Ультразвуковой контроль материалов. Справочник.
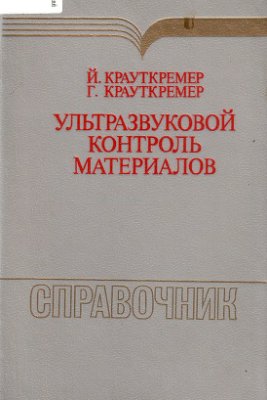
Крауткремер Й., Крауткремер Г.
Металлургия, 1991 г.
Учение о звуке — акустика — описывает процессы механических колебаний и их распространение в твердых, жидких или газообразных веществах. В пустом пространстве не может быть звука, потому что пет материальных частиц — проводников колебаний — в противоположность, например, световым или высокочастотным колебаниям, при которых колеблется электрическое и магнитное состояние пространства самого по себе. Звуковая волна в воздухе выводит небольшой объем воздуха из состояния покоя и перемещает его возвратно-поступательно, тогда как световая волна не влияет на характер движения пространства.
Если охарактеризовать такие механические движения в материн, которые регулярно повторяются по крайней мере в течение небольшого отрезка времени, т. е. являются периодическими, числом периодов в секунду, то можно будет выделить область частот, в которой звук выявляется человеческим ухом: мы слышим звук, когда он проходит через воздух или через наше тело к нашему уху и когда его частота не слишком низка и не слишком высока. При частоте ниже чем ~10 Гц (число колебаний в секунду) мы не слышим звука, и при частоте, превышающей —15—20 тыс. Гц, тоже не слышим. (Впрочем, первое утверждение правильно только в том случае, если речь идет о синусоидальном колебании. Другие формы колебаний ухо раскладывает на обертоны, в результате чего колебание получается слышимым в виде последовательности тонов и щелчков или хлопков, т. е. треска.)
По аналогии с тем как в области световых волн, уже не воспринимаемых нашим глазом, повышенные частоты называют ультрафиолетовым излучением, звуковые волны с частотой более 20 000 Гц (20 кГц) называют ультразвуком. В соответствии с этим для звуковых частот ниже 10 Гц предложено наименование инфразвук. Это разделение произвольно привязано к особенностям человеческого уха. При других методах обнаружения и получения звука будут совершенно другие пределы.
Ультразвуковые волны встречаются в природе и в обыденной жизни довольно часто и иногда имеют такую интенсивность, что отсутствие дополнительной нагрузки от них на человеческое ухо можно считать за счастье; таков, например, шум от паровых гудков и турбин авиационных двигателей. Вращающийся шлифовальный круг при обработке деталей излучает кроме слышимого шума еще и интенсивные ультразвуковые волны, причем в области высоких частот, используемых для испытаний материалов, а именно примерно от 100 кГц до 10 МГц и более.
Многочисленные применения звуковых и ультразвуковых волн в технике можно подразделить на две группы, как и в медицине, где лучевые способы используют для двух различных целей:
с терапевтической целью (чтобы вызвать длительное изменение состояния вещества, например при облучении раковых опухолей)
и с целью диагностики (для выявления определенного состояния вещества, например при рентгеновском просвечивании легких).
В технике энергию звуковых волн используют, например, для выбрасывания частиц грязи из волокон ткани при стирке, для отделения посторонних частиц от поверхности изделия при очистке, для преодоления сил поверхностного натяжения при эмульгировании, для перемешивания и для многих других целей как механическую энергию1.
В других случаях энергию звуковых волн используют при передаче какого-либо явного сигнала, например при передаче звука через громкоговоритель, при решении задач по локации и измерению глубины па море, а также для испытания материалов с целью выявления их состояния, т. е. для проверки на отсутствие дефектов или для определения их упругих свойств и других характеристик металла. Звуковая волна используется как носитель информации о состоянии вещества. Чтобы получить эту информацию, обычно бывает нужно послать волну в изделие и снова принять волну, вышедшую из изделия. В тех случаях, когда звуковой сигнал генерируется в самой детали, например в металлах или композиционных материалах под нагрузкой на растяжение или сжатие, говорят об излучении звука изделием.1
В предлагаемой книге рассматривается диагностическое применение ультразвуковых волн с целью испытания материалов.
