Точная прокатка тонких полос
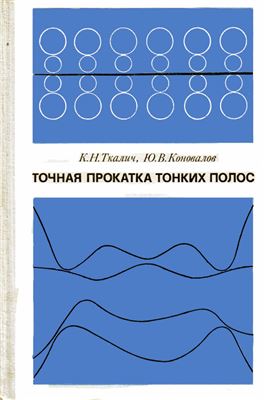
Ткалич К.Н., Коновалов Ю.В.
Металлургия, 1972 г.
ЭЛЕКТРОМЕХАНИЧЕСКИЕ СИСТЕМЫ РЕГУЛИРОВАНИЯ ТОЛЩИНЫ ПОЛОСЫ
Программное регулирование толщины полосы
Наиболее простым является программное автоматическое регулирование толщины полосы. Его можно производить либо по всей длине полосы, либо на отдельных участках (как правило, на заднем конце полосы).
Зная величину и протяженность утолщения заднего конца полос при прокатке на данном стане, можно давать дополнительное обжатие, уменьшая зазор между валками с помощью нажимных винтов. В этом случае заранее задают величину дополнительного обжатия и момент включения нажимных винтов на одной или нескольких клетях.
Рассматриваемая система испытывалась на стане 810 Новосибирского металлургического завода . При автоматическом опускании нажимных винтов в 3-й клети чистовой группы стана на 0,8 мм задний конец полосы выходил без утолщения.
Однако при прокатке сталей, имеющих большое сопротивление деформации, возникает перегрузка двигателя клети, а при высоком темпе прокатки нажимные винты не успевают за время паузы возвращаться в исходное положение.
На стане 1450 Магнитогорского металлургического комбината дополнительное обжатие заднего конца полосы производили во 2, 3, 4 и 5-й клетях непрерывной группы стана ручным включением нажимных винтов. При этом разница в толщинах концов полосы снижалась до 0,05—0,03 мм, а при обычной прокатке составляла 0,26 мм. Несколько позже на том же стане была внедрена система автоматического дополнительного обжатия заднего конца полосы в 1, 2, 3 и 4-й клетях непрерывной группы стана; величина дополнительного обжатия по клетям соответственно составила 0,75;
0,75—0,5; 0,6—0,3 и 0,4—0 мм. При этом разнотолщинность между передним и задним концами была равной 0,08—0,24 мм (67).
На стане 1700 Ждановского завода им. Ильича проведены опыты по уменьшению продольной разнотолщинности полос путем дополнительного обжатия заднего конца полосы в 9-й клети стана [47]. Установлено, что опускание нажимных винтов в клети 9 на
0,40 мм (no показаниям продуктиметров) позволяет снизить продольную разнотолщинность на 0,07—0,10 мм. При этом продольная разнотолщинность опытных полос оставалась довольно высокой 0,18—0,25 мм.
Были опробованы два варианта увеличения скорости прокатки в клетях 9 и 10 при одновременном дополнительном обжатии заднего конца полосы в 9-й клети: 1) увеличение скорости прокатки в обеих клетях на 4—5% по сравнению с обычной; 2) увеличение скорости прокатки в клети 9 на 7,5—10% и в клети 10 на 8,5—9%. Дополнительное обжатие в 9-й клети составляло 0,40 мм. В обоих случаях продольная разнотолщинность оставалась практически такой же, как и при применении только дополнительного обжатия, но длина утолщенной части заднего конца уменьшилась до 8—10 м. Обычно она равна 20—30 м при общей длине полос 330—420 м.
На рис. 37 приведены продольные профили полос, прокатанных по обычной технологии (7), с дополнительным обжатием заднего конца (2), а также с дополнительным обжатием задних концов и увеличением скорости прокатки в 9-й и 10-й клетях (3, 4). При дополнительном обжатии заднего конца полосы продольная разнотолщинность снижается, а одновременное с дополнительным обжатием увеличение скорости прокатки позволяет значительно уменьшить длину утолщенной части заднего конца.
