Валки для профильного проката
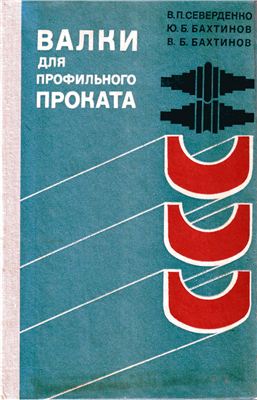
Северденко В.П., Бахтинов Ю.Б., Бахтинов В.Б.
Металлургия, 1979 г.
6. МАТЕРИАЛ ВАЛКОВ
Большую роль при производстве профильного проката играет правильный выбор металла валков.
Чугунные валки для сортовых станов горячей прокатки изготавливают по ГОСТ 11143—65 следующих видов: из нелегированного чугуна с /пластинчатым (СП) и шаровидным (СШ) графитом; из легированного чугуна с пластинчатым (СПХН) и шаровидным (СШХН) графитом.
Легированные чугунные валки с пластинчатым графитом (СП) изготавливают с отбеленным перлито-графитовым и с перлито-карбидо-графитовым рабочим слоем.
Легированные чугунные валки с пластинчатым графитом (СПХН) изготавливают с отбеленным или с перлито-карбидо-графитовым рабочим слоем, а также двухслойными с рабочей поверхностью из легированного отбеленного чугуна и с сердцевиной из серого или легированного чугуна.
Нелегироваяные чугунные валки с шаровидным графитом (СШ) (изготавливают с отбеленным перлито-графитовым и перлито-карбидо-графитовым рабочим слоем.
Легированные чугунные валки с шаровидным графитом (СШХН) изготавливают с перлито-карбидо-графитовым рабочим слоем, а также двухслойный с рабочей поверхностью из легированного отбеленного чугуна и с сердцевиной из серого или легированного чугуна. Все указанные выше типы чугунных валков отливают гладкими или с профильными ручьями.
Твердость поверхности бочек отбеленных чугунных валков, как правило, определяют приборами типа Шора. Твердость валков с перлито-окарбидо-графитовой структурой должна определяться по Бринеллю.
Стальные валки (кованые и литые) для сортовых станов горячей прокатки изготавливают по ГОСТ 9487—70 (технические требования) и ГОСТ 5399—69 (основные размеры).
Стальные прокатные валки изготовляют литыми и коваными для горячей прокатки и коваными для холодной прокатки.
Стальные литые валки для горячей прокатки выполняют из доэвтектоидных (0,46—0,70% С, HS24—27), эвтектоидных (0,75—0,85% С, HS30—40) и заэвтектоидных (1,1—1,6% С, HS32—50) сталей.
Стальные кованые валки для холодной прокатки изготовляют по ГОСТ 3541—74, а для горячей прокатки — по техническим условиям, согласованным между заводами-изготовителями и заводами-потребителями.
Стальные валки для блюмингов, слябингов и заготовочных станов изготовляют в основном из кованой углеродистой стали, содержащей 0,6— 0,8% С, или легированной хромоникелевой стали марок 50ХН и 60ХН, а также из литой стали 50, 50ХН, 150ΧΉΜ; валки рельсо-балочных и крупносортных станов — из кованой стали 50, 55, 55Х, 40ХН, 50ХН, 60 ХН, 9Х и 9ХФ; валки среднесортных станов—из кованой стали 50, 55, 55Х и 50ХН и литой 150ХНМ; валки мелкосортных станов из кованой стали 50, 55, 55Х и 60ХГ и литой 150ХНМ; проволочных станов — из кованой стали 50, 9Х, 9ХФ и 9Х2МФ и литой 150ХНМ; штрипсовых станов — из кованой стали 50, 60ХГ и литой 150ХНМ.
Бандажи сборных валков станов холодной прокатки изготовляют из сталей 9Х, 9X2, 9ХФ, 75ХМ и оси валков из сталей 45ХНМ, 40ХН2МА, 55Х.
Химический состав металла калков должен соответствовать ГОСТ 1050— 74 для сталей марок 50 и 55, ГОСТ 4543—71 для сталей марок 40ХН, 50ХН и 40ХН2МА; ГОСТ 3541—74 для сталей марок 55Х, 9ХФ; ГОСТ 5950—63 для стали 9Х; ГОСТ 10207—70 для стали 45ХНМ.
