Ультразвуковая дефектоскопия.
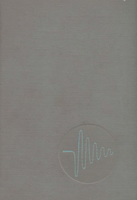
Д.С.Шрайбер.
Array, 1965 г.
Ультразвуковой контроль металлических заготовок, полуфабрикатов и изделий
Практика отечественной и зарубежной ультразвуковой дефектоскопии показывает, что возможности ее весьма широки, однако, чтобы получить нужный эффект, следует к каждой конкретной задаче подходить с учетом всех данных о свойствах материала, технологии изготовления контролируемого изделия, характере и размерах возможных дефектов.
При таком подходе, даже с помощью обычных дефектоскопов промышленных типов, часто оказывается возможным решение задач, считавшихся до недавнего времени неразрешимыми,
а. Контроль литья
Принято считать, что для контроля фасонного литья ультразвуковые методы контроля неэффективны. Действительно, сложная форма отливок, плохое качество поверхности, крупнозернистая структура, различие в величине зерна между сердцевинной и периферийной зонами в толстых сечениях, различие в величине зерна между толстыми и тонкими сечениями — все это сильно затрудняет контроль и практически исключает возможность его автоматизации. Если к тому же добавить, что трещины, выходящие на поверхность отливки, могут быть обнаружены капиллярными и иногда — магнитными методами, то для обнаружения одних лишь внутренних дефектов использование ультразвуковых методов следует признать экономически малоэффективными. Однако если для фасонных отливок из легких сплавов для этой-цели можно применять просвечивание рентгеновскими лучами, то стальные и чугунные отливки значительной толщины просвечиваются уже с трудом.
Стальное литье (в том числе трубы, отлитые центробежным способом) можно контролировать при толщине да 50—80 мм. При этом можно использовать продольные и сдвиговые УЗК, вводимые под острым углом к поверхности изделия. В последнем случае из-за плохого качества поверхности лучший акустический контакт получается, если тело искательной головки вместо органического стекла выполнить из резины.
Можно также измерять и толщину стенок чугунных и стальных отливок, если искательную головку снабдить пьезоэлементом высокой чувствительности с малой контактной поверхностью.
Все же более эффективным по сравнению с контролем фасонного литья является использование ультразвуковых методов для контроля слитков, подлежащих обработке давлением, с целью обнаружения в них грубых дефектов. Для таких слитков из различных металлов и сплавов, предназначенных для изготовления полуфабрикатов и изделий ответственного назначения, обычно характерны относительно крупные габариты, несложная форма (цилиндр, прямоугольный параллелепипед), весьма неровная поверхность и грубозернистая структура. Последняя, особенно в слитках из металлов, обладающих значительной упругой анизотропией, приводит к сильному затуханию УЗК из-за рассеяния их зернами металла и к высокому уровню структурной реверберации.
Стальные слитки могут быть прозвучены на глубину около 1 м на частоте 0,25 Мгц. Однако, чтобы более точно определить координаты дефектов, лучше там, где это возможно, использовать частоту 0,5 Мгц. В ряде случаев условия контроля улучшаются после применения гомогенизирующего отжига слитков.
Слитки из легированной стали прозвучиваются значительно хуже из-за сильного затухания УЗК. Слитки из алюминиевых и титановых сплавов могут быть проконтролированы на частотах 0,5—1,5 Мгц на глубину свыше 1 м. Слитки из циркония и молибдена диаметром до 300 мм и высотой до 1 м хорошо прозвучиваются на частоте 1 Мгц, а небольшие слитки из гафния — на частоте до 5 Мгц. Вольфрамовые слитки отлично контролируются на частотах до 5 Мгц при высокой чувствительности, так как упругая анизотропия у вольфрама отсутствует и структурной реверберации нет. Упругая анизотропия сильно затрудняет контроль слитков из никелевых сплавов, латуни, бронзы (здесь сказывается также и сильное затухание УЗК).
В большинствеслучаев поверхность слитковиз легких и специальных сплавов подвергают обработке перед пластической деформацией. Поэтому во многих случаях можно применятьконтактный эхо-метод. Более надежно, однако, использовать иммерсионный, а иногда — струйный контакт. Прозвучивание плоских слитков удобно вести путем сканирования строчками в направлении толщины слитка. Прозвучивание цилиндрических слитков можно осуществлять либос торцовой поверхности вдоль оси, либо, что надежнее,— со стороны боковой поверхности вдоль диаметра. При этом, поскольку угол расхождения УЗК большой, не требуется сканирования по винтовой линии. Достаточно провести головку 4—6 раз вдоль образующей цилиндра, поворачивая слиток после каждого прохода на 90—60 град. Таким образом может быть достигнута достаточная производительность контроля. Грубые горячие трещины при таком контроле обнаруживаются вполне надежно
Хорошо обнаруживаются также раковины и зоны рыхлоты. При обнаружении раковин в слитках из металлов, выплавляемых в нейтральной или восстановительной атмосфере, следует учитывать, что внутренние поверхности таких раковин не окислены и при дальнейшей обработке давлением могут завариться. Такие раковины не являются браковочным признаком. Отбраковка же слитков, содержащих грубые трещины, позволяет повысить качество полуфабрикатов, получаемых в процессе дальнейшей деформации,
б. Контроль поковок
Контроль поковок (особенно крупногабаритных) — одно из наиболее эффективных применений ультразвуковой дефектоскопии. Заготовки роторов турбогенераторов, имеющие диаметр около полутора метров и весящие десятки тонн, заготовки крупных штампов («кубики»), имеющие вес того же порядка, заготовки дисков турбин и компрессоров для газотурбинных двигателей, поковки из легких сплавов для деталей самолетов могут быть проконтролированы ультразвуковыми методами на наличие флокенов, ликвационных скоплений, зон рыхлоты, остатков усадочных раковин, шлаковых, неметаллических и инородных включений, ковочных трещин, внутренних разрывов, расслоений, окисных плен, зон крупнозернистости и т. п. Структура металла поковок значительно отличается от структуры слитка, поскольку металл претерпел некоторую деформацию. Зерна металла поковки вытянуты в направлении течения, что определяет ориентировку многих дефектов.
Не менее эффективен контроль заготовок для крупных штампов. Эти заготовки, вес которых доходит до нескольких десятков тонн, изготавливают из специальных сталей, легированных дефицитными металлами, и подвергают весьма сложной и дорогой машинной и ручной обработке для изготовления «фигуры» штампа.