В результате исследований была разработана система дополнительного обжатия заднего конца полосы по жесткой программе в 8-й и 9-й клетях стана 1700. Опыт показал надежность системы. Продольная разнотолщинность полос была снижена на 0,2 мм, благодаря чему, с одной стороны, увеличилась длина горячекатаных полос, а следовательно, и количество годных листов, а с другой стороны, улучшились условия стыковой сварки полос в цехе холодного проката. До внедрения системы количество разорванных при прокатке швов составляло 27,1% от общего числа швов, а после внедрения 21,5%, т. е. уменьшилось на 5,6% 168].
Изучение общих закономерностей изменения толщины по длине полосы позволяет заранее рассчитать требуемую программу перемещения нажимных винтов при прокатке.
Институтом автоматики и телемеханики АН СССР (ныне Институт проблем управления) предложена и осуществлена на станах 1450 и 2500 ММК система регулирования толщины по самоустанавливающейся программе (СРСП) [69]. В основу работы системы положен следующий принцип. Кривые разнотолщинности полос данной партии можно представить как сумму двух функций: функции, характеризующей «закономерную» составляющую продольной разнотолщинности, и случайной функции, обусловливающей отклонение кривой разнотолщинности данной полосы от первой функции. Если случайная функция мало влияет на продольную разнотолщинность, то последнюю можно устранить путем перемещений нажимных винтов по программе, соответствующей «закономерной» составляющей.
В процессе прокатки на вход следящего привода нажимного устройства каждой из регулирующих клетей счетно-решающим устройством выдается программа корректирующих обжатий, состоящая из следующих одна за другой команд. Каждая команда относится к определенному интервалу длины прокатываемой полосы и выдает величину корректирующего обжатия, необходимого для устранения отклонения толщины в данном интервале. Команды подаются на каждую последующую клеть со сдвигом, соответствующим времени прохождения данного участка от одной клети к другой, и с соотношениями величины обжатий, пропорциональными вытяжкам по клетям.
При полуавтоматическом режиме работы оператор выставляет программу, составленную на основании ранее полученных для данного профиля результатов. При автоматическом режиме работы составление и установка программы производятся автоматически на основании разнотолщинности, полученной сравнением показаний толщиномера за чистовой группой и заданной толщины полосы. Программа обжатий для данной полосы строится на основании статистического взвешивания кривых разнотолщинности, полученных при прокатке предыдущих полос с этой же партии.
Результаты работы системы на станах 1450 и 2500 ММ К приведены на рис. 38.
Системы программного автоматического регулирования толщины полосы имеют серьезные недостатки:
1) не регулируются отклонения толщины в пределах партии полос;
2) не учитываются случайные причины возникновения продольной разнотолщинности;
3) необходимо иметь большое число программ работы нажимных винтов.
СПОСОБЫ УСТРАНЕНИЯ ПРОДОЛЬНОЙ РАЗНОТОЛЩИННОСТИ полос
- ТЕХНОЛОГИЧЕСКИЕ СПОСОБЫ
Часть причин, вызывающих колебания толщины полосы и связанных с технологией, можно устранить (или несколько ослабить их влияние) путем совершенствования технологического процесса и улучшения конструкции стана. Один из способов устранения продольной разнотолщинности предлагает Р. Б. Симе [46], рекомендующий обеспечивать равенство скоростей выхода полосы из последней черновой клети и входа ее в первую чистовую клеть. При этом разность температур прокатки концов полосы будет минимальной. Однако эта рекомендация в настоящее время в производственных условиях трудно осуществима.
