Термитная сварка
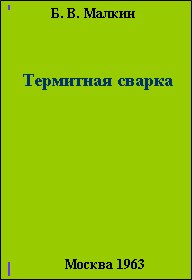
Б.В. Малкин, А.А. Воробьев
МКХ РСФСР, 1963 г.
Основным высококалорийным горючим, применяющимся в термитных смесях, является алюминий. После кислорода и кремния алюминий является самым распространенным элементом земной коры и составляет около 8% массы Земли (железо 4,7%).
Алюминий в тонкоизмельченном состоянии при нагревании на воздухе быстро окисляется, выделяя большое количество тепла, и образует окись алюминия А12Oз—прочное химическое соединение с температурой плавления 2050° и температурой кипения 2980°. Теплота образования окиси алюминия 378 ккал/моль.
Удельный вес алюминия 2,7 г/смъ при 20°; в расплавленном состоянии, при температуре 1000°C - 2,35 г/смг. Температура плавления технически чистого алюминия (99,5%)—659,8°; температура кипения—2400°. Для окисления алюминия на 1,12 г металла требуется 1 г кислорода. При этом алюминий, сгорая, выделяет 714 кал тепла и развивает температуру до 3000°.
Принцип получения трудновосстанавливаемых металлов из их окислов впервые был выдвинут крупнейшим русским ученым-химиком, основоположником современной физической химии Н. Н. Бекетовым. В 1865 г. в своей докторской диссертации «Исследования над явлениями вытеснения одних элементов другими» Бекетов превратил этот принцип в научную теорию, заложив основу алюминотермии. Он установил, что алюминий обладает очень большой активностью, соединяясь с кислородом, и что при определенных условиях алюминий легко восстанавливает из окислов другие металлы, стоящие правее его в таблице напряжений химических элементов.
Сварочный термит состоит из порошкообразного металлического алюминия и окислов железа в виде окалины (технологического отхода горячей обработки стали), а также различных присадок, вводимых в шихту для легирования получаемой стали.
Какие условия необходимы для начала термитной реакции?
1. Термитная шихта должна быть рассчитана так, чтобы в ходе реакции выделилось необходимое количество тепла для расплавления и перегрева конечных продуктов термитной реакции.
2. Компоненты термитной шихты: алюминиевый порошок и окислы железа должны быть мелких фракций и тщательно перемешаны.
3. Для начала термитной реакции в любой точке термитной шихты необходимо создать температурный толчок не ниже 1350°, после чего термитная реакция быстро распространится на всю шихту.
В результате термитной реакции, которая в течение 15—30 сек. протекает очень активно, образуются металл (около 50% от первоначального веса термитной шихты) и шлак.
В процессе термитной реакции часть тепла расходуется на нагревание стенок тигля, лучеиспускание и т. д. Однако, несмотря на это, количество выделяющегося тепла достаточно для того, чтобы расплавить шихту и перегреть продукты реакции—жидкий металл и шлак—до 2600—2700°. Это обусловливает возможность получения чистого металла, так как благодаря значительной разнице в удельных весах жидкий шлак всплывает на поверхность, а металл опускается на дгго тигля.
Качество термитного металла определяется физико-химическими свойствами компонентов шихты.
Для получения металла (стали) нужного химического состава в шихту вводят в измельченном состоянии легирующие материалы: ферромарганец, ферромолибден, ферротитан, феррованадий, углерод и т. д.
Измельчзнная легирующая присадка закладывается в тигель вместе с термитными компонентами.
Участие легирующих элементов в термитной реакции—очень многообразно: они легируют термитную сталь, раскисляют и рафинируют ее. Кроме того, они частично теряются—испаряются и переходят в шлак.
Ценные ферросплавы (ферротитан, феррованадий и др.) повышают прочность термитной стали, так как в ходе реакции, находясь в'" жидком состоянии, они образуют карбидную фазу титана и ванадия. Наличие в стали перечисленных карбидов увеличивает ее мелкозернистость, повышает твердость и т. п.
