Вакуумные плазменные электропечи
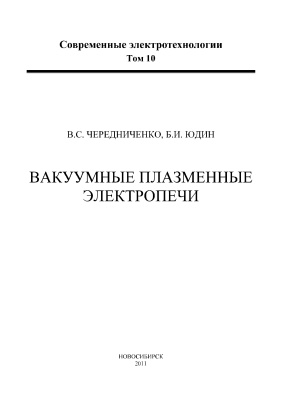
Чередниченко В.С., Юдин Б.И.
Красноярск: СФУ, 2011 г.
§ 10.2. ВАКУУМНЫЕ ПЛАЗМЕННЫЕ ПЕЧИ ДЛЯ ВЫПЛАВКИ СЛИТКОВ
Вакуумные плазменные печи для выплавки металла по их принципу действия можно разделить на печи для переплава расходуемых массивных заготовок, кусковой или таблеточной шихты и порошковых материалов без предварительной их подготовки [207, 283, 284]. В первом варианте электротехнологий используются цилиндрические полые катоды, а при переплаве порошковых материалов - кольцевые полые катоды с центральной технологической трубкой для подачи порошков транспортным газом. Кристаллизатор, выполняющий функцию анода, изготавливается небольшой длины с подвижным дном, перемещающимся вниз по мере наплавления слитка со скоростью его наплавления. Под кристаллизатором расположена холодильная камера, в которой осуществляется окончательное охлаждение слитка. Электропечи такого типа могут иметь промежуточную емкость (холодный под), в [207]. Например, как указывается в [282], процесс раскисления гафния при температуре плавления этого металла протекает очень медленно. Однако если перегреть жидкий гафний на несколько сотен градусов, то содержание примесей может заметно уменьшиться в течение приемлемого промежутка времени.
Аналогично процесс развивается при глубоком рафинировании олова от сурьмы и мышьяка (см. § 10.4). Не менее важное значение имеет степень перегрева при плавке циркония. Среди тугоплавких металлов цирконий обладает самым низким давлением паров при температуре плавления, что позволяет перегревать его примерно на 425 °С без серьезных потерь за счет испарения. Этот технологический прием обеспечивает испарение примесей с низким давлением паров, которые не удаляются другими технологиями. Перегревом циркония можно обеспечить значительное снижение твердости плавленого металла. Длительная выдержка в перегретом состоянии более эффективно воздействует на испарение примесей, чем многократная переплавка. Показательным примером может служить высокая эффективность вакуумной плазменной плавки чернового порошка тантала натрийтермического восстановления. Качество получаемого тантала при одном переплаве оказывается равнозначным дубль-процессу ВДП-ЭЛУ. Результаты этих работ приведены в § 10.2.
§ 10.2. ВАКУУМНЫЕ ПЛАЗМЕННЫЕ ПЕЧИ ДЛЯ ВЫПЛАВКИ СЛИТКОВ
Вакуумные плазменные печи для выплавки металла по их принципу действия можно разделить на печи для переплава расходуемых массивных заготовок, кусковой или таблеточной шихты и порошковых материалов без предварительной их подготовки [207, 283, 284]. В первом варианте эл сктротсх11ojιοi ий используются цилиндрические полые катоды, а при переплаве порошковых материалов - кольцевые полые катоды с центральной технологической трубкой для подачи порошков транспортным газом. Кристаллизатор, выполняющий функцию анода, изготавливается небольшой длины с подвижным дном, перемещающимся вниз по мере наплавления слитка со скоростью его наплавления. Мод кристаллизатором расположена холодильная камера, в которой осуществляется окончательное охлаждение слитка. Электропечи такою типа могут иметь промежуточную емкость (холодный под), в
которой металл расплавляется и рафинируется, а затем путем перелива в кристаллизатор формируется слиток. В этом случае печь имеет 3— 5 плазмотронов, объединенных одним анодом.
Первая отечественная промышленная вакуумная плазменная электропечь ВПП-500 была разработана, изготовлена и пущена в эксплуатацию на опытной базе СКВ производственного объединения «Сибэлектротерм» в 1972 году. Она предназначалась для реализации комплексной технологии получения чистого урана [9, 10, 49]. В этот период на одном из новосибирских заводов (ныне НЗХК) в плазменной электропечи шахтного типа был получен уран карботермическим восстановлением в водородной плазме со степенью восстановления 92...95 % [9]. Процессы довосстановления и дистилляционного рафинирования уранового полупродукта осуществлялись в электропечи ВПП-500, схема которой дана на рис. 10.1, а работа на промышленной электропечи иллюстрируется рис. В.ЗО.