Для выявления механических свойств какого-либо вещества (материала) механический метод является прямым и наиболее естественным. Чтобы выявить трещину в оси, можно нагружать эту ось на растяжение или изгиб до тех пор, пока трещина не вызовет разрушения. Это, однако, будет разрушающим способом испытания. Напротив, звук и ультразвук позволяют применить неразрушающие способы контроля, при которых хотя тоже действуют механические силы, но эти силы растяжения, сжатия, среза или изгиба настолько малы, что они не вызывают повреждения материала.
Сказанное не означает, что какой-либо косвенный способ, например магнитный, по выявлению силовых линий, образующихся около трещины, в конкретных случаях не может оказаться более эффективным для обнаружения трещин. Существенно, что взаимосвязь между показателем механического свойства изделия и примененным средством испытания (магнетизмом, электричеством, излучением и т. п.) должна быть однозначной.
Если отвлечься от ограничивающей приставки «ультра», то звук уже давно применяется для испытания материалов: грубые внутренние дефекты в поковках и отливках можно легко выявить по измененному звучанию при ударе молотком. Любая домашняя хозяйка знает, что трещину в чашке или тарелке, если она есть, можно выявить по звуку. Известно, что уже сами изобретатели керамики пользовались этим способом контроля. Звуковой контроль поэтому можно считать одним из старейших способов неразрушающего контроля изделий для выявления невидимых дефектов.
Теперь эта старая техника контроля по анализу звучания возрождается применительно к самым современным материалам — пластмассам, композиционным материалам и материалам, армированным волокном, разумеется с привлечением современных электронных вспомогательных средств.
Разработка способа ультразвукового контроля материалов была осуществлена только в последние 50 лет, после того как были созданы все существенные предпосылки для его технического применения;]
Хотя Спалланцани еще в 1779 г. предполагал, что летучие мыши ориентируются при помощи неслышимых для нас звуковых сигналов (обнаружить эти сигналы сумели только Пирс и Гриффин в 1938 г.), решающие факторы заключались в том,, что
Жак и Пьер Кюри в 1880—1881 гг. обнаружили обратимый пьезоэлектрический эффект [281, 282], что позволило использовать кварц как преобразователь электрических колебаний в звуковые;
лорд Рэлей уже в 1885—1910 гг. [31] разработал теорию распространения звука в твердых веществах;
была известна идея эхо-импульсного способа (впервые его применили Лангвэн и Шиловски с пьезоэлектрическими преобразователями в водной среде в 1915—1917 гг. [89];
разработка электронных конструктивных элементов быстро продвигалась вперед благодаря развитию радарной техники.
Первые дефектоскопы, работающие на непрерывном звуке, создали еще в 1929 г. С. Я. Соколов [1446] и в 1931 г. Мюльхойзер [1071]. Наши теперешние эхо-импульсные дефектоскопы (принцип действия и прибор) создали впервые в 1939— 1942 г. Файрстон в США [454], Спрулс в Великобритании [313] и Крузе в Германии [862]; по этим вопросам имеется и другая литература [15, 558, 991, 990, 862]; исторический обзор приводится в разделе 9.2.
Примерно с 1950 г. преобладающим в технике ультразвукового контроля является эхо-импульсный способ, применяемый преимущественно в следующих областях:
на транспорте для контроля катящегося и летающего оборудования и самих дорожных средств (рельсов);
в металлургическом производстве для контроля литых, кованых и катаных изделий;
в судостроении и при производстве стальных конструкций для контроля заготовок и их соединений;
в автомобилестроении и самолетостроении для контроля деталей привода, ходового механизма и рулевого управления, сварных, паяных и клеевых соединений;
при производстве пластмасс для измерения толщины стенки и для контроля сварных и клеевых соединений;
в машиностроении и в электротехнической промышленности для испытания заготовок, для контроля сварных, паяных и клеевых соединений, а также для контроля допусков на изготовление;
на электростанциях всех родов для приемо-сдаточного и текущего контроля (инспектирования) сосудов и трубопроводов, работающих под давлением и при повышенных температурах, для наблюдения за работой турбин и генераторов;
в химической промышленности для контроля продукции и для наблюдения за деталями агрегатов, опасными по коррозии;
в научно-исследовательских лабораториях для определения свойств твердого тела и молекулярных свойств.