Термическая обработка стали
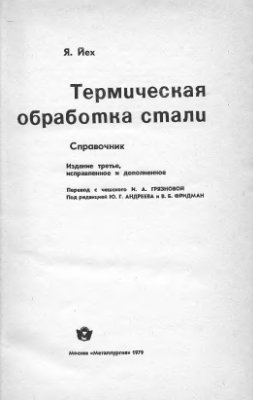
Йех Я
Металлургия, 1979 г.
2.1. ОТЖИГ
2.1.1. Гомогенизирующий отжиг
Гомогенизирующий отжиг проводят с целью максимального выравнивания химического состава стали за счет диффузии. Неоднородность химического состава возникает еще при кристаллизации стали в диапазоне температур между ликвидусом и солидусом.
Собственно гомогенизирующий отжиг — это нагрев до температур, намного превышающих точки А3 и Аст(1000—1250°С), достаточно длительная выдержка при этой температуре (6 ч и более) н последующее медленное охлаждение. Весьма целесообразной является комбинация гомогенизирующего отжига с нагревом под прокатку или ковку; для этого необходимо на 2—4 ч увеличить длительность выдержки при нагреве под прокатку или ковку.
Однако увеличенная длительность выдержки при высокой температуре приводит к обезуглероживанию и к образованию окалины на поверхности изделия, что влечет за собой увеличение припусков на обработку. Поэтому гомогенизирующий отжиг следует применять только в случае необходимости, причем подвергать отжигу лучше слитки или заготовки, а не изделия. В деформированной стали (с разрушенной литой структурой) диффузионное выравнивание химического состава происходит гораздо быстрее. Желательно после гомогенизирующего отжига проводить деформацию с целью измельчения зерна. Если диффузионный отжиг проводят с целью выравнивания состава по элементам, растворенным в феррите, то можно, используя более высокую скорость диффузии в α-Fe, вести отжиг при температурах немного ниже A1а дли стали с очень низким содержанием углерода — ниже А3.
2.1.2. Нормализация
Нормализацию проводят с целью измельчения крупного зерна, образующегося в стали или при затвердевании, или при высокотемпературной деформации, или при длительном отжиге при повышенных температурах.
Температура конца ковки или прокатки, степень деформации и скорость охлаждения после деформации неодинаковы как в объеме одной заготовки (особенно сложной формы с различными сечениями), так и для различных заготовок. Поэтому в литых и кованых заготовках (и других горячедеформированных полуфабрикатах) наблюдается разнозернистость. Объемы с зерном разной величины могут по-разному вести себя при последующей термической обработке. В результате нормализации зерна не только измельчаются, но и выравниваются по величине.
Нормализация доэвтектоидной стали заключается в нагреве до температуры, превышающей на 30—50°С точку превращения Ас3, и последующем спокойном охлаждении на воздухе.
Заэвтектоидную сталь, как правило, не подвергают нормализации. Если же стремятся устранить карбидную сетку, образовавшуюся в результате медленного охлаждения после деформации, то температуру нормализации выбирают примерно на 30°С выше АсСт, охлаждение производят с большой скоростью до температуры ниже 700°С, затем скорость охлаждения уменьшают с тем, чтобы прошло перлитное превращение, а не закалка, которая при таких высоких температурах аустенитизации привела бы к возникновению высоких напряжений и растрескиванию. Скорость охлаждения, которая обеспечивает подавление выделения заэвтектоидных карбидов по границам зерен в диапазоне температур между Агсти Аг\9для изделий малого размера достигается охлаждением на воздухе; для изделий больших размеров (диаметром более 100 мм) даже кратковременное охлаждение в воде может оказаться недостаточным.
Если нормализацию заэвтектоидной стали производят с целью измельчения зерна, то температура нагрева незначительно превышает Асиа охлаждение ведут на воздухе, так как при нагреве до температуры Асетзерно слишком укрупняется, а при медленном охлаждении растворенные в аустените карбиды выделяются по границам зерен, образуя карбидную сетку.
Нормализацию применяют не только в качестве подготовительной операции к последующей закалке, но и в качестве окончательной операции термической обработки менее нагруженных деталей машин (обычно из углеродистой стали). С целью снятия внутренних напряжений, снижения твердости и улучшения пластических свойств изделие после нормализации подвергают высокому отпуску при температурах 500—600°С.
Измельчение зерна при нормализации обусловлено перекристаллизацией, поэтому оио будет тем интенсивнее, чем больше скорость нагрева до температуры нормализации и чем больше скорость охлаждения.
Так как для нормализации характерны относительно быстрый нагрев и охлаждение на воздухе, то для этой обработки можно применять обычные закалочные печи, например камерные, с выдвижным подом или проходные.
