Термическая обработка металлов и оборудование термических цехов
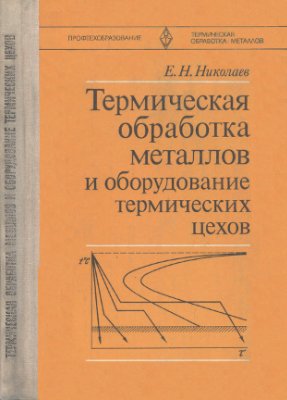
Николаев Е.Н.
Высшая школа, 1980 г.
В зависимости от вида термообработки конструкционные легированные стали подразделяются на две группы: цементуемые (низкоуглеродистые) и улучшаемые (среднеуглеродистые).
Содержание углерода в цементуемых сталях от 0,1 до 0,30%. В состав цементуемых сталей входят кремний от 0,17 до 0,37%, марганец от 0,3 до 1,1%, хром от 0,45 до 1,65%, никель от 0,25 до 1,4% и другие элементы в небольших количествах. Цементуемые стали: 15Х, 30ХГТ, 25ХГМ, 12Х2Н4А и т. п.
Термическому улучшению — закалке и высокому отпуску (500—600° С) на структуру сорбит подвергают стали, содержащие 0,3—0,5% С и не более 5% легирующих элементов.
Улучшаемые легированные стали применяются для изготовления ответственных деталей машин (валов, штоков и других деталей), работающих при циклических и ударных нагрузках, а также при пониженных температурах. Улучшаемые стали: хромистые — 40Х, 45Х, 50Х; хромокремнемарганцовые — 30ХГСА, 35ХГСА; хромоникелевые — 40ХН, 45ХН, 50ХН; хромоникельмолибденовые
(вольфрамовые) — 40ХНМА, 18Х2Н4МА и другие относятся к лучшим улучшаемым конструкционным сталям.
§ 2. РЕССОРНО-ПРУЖИННЫЕ СТАЛИ
Рессорно-пружинные стали применяют для изготовления пружин, рессор и других деталей. Эти стали должны обладать высоким пределом упругости и пределом выносливости. Этим условиям удовлетворяют углеродистые стали с содержанием 0,5—0,7% С, дополнительно легированные кремнием, марганцем, хромом, ванадием и вольфрамом.
Для получения наиболее высокого предела упругости рессорные листы и пружины после закалки отпускают при температуре 400—500° С.
Для увеличения срока службы готовые пружины и листы рессор подвергают поверхностному наклепу обдувкой дробью. При этом в наклепанном слое возникают напряжения сжатия и уменьшается вредное действие поверхностных дефектов (грубых рисок, трещин, обезуглероживание и др.).
Наиболее высокими механическими свойствами обладают стали марок: 50ХФА, 70СЗА, 60С2ХА, 60С2Н2А.
Пружины также изготовляют из шлифованной холоднотянутой проволоки — серебрянки. Чаще применяют углеродистые стали марок: У8, У10, 65 и 70.
§ 3. ШАРИКОПОДШИПНИКОВЫЕ СТАЛИ
Шарикоподшипниковые стали должны обладать высокой твердостью, износостойкостью, высокой прочностью и иметь высокий предел выносливости, так как детали подшипника (шарики, ролики, кольца) воспринимают значительные знакопеременные нагрузки. К шарикоподшипниковым сталям предъявляются высокие требования по минимальному содержанию неметаллических включений, различных дефектов (пор, пузырей и др.) и карбидной неоднородности. Эти дефекты являются концентратами напряжений, вызывающими образование трещин и выкрашивание металла, что приводит к разрушению, подшипника.
Для подшипников применяют следующие марки стали: ШХ6, ШХ9, ШХ15, и ШХ15СГ, которые содержат углерода от 0,95 до 1,15%, хрома от 0,4 до 1,65%, марганца от 0,20 до 1,20%, кремния от 0,17 до 0,65%- Во всех указанных сталях серы <0,020%, фосфора < 0,027%, никеля < 0,3% и меди < 0,25%.
