Твердые сплавы для обработки металлов резанием
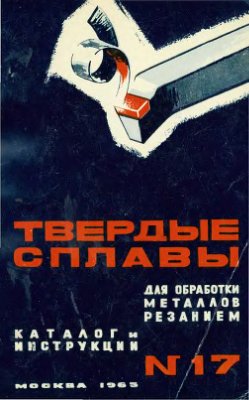
Яншин С.И (ред)
Издательство: ВНИИТС, 1965 г.
Металлокерамические твердые сплавы, выпускаемые в Советском Союзе подразделяются на три группы:
- группу вольфрамовых твердых сплавов, состоящих из зерен карбида вольфрама, сцементированных кобальтом;
- группу титановольфрамовых твердых сплавов, состоящих из зерен твердого раствора карбида вольфрама в карбиде титана и избыточных зерен карбида вольфрама, сцементированных кобальтом, или только из зерен твердого раствора карбида вольфрама в карбиде титана, сцементированных кобальтом;
- группу титанотанталовольфрамовых твердых сплавов, состоящих из зерен твердого раствора карбид титана — карбид тантала — карбид вольфрама и избыточных зерен карбида вольфрама, сцементированных кобальтом.
Вольфрамовая группа твердых сплавов предназначается для обработки чугуна, цветных металлов и их сплавов и неметаллических материалов. Титановольфрамовая группа сплавов предназначается для всех видов обработки сталей. Назначение титанотанталовольфрамовых сплавов — особо тяжелые случаи обработки сталей.
Каждая группа твердых сплавов подразделяется в свою очередь на марки, различающиеся между собой по химическому составу и физико-механическим и эксплуатационным свойствам.
Некоторые марки сплавов, имея одинаковый химический состав, отличаются размером зерен карбидных составляющих, что определяет различие их физико-механических и эксплуатационных свойств, а отсюда и областей их применения.
Вольфрамовая группа твердых сплавов содержит 14 марок, титановольфрамовая — 5 марок и титанотанталовольфрамовая группа — 1 марку сплава.
Титановольфрамовую марку твердого сплава Т5К12В и титанотанталовольфрамовую марку ТТ7К12 называют еще марками сплавов «промежуточного» типа. Называются они так потому, что по своим режущим свойствам эти сплавы находятся между быстрорежущей сталью и маркой твердого сплава Т5К10, предназначенной для черновой обработки сталей, заполняя пробел по прочности и износостойкости между этими видами инструментальных материалов.
Свойства марок твердых сплавов рассчитаны таким образом, чтобы выпускаемый ассортимент мог в максимальной степени удовлетворить потребности, могущие возникнуть в современном производстве.
Правильный выбор марок твердых сплавов для выполнения той или другой работы чрезвычайно важен и является одним из основных факторов, обеспечивающих получение надлежащей эффективности от применения твердых сплавов.
При выборе марки сплава следует учитывать:
- Физико-механические и эксплуатационные свойства твердых сплавов;
- Характеристику обрабатываемого материала;
- Вид и условия обработки;
- Характер требований, предъявляемых к точности, обработанных поверхностей;
- Состояние станка и его кинематические и динамические данные.
В помещаемых ниже таблицах приводятся данные о химическом составе и физико-механических свойствах твердых сплавов в соответствии с ГОСТ 3882—61, сравнительных эксплуатационных свойствах марок сплавов и рекомендации по выбору стандартных марок твердых сплавов для различных видов обработки резанием металлов и неметаллических материалов.
При ознакомлении с номенклатурой марок твердых сплавов нужно иметь в виду, что обозначение марок в Советском Союзе построено по следующему принципу: Марки сплавов вольфрамовой группы, содержащие карбид вольфрама и кобальт, обозначаются буквами ВК, после которых цифрами указывается процентное содержание в сплаве кобальта. Таким образом, например, сплав ВК6 содержит 6% кобальта и, следовательно, 94% карбида вольфрама. Кроме того, в этой группе к обозначению крупнозернистых марок твердых сплавов (величина зерен 3—5 мк) добавляется буква В, например, ВК6В, а к обозначению мелкозернистых марок сплавов (величина зерен 0,5—1,5 мк) — буква М, например, ВК6М.
Сплавы титановольфрамовой группы, имеющие в своем составе карбид титана, карбид вольфрама и кобальт обозначаются буквами ТК, причем после буквы Т указывается цифрами процентное содержание карбида титана, а после буквы К — содержание кобальта. Например, сплав Т15К6 содержит 15% карбида титана, 6% кобальта и остальное, т. е. 79%, карбида вольфрама.
Сплавы титанотанталовольфрамовой группы, содержащие кабриды титана, тантала и вольфрама, а также кобальт, обозначаются буквами ТТК, причем после букв ТТ указывается суммарное процентное содержание карбидов титана и тантала, а после буквы К — процентное содержание кобальта. Таким образом сплав ТТ7К12 содержит 7% карбидов титана и тантала, 12% кобальта и остальное, 81%, — карбида вольфрама.
