Термическая обработка и свойства сварных соединений
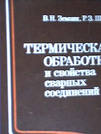
Земзин В.Н., Шрон Р.З.
Машиностроение, 1978 г.
ВЛИЯНИЕ ТЕРМИЧЕСКОЙ ОБРАБОТКИ НА СВОЙСТВА СВАРНЫХ СОЕДИНЕНИЙ
Процесс сварки оказывает сравнительно небольшое влияние на механические свойства различных зон сварного соединения большинства свариваемых аустенитных сталей. Поэтому термическая обработка сваренных узлов по соображениям восстановления механических свойств сварного соединения в большинстве случаев не требуется. Ее могут вводить по условиям восстановления коррозионной стойкости сварного соединения и повышения эксплуатационной надежности узлов, работающих при высоких температурах ползучести. Так как термическая обработка рассматриваемых конструкций связана обычно с нагревом выше 900—1000° С, а основным видом изделий являются сосуды, то стараются ее не применять, а надежность изделия обеспечивают подбором соответствующего основного металла. В изделиях химического машиностроения используют для этих целей сверхнизко-углеродистые и стабилизированные стали; узлы энергоустановок, эксплуатируемые при 500—650° С, целесообразно изготовлять из молибденосодержащих аустенитных сталей.
Проведение, при необходимости, операции термической обработки аустенитных сталей и сплавов сказывается прежде всего на изменении свойств металла шва и околошовной зоны сварного соединения. При сварке аустенитных сталей из-за опасности образования горячих трещин в швах их композиция, как правило, не воспроизводит полностью состав свариваемой стали, а в ряде случаев заметно от него отличается. Обеспечение требуемой технологической прочности швов достигается подбором легирующих элементов в проволоке и покрытии, приводящим к получению двухфазных швов (аустенитно-ферритного, аустенитно-карбидного и аустенитно-боридного) или однофазных при условии повышенной концентрации в них молибдена и марганца. Принципом легирования повышенным содержанием молибдена руководствуются и при создании электродов для сварки сплавов на основе никеля. Повышение жаропрочности таких швов может достигаться дополнительным их легированием титаном и алюминием.
Наиболее широко для сварки аустенитных сталей используются аустенитно-ферритные электроды и проволоки двух композиций (Х19Н9Б и Х19Н11М3). В зависимости от соотношения в металле подобных швов аустенизирующих и ферритизирующих элементов количество в них свободной ферритной фазы может меняться. ГОСТ 10052—75 в зависимости от назначения свариваемой конструкции содержа1 ие ферритной фазы в швах регламентируется в пределах 0,5—4,0; 2,0—4,0; 2,0—5,5; 2,0—8,0; 4,0—10,0 и 10,0—20,0%.
Влияние двух основных видов термической обработки сварных узлов из аустенитной стали (гомогенизирующего отжига и аусте-низации) на прочность сварных швов мало зависит от их фазового состава и подчиняется общим закономерностям (см. гл. III). Гомогенизирующий отжиг относительно мало меняет прочностные свойства сварных швов; аустенизация снижает их вне зависимости от жесткости соединения до уровня для аустенитных сталей близкого легирования (см. рис. 11 и 48). В отличие от этого пластические свойства и, особенно, ударная вязкость, могут сильно изменяться в зависимости от фазового состава швов. Так, если однофазный аустенитный шов типа Э-07Х19Н11МЗГ2Ф мало меняет свою ударную вязкость после выдержек длительностью 10 ч в интервале 100—1000° С (см. рис. 39), то уже при наличии в нем 3—4% феррита проявляется охрупчивание шва при 750—850° С за счет выделения σ-фазы. Если содержание ферритной фазы составляет 8%, то σ-охрупчивание является значительным, а при 10—20% феррита резко проявляется и 475-градусное охрупчивание в области температур 400—475° С.
