Управление процессами затвердевания слитка спокойной стали
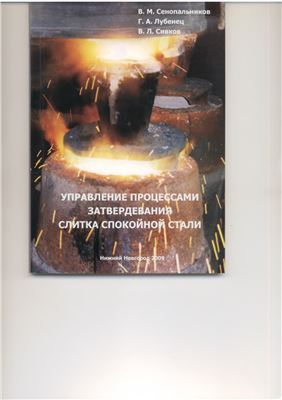
Сенопальников В.М., Лубенец Г.А., Сивков В.Л.
Нижегород. гос.техн. ун-т. , 2009 г.
АНАЛИЗ СУЩЕСТВУЮЩИХ МЕТОДОВ ПОВЫШЕНИИ ОДНОРОДНОСТИ СТАЛЬНЫХ СЛИТКОВ И ВЫБОР НАПРАВЛЕНИЙ ИССЛЕДОВАНИЙ
В настоящее время повышение однородности стальных слитков, отливаемых в изложницы, достигается:
- рафинированием жидкого металла по газам, неметаллическим включениям и ликвирукщим примесям и корректировкой его состава;
- оптимизацией геометрических размеров слитков;
- улучшением работы прибыли;
- применением внешних воздействий на процесс кристаллизации.
Повышение качества жидкого металла ведется применением при выплавке чистых исходных материалов обработки стали в ковше синтетическими шлаками и порошкообразными реагентами, использованием различных методов вакуумирования и ковшевой металлургии (АСЕА-СКФ, ФИНК и другие процессы) [62, 63]. Эти методы весьма материально и энергетически затратны, но обеспечивают значительное повышение химической однородности литого металла. Так, сравнительные исследования двух слитков массой 147 т показали существенное улучшение макроструктуры и снижение ликвации, в том числе и легирующих элементов, при снижении содержания примесей в хромникельмолибденовой стали[64]. В тоже время ликвационные шнуры в крупных слитках проявляются даже при крайне низких содержаниях примесей [65, 66]. Практические результаты глубокого рафинирования металла по сере показывают, что этим методом добиться устранения внецентренной ликвации нельзя дефект проявляется в виде «белых шнуров» [47, 67], не выявляемых на Баумановских отпечатках, но обнаруживаемых при травлении.
Перспективным методом является технология вакуумно-углеродного раскисления (ВУР) стали с низким содержанием кремния [29, 68 - 71], обеспечивающая, наряду с низким содержанием водорода и кислорода в металле, существенное повышение физико-химической однородности слитков из хромникельмолибденванадиевых сталей. В тоже время сравнительные исследования поковок роторов, полученных по различным вариантам технологии, показывают, что металл ВУР уступает по качеству металлу со сверхнизким содержанием серы (0,001 - 0,002%) [68]. Видимо, с учетом этого технология ВУР применяется в Японии для производства самых крупных в мире слитков массой до 570 т из стали, выплавленной с применением чистых по примесям исходных материалов [69].
Корректировка химического состава стали применяется при многоковшевой заливке крупных слитков в вакууме. В работах [67, 72] утверждается, что отливка слитков порциями стали с последовательным снижением содержания углерода в каждой, является эффективным способом уменьшения ликвации этого элемента по высоте заготовки. Однако этому противоречат результаты исследования опытного слитка массой 290 т (гл. 2), а также экспериментов по данным [10].
МР-процесс (Multi Pouring), или МКД-процесс - многоковшевая заливка слитка с одновременным ВУР и дифференцированием содержания как углерода, так и легирующих элементов в каждой заливаемой порции позволила существенно снизить уровень развития ликвации в поковке ротора генератора из слитка массой 500 т [73]. При этом изменение содержания элементов от первого до последнего ковша составляло: углерода - 0,15%, марганца - 0,10%, никеля - 0,30%, хрома - 0,45%, молибдена - 0,35%, ванадия - 0,10%.
Технологии ВУР и МР имеют ограниченное распространение и применяются только для производства крупных заготовок уникальных изделий из хромникельмолибденванадиевых сталей.
Оптимизация геометрических размеров слитков особенно характерна для производства кузнечных заготовок. Уменьшение отношения высоты к среднему диаметру(НЛЭ) и повышение обратной конусности при изготовлении таких слитков существенно снижает развитие отрицательной сегрегации и V-образной неоднородности [14, 74]. Так, изменение H/D для слитков массой 20-22 тс 1,82 до 1,63 и повышение конусности изложницы с 4,7 до 9,5% привело к снижению высоты зоны отрицательной ликвации с 720 до 320 мм. В слитках массой 51-52 т в придонной области выявлены две зоны отрицательной ликвации углерода – внутренняя (более обедненная примесями) и охватывающая её внешняя! 14]. При изменении конусности слитка с 3,6 до 8,6% (при незначительном снижении Η/D с 1,74 до 1,7) высота внутренней зоны существенно уменьшилась, в то время как высота внешней практически не изменилась.