Длительность термитной реакции от момента зажигания термита до ее окончания и полного отделения металла от шлака находится в прямой зависимости от количества сжигаемого термита и колеблется от 15 до 40—50 сек.
При одновременном сжигании больших количеств термита реакция протекает с относительно небольшими потерями тепла.
Термитные смеси в зависимости от их назначения можно условно разделить на следующие группы:
1) элементарная термитная смесь — железная окалина плюс алюминиевый порошок в стехиометрическом соотношении;
2) термит для сварки рельсовых стыков. В шихту вводится стальной наполнитель—мелкие кусочки малоуглеродистой прово^ локи или стальная малоуглеродистая стружка, ферромарганец и порошкообразный графит;
3) термит для сварки легированных сталей. В качестве присадки используются ферротитан, феррованадий и др.;
4) термит для сварки чугуна. В присадку вводится значительное количество кремния. Марганец исключается. Высокое содержание кремния в термитном металле способствует выделению графита в сварочной и переходной зонах и обеспечивает получение достаточно прочных сварных соединений;
5) термит для сварки высокомарганцовистых сталей. В этот термит вводится увеличенное количество марганца и углерода в виде ферромарганца и чугунной стружки;
6) специальные термиты — пиротехнические, для наварки пода в металлургических печах, уменьшения усадочных раковин в слитках, вторичного дробления минералов и руд, изготовления термитных брикетов и т. п.
1. История развития производства термита и термитной сварки рельсов
В Москве термитную сварку впервые применили в 1915 г., когда было сварено 126 стыков. В 1918 г. сварили еще 151 стык. С 1923 г. в трамвайных путях столицы начинают регулярно варить стыки термитом. До 1925 г. стыки сваривали импортным термитом. В 1925 г. на Московском термитно-стрелочном заводе инженером М. А. Карасевым было налажено промышленное производство термита.
М. А. Карасев внес крупный вклад в развитие алюминотермии, организовав на базе отечественной технологии выпуск термитных смесей для народного хозяйства. Он предложил рациональные способы производства алюминиевого порошка и термита. Ему были выданы авторские свидетельства на «аппарат для получения зерноволокнистого алюминия», «шаровой мельницы для производства алюминиевого порошка», «механической нагревательной печи для обжига железной обсечки и окалины при изготовлении термита» и т. п.
В последующие годы в путях московского трамвая было сварено термитом свыше 100 000 стыков.
Сварка производилась двумя способами: комбинированным и врасклинку. Ввиду того, что стыки, свариваемые последним способом, Часто выходили из строя, к 1931 г. этот способ перестали применять. Вместо него начали внедрять способ сварки промежуточным литьем. Одновременно начали применять способ сварки «дуплекс» (способ промежуточного литья с последующим прессованием). Однако этот способ не получил широкого распространения из-за сложности технологического процесса.
Качество сварки термитных стыков за первые 10 лет ежегодно улучшалось, и количество лопнувших (в течение года) стыков в среднем не превышало 0,8%.
Применение отечественного термита для сварки рельсовых стыков показало его превосходство перед импортировавшимся термитом. В стыках рельсов, сваренных отечественным термитом, значительно меньше процент брака. Это подтверждают результаты эксплуатации первой очереди Московского метрополитена. Так, например, каждый рельсовый стык на участке Сокольники— Парк культуры в 1938 г. выдержал 13,4 млн. ударов с грузонапряженностью 53 млн. т-км.
В 1936 г. вышло из строя 0,17% от количества эксплуатируемых в путях стыков, в 1937 и 1938 г. — по 0,5%.
Из приведенного количества выбывших из строя стыков 75% разрушились из-за наличия болтовых отверстий в зоне сварки.
В эти же годы термит стали внедрять в другие отрасли народного хозяйства. В частности, была разработана и успешно осуществлена термитная сварка стыков легированных труб первого прямоточного котла высокого давления; начали применять также термитную сварку для ремонта крупногабаритных стальных деталей: валов, колонн и т. п.