А.М. Самарин
Москва
http://publ.lib.ru/ARCHIVES/S/SAMARIN_Aleksandr_Mihaylovich/Vakuumnaya_metallurgiya.(1958).[pdf].zip
1958
Текст:
<p><font size="2">В результате наблюдений установлено, что при выплавке трансформаторной <a href="/slovar/stal">стали</a> в <a href="/slovar/vakuum">вакууме</a> жидкий <a href="/slovar/metally">металл</a> очищается от кислорода и серы при отсутствии шлака на поверхности ме­талла. Раскислительная способность углерода при снижении дав­ления в плавильном пространстве до 1 мм рт. ст. повышается почти в сто раз (21.)</font></p>
<div><font size="2">Использование вакуума при выплавке трансформаторной стали обеспечивает возможность повышения содержания в ней <a href="/slovar/krivaya">кремния</a> и снижения ваттных потерь на 20—25%.</font></div>
<div><font size="2">Подобное снижение ваттных потерь имеет огромное народно­хозяйственное значение в период быстрого роста новых устано­вок для генерации электрической энергии. Если для сооружения устройств, связанных с передачей и распределением электриче­ской энергии, использовать трансформаторную сталь, ваттные потери которой на 20 процентов ниже, чем стали, ныне используемой, то, принимая современный уровень расхода этой стали на силовые трансформаторы, ежегодная экономия электриче­ской энергии, только ори эксплуатации вновь вводимых каждый год трансформаторов, составит более 500 миллионов киловатт-часов. Использование трансформаторной стали улучшенного ка­чества позволит, помимо экономии электрической энергии, сни­зить расход этой стали и мели на сооружение трансформаторов.</font></div>
<div><font size="2">Положительные результаты в повышении качества хромоникелевой нержавеющей стали получены при <a href="/slovar/obezuglerozhivanie">обезуглероживании</a> этой стали в индукционной вакуумной печи (3].</font></div>
<div><font size="2">Как известно, в последнее время, за счет применения кисло­рода, значительно улучшены показатели <a href="/slovar/proizvodstvo">производства</a> нержа­веющей стали методом <a href="/slovar/pereplav">переплава</a> отходов этой стали. Несмот­ря на эти достижения, нельзя ныне используемый метод признать оптимальным, вследствие того, что при его применении нельзя получить нержавеющую сталь с весьма низким содержанием уг­лерода. Кроме того, при этом методе выплавки потери хрома остаются еще очень высокими (иногда достигают 20 процентов от содержания хрома в отходах нержавеющей стали); повышает­ся также расход огнеупорных материалов из-за быстрого <a href="/slovar/iznos">износа</a> <a href="/slovar/futerovka">футеровки</a> <a href="/slovar/podina">подины</a> и откосов дуговых печей.</font></div>
<div><font size="2">Поэтому по-прежнему необходимо продолжать поиски более рационального метода использования отходов нержавеющих сталей.</font></div>
<div><font size="2">В дуговых вакуумных печах как с постоянным, так и с расхо­дуемым электродом обеспечено получение стали и <a href="/slovar/splavy">сплавов</a> с бо­лее низким содержанием кислорода, азота и водорода, чем при выплавке в индукционных вакуумных печах. Эта повышенная чистота стали и сплавов объясняется тем, что в дуговых вакуум­ных печах нет контакта жидкого металла с огнеупорными мате­риалами футеровки. В этих печах жидкий металл а <a href="/slovar/techenie">течение</a> очень короткого промежутка времени находится в соприкосно­вении лишь со стенками водоохлаждаемого медного <a href="/slovar/kokil">кокиля</a>, в ко­тором он и .затвердевает. Кроме того, весьма высокая температу­ра в зоне электрической дуги благоприятствует <a href="/slovar/dissotsiatsiya">диссоциации</a> нитридов и <a href="/slovar/vosstanovlenie">восстановлению</a> окислов.</font></div>
<div><font size="2">В промышленной практике более широкое применение для по­лучения слитков имеют дуговые вакуумные печи с расходуемым электродом. Естественно, что эти печи предназначены для пере­плава в вакууме сталей и сплавов, выплавленных ранее в других сталеплавильных агрегатах, поэтому дополнительное леги­рование в них практически не осуществляется. Это, 'Конечно, яв­ляется известным недостатком дуговых вакуумных печей с рас­ходуемым электродом.</font></div>
<div><font size="2">На рис. 7 показано устройство лабораторной дуговой вакуум­ной печи, в которой возможно получение слитков диаметром 100—150 мм. В качестве расходуемого электрода использованы штанги длиною 1200 мм и диаметром 60—100 мм. Вес получае­мых стальных слитков составляет 25—75 кг.</font></div>
<div><font size="2">Печь питается постоянным током с отрицательной полярно­стью на электроде. Источником постоянного тока являются два генератора, подключенные параллельно; мощность каждого ге­нератора 60 кет, напряжение 60 в. При параллельном <a href="/slovar/vklyucheniya">включении</a> генераторов возможно подведение тока силою 2000 а.</font></div>
<div><font size="2">Перемещение электрода автоматизировано — во время плав­ки регулятор поддерживает заданную длину дуги.</font></div>
<div><font size="2">Расход электрической энергии в этой небольшой печи на .рас­плавление стальных электродов составляет 800 квт-ч/т. Понижение <a href="/slovar/davlenie">давления</a> в рабочем пространстве печи до 1 * 10-4 мм рт. ст. достигается за счет работы двух бустерных ма­сляных насосов БН-3 (производительность каждого 500 л/сек) и двух форвакуумных насосов ВН-1 (производительность каж­дого 1100 л/мин). Эта печь была использована для переплава шарикоподшипниковой стали, выплавленной в дуговой электрической печи, с целью снижения содержания в стали неметаллических включе­ний.</font></div>