ЗАВИВАНИЕ И ЛОМАНИЕ СТРУЖКИ
Для завивания и ломания стружки применяются следующие способы;
образование на передней поверхности инструмента канавок;
образование на передней поверхности инструмента уступов;
припайка на переднюю поверхность инструмента специальных пластинок из твердого сплава или из инструментальных сталей;
применение накладных стружкозавивателей и стружколомателей,
Образование канавок на передней поверхности осуществляется либо путем абразивной заточки, либо электроэррозионным способом. Размеры канавок R при работе с подачами до 0,8 мм принимаются равными 4—6 мм, а при работе с подачами более 0,8 мм — R= 10—12 мм.Основным недостатком завивания стружки посредством канавок является повышенный расход твердого сплава. Образование уступов на передней поверхности осуществляется, главным образом, абразивной заточкой. Размеры ширины уступа устанавливаются в зависимости от условий обработки.
Рекомендуемые размеры ширины уступа в зависимости от условий обработки
Глубина резания, мм |
| Ширина уступа | в при подаче | на 1 оборот, мм | |
до 0,3 | 0,3—0,45 | 1 0,45—0,60 | 0,6—0,7 | 0,7—1,0 | |
до 1,5 | 1,5 | 2,0 | 2,5 | 3,0 | 3,5 |
1,5—6 | 2,5 | 3,0 | 4,0 | 4,5 | 5,0 |
6—12 | 3,0 | 4,0 | 5,0 | 5,5 | 6,0 |
12—20 | 4,0 | 5,0 | 5,5 | 6,0 | 6,5 |
Припайка на переднюю поверхность специальных пластинок из твердого сплава или из инструментальных сталей может производиться в двух положениях. При параллельном расположении специальной пластинки относительно режущей кромки будет происходить завивание стружки в виде длинных спиралей, а при расположении специальной пластинки относительно режущей кромки под углом в 10° будет происходить стружколомание. Расстояния от режущей кромки до специальной пластинки рекомендуются такие же, как и ширина уступа при абразивной заточке, а толщина «с» специальных пластинок обычно принимается равной 6—8 мм.
Для завивания и ломания стружки применяются также накладные стружкозавиватели различных конструкций. В этих конструкциях (см. рис.) сухарь 3 с наплавленной наплавочным твердым сплавом (сормайтом) рабочей поверхностью свободно вращается вокруг оси 2, запрессованной в корпус стружкозавивателя 1. В процессе резания сходящая стружка плотно прижимает сухарь к передней поверхности резца. К числу накладных стружкозавивателей и стружколомателей относятся также и прижимные (крепежные) детали в резцах с механическим креплением режущих твердосплавных пластинок.
РЕКОМЕНДАЦИИ ПО ИЗГОТОВЛЕНИЮ РЕЗЦОВ С ПЛАСТИНКАМИ ИЗ ТВЕРДЫХ СПЛАВОВ
В процессе изготовления резцов выполняются следующие работы:
обработка стержней резцов; подготовка к напайке твердых сплавов; напайка твердых сплавов на стержни резцов; заточка и доводка резцов. Эти элементы технологического процесса состоят из ряда операций, правильное выполнение которых обеспечивает качественное изготовление резцов, что, в свою очередь, дает возможность получения максимальной экономической эффективности от применения твердых сплавов. Стержни резцов следует изготавливать из углеродистой конструкционной стали с пределом прочности при растяжении 60—65 кгс/мм2. Стержни резцов ослабленной конструкции (отрезные, прорезные, и т. п.) изготавливаются из конструкционной легированной стали марок 40Х, 45Х и т. п. с последующей термической обработкой до твердости RC = 40—45. Стандарные размеры сечения заготовок стрежней резцов указаны ниже, в таблице. Выбор размеров сечения заготовок производится в зависимости от условий обработки и размеров оборудования и приспособлений. Рекомендуется выбирать по возможности наибольшие размеры сечения стержня, что будет способствовать увеличению жесткости резца, необходимой при работе твердосплавным инструментом.
ОБРАБОТКА СТЕРЖНЕЙ РЕЗЦОВ
Заготовка материала для стержней резцов. Эта операция, по убывающей степени ее эффективности, может выполняться:
на прессножницах;
на станках для холодной разрезки металла (дисковых пилах и приводных ножовках);
на горизонтально-фрезерных станках;
на поперечно-строгальных станках.
Для резцов, у которых стержень должен обрабатываться с четырех сторон, сечение заготовки следует выбирать с учетом припуска на обработку.
Кузнечная обработка головки стержня резца
Кузнечной обработке подвергаются стержни резцов следующих типов: проходные отогнутые, изогнутые, подрезные, отрезные, прорезные и т. п. Кроме того, кузнечной обработке могут подвергаться и все остальные типы резцов.
Наиболее эффективным методом кузнечной обработки является ковка в штампах, но можно эту операцию выполнять и свободной ковкой по чертежам. В процессе отковки производится и обработка задних граней, с приданием им соответствующих задних углов, что значительно сокращает время на последующую механическую обработку. Обработке в штампах могут подвергаться также и такие резцы, как, например, прямые проходные.
Отжиг стержней резцов после кузнечной обработки
С целью облегчения дальнейшей механической обработки стержни резцов, прошедшие кузнечную обработку, подвергаются отжигу. Отжиг производится для стержней из сталей марок 45 и 50 при температуре 820—850°, а из сталей марок 40Х или 45Х при температуре 840—870°.
Обработка опорной плоскости стержня резца
Обработка опорной плоскости производится с целью создания базы для правильной установки резцов на станках. Обработка опорной плоскости производится фрезерованием или чистовым строганием, а при изготовлении резцов для точных работ рекомендуется шлифовать опорную плоскость стержня. Наиболее эффективным методом обработки является шлифование сегментными кругами на плоско-шлифовальных станках.