Термическая обработка металлов токами высокой частоты
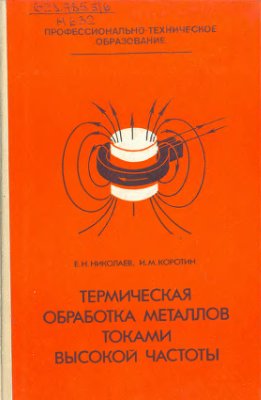
Николаев Е.Н., Коротин И.М.
Высшая школа, 1984 г.
ПОВЕРХНОСТНАЯ ЗАКАЛКА СТАЛИ И ЧУГУНА
Назначение. Данная закалка служит для упрочнения поверхностных слоев стальных и чугунных деталей.
Основные особенности. При этом виде поверхностного упрочнения глубина закалки на мартенсит примерно равна глубине слоя, нагретого до надкритических температур. Более глубокие слои детали, лежащие ниже слоя закалки (за исключением небольшого переходного слоя), упрочнению не подвергаются. Для максимальной экономии электроэнергии поверхностный нагрев осуществляют с возможно большой скоростью. Скорость в области фазовых превращений составляет 30—300° С/с, время нагрева под закалку 2—10 с, удельная мощность 0,5—1,5 кВт/см2.
Данная закалка имеет следующие недостатки: малая статическая прочность тяжелонагруженных деталей, так как при этом методе сердцевина изделия не упрочняется; недостаточная износостойкость и стойкость против выкрашивания; трудность или невозможность осуществления равномерного поверхностного нагрева и закалки деталей, имеющих сложную форму, например шестерен.
Микроструктура закаленной доэвтектоидной стали распределяется от периферии к центру так: мартенсит (зона I); мартенсит, феррит и троостит (зона II); феррит и перлит (зона III). Характеру распределения структур по сечению закаленной детали соответствует распределение твердости. Твердость поверхностного слоя: с мартенситной структурой составляет HRC60—65. Рекомендуемая толщина закаленного слоя (0,10,15)D, где D— диаметр детали, мм. Переходный слой должен составлять 25—30% толщины закаленного слоя.
Одновременная закалка. Применима для закаливания деталей небольших размеров (например, муфт, фланцев, поршневых палец) .
При поверхностной закалке удельная мощность для закаливаемой детали колеблется в пределах 0,3—1,5 кВт/см2. Необходимая мощность нагрева (в кВт) определяется формулой Ρ = SΡο/η, где S — нагреваемая поверхность, см2; Р0— удельная мощность для закаливаемой детали, кВт/см2; η — кпд индукционного нагрева.
Частоту питающего тока находят из такого соотношения (150Дк2) <f<(2500Дк2), где Хк — глубина закаленного слоя, см; f — частота тока, Гц.
Так как мощность Р, передаваемая детали, изменяется обратно пропорционально квадрату расстояния а между деталью и индуктором, то Р=1/а2, поэтому зазор между ними выбирают минимальный.
Последовательная закалка. Целесообразна для получения сравнительно неглубокого слоя; рекомендована к использованию для мало- и умеренно нагруженных деталей. Ее выполняют непрерывным и прерывистым способом.
Непрерывно-последовательная закалка получила наибольшее применение. Спрейер при такой закалке устанавливают ниже индуктора на расстоянии до 5 мм, так как при большем расстоянии нагретые участки будут подстуживаться.
Мощность (в кВт) для нагрева детали P = P0/S, где Р0 — удельная мощность для закаливаемой детали, кВт/см2; 5 — площадь, равная проекции на нагретую деталь, см2.
Для каждого элемента поверхности время нагрева t — b/υ, где Ь — размер индуктора в направлении детали, см; υ — скорость движения детали, см/с.
Активная зона (в см2) индуктора S = P/P0.
Необходимая скорость нагрева детали (в см/с) v = b/t.
В табл. 7 приведены ориентировочные значения скорости нагрева и удельной мощности, необходимые для достижения разных глубин нагрева.
7. Зависимость глубины нагрева от скорости нагрева и удельной мощности закаливаемой детали
Глубина нагрева, мм | Скорость нагрева в области фазовых превращений, °С/с | Удельная мощность, кВт/см2 |
1—2* | 100-300 | 0,8-1,5 |
3—5 | 20 -80 | 0,5-1,3 |
6—10 | 2-15 | 0,05-0,2 |