<p> </p>
<div><font size="2">Использование вакуума при выплавке трансформаторной стали обеспечивает возможность повышения содержания в ней <a href="/slovar/krivaya">кремния</a> и снижения ваттных потерь на 20—25%.</font></div>
<div><font size="2">Подобное снижение ваттных потерь имеет огромное народно­хозяйственное значение в период быстрого роста новых устано­вок для генерации электрической энергии. Если для сооружения устройств, связанных с передачей и распределением электриче­ской энергии, использовать трансформаторную сталь, ваттные потери которой на 20 процентов ниже, чем стали, ныне используемой, то, принимая современный уровень расхода этой стали на силовые трансформаторы, ежегодная экономия электриче­ской энергии, только ори эксплуатации вновь вводимых каждый год трансформаторов, составит более 500 миллионов киловатт-часов. Использование трансформаторной стали улучшенного ка­чества позволит, помимо экономии электрической энергии, сни­зить расход этой стали и мели на сооружение трансформаторов.</font></div>
<div><font size="2">Положительные результаты в повышении качества хромоникелевой нержавеющей стали получены при <a href="/slovar/obezuglerozhivanie">обезуглероживании</a> этой стали в индукционной вакуумной печи (3].</font></div>
<div><font size="2">Как известно, в последнее время, за счет применения кисло­рода, значительно улучшены показатели <a href="/slovar/proizvodstvo">производства</a> нержа­веющей стали методом <a href="/slovar/pereplav">переплава</a> отходов этой стали. Несмот­ря на эти достижения, нельзя ныне используемый метод признать оптимальным, вследствие того, что при его применении нельзя получить нержавеющую сталь с весьма низким содержанием уг­лерода. Кроме того, при этом методе выплавки потери хрома остаются еще очень высокими (иногда достигают 20 процентов от содержания хрома в отходах нержавеющей стали); повышает­ся также расход огнеупорных материалов из-за быстрого <a href="/slovar/iznos">износа</a> <a href="/slovar/futerovka">футеровки</a> <a href="/slovar/podina">подины</a> и откосов дуговых печей.</font></div>
<div><font size="2">Поэтому по-прежнему необходимо продолжать поиски более рационального метода использования отходов нержавеющих сталей.</font></div>
<div><font size="2">В дуговых вакуумных печах как с постоянным, так и с расхо­дуемым электродом обеспечено получение стали и <a href="/slovar/splavy">сплавов</a> с бо­лее низким содержанием кислорода, азота и водорода, чем при выплавке в индукционных вакуумных печах. Эта повышенная чистота стали и сплавов объясняется тем, что в дуговых вакуум­ных печах нет контакта жидкого металла с огнеупорными мате­риалами футеровки. В этих печах жидкий металл а <a href="/slovar/techenie">течение</a> очень короткого промежутка времени находится в соприкосно­вении лишь со стенками водоохлаждаемого медного <a href="/slovar/kokil">кокиля</a>, в ко­тором он и .затвердевает. Кроме того, весьма высокая температу­ра в зоне электрической дуги благоприятствует <a href="/slovar/dissotsiatsiya">диссоциации</a> нитридов и <a href="/slovar/vosstanovlenie">восстановлению</a> окислов.</font></div>
<div><font size="2">В промышленной практике более широкое применение для по­лучения слитков имеют дуговые вакуумные печи с расходуемым электродом. Естественно, что эти печи предназначены для пере­плава в вакууме сталей и сплавов, выплавленных ранее в других сталеплавильных агрегатах, поэтому дополнительное леги­рование в них практически не осуществляется. Это, 'Конечно, яв­ляется известным недостатком дуговых вакуумных печей с рас­ходуемым электродом.</font></div>
<div><font size="2">На рис. 7 показано устройство лабораторной дуговой вакуум­ной печи, в которой возможно получение слитков диаметром 100—150 мм. В качестве расходуемого электрода использованы штанги длиною 1200 мм и диаметром 60—100 мм. Вес получае­мых стальных слитков составляет 25—75 кг.</font></div>
<div><font size="2">Печь питается постоянным током с отрицательной полярно­стью на электроде. Источником постоянного тока являются два генератора, подключенные параллельно; мощность каждого ге­нератора 60 кет, напряжение 60 в. При параллельном <a href="/slovar/vklyucheniya">включении</a> генераторов возможно подведение тока силою 2000 а.</font></div>
<div><font size="2">Перемещение электрода автоматизировано — во время плав­ки регулятор поддерживает заданную длину дуги.</font></div>
<div><font size="2">Расход электрической энергии в этой небольшой печи на .рас­плавление стальных электродов составляет 800 квт-ч/т. Понижение <a href="/slovar/davlenie">давления</a> в рабочем пространстве печи до 1 * 10-4 мм рт. ст. достигается за счет работы двух бустерных ма­сляных насосов БН-3 (производительность каждого 500 л/сек) и двух форвакуумных насосов ВН-1 (производительность каж­дого 1100 л/мин). Эта печь была использована для переплава шарикоподшипниковой стали, выплавленной в дуговой электрической печи, с целью снижения содержания в стали неметаллических включе­ний.</font></div>
<p> </p>
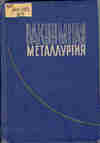
В брошюре кратко изложены методы вакуумной плавки металлов и сплавов, а также способы обработки жидкой стали в вакууме. На основе ряда исследований и практического опыта металлургических заводов СССР приведены сравнительные данные, характеризующие качество металла, полученного методом вакуумирования, и металла, выплавленного по обычной технологии. Изложены проблемы и перспективы дальнейшего развития вакуумной металлургии.