Упрочнение деталей металлургического оборудования
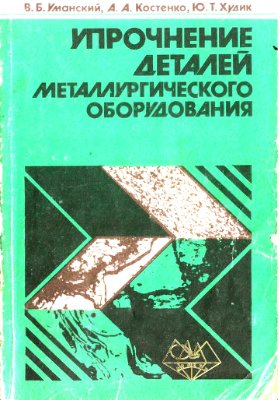
Уманский В.Б., Костенко A.A., Худик Ю.Т.
Металлургия, 1991 г.
НОЖИ ХОЛОДНОЙ И ГОРЯЧЕЙ РЕЗКИ ПРОКАТА
Классификация ножей определяется характером резания, рабочей температурой, видом нагрузки, действующей на ножи, материалом, подвергаемым резке. Эти же факторы определяют стойкость и долговечность ножей. Ножи холодной резки проката во время эксплуатации испытывают значительные напряжения при ударном приложении циклических температурно-силовых нагрузок в сочетании с малой пластической деформацией и износом режущих кромок в условиях сухого трения [31, 57]. Ножи горячей резки проката испытывают динамические нагрузки от ударов разрезаемого металла; при этом в процессе реза отмечается интенсивный износ и пластическая деформация их режущей кромки. Кроме того, рабочая поверхность ножей подвергается многократным нагревам под влиянием высокой температуры разрезаемого раската и охлаждению водой, подводимой к ножу [31]. В настоящее время для изготовления ножей различного типа для холодной резки проката используют в основном инструментальные легированные стали повышенной прокаливаемоети (6ХС, 5ХВ2С, 6ХВ2С [58], 55ХН2Ф, 4XI0C2H[59], 9Х2МФ, 28ХЗСНМВФА [60], 5Х2ГСВМ (ДИ42), 5ХНМ, 5ХНВ [57] и др.). Свойства и структура инструментальных сталей подробно рассмотрены в работах [4, 61] и др.
Из перечисленных выше сталей наибольшее распространение получила сталь 6ХВ2С по ГОСТ 5950-73 для порезки как сортового, так и листового проката. Эта сталь характеризуется повышенной вязкостью, высокой прокаливаемостью в сечениях до 60-70 мм при охлаждении в масле, хорошей закаливаемостью, в том числе и в горячих средах. Легирование вольфрамом повышает ее устойчивость против отпуска [58, 4 и др.] .
Применение сталей типа XI2 для ножей холодной резки нецелесообразно из-за их повышенной карбидной неоднородности, которая при изготовлении поковок для ножей полностью не устраняется даже после электрошлакового переплава. Для холодной резки листового проката успешно используют ножи из стали ДИ42 [57]. На Донецком металлургическом заводе для ножей кромкокрошительных ножниц листового проката широко применяют сталь 5Х2МНФ (ДИ32). На Коммунарском металлургическом заводе применение для гильотинных ножниц стали 20ХЗСНМВФА позволило из-за более высокой вязкости повысить стойкость ножей по сравнению со сталью 6ХВ2С в 2 раза [62].
В работе [63] описан опыт изготовления и эксплуатации твердосплавных плоских ножей для раскроя движущегося рулонного проката. Твердосплавными ножами (твердосплавная пластина прикреплена к стальному корпусу методом пайки) разрезали рулонную сталь толщиной 0,25-0,5 мм на листы длиной 1500 мм. Стойкость твердосплавных ножей относительно стойкости аналогичных стальных ножей повысилась в 30-40 раз и достигла 300-400 тысяч резов между переточками. Стали для ножей горячей резки проката должны обладать следующими качествами [31]:
высокой прочностью и вязкостью, сохраняющимися при разогреве. Ножи не должны изменять форму и разрушаться под действием больших удельных давлений и ударных нагрузок;
удовлетворительной теплопроводностью, чтобы обеспечить быстрый отвод тепла, притекающего на поверхность ножа, и не допускать чрезмерного разогрева рабочей поверхности;
высоким сопротивлением термической усталости, вызываемой многократными нагревами и охлаждениями рабочей поверхности ножа.