Увеличение конусности до 12% при H/D =1,5 повысило плотность осевой зоны крупного слитка, но не привело к полному устранению дефектов усадочного происхождения [10, 75, 76]. ЦНИИТМАШ совместно с Ижорским заводом создали конструкцию слитка с H/D =0,8-1,3 и конусностью 16%[76]. Это полностью решило проблемы плотности осевой зоны сверхкрупных слитков при увеличении объема прибыли с 17-20 до 22 - 28% (см. гл.2). Однако увеличение диаметра литой заготовки ведет к усилению развития внеосевой неоднородности.
Улучшение работы прибыли слитка позволяет снизить развитие дефектов усадочного происхождения в осевой зоне и может быть достигнуто за счет повышения теплоизолирующих свойств и толщины футеровки надставки, использования экзотермических смесей, теплоизолирующих засыпок и крышек, а также с помощью обогрева от внешних источников энергии.
Увеличение зоны теплового влияния прибыли усиливает температурный градиент по высоте слитка и существенно влияет на плотность его осевой зоны. Для листовых и сортовых слитков, конусность которых определяется возможностями прокатного оборудования и не превышает, как правило, 4%, улучшение тепловой работы прибыли является наиболее распространенным методом физической однородности осевой зоны.
Из применяемых способов самым простым и достаточно эффективным является теплоизоляция зеркала металла в головной части. По данным [77], в тепловом балансе прибыли слитка массой 3,7 т при теплоизоляции зеркала металла резко изменяются две статьи: уменьшаются тепловые потери в атмосферу(4,4 против 39%) и заметно возрастает передача тепла в тело слитка(31 против 3,8%). Показательным примером возможности повышения качества крупных литых заготовок за счет улучшения работы прибыли является отливка слитка массой 235 т (при H/D =1,7, конусности 13,5% и объеме прибыли 21,5%) на Ижорском заводе[75]. Слиток был получен без усадочных дефектов за счет использования засыпки зеркала металла вермикулитом, футерованной крышки и улучшенной теплоизоляции надставки. Однако в удлиненных слитках теплоизоляция прибыли снижает V- образную неоднородность за счет увеличения протяженности «моста», но не устраняет её.
Обогрев прибыли экзотермическими смесями эффективен при продолжительности их горения, близкой к времени затвердевания слитка[78].
Дальнейшее улучшение качества слитков, отливаемых в чугунные изложницы, может быть достигнуто путем электроподогрева прибылей. Эти процессы целесообразны при производстве крупных слитков для изделий ответственного назначения. Возможные технологические варианты - электродуговой[79], индукционный [78] и электрошлаковый подог- рев[80].
Индукционный обогрев прибылей - самый эффективный в энергетическом отношении способ, не нашел промышленного применения в связи со сложностью оборудования для его реализации[78, 80].
Элекродуговой подогрев прибыли с последующей её доливкой вакуумированной сталью по ходу затвердевания(УРР - процесс, Чехия), применяется при производстве крупных кузнечных слитков[81].
Наибольшее распространение получил процесс электрошлакового подогрева(подпитки) прибыли(ЭШГТП). В СССР и России эта технология, несмотря на солидную историю(первые публикации относятся к 1958 г. [82]) нашла лишь ограниченное промышленное внедрение. Одним из вариантов ЭШПП является процесс электрошлаковой разливки(ЭШР), разработанный на заводе «Элекростальтяжмаш» и совмещающий разливку стали через жидкий рафинирующий шлак в чугунную изложницу и обогрев прибыльной части двумя фафитированными электродами[83, 84]. В слитках ЭШР отмечено существенное снижение загрязненности неметаллическими включениями и степени развития макроликвации.
В Австрии (БЭСТ - процесс), Италии (ТРЕСТ - процесс) и Японии (ESHT-j - процесс) ЭШПП достаточно широко используется при производстве крупных кузнечных(массой более 60т) и листовых(более 30т) слитков[76, 85 - 93]. Практическое применение электрошлакового подогрева в сравнении с традиционной технологией обеспечило резкое повышение качества слитка, приближая его по чистоте металла по неметаллическим включениям, по химической неоднородности, по развитию осевой и внеосевой неоднородности к слитку электрошлакового переплава В сравнении с ЭШП эти способы требуют меньших материальных и энергетических затрат. Так, по данным [87], стоимость 50-тонных слитков, полученных по БЭСТ-процессу, в три раза ниже стоимости аналогичных по массе электрошлаковых слитков, а при производстве БЭСТ-слитков массой более 70 т их стоимость становится ниже стоимости металла обычной разливки.
Процессы ЭШПП обеспечивают последовательность вертикального затвердевания слитка, уменьшение протяженности двухфазной зоны за счет повышения градиента температуры в затвердевающем слитке и позволяют полностью устранить V- образную неоднородность. Однако, как показала практика, способы специальной электрометаллургии не могут обеспечить полного подавления шнуровой и отрицательной ликвации[36, 66].
Методы внешнего воздействия на процесс кристаллизации, в отличие от рассмотреных выше технологических приемов активно влияют на развитие в слитке конвективных и двухфазных потоков.
