Тепловые процессы при обработке металлов и сплавов давлением
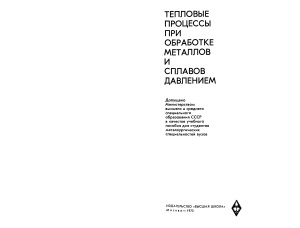
Яловой Н.И. и др.
Высшая школа, 1973 г.
2. УСЛОВИЯ СЛУЖБЫ И ДОЛГОВЕЧНОСТЬ ВАЛКОВ ХОЛОДНОЙ ПРОКАТКИ
Стойкость валков холодной прокатки зависит от ряда факторов, связанных с технологией их изготовления и условиями эксплуатации. К первой группе факторов следует отнести химический состав и механические свойства валка, технологию выплавки валковой стали, режимы ковки, термической и механической обработки.
Ко второй группе относятся режимы обжатий, скорость прокатки, давление металла на валки, натяжение полосы, условия охлаждения и температурный режим валков, механические свойства и качество прокатываемого металла и др. Стойкость валков зависит от правильной организации валкового хозяйства: режимов и норм перевалок, перешлифовок и «отдыха», маршрутов продвижения валков по клетям непрерывных станов, условий хранения и т. д.
Особо следует отметить влияние таких субъективных факторов, как культура производства, опыт и мастерство операторов и вальцовщиков, соблюдение ими технологических инструкций и норм.
Отмеченные факторы влияют на величину и глубину расположения действующих максимальных скалывающих напряжений во время эксплуатации валка, а значит, влияют на стойкость. Как известно, действующие напряжения слагаются из механических, возникающих в упругом или упруго-пластическом контакте, остаточных и тепловых напряжений. Следует также иметь в виду, что непрерывная прокатка, как и прокатка на реверсивных станах с моталками, характеризуется взаимосвязью распределения удельных давлений и величины переднего и заднего натяжений. В общем случае чем больше натяжение (особенно заднее), тем благоприятнее режим работы валков. Наиболее часто величина удельного давления характеризуется долей величины предела текучести для соответствующей клети непрерывного или пропуска реверсивного станов. На практике эта величина при установившемся процессе прокатки составляет 0,2— 0,4 . Величина максимального скалывающего напряжения, характеризующая наибольшее напряжение цикла, в общем случае является функцией неравномерности распределения удельных давлений (отношение максимального значения удельного давления к среднему удельному давлению). Поэтому режим работы валков определяется также значением коэффициента трения, с ростом которого растет неравномерность распределения удельных давлений, а следовательно, и величина максимального скалывающего напряжения. В том же направлении действует и увеличение относительной жесткости прокатываемой полосы, представляющей собой отношение предела текучести к модулю упругости материала валка [169].
Кроме зоны упруго-пластического контакта, определяющей режим работы валков по механическим напряжениям, в ряде случаев опасными являются напряжения в упругом контакте (контакт опорного и рабочего валков). В этом случае усталостную прочност1 валка следует подсчитывать с учетом величины наибольшего напряжения цикла в контакте валок — валок.
Режим работы валков зависит также от вида эпюр межвалкового давления [139]. Как показали исследования, эпюра может быть выпуклой с максимальным значением межвалкового· давления в середине бочки валка,' ровной—с одинаковыми значениями по бочке валка и вогнутой — с максимальными значениями по краям бочки. Процесс холодной прокатки листов сопровождается значительным выделением тепла. Изучение теплового баланса на стане 1200 одного из заводов показало, что валки аккумулируют 2,4% тепла, выделяющегося при деформации полосы. При этом они нагреваются до 50—80° С. Температура валков по клетям (I—V) при прокатке жести, измеренная в паузах между прокаткой рулонов, соответственно равна 30—40, 45—50, 60—65, 45—55 и 60—70° С.
Разогрев валков и сопровождающие его изменения профилировки отражаются на устойчивости процесса прокатки. Кроме того, разогрев способствует возникновению температурных напряжений, непосредственно влияющих на стойкость и прочность валков. Для непрерывных станов устойчивость процесса прокатки является определяющей при оценке работоспособности валков.