Для работы при повышенных температурах рекомендована сталь 4ХВ2ФС (4Х5МК), а для рубки прочных сталей (с повышенным сопротивлением пластической деформация при 500 °С) - сталь 5ХЗВЗМК [4]. Для ножей, работающих в условиях охлаждения водой, рекомендована сталь ЗХЗМЗФ [6].
ДонНИИЧЕРМЕТом [64] разработана для ножей горячей резки проката комплекснолегирсванная низковольфрамовая сталь 4ХЗМ2ВФГС (ДИ41) с повышенной вязкостью, разгаро- и теплостойкостью. Промышленное опробование этой стали показало, что стойкость ножей из нее в 3-5 раз выше стойкости ножей из стали 45, наплавленных сталью ЗХ2В8, и более чем в 2 раза выше стойкости ножей из сталей ЗХ2В8 и 6ХВ2С.
Изготовление ножей горячей резки из сталей 5ХНМ и 6ХВ2С широкого распространения на металлургических заводах не получило из-за недостаточной теплостойкости и прочности, особенно при порезке высокопрочных сталей [58, 4]. Повышение эксплуатационной стойкости ножей из стали 6ХВ2С может быть достигнуто плазменной
наплавкой режущих кромок ножей порошком ПГ-СР4 (ПН70ХГ7С4Р4), в состав которого введена медь и оксид алюминия [65J. Для изготовления ножей рекомендованы стали 5Х2МНФ (ДИ32) [4], 28ХЗСНМВФА (СП28) [64] и др. Промышленное применение ножей из стали ДИ32 для порезки высокопрочных сталей при 800-1000 °С не показало их преимуществ по сравнению с ножами из стали 45,, наплавленной сталью ЗХ2В8.
На металлургическом заводе "Красный Октябрь" проведены промышленные испытания стали 50Х5Н2СМФ, которые позволили рекомендовать ее для ножей горячей резки проката при 600-800 °С [бб].
За рубежом для изготовления ножей горячей резки применяют стали, близкие по легированию к отечественным.
Опыт эксплуатации ножей горячей резки импортного и советского производства на стане 3600 металлургического комбината "Азов-сталь" показал примерно одинаковую эксплуатационную стойкость их. При близких показателях стойкости целесообразно применять стали, подвергаемые термической обработке при более низких температурах нагрева, поскольку отсутствие на заводах оборудования для приготовления защитных атмосфер создает значительные технологические трудности при высокотемпературной обработке.
Стали, применяемые для изготовления ножей холодной резки, подвергают отжигу или отпуску. Сталь 6ХВ2С для сохранения хорошей закаливаемости отжигать нецелесообразно [4, 69]. Для нетеплостойких сталей типа 6ХВ2С, 6ХЗФС и др. целесообразно проводить с целью упрощения обработки или получения более чистой поверхности при резании вместо отжита смягчающий отпуск, тогда твердость может повыситься на НВ 20-30.
По данным работы [69], замена отжига высоким отпуском улучшает обрабатываемость поковок из стали 6ХВ2С на 20-25 %, а стойкость ножей после закалки повышает в 1,5-2 раза.
Стали, применяемые для ножей холодной резки, ю.а.Геллер [4] рекомендует предварительно термически обрабатывать для уменьшения деформации при последующей закалке. Для стали 6ХЗФС предварительная термическая обработка включает закалку при 790-800 °С в масле и отпуск при 520-600 °С (твердость HRC 23-26). Для стали 6ХВ2С температуры закалки и отпуска составляют соответственно 780-790 и 520-580 °С ( HRC 23-25). В этом состоянии стали имеют также более чистую поверхность при резании. В табл. 15 приведены режимы предварительной термообработки некоторых сталей, применяемых для изготовления ножей холодной и горячей резки.