Электропечь включает в себя следующие основные узлы: рабочую камеру /; узел вакуумных плазмотронов 2; холодный под - медную водоохлаждаемую емкость 3, предназначенную для расплавления и рафинирования металла; механизм загрузки исходного чернового металла 4; механизм вытяжки слитка 5; стабилизирующий соленоид 6; вакуумную систему; кристаллизатор 7 с поддоном; источник питания с системой запуска вакуумных плазмотронов в рабочий режим; стенды газоснабжения, водоохлаждения, регистрации давлений и контроля температурных режимов. Механизм загрузки исходного чернового металла имеет шнековый питатель для подачи специально подготовленного шихтового материала, получаемого в электропечи карботермического восстановления урана. При необходимости переплава металла в виде слитков (прутков) шнековый механизм загрузки заменялся на устройство для подачи цилиндрического слитка, а жидкий металл стекал и накапливался на холодном поду. Подаваемый черновой металл и холодный под выполняли роль анодов, а распределение тока между анодными цепями отдельных плазмотронов обеспечивалось внешней системой управления. Катододержатели установлены в специальных шаровых уплотнениях, что позволяет перемещать катоды и увеличивать площадь нагрева металла.
Установка обеспечивает непрерывный процесс рафинирования металла с организацией движения расплава на холодном поде - в водоохлаждаемой металлической ванне, а формирование слитка чистого металла - в кристаллизаторе с непрерывной вытяжкой.
После получения положительных результатов в технологии довосстановления и рафинирования урана электропечь находилась в опытной эксплуатации для проведения цикла исследований вакуумных плазмотронов и отработки технологий восстановления и рафинирования цветных металлов и сталей различных сортаментов с получением слитков, соответствующих по составу действующим стандартам:
- переплав и довосстановление урана с получением слитка диаметром 120 мм;
- получение слитков тантала, ниобия и молибдена в кристаллизаторах диаметрами 80 и 120 мм;
- переплав отходов титана с получением слитков в кристаллизаторе диаметром 220 мм;
- выплавка сложнолегированных жаропрочных сплавов на основе хрома и никеля с получением слитков диаметром 120 мм;
• получение слитков азотированной стали путем добавки азота в плазмообразующий газ.
Технические характеристики электропечи ВПП-500
Установленная мощность, кВт 562
Количество вакуумных плазмотронов, пп 4
Номииальпая мощность одною вакуумного ιглазмотропа, кВт 100...150 Род тока для питания вакуумного плазмотрона Постоянный
Рабочий газ Аргон
Расход ι гтазмообразу ιοί него газа, кг/с (2... 8)· 10-5
Рабочее давление в камере элек тропечи, 11а 13,3.. .0,133
Рабочее на пряжение, В 40... 120
Размеры выплавляемого слитка, мм
диаметр 80... 220
высота 1000
Последующие разработанные в ПО «С и бэл ектротер м» вакуумные плазменные печи для получения слитков [49-51], имеют мощность от 500 до 1200 кВт и предназначены для переплава высокореакционных металлов и для восстановительных металлургических процессов. Печи имеют типовую конструкцию, включающую горизонтально расположенные рабочие камеры, промежуточные емкости и кристаллизаторы с механизмами вытяжки и охлаждения слитков. Условия работы и назначение различных узлов печи для довосстановления и рафинирования урана в сущности ничем не отличаются от условий работы и назначения узлов печи мощностью 1200 кВт, предназначенной для получения слитков таких металлов, как тантал, ниобий, молибден, гафний, титан и др. В комплект оборудования входят сменные узлы загрузки кусковой шихты или переплавляемых слитков и до за грузки в промежуточную емкость легирующих материалов. Полые катоды выполнены в виде цилиндров, рабочие газы - аргон, гелий, азот. Схема электропечей приведена на рис. 10.2, а технические характеристики даны в табл. 10.1.
Для разработки новых электротехнологий получения слитков из кусковой шихты, таблеток и переплавляемых слитков создана лабораторная печь BIII1-80, общий вид которой приведен на рис. 10.3.
Рабочая камера представляет собой стальной цилиндр с водоохлаждаемыми днищем и крышкой, внутренний диаметр камеры 0,7 м, высота 0,55 м. На кожухе расположены патрубок для подсоединения камеры к вакуумной системе, гляделки, патрубки для ввода в рабочее
пространство термопар, электрических зондов, манометрических ламп для измерения давления в камере, токоподвода соленоида и др. Гляделки с кварцевыми стеклами, охлаждаемые водой, установлены диаметрально противоположно, что позволяет наблюдать за всем рабочим объемом камеры и измерять температуру катода и переплавляемых металлов, используя различную аппаратуру.
Днище выполнено конструктивно как единое целое с кожухом и имеет несколько вакуумных вводов для установки в камере водоохлаждаемых тепломеров, водоохлаждаемых анодов и кристаллизаторов различной конструкции и различных датчиков. На рис. В.31 показаны внутреннее рабочее пространство печи и кристаллизатор.
На крышке камеры с помощью координатного механизма установлен вакуумный плазмотрон, который может перемещаться вдоль вертикальной оси. Конструкция катододержателя позволяет подавать плазмообразующий газ в катод и измерять давление непосредственно в начале канала катода. Фланец одной из гляделок позволяет устанавливать устройство с перемещающимся в горизонтальной плоскости электростатическим зондом Лэнгмюра.
Вакуумная система установки состоит из паромасляного насоса БН-4500 и форвакуумного механического насоса ВН-6Г. Для расширения возможностей вакуумной системы параллельно-последовательно насосу БН-4500 установлен механический бустерный насос ДВН-1500.