7. МЕТОДЫ ИЗГОТОВЛЕНИЯ ВАЛКОВ
Чугунные валки изготавливают только отливкой. Изготовление литых, валков — сложный процесс с большим числом промежуточных операций. Качество литых валков зависит в основном от вида литейной формы. Например, тепловое сопротивление земляной формы в несколько (раз больше, чем металлической.. Валки, отлитые в земляную форму, имеют более низкие прочность и износостойкость, что обусловлено медленным затвердеванием жидкого металла.
Мягкие (незакаленные) валки отливают из черного чугуна в земляную форму -(опоку). (Полутвердые (полузакаленные) валки отливают в металлическую чугунную форму (кокиль), покрытую изнутри слоем глины толщиной до 15—20 :мм для замедления -процесса отбеливания чугуна «а бочке валков. Твердые (закаленные) валки отливают в металлическую нефутерованную форму. Валки высокой твердости изготавливают двухслойными: наружный слой из высоколегированного чугуна, а сердцевину — из чугуна дешевого, но более прочного при работе на изгиб.
Механическая обработка валков с отлитыми ручьями значительно проще. Требуемые глубина и твердость отбеленного рабочего слоя достигаются подбором толщины слоя обмазки и химическим .составом чугуна. Глубина отбеленного рабочего слоя валков мелкосортных станов составляет 15—30 мм, средне-сортных 20—40 мм и крупносортных и рельсо-балочных 150—200 мм/ Глубина отбеленного слоя ручьевых валков должна обеспечить возможность полной их переточки.
Магнитогорский (ММК) и Кузнецкий (КМК) металлургические комбинаты, Серовский металлургический завод применяют передовую технологию литья валков в металлические сборные формы. Большого внимания заслуживает технология литья валков на КМК. Верхняя шейка валка формируется в земляной форме, а бочка и нижняя шейка — в чугунном кокиле. Внутреннюю поверхность литейной формы окрашивают хромомагнезитовой краской толщиной до б мм. Окрашенные формы сушат при 300—350°С.
Чугунные валки отливают на Днепропетровском чугуно-вальцеделательном заводе (ДЧВЗ), Лутугинском заводе прокатных валков (ЛЗПВ), Кушвинском заводе и для собственных нужд на КМК, ММК, Серовском металлургическом заводе и на других заводах.
Химический анализ чугуна должен проводиться (ГОСТ 2331—63) на пробах, взятых при заливке чугуна.
Работниками Лутугинского завода освоен способ обработки чугуна магнием с использованием жидкой чугуно-магниевой лигатуры. Сущность способа заключается в том, что обработке магнием подвергают не всю массу (металла в 35-т ковше, а только часть его в малом ковше емкостью 10— 15 т.
Плавку ведут одновременно в вагранке и пламенной печи. Обе части плавки (ваграночная, обработанная магнием и печная) после смешивания обеспечивают требуемые химический состав, твердость и микроструктуру отливок.
Обработка чугуна жидкой чугуно-магниевой лигатурой позволяет повысить температуру заливки и сохранить в массовых отливках остаточный магний, необходимый для образования в чугуне шаровидной формы графита.
Опыт Лутугинского завода получения тяжелых отливок из магниевого чугуна переняли многие заводы как в нашей стране, так и за рубежом.
Вакуумирование жидкого чугуна при отливке способствует уменьшению газонасыщенности и загрязненности неметаллическими включениями металл а валков; при этом глубина отбеленного слоя валков уменьшается в 1,3 раза, а переходной зоны — в 1,5 раза.
На некоторых металлургических заводах при изготовлении литых стальных валков наряду с заливкой металла в -форму (кокиль) сверху применяют сифонную заливку. Сифонная заливка позволяет уменьшить припуск под механическую обработку валков на 25—30%. Однако сифонная заливка усложняет процесс формовки и выбивки валков из формы, повышает стоимость изготовления форм и требует больше производственных площадей.
Стойкость кокилей для валков диаметром 800—1100 мм и длиной бочки до 2000 ммдостигает 35 заливов, а для валков диаметром до 800 мм находится в пределах 40—50. На КМК кокили массой более 10 τ отливают с бандажами, что приводит к увеличению стойкости кокилей на 20—25%.