Термическая обработка указанных сталей включает операции отжига, закалки и отпуска. Отжиг необходим для снижения твердости и получения зернистого перлита. Закалка с температуры нагрева 830—840° С, охлаждение в масле, отпуск при 150—160° С в течение 1—2 ч. Структура — мелкоигольчатый мартенсит с равномерно распределенными карбидами. Твердость HRC > 62;
Для крупных подшипников диаметром 0,5—2 м применяют цементную сталь 20Х2Н4А.
Сталь XI8 (0,9—1,0% С, 17—19% Сr, другие элементы в обычных пределах) применяется для подшипников, работающих в химически агрессивных средах (морская вода, растворы кислот и солей, органические среды и т. д.).
Высокое содержание хрома придает стали повышенную коррозионную стойкость. Термическая обработка для получения высокой твердости и стабильности в размерах состоит из закалки при температуре 1000—1050° С с охлаждением в масле, обработки холодом при температуре 203 К (—70°С) и отпуска при 150—160°С. Твердость после обработки HRC 60—61. Подшипники, работающие при температуре 400—500° С, изготовляют из быстрорежущей стали.
§ 4. АВТОМАТНЫЕ СТАЛИ
Автоматные стали А12, А20, АЗО, А40Г (0,08—0,45% С) имеют повышенное содержание серы (0,08—0,30%) и фосфора (0,08— 0,06%) и отличаются хорошей обрабатываемостью на металлорежущих станках. Причиной этого является образование сульфида марганца MnS, способствующего образованию короткой и ломкой стружки, что повышает стойкость инструмента и увеличивает скорость резания. Фосфор, повышая твердость и снижая пластичность стали, способствует получению гладкой блестящей поверхности при резании, но, улучшая обрабатываемость резанием, сера и фосфор ухудшают качество стали. Автоматные стали имеют пониженные вязкость и пластичность в поперечном направлении, усталостную прочность и коррозионную стойкость. Автоматные стали применяют для малоответственных деталей (крепежные детали, втулки и др.).
В последнее время применяют качественные углеродистые и легированные стали с добавками свинца (0,15—0,30%), улучшающего обрабатываемость.
§ 5. ВЫСОКОМАРГАНЦОВИСТАЯ СТАЛЬ
Высокомарганцовистая сталь Г13Л (сталь Гатфильда) содержит 1,2% С и 13% Мn, имеет высокую износостойкость в условиях ударных нагрузок, вызывающих поверхностный наклеп, высокую прочность 785—981 МПа (80—100 кгс/мм2) при низкой твердости (НВ 180—220).
Сталь закаливается в воде с температуры 1050—1100° С с образованием аустенитной структуры. Сталь применяют для изготовления трамвайных стрелок, черпаков экскаваторов, траков гусениц тракторов, деталей камнедробилок и др.
§ 6. ЖАРОСТОЙКИЕ И ЖАРОПРОЧНЫЕ СТАЛИ И СПЛАВЫ
Способность стали сопротивляться окислению при высокой температуре (>550° С) называется жаростойкостью (окалиностойкостью).
Степень жаростойкости зависит от количества находящихся в стали легирующих элементов: хрома, кремния, алюминия, причем чем больше содержится в стали этих элементов, тем выше жаростойкость. Например, сталь 12X17 с содержанием хрома 17% жаростойка до температуры 900° С, сталь 15X28 (28% Сr) —до температуры 1150°С.
Жаропрочность характеризуется пределом ползучести (напряжением, вызывающим деформацию заданной величины, например от 0,1 до 1% за 100, 300, 500, 1000 ч при заданной температуре) и пределом длительной прочности (напряжением, вызывающим разрушение при данной температуре за данный интервал времени). Жаропрочные стали и сплавы классифицируют по температуре эксплуатации. Например, для работы при температурах 400—550° С применяют стали перлитного класса (15ХМ, 12Х1МФ). Эти стали подвергаются нормализации с температуры 950—1050° С и отпуску при 650—750° С с получением структуры сорбита и карбидов пластинчатой формы.