Изменение свойств аустенитно-ферритного наплавленного металла типа Э-07Х19Н11ГЗМ2Ф с содержанием ферритной фазы от 0 до 10% в различных термических состояниях показано на рис. 201. Увеличение феррита во всех случаях приводит к некоторому повышению прочности наплавленного металла. Максимальную прочность имеет металл исходного состояния, минимальную — в состоянии аустенизации с последующим стабилизирующим отжигом (рис. 201, а). Разница между ними сравнительно мала, так как испытуемые образцы вырезались из относительно мало жесткой наплавки на ребро пластины.
Изменение в заданных пределах количества ферритной фазы практически не влияет на пластичность и ударную вязкость наплавленного металла в исходном состоянии. Если количество феррита превышает 5%, то стабилизирующий отжиг приводит к заметному снижению при комнатной температуре относительного удлинения (менее 20%) и ударной вязкости (менее 5 кгс-м/см2). В условиях испытания при 600° С общая тенденция изменения ударной вязкости сохраняется, но ее абсолютные значения выше.
Аустенизация с последующей стабилизацией позволяет расширить допустимые пределы содержания ферритной фазы без опасности заметного снижения пластических и вязких свойств. Однако и для данного термического состояния увеличение содержания ферритной фазы свыше 8% также приводит к резкому падению относительного удлинения и ударной вязкости. Проведение одной лишь аустенизации без последующего стабилизирующего отжига расширяет допустимое содержание ферритной фазы до 12—15%.
Наблюдаемое после проведения термической обработки изменение свойств наплавленного металла можно объяснить его структурным состоянием, обусловленным процессами, проходящими в выделениях ферритной фазы. Если наплавленный металл содержит менее 5% феррита, то стабилизирующий отжиг приводит к выделению дисперсных частиц σ-фазы в разомкнутых участках α-фазы. В результате этого свойства наплавленного металла меняются сравнительно мало. При содержании в нем более 5% феррита образуются сравнительно крупные участки хрупкой σ-фазы, что вызывает резкое падение пластических и вязких свойств. Сохранение их на более высоком уровне в наплавленном металле после аустенизации и стабилизирующего отжига связано с уменьшением числа ферритных выделений и изменением их формы — превращением из пластинчатых в округлые выделения. Анализ механизма фазовых превращений при термической обработке и старении в аустенитно-ферритных швах разных композиций дан в работах [45; 49; 511.
Благоприятное влияние аустенизации сказывается и на сохранении вязких свойств металла аустенитно-ферритных швов при криогенных температурах (см. рис. 42). Во всех случаях (см. рис. 42, б) проведение аустенизации даже для сварных швов с повышенным содержанием феррита до 10—15% обеспечивает высокую ударную вязкость до —196° С
Наибольшее снижение вязких свойств аустенито-ферритных швов в результате σ-охрупчивания происходит после выдержек при 700—900° С (см. рис. 39). Повышение их до 950—1000° С, меняя характер процесса структурных превращений, приводит к восстановлению ударной вязкости швов.
Для сварных узлов из аустенитных сталей энергооборудования, эксплуатирующихся при температурах выше 500° С, важно знать изменение свойств швов в результате длительного старения при рабочих температурах и. оценить влияние режима термической обработки. Как показано в работе [51 ], такая оценка может быть сделана с использованием параметрического метода. Полученные значения ожидаемой ударной вязкости наплавленного металла Э-07Х19Н11ГЗМ2Ф за срок старения до 105 ч в интервале 550— 700° С приведены на рис. 202. В соответствии с ними и результатами аналогичной обработки для швов типа Э-08Х19Н9Г2Б получено, что в исходном состоянии и после стабилизирующего отжига при 800° С швы указанных композиций с содержанием ферритной фазы до 5% могут эксплуатироваться до 105 ч при температурах до 600° С. Повышение температуры эксплуатации до 650° С можно допустить для швов типа Э-08Х19Н9Г2Б лишь после проведения термической обработки по режиму аустенизации.