Исследования, проведенные А. В. Третьяковым и др. на трехклетевом стане 740 и четырехклетевом стане 1700, позволили установить, что температура валков после перевалки постепенно повышается и примерно через 20—60 мин (после прокатки нескольких рулонов) устанавливается на определенном уровне. Цикл колебаний температуры при этом -становится стабильным; температура в паузах, скорости нагрева и охлаждения, перепад температур по длине бочки практически постоянны.
Установлено, что средняя скорость нагрева на участках разгона двигателя составляет 20—30° С/мин. Средняя скорость охлаждения на участках торможения соответственно равна: при автоматическом отключении подачи эмульсии в паузах между рулонами (или при быстром ручном охлаждении) 25—35° С /мин, при охлаждении эмульсией 40—60° С /мин; все это отрицательно сказывается на стойкости валков.
При нормальной работе стана разность температур между серединой и краями бочки может составлять 5—25° С. Это приводит к неравномерному тепловому расширению и перераспределению натяжения; зачастую отмечаются обрывы полосы [169]. Существенное влияние «а абсолютное значение и распределение температуры вдоль бочки оказывают количество и температура эмульсии, подаваемой на середину и края бочки, профиль и раз* нотолщинность подката, профилировка валков и др. Установлено, что наиболее целесообразно комбинированное охлаждение рабочих валков (снаружи эмульсией и изнутри водой). При этом снижаются максимальные скалывающие напряжения в поверхностном слое, существенно повышается устойчивость теплового профиля валков, а значит, и всего технологического процесса прокатки. Средняя стойкость валков при комбинированном охлаждении на 8—14% выше.
Таким образом, для определения оптимального режима работы валков необходимо знать величину и глубину зоны действия максимальных скалывающих напряжений в различных клетях непрерывного стана. Глубина действия максимальных скалывающих напряжений зависит от отношения среднего удельного давления к максимальному и от длины дуги контакта. Режим работы валков следует назначать с учетом несовпадения зон действия максимальных скалывающих напряжений в разных клетях непрерывного стана.
На стойкость валков большое влияние оказывают и контактные напряжения. При неравномерном распределении удельных давлений контактные напряжения могут вызвать разрушение поверхностных слоев валка. По данным зарубежной литературы, контактные напряжения считают допустимыми, если ртах = 2100 Мн/м2 (210 кГ/мм2), где /?тах—максимальное удельное давление на контакте.
Режимы работы валков холодной прокатки характеризуются значительными удельными давлениями [до 2500 Мн/м2 (250 кГ/мм2)], высокими контактными напряжениями и значительной относительной жесткостью полос (из-за высокой степени обжатия, достигающей 70—90%). Поэтому для повышения стойкости следует учитывать все факторы, влияющие на напряженное состояние валков.
Однако следует иметь в виду, что от 40 до 90% всех вводимых в эксплуатацию рабочих валков холодной прокатки в первые же моменты получают повреждения рабочей поверхности. Это приводит к значительному расходу закаленного слоя и в отдельных сл^^ чаях уменьшает усталостную прочность валков.
Интенсивность и частота повреждений рабочих валков холодной прокатки зависят от технологии производства, качества подката, сортамента холоднокатаного листа, скорости прокатки и типа стана. Иными словами, частота и интенсивность повреждения рабочей поверхности валков пропорциональны степени устойчивости процесса прокатки. Опыт работы ряда заводов показывает, что валки выходят из строя в результате естественного износа, поломок и вследствие возникновения поверхностных дефектов [170—176]. Валки с естественным износом подвергаются только плановой перешлифовке. Бели б результате многократных плановых перешлифовок расходуется весь закаленный поверхностный слой валка и твердость его оказывается недостаточной, валок списывают. Износостойкость валков зависит от структуры и твердости 'поверхности бочки, механических свойств прокатываемого металла, трения в очаге деформации и др.
Поверхностные дефекты валков можно разделить на две группы: к первой группе относятся дефекты, устраняемые при переточке валков: надавы (порезы, вмятины, хвосты), небольшие навары, мелкая сетка трещин, мелкая выкрошка и др.; ко второй — дефекты, вызывающие окончательный выход валков из строя (грубые навары, отслоения, отколы, трещины и др.) [169].
При отсутствии натяжения, обрывах полосы, задаче и выдаче концов из клетей на прокатываемой полосе могут образоваться складки, которые попадают в очаг деформации и вызывают повышенные давления, приводящие к продавливанию поверхности валка. В результате на поверхности остаются отпечатки складки, различные по глубине и площади (порез).
