Вакуумная дуговая плавка металлов и сплавов (сборник статей)
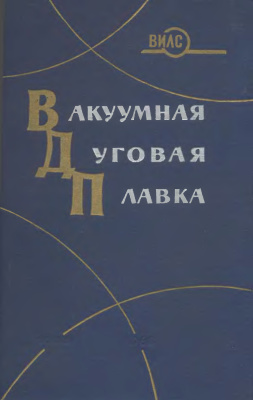
Добаткин В.И. (ред.)
Ордена Трудового Красного Знамени Первая Образцовая типография имени А.А. Жданова, 1968 г.
ВЛИЯНИЕ КАРБИДА ЦИРКОНИЯ НА СТРУКТУРУ И СВОЙСТВА СПЛАВА ЭИ437БУ
В литературе почти отсутствуют данные о влиянии тугоплавких и термодинамически стойких соединений, в частности карбидов, на структуру и свойства никелевых сплавов.
В данной работе были сделаны попытки изыскания методов измельчения структуры, повышения уровня жаропрочности и улучшения механических свойств деформированного сплава ЭИ437БУ. С этой целью в качестве микродобавки (0,1—0,5%) был пробован карбид циркония.
Для выплавки опытных слитков использовали металл открытой плавки, полученный в дуговой печи емкостью 5 т с вовлечением 35% отходов. Расходуемыми электродами служили штанги диаметром 90—100 и длиной 750—800 мм, которые были отпрессованы на горизонтальном прессе 5000 т из заготовок диаметром 230 и длиной 300 мм. Кроме того, в качестве расходуемых электродов были использованы кованые штанги диаметром 90 мм, изготовленные из металла завода «Электросталь». Химический состав сплава открытой плавки и опытных слитков соответствовал ЧМТУ/ ЦНИИЧМ 875—63.
Слитки выплавляли в вакуумных дуговых печах типа ВД-5М в кристаллизаторе диаметром 120 мм. Всего было выплавлено 10 слитков: по два слитка с добавкой карбида циркония 0,1; 0,2; 0,3 и 0,5% и два слитка без добавки.
Карбид циркония, предназначенный для микролегирования сплава, получали в графитовом тигле путем восстановления двуокиси циркония углеродом при нагреве в открытых индукционных печах типа МГП-102 и МГП-252. Размер частиц порошка был менее 0,2 мм. Химический состав порошка по углероду был следующим: свободный углерод—0,25 и общий—12,1%.
Для введения карбида циркония в сплав вакуумного дугового переплава в электродах по образующей были просверлены отверстия диаметром 16 и глубиной 60 мм с шагом 50 мм. Навески карбида циркония засыпали в отверстия и затем уплотняли стружкой того же металла.
Количество углерода в сплаве увеличилось в пределах расчета, но не превышало уровня, предусмотренного ТУ для сплава ЭИ437БУ (табл. I).
время плавки в камере печи колебался от 1,9 до 0,53 я/ж2, а натекание не превышало 20—30 мк рт. ст.л/сек. Масса выплавленных слитков составляла 25—30 кг. Приведенные режимы плавок обеспечивали довольно равномерное распределение карбида циркония и низкое газосодержание по всему объему слитка.
Химический анализ проб, отобранных в различных частях слитка, показал, что содержание циркония в основном находится в заданных пределах и разброс
значении не превышает ошибки анализа.
При изучении макроструктуры на продольных темплетах, вырезанных из слитков, установлено, что добавки карбида циркония не меняют общего характера кристаллического и дендритного строения металла (рис. I).
Измельчения зерен первичных кристаллов не происходит. При исследовании макроструктуры с увеличением в 10 раз также не установлено заметного измельчения дендритов и изменения ориентации зерен по сравнению с обычными слитками дугового переплава. Во всех случаях структура слитков была плотной, без каких-либо внутренних дефектов.
Деформацию слитков проводили по схеме: осадка (10^ 15% по высоте) с последующей вытяжкой в осевом направлении на пруток диаметром 60 мм на 5-т молоте. Общая степень деформации со-
ставляла 65—70%. Температура начала и конца ковки изменялась от 1180 до 950°С.
Макроструктура деформированного сплава в основном однородная по размерам зерен; заметного различия в величине зерна при добавках 0,1 и 0,5% ZrC не обнаружено.
Микроструктуру изучали на образцах до и после термической обработки. Шлифы приготавливали механической полировкой и последующим травлением на структуру в реактиве Круппа. Плоскость шлифов у всех образцов была перпендикулярна направлению деформации.
Дробление литых зерен в процессе ковки происходит в основном по первичным карбидным выделениям, количество и размеры которых заметно увеличиваются по мере возрастания содержания карбида циркония в сплаве (рис. 2).