Поковки из сталей 5ХНМ [4], 5Х2МНФ (ДИ32) [61] и 28ХЗСНМВФА (СП28) [62] подвергают высокому отпуску с замедленным охлаждением со скоростью 50 °С/ч до 500 °С, а затем - на воздухе. Стали марок ЗХЗМЗФ и 6ХЗФС отжигают с замедленным охлаждением после выдержки со скоростью 50 °С/ч до 600 °С, затем - на воздухе. Сталь 50X5CM1 после отжига охлаждают до 550 °С со скоростью 40 °С/ч, с печью - до 300 °С, дальнейшее охлаждение проводят на воздухе [66]. Стали марок 4ХЗМ2ВФГС (ДИ41) и 5Х2ГСВМ (ДИ42) после выдержки при температуре отжига замедленно (со скоростью 40 °С/ч) охлаждают до 640 °С, а затем на воздухе.
Для получения требуемых эксплуатационных свойств ножи холодной и горячей резки проката подвергают окончательной термической обработке - закалке и отпуску. В табл. 16 приведены режимы окончательной термической обработки ножей.
В работе [69] показано, что для стали 6ХВ2С оптимальным является режим термообработки: закалка в масле с 960-980 °С и отпуск при 250 °С. Максимальная стойкость ножей холодной резки, обработанных по этому режиму, для порезки полосового проката из рессорной стали 50хга повысилась в г,5-2 раза по сравнению с обработанными по другим режимам. Стойкость ножей из легированных сталей для резки полосового, квадратного и круглого проката повысилась в 3-3,5 раза. В то же время,ножи из стали 6ХВ2С, закаленные с 960-980 °С и отпущенные 1дри 350 °С, что рекомендуется в работе [58], имели минимальную стойкость. Причиной их выхода из строя является выкрашивание рабочих кромок, а в ряде случаев и поломка ножей. Это можно объяснить "провалом" ударной вязкости при этой температуре [4, 69].
Стали, применяемые для изготовления ножей холодной и горячей резки, требует посадки при температуре 600-800 °С в печь и замедленного нагрева (со скоростью до 100 °С/ч) до температуры нагрева под закалку. Особое внимание следует обратить на защиту поверхности ножей от обезуглероживания и окисления. Наиболее надежным средством защиты являются защитные и контролируемые атмосферы. Опыт применения эндогаза в электрических печах типа СНЗ для нагрева под закалку и отжиг на Донецком металлургическом заводе показал, что в этом случае обезуглероживания и окисления практически не происходит.
Стойкость ряда деталей, применяемых для ножей холодной резки, можно повысить, применяя вместо непрерывной закалки изотермическую. Изотермическая закалка целесообразна для ножей, обрабатываемых на твердость HRC 45-55. Сталь приобретает бейнитную структуру и повышенное количество остаточного аустенита, что обеспечивает повышение вязкости по сравнению с получаемой в результате непрерывной закалки и отпуска на ту же твердость [4].
По данным работы [70], изотермическая закалка с 980-1000 °С з горячий расплав смеси солей состава: 55 % калиевой селитры и 45 % нитрида натрия при 250-275 °С дает вязкость (твердость HRC 50-56), в 2 раза превышающую вязкость после закалки на мартенсит и отпуска на ту же твердость.
На Днепровском металлургическом комбинате им. Дзержинского стойкость ножей холодной резки из стали 6ХВ2С после изотермической закалки с 880-900 °С в расплав смесей (45 % натриевой селитры + 55 % нитрида натрия) с добавлением 3-5 %' воды при 250 °С (твердость HRC 52-55) повысилась в 2-2,5 раза по сравнению со стойкостью после закалки в масле и отпуска на ту же твердость. Однако повысить эксплуатационную стойкость ножей из стали 6ХВ2С путем ступенчатой закалки с 960 °С в расплав солей при 210 °С