2.1.3.Отжиг на крупное зерно
Низкая твердость после неполного отжига малоуглеродистой стали определяет ее плохую обрабатываемость резанием. Поэтому такую сталь, например цементуемую, перед обработкой резанием обычно подвергают нормализации. Поскольку крупнозернистые структуры лучше обрабатываются, производят искусственное укрупнение зерна, для чего сталь нагревают до более высокой температуры (950— 1100°С) и затем медленно охлаждают с печью. Горячедеформированные заготовки уже имеют крупнозернистую структуру, поэтому достаточно подвергнуть их отпуску при температуре ниже точки Ас1 для снижения твердости.
2.1.4.Полный отжиг
Этот отжиг производят с целью улучшения обрабатываемости резаннем и деформируемости стали, снижение твердости и снятия внутренних напряжений. После нагрева стали до температуры, превышающей на 30—50°С температуру Ас3или Ассm ее выдерживают при этой температуре и затем медленно охлаждают с печью.
2.1.5.Сфероидизирующий отжиг
Этот отжиг проводят как для смягчения стали с целью улучшения последующей обработки резанием или деформации в холодном состоянии, так и для получения соответствующей структуры под последующую закалку. Температуры неполного отжига представлены на рис. 55.
Наиболее простым способом отжига является нагрев до температуры несколько ниже Ас1 с последующей выдержкой при этой температуре в течение нескольких часов (рис. 56,а). Если исходной структурой является пластинчатый перлит, то сфсроидизация пластинок происходит сравнительно медленно, причем тем медленнее, чем пластинки крупнее. При этом способе отжига из крупно пластинчатого перлита образуется крупный зернистый перлит, представляющий собой структуру, непригодную для последующей закалки, особенно для заэвтектоидной стали. Карбидная сетка (заэвтектоидные карбиды, выделившиеся по границам зерен) при этом способе отжига не устраняется. Процесс отжига можно несколько ускорить путем периодического повышения и понижения температуры относительно точки A1, (рис. 56,6). Такой отжиг, являющийся разновидностью сфероидизирующего отжига, называется маятниковым. При отжиге крупных деталей или при большой садке он трудно применим из-за различия температур на поверхности и внутри детали (садки).
Значительно быстрее зернистый перлит можно получить при нагреве выше Асхс последующим медленным охлаждением.
Если в исходной структуре имеется крупнопластинчатый перлит, то этот способ отжига является единственным, обеспечивающим получение мелкого глобулярного перлита. Предпосылкой для аустенизации перлита без слишком интенсивной гомогенизации аустенита является сохранение в нагретой стали как можно большего числа зародышей, из которых при охлаждении образуются мелкодисперсные равномерно распределенные карбиды.
Чем выше содержание углерода в стали, тем дольше растворяются карбиды, поэтому температура отжига заэвтектоидной стали должна быть повышенной (см. рис. 55).
Чем медленнее сталь проходит критическую область температур при охлаждении, тем крупнее карбиды и тем ниже окончательная твердость. Сталь следует медленно охлаждать до температуры 600—650°С, т. е. не только до окончания превращения аустенита в перлит, но и до температуры ниже температуры максимальной растворимости углерода в феррите.
Высокая температура отжига, как и большая длительность выдержки при этой температуре, приводит к слишком сильной гомогенизации аустенита. Поэтому последующее охлаждение должно быть медленным, так как всегда существует опасность образования пластинчатого перлита. При отжиге в большегрузных камерных печах возможность 'поддержания равномерного распределения температур по всей садке практически отсутствует. Даже при очень малой скорости нагрева заданная температура достигается гораздо раньше на поверхности садки, и гомогенизация аустенита здесь гораздо больше, чем внутри садки. Поэтому поверхность садки следует охлаждать очень медленно. Гораздо лучшее распределение температур достигается в небольших печах или (в случае высокопроизводительных печей) в проходных печах — туннельных или с роликовым подом.
На рис. 56 схематически представлены различные способы отжига при температурах выше Ac1 с последующим медленным охлаждением. Для достижения возможно более равномерного распределения температур в садке нагрев в камерных печах ведется медленно (рис. 56, в)или ступенчато (рис. 56,5). В проходных туннельных печах можно применять более быстрый нагрев с менее длительной выдержкой для выравнивания температур (рис. 56,е). В проходных печах, в частности с роликовым подом, для лучшего выравнивания температуры быстрый нагрев в первой зоне можно осуществлять до более высокой температуры без опасности слишком сильной гомогенизации (рис. 56 с). Перед .началом непрерывного охлаждения можно проводить подстуживание до температуры на 50—100°С ниже температуры начала медленного охлаждения. При таком способе образуется большое количество центров кристаллизации; окончательная структура при этом состоит из большого количества мелкодисперсных карбидов. Для выравнивания температуры между поверхностью и серединой садки в камерных печах на участке охлаждения имеется томильная зона, где осуществляется выдержка при температуре непосредственно ниже точки превращения (рис. 56,г, д). Состояние стали после такой термической обработки обозначают в стандартах ЧССР на качество стали дополнительной цифрой 3.