Микроструктура сплава после деформации характеризуется значительной разнозернистостью (рис. 3). У сплава без добавок и с 0,1% ZrC наряду с большим количеством мелких зерен, соответствующих 6—7 баллу, имеются более крупные зерна — до 3—4 балла. В случае содержания добавки до 0,3% при том же приблизительно количественном соотношении мелких и крупных зерен размеры отдельных крупных зерен значительно больше. В сплаве с 0,5% ZrC преобладают крупные зерна — до 3 балла.
Увеличение в сплаве карбидной фазы подтверждается ростом твердости и микротвердости по границе зерна и по зерну (рис. 4).
Термическая обработка (гомогенизация при 1080° С, 8 ч, охлаждение на воздухе и старение при 760° С, 16 ч) сплава с различным количеством добавок приводит к нивелированию значений микротвердости по зерну и по границе зерна. Карбидная фаза по
сравнению с исходной структурой деформированного сплава заметно измельчается. Разнозернистость микроструктуры сохраняется, но размеры зерен при этом заметно увеличиваются, особенно у сплава без добавок (см. рис. 3).
В табл. 2 приведены средние результаты кратковременных испытаний (3—4 образцов) на растяжение при различных температурах. Эти данные свидетельствуют о том, что прочностные и пластические характеристики сплава с добавками карбида циркония в интервале температур 20—600° С выше, чем у сплава без добавок.
Данные кратковременных испытаний при 20° С показали, что прочностные и пластические характеристики с увеличением количества вводимой добавки несколько улучшаются (см. табл. 3). Так, сплав с содержанием 0,5% ZrC имеет предел прочности и текучести на 10 и 7% выше, чем у соответствующего сплава без добавки; пластические характеристики увеличиваются в среднем на 20—30% у сплавов с добавками 0,1 и 0,5% ZrC.
Наиболее заметное влияние микродобавки карбида циркония оказали на жаропрочность сплава ЭИ437БУ. Испытание образцов на длительную прочность проводили при температуре 750° С
и напряжении 343 Мн/м2 (35 кГ/мм2).
Полученные данные свидетельствуют о значительном повышении длительной прочности (в 2—3 раза) у сплава с добавками карбида циркония. Максимальная жаропрочность была получена на сплаве с добавками О, I и 0,5% ZrC; жаропрочность сплава с 0,3% ZrC несколько ниже, что связано с более значительной разнозернисто- стью микроструктуры, полученной в результате термомеханической обработки. Так, разброс значений времени до разрушения образцов составляет 24—34% для сплава с 0,1% ZrCH70—90% для сплава с 0,3% ZrC. Наиболее одинаковые результаты времени разрушения образцов при длительных испытаниях были получены на сплаве с 0,5% ZrC, имеющего более равномерные размеры зерен микроструктуры.
Приведенные значения времени до разрушения образцов при длительных испытаниях значительно выше, чем у штамповок, полученных из промышленных слитков вакуумного дугового переплава.
По результатам статистической обработки данных 200 плавок вакуумного дугового переплава время разрушения образцов, вырезанных из дисков, составляет 100—130 ч *.
Пластические характеристики (δ, ψ) сплава с 0,1 и 0,5% ZrC при длительных испытаниях увеличиваются на 5—6 и 10—12% соответственно.
В задачу настоящей работы входило выявление механических и жаропрочных характеристик сплава ЭИ437БУ в зависимости от добавок карбида циркония. В дальнейшем эта работа будет продолжена с целью определения оптимального содержания добавок и механизма воздействия карбида циркония на упрочнение сплава.
Выводы
1. Время разрушения образцов при испытании на длительную прочность у деформированного сплава с добавками 0,1; 0,3 и 0,5% ZrC составляет от 170 до 270 ч, что в 2—2,5 раза выше, чем у промышленных изделий металла вакуумной дуговой плавки. Наилучшие результаты по жаропрочности получены у сплава с добавками 0,5% ZrC.
2. Прочностные характеристики сплава с добавками карбида циркония при кратковременных испытаниях (20° С) увеличиваются на 7—10% по сравнению с металлом без добавок, а пластические — на 20—30%. При дальнейшем повышении температуры до 600° С высокие прочностные и пластические свойства сохраняются, превышая свойства исходного сплава на 7—10%.
3. Металлографическое исследование не выявило модифицирующего воздействия карбида циркония на макро- и микроструктуру сплава. Измельчения зерна и дробления дендритов не происходит. Микроструктура характеризуется разнозернистостью с повышенным количеством карбидных выделений.
4. Разброс значений времени до разрушения образцов при длительных испытаниях, особенно у сплава с добавкой 0,3% ZrC, связан с неоднородностью микроструктуры, полученной в процессе термомеханической обработки.