала алюминием, а затем кремнием обеспечивались значительно лучшие результаты по оксидным включениям, чем при обратном порядке окончательного раскисления.
Подробных результатов исследований, подобных приведенному выше, насколько нам известно, опубликовано не было. Поэтому трудно оценить, в какой степени последовательность раскисления вакуумированного металла кремнием и алюминием влияет на степень загрязненности готового проката оксидными включениями в отличающихся производственных условиях и при обработке стали других марок.