Литые стальные валки для горячей прокатки находят все большее применение. Ряд заводов черной металлургии, используя передовую технологию-изготовления валков, уже в течение нескольких лет успешно применяет литые стальные валки вместо кованых.
Литые валки из углеродистых заэвтектоидных сталей (марок У10, У12) изготавливают и эксплуатируют на ММК и КМК в черновых клетях рельсо-балочных и крупносортных станах.
Успешное применение литых стальных валков объясняется их низкой, стоимостью и высокой стойкостью. Срок службы литых валков обычно в 1,5—2,5 раза больше, чем кованых.
Основными поставщиками кованых валков горячей прокатки являются УЗТМ, НКМЗ, ЭЗТМ, ЮУМЗ, Ижорский, Днепропетровский и некоторые другие заводы тяжелого машиностроения, располагающие мощным кузнечно-прссовым оборудованием и необходимыми рредствами термообработки.
Качество валков, выпускаемых отдельными заводами, неодинаково. Как показывают многочисленные статистические данные, наиболее высокую стойкость при эксплуатации имеют валки Уралмашзавода. Ковку валков на УЗТМ в отличие от ковки на большинстве других заводов осуществляют, как правило, с одной осадкой при степени укова не менее трех. Для повышения износостойкости бочку валков можно подвергать поверхностной закалке, наплавке твердыми сплавами и обкатке роликами.
В зависимости от марки стали валки для горячей прокатки подвергают следующим видам термической обработки: нормализации и отпуску (для рельсо-балочных и крупносортных станов) — стали марок 50, 55, 9Х, 9ХФ; закалке и отпуску (для проволочных станов) —9Х, 9ХФ, 9Х2МФ; двойной нормализации и отпуску (для непрерывно-заготовочных, среднесортиых, мелкосортных станов) — 150ХНМ.
Стали марок 55Х, 60ХГ, 50ХН и 60ХН подвергают нормализации и отпуску или по требованию заказчика — закалке и отпуску для валков с бочкой диаметром до 500 мм, а с бочкой диаметром более 500 мм закалка и отпуск должны проводиться по соглашению сторон.
Литые валки из стали марок типа 60ХН подвергают термической обработке по следующему режиму '[}]: выдержка в печи в течение 4 ч при 250°С, последующий нагрев до 650° со скоростью 40°С/ч, выдержка 3—5 ч; нагрев до 950°С со скоростью 60°С/ч, выдержка 18—22 ч; охлаждение на воздухе до 550—600°С; нагрев до 850—870°С, со скоростью 80°С/ч выдержка 14— 18 ч; охлаждение на воздухе до 400—500°С; нагрев до 600°С со скоростью 80°С/ч; выдержка 12 ч; охлаждение с печью до 200°С со скоростью 25°С/ч. Время термической обработки составляет около ПО ч.
На ММК литые валки из стали У150ХНМ подвергают термической обработке по следующему режиму: тройная нормализация с температур 1050, 820, 900°С, последующий отпуск при 600°С (твердость HS46—49), нормализация с Ш50°С, последующий отжиг при 820°С (твердость HS41—45),
Кованые стальные валки из углеродистых сталей подвергают термической обработке по следующему режиму : нагрев до температуры нормализации (830—870°С) с выдержкой в печи после выравнивания температуры из расчета 0,6 ч на 100 мм толщины с последующим охлаждением на воздухе до '250—550°С. Температура отпуска 580—660°С, время выдержки из расчета 1,2 ч на 100 мм толщины. Охлаждение после отпуска: до 400°С со скоростью 40—60°С/ч, охлаждение до 250—300°С со скоростью 20—30°С/ч. Нагрев и охлаждение валков из легированных сталей осуществляют более осторожно.
Валки из углеродистых сталей можно подвергать термической обработке в необработанном виде, а из легированных — только после механической обработки.
Валки для горячей прокатки должны поставляться с чисто обработанными и зацентрованными шейками. Шероховатость поверхности бочки валков для горячей прокатки должна быть не ниже 5-го класса, а грубообработанной поверхности бочки —не ниже 3-го класса (ГОСТ 2789—73).