Кусочки металла, попадая на полосу и 'проходя через очаг деформации, продавливают поверхность валка, в результате чего возникают вмятины. Образование поверхностных дефектов происходит и в случаях, когда полоса, выходящая из клети, неравномерно обжимается. Вследствие этого одна сторона полосы вытягивается, и давление по мере выхода полосы из валков концентрируется на все уменьшающейся площадке. Если предел текучести валка будет превышен, произойдет местная пластическая деформация и останется отпечаток вытянутого конца в форме треугольника. Склонность к надавам (порезам, хвостам, вмятинам) возрастает с уменьшением твердости -бочки и глубины активного закаленного слоя.
При нарушении технологии холодной прокатки возможны обрывы полосы или «броски» ее в сторону при задаче переднего и выпуске заднего концов; при этом в очаг деформации попадают обрывки металла. При большом местном давлении и трении валок схватывается с металлом (образуется навар) и подвергается сильному разогреву с последующим резким охлаждением. Это приводит к объемным и структурным изменениям: возникают напряжения предельной величины и в месте навара образуются трещины, преждевременно выводящие валок из строя.
Сильные навары, получаемые при оковывании валков прокатываемым металлом, вызывают последующее отслоение или глубокое выкрашивание, -приводящее к окончательному выходу -валка из строя. Мелкие навары наблюдаются в основном на дрессировочном -стане и при прокатке тонких полос в последних клетях пятиклетевого стана.
Появление трещин (осевых или окружных различной глубины, сетки мелких трещин и т. д.) является результатом совместного действия внутренних (остаточных), контактных и температурных напряжений, возникающих в процессе эксплуатации, шлифовальных прижогов, а также структурных .превращений, которые могут происходить 'при прокатке. Навары, надавы, разогрев бочки, создавая местные концентр ад и и напряжений, приводят к появлению трещин, которые могут постепенно развиваться; трещины углубляются и неизбежно приводят к отслоениям или выкрашиванию металла с поверхности валка.
Выкрашивание по площади может быть мелким и крупным и по происхождению тесно связано с трещинами. Чем меньше суммарное (эквивалентное) напряжение, тем больше период работы валка до начала .выкрашивания. Крупные выкрашивания называются отколами.
Одним из наиболее распространенных дефектов валков холодной прокатки, прошедших поверхностную закалку, является отслоение, которое обычно наблюдается на поверхности бочки, контактирующей с прокатываемым металлом. Обычная глубина местных отслоений и кругового скалывания 'бочки находится в пределах от 5 до 25 мм; она зависит от распределения остаточных напряжений в закаленном слое, его физических и механических характеристик и глубины расположения максимальных скалывающих напряжений. Этот дефект, так же как и описанные выше, тесно связан с образованием очагов усталостного разрушения. Значительная часть отслоений наблюдается в тех местах поверхности валка, в которых ранее произошел навар или надав. В результате этого появляются микротрещины, которые в дальнейшем могут развиваться в очаги усталостных разрушений и привести к отслоению.
Местный разогрев бочки валка встречается редко, но приводит к окончательному выходу его из строя. Дефекты, связанные с местным повышением температуры, возникают по следующим причинам:
- При превышении предельно допустимого давления на валки в отдельных точках (в связи с неравномерностью распределения давления) местные контактные напряжения оказываются больше предела упругости материала валков, что при недостаточном отводе тепла вызывает появление очага разогрева.
- При достижении предельно допустимого удельного давления на валки в результате нагрева от трения скольжения и качения.
- При наличии на поверхности контакта мест с повышенными удельным давлением и коэффициентом трения вследствие неудовлетворительного шлифования или неравномерной насечки валков на дробеструйной машине.
- При низких и неравномерных 'механических свойствах материала валков.
При шлифовании на валках могут образоваться трещины, сетка, местный отпуск, что впоследствии приводит к выкрашиванию бочки с отслоением.
Поломки валков, как правило, вызываются: наличием значительных остаточных напряжений I и II рода в результате неудовлетворительной термической обработки; напряжениями, появляющимися в результате приложения внешних усилий (давления прокатки) и термического -воздействия в период -неустановившегося теплового режима валка, характеризующегося перепадами темпе-' ратуры в его сечениях; металлургическими дефектами (флокенами, дендритной ликвацией, неметаллическими включениями, повышенным содержанием серы и фосфора), понижающими прочность ма-. териала валков.