Одним из таких способов является продувка расплава инертным газом в изложнице. Б.Б.Гуляев в работе [94] указывал, что продувка стали при затвердевании газом предотвращает образование «усов» даже при резком усилении других форм ликвации. Этот процесс реализуется путем продувки жидкого металла газами снизу через поддон или сверху, с помощью погружаемой фурмы, и получает все более широкое распространение [95]. Продувка жесткими струями аргона слитков массой 3 и 10 т привела к измельчению первичной структуры в 5-10 раз, снизило развитие А- и V- образных форм зональной ликвации, содержание водорода и кислорода (на 20-30%) и неметаллических включений[96]. В.А.Ефимов рассматривает эту технологию как способ эндогенного «суспензионного» литья и, на основании проведенных Ю.Я.Скоком экспериментов, указывает на перспективность совмещения этого процесса, с десульфурацией и модифицированием стали комплексными сплавами. При этом отмечает, что при превышении доли твердой фазы в эндогенной «суспензии» более 30%, существует вероятность получения пористой осевой зоны слитка [95]. На значительное влияние режима обработки указывают и результаты исследований, в соответствии с которыми продувка металла в изложнице аргоном через пористый блок в период отливки слитков привела к усилению их химической неоднородности и в том числе внеосевой ликвации [97].
Газоимпульсная обработка(пневмоосциллирование) приводит к нарушению конвективных и двухфазных потоков в затвердевающих заготовках. Сущность этой технологии заключается в принудительном возмущении внутренних объемов жидкого металла упругими колебаниями частотой 0,05-2,5 Гц, создаваемыми за счет изменения давления аргона в огнеупорной трубе, погруженной одним концом в расплав. При использовании этого процесса было достигнуто снижение степени развития внеосевой неоднородности в слитках массой 19,5 и 23 т в 3-5 раз. Одновременно уменьшилась положительная ликвация в подприбыльной части слитка на 25-30%. Эти результаты были обеспечены при мощности перемешивания 7-8 Вт/т и скорости потока, исходящего из осциллятора, 0,3м/с [99]. В процессе экспериментов было установлено, что начало проявления внеосевой неоднородности в слитках, отлитых с газоимпульсной обработкой, совпадает с положением границы затвердевания в момент окончания воздействия[100].
Магнитогидродинамическое воздействие(МГДВ) на затвердевающий расплав, нашедшее широкое применение при непрерывной разливке стали, для повышения однородности слитков, отливаемых в изложницы, в промышленных масштабах в нашей стране до настоящего времени не используется. Одной из причин являются трудности в реализации данного способа при наличии чугунной оснастки, экранирующей электромагнитное поле. Такое решение, как использование в качестве материала изложниц немагнитных сплавов [101], привело бы к замене всего парка изложниц, и использование его мало вероятно. В этом плане более перспективным представляется магнитодинамическое воздействие на расплав в объёме прибыльной части слитка, как, например, при индукционном подогреве прибыли, обеспечивающем интенсивное перемешивание расплава во всём объёме затвердевающего слитка [78]. Однако индукционное воздействие требует сложного оборудования, эксплуатация которого в разливочных пролётах сталеплавильных цехов затруднена. В связи с этим ведутся работы в направлении применения кондукционного (кондуктивного) метода МГДВ на расплав, осуществляемого за счет силового взаимодействия скрещенных электрического и магнитного полей. Перспективность этого метода отмечает Г.Ф.Баландин [8].
Разработаны различные схемы кондукционного воздействие для непрерывной разливки [102], ЭШП [103] и отливки слитков в стационарные изложницы [104]. Результаты внедрения и экспериментальных исследований в этих направлениях дали противоречивые результаты. Обработка слябов на МНЛЗ скрещенными постоянными электрическим и магнитным полями обеспечила повышение однородности металла, как по сравнению с обычной разливкой, так и с разливкой с индукционным воздействием [102]. Исследования по электромагнитному перемешиванию металлической ванны при ЭШП показали, что происходит ускоренное оплавление расходуемого электрода при неизменной мощности, вводимой в шлак и, соответственно, углубление жидкой лунки, причём последний процесс ведет к усилению ликвационных явлений [103]. Физическим моделированием МГД - воздействия на кристаллизацию слитка в изложнице было установлено, что интенсификация естественной конвекции приводит к выводу растворимой примеси из объема слитка в его прибыльную часть [105]. Однако эксперименты по отливке слитков массой 1250 кг из легированной стали с кондукционным перемешиванием кристаллизирующегося расплава не показали значительного изменения качества металла [106]. МГДВ на слиток в этом случае осуществляли в изложнице из немагнитного чугуна, вокруг которой(на всю её высоту) был размещен соленоид. Токоподвод к расплаву осуществляли через поддон и электрод, помещенный в прибыль.
Приведенные данные показывают, что методы воздействия на конвективные и двухфазные потоки в затвердевающем слитке способствуют подавлению развития ликвационных дефектов только при оптимальных режимах.
Из изложенного следует, что в настоящее время отсутствуют универсальные технологии, позволяющие полностью устранить физическую и химическую неоднородности в стальных слитках.