Для уменьшения продольной разнотолщинности применим также дифференцированный по длине нагрев (нагрев с «перекосом») слябов. На стане 1700 Ждановского завода им. Ильича проведены исследования дифференцированного нагрева слябов [47]. Для определения эффективности способа и сравнения его с нагревом по обычной технологии две печи были переведены на дифференцированный нагрев слябов, а две работали по старому режиму. Опыты проводились при прокатке полос толщиной 2,75 и 4 мм. Температуру фиксировали после выхода полос из черновой и чистовой групп клетей. При нагреве по обычной технологии температура переднего и заднего концов раската после черновой группы была примерно одинаковой, а при дифференцированном нагреве — у заднего конца выше на 20—40 град. Это позволило снизить продольную разнотолщинность полос на 0,05—0,10лш (на 15—20% по сравнению с существовавшей ранее).
Несмотря на то что дифференцированный нагрев слябов позволяет снижать продольную разнотолщинность, его применение ограничено, так как возможно оплавление концов слябов и снижение производительности печи.
Перепад температур прокатки между передним и задним концами полос можно уменьшить путем сокращения подачи воды гидросбивом на задний конец полосы (перед непрерывной группой клетей) [48].
Исследования, выполненные авторами на отечественных станах, показали, что максимальная по абсолютной величине продольная разнотолщинность наблюдается в первых клетях непрерывной группы на средней части полосы (обусловлена пятнами от глиссажных труб) далее происходит выравнивание толщины полосы. Утолщение концов полос начинает формироваться в клетях 3, 4 непрерывной группы и увеличивается к последней клети стана. Подробно об этом будет сказано ниже.
Следовательно, имея заданным суммарное обжатие полосы в непрерывной группе, можно выбрать рациональный режим обжатий с точки зрения минимальной продольной разнотолщин-ности полос. Как правило, это сводится к уменьшению обжатия в последних трех-четырех клетях и увеличению его в первых [15, 49].
На станах 2300/1700 Челябинского металлургического завода и 2500 Магнитогорского металлургического комбината для снижения утолщений переднего конца полосы увеличивают скорость полосы при прохождении ее передней части под гидросбивами. С этой/целью увеличивают скорость валков чистового окалиноло-мателя после захвата переднего конца полосы и снижают ее перед захватом валками первой клети непрерывной группы. Исследования, проведенные Ленинградским отделением Тяжпромэлектропроекта, показали, что при увеличении скорости прохождения переднего конца полосы под гидросбивом максимальная разнотолщинность этого конца уменьшается почти в два раза.
Широкое распространение за рубежом получило ускорение непрерывной группы клетей с полосой в валках после захвата
Переднего конца полосы моталками [50, 51]. Два отечественных стана, введенных в эксплуатацию в последнее время (1700 Карагандинского металлургического комбината и 2000 Ново-Липецкого металлургического завода) также работают с ускорением чистовой группы клетей.
Необходимость ускорения вызвана созданием мощных широкополосных станов, предназначенных для прокатки слябов массой до 40 т. При этом длина готовых полос достигает 1—2 км, а продолжительность прокатки одной полосы составляет 1,5— 3 мин.
Для получения определенных по длине полос механических свойств и размеров температура конца прокатки должна быть не ниже 850° С и оставаться постоянной по длине полосы.
Если скорость прокатки в непрерывной группе постоянна, то снижение температуры от переднего конца полосы к заднему при прокатке слябов массой свыше 6—8 т может достигать значительной величины, что вызовет ощутимое изменение толщины готовой полосы и неравномерность механических свойств подлине.
Так, на стане 1700 Карагандинского металлургического комбината температура прокатки заднего конца бывает на 60 град (а иногда и более) ниже температуры переднего конца, при этом продольная разнотолщинность полос достигает 0,50, мм. Эти данные получены при прокатке слябов массой 12—18 т.
Общий тепловой баланс полосы в непрерывной группе стана складывается из тепловых потерь за счет радиации и конвекции во время транспортировки полосы в межклетевых промежутках и изменения энтальпии полосы в очаге деформации каждой клети при отдаче тепла полосой валкам и при внесении в полосу тепла за счет процесса деформации [50, 52—56].
Ускорение чистовой группы клетей в идеальном случае должно устранить температурный перепад по длине полосы