К случайным причинам выхода валков из строя прежде всего относят повреждения шеек и трефов. При несоблюдении правил перевалок возможен изгиб шейки, что выводит валок из строя. Задиры, забоины и коррозия валков появляются при небрежном обращении с ними при перевалках, транспортировании или хранении,. Эти дефекты способствуют образованию трещин, отслоений, выкрашиваний, вызывая бесполезный съем закаленного слоя [169].
А. В. Третьяков [134] указывает, что основной причиной выхода из строя валков является разрушение поверхностного слоя бочки, носящее часто контактно-усталостный характер. Возникновение этого дефекта связано с условиями изготовления (особенно термической обработки) и эксплуатации (режим обжатий, скорость прокатки, давление металла на -валки, натяжение полосы, степень и частота повреждений рабочей поверхности) валков. Один из наиболее распространенных и характерных дефектов валков — отслоение — вызывается образованием зон усталостного разрушения и зависит от величины суммарного напряжения и числа циклов нагружения валка. Допускается, что причиной отслоений может быть избыточное количество остаточного аустенита в закаленном слое.
В результате изучения большого количества поврежденных валков авторы [176] считают установленным, что первоначальной причиной отслаивания части закаленного слоя валков являются трещины, возникшие на поверхности бочки от прижогов, при местной перегрузке валка во время работы, сопровождающихся структурными изменениями в поверхностных слоях под влиянием рабочих напряжений прокатки. Из поверхностных слоев трещина развивается внутрь валка до некоторой критической глубины (7—17 мм), а затем снова приближается к поверхности бочки, увеличиваясь по площади. Весь процесс разрушения протекает в четыре стадии:
- зарождение первой микротрещины вблизи поверхности бочки или на самой поверхности;
- проникновение трещины в глубь бочки;
- медленное развитие трещины внутри -валка с увеличением площади и постепенным приближением к поверхности;
- отрыв осколка от валка.
В работах [133, 134, 169, 175—177] отмечается, -что условия службы -валков зависят от накопления на некоторой глубине от поверхностного слоя усталостных изменений, вызываемых скалывающими напряжениями. Появление отколов может быть ускорено действием локальной перегрузки (ή а дав, порез и т. д.). Выход ослабленного слоя на поверхность при перешлифовках учащает усталостные отколы и выкрашивания. Механизм усталостного разрушения валков представляется состоящим из двух этапов.
Во-первых, работа валка в нормальных условиях установившегося процесса прокатки, когда усталостные изменения постепенно накапливаются в глубинных зонах. Интенсивность этого -накопления определяется величиной максимальных касательных напряжений.
Во-вторых, работа валка в условиях резко увеличивающейся поверхностной нагрузки с возрастанием коэффициента трения при выходе конца полосы из валков, при порезах и обрыве полосы и пр. В этом случае в поверхностных слоях материала достигают предельного значения напряжения и происходит местное разрушение. Подтверждение такого механизма усталостного разрушения авторы видят в том, что глубина отколов и отслоений совпадает с глубиной расположения максимальных касательных напряжений и соизмерима с длиной дуги контакта. _
К выводу, что основной причиной выхода валков из строя по отслоениям, отколам и выкрашиваниям является неблагоприятное распределение остаточных напряжений в поверхностных слоях валка, пришли и некоторые другие исследователи [178, 179]. Л. И. Боровик и А. Ф. Пименов [178] считают, что глубина отслоений и скалывания упрочненного слоя толщиной от 5 до 15 мм зависит от распределения остаточных напряжений в этом упрочненном закалкой слое. Отслоения вызываются остаточными температурными и контактными напряжениями. Для выяснения влияния указанных причин на отслоения металла с бочек валков авторы проанализировали 150 случаев прокатки полос толщиной 0,5 мм и менее при среднем удельном давлении 1100—1300 Мн/м2 (110— 130 кГ/мм2) и установили, что валки, прошедшие закалку с нагрева токами промышленной частоты, имеют резкий переход от закаленного слоя к незакаленному, в результате чего более 50%' валков выходят из строя по отслоению.