Теория высокотемпературной прочности материалов
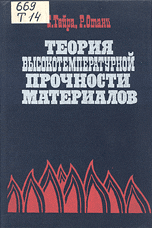
Тайра С., Отани Р.
Металлургия, 1986 г.
ПРАКТИЧЕСКИЕ ПРОБЛЕМЫ ВЫСОКОТЕМПЕРАТУРНОЙ ПРОЧНОСТИ И ВЫСОКОТЕМПЕРАТУРНЫЕ МАТЕРИАЛЫ
1.3.1.Котлы
Наиболее важной проблема высокотемпературной прочности является для больших котлов тепловых электростанций. Год за годом возрастали рабочие давления и температуры, повышались параметры котельных установок. В настоящее время давление пара в котлах сверхкритического давления превышает 25 МПа, а температура пара— 540 °С. На рис. 1.4 приведена схема котельной установки и указаны применяемые материалы. Наиболее важной частью установки являются трубы котла теплообменника. Объем производства этих труб очень велик, а применяются они в таких условиях, когда к ним предъявляются требования высокотемпературной прочности. В табл. 1.1 приведен химический состав сталей, применяемых для указанных труб. Размеры используемых труб (пароперегревательных, подогревательных) изменяются в широких пределах — наружный диаметр 35—60 мм, толщина стенок 3—12 мм, отношение внутреннего и наружного диаметров 1,2—1,9.
На рис. 1.5 показана котельная труба с трещиной. Ее вид сходен с цилиндрической трубой, разрушенной при испытаниях на ползучесть под внутренним давлением, описываемых ниже. Следовательно, высокотемпературная прочность, которая является наиболее важной проблемой для указанных труб, характеризуется Длительной прочностью. Материалы, указанные в табл. 1.2, в общем имеют высокую длительную прочность. То, что обычно углеродистые стали применяют при температурах до 450 °С, малолегированные стали при 450—600 °С, нержавеющие стали До 550—650 °С, обусловлено регламентацией допустимых напряжений с учетом сопротивления ползучести. На практике помимо сопротивления ползучести к сталям предъявляют требования свариваемости , способности к деформации изгибом , жаростойкости, коррозионной стойкости в продуктах сгорания. Аварии, происходящие в настоящее время, часто связаны с коррозионным воздействием среды.
1.3.2. Корпуса ядерных реакторов
На рис. 1.6 в качестве примера показан общий вид водоохлаждаемого ядерного реактора (PWR) с разрезом, а на рис. 1.7 приведена схема установки ядерного реактора на атомной электростанции и указаны основные материалы, применяемые для различных агрегатов. Используемые материалы незначительно отличаются от материалов для электростанций с котельной установкой. Температура пара на атомной электростанции низкая, поэтому длительная прочность материалов не вызывает каких-либо проблем. Однако серьезные проблемы вызывает деформация ползучести, так как толщина стенок корпусов реакторов составляет до 200 мм. Для них следует использовать материалы с большим сечением поглощения нейтронов, не содержащие бора и кобальта , вызывающего γ-излучение вследствие испускания нейтронов. В будущем, когда будут применяться реакторы-размножители и высокотемпературные реакторы с газовым охлаждением, условия работы материалов станут более жесткими, чем в котельных установках. При этом придется учитывать не только высокотемпературную прочность, но также возможность возникновения высокотемпературной малоцикловой усталости и термических скачков деформации.
1.3.3. Химическое оборудование
Высокотемпературная прочность материалов для химического оборудования стала важной проблемой в связи с увеличением размеров оборудования для нефтеочистных и нефтехимических заводов. В табл. 1.2 приведен состав применяемых в настоящее время жаропрочных сталей. Теплообменные аппараты на нефтеочистных заводах эксплуатируются при наиболее высоких температурах, для труб этих аппаратов применяют котельную сталь. На нефтехимических заводах рабочие температуры в реакционных башнях разложения нефти также очень высоки и достигают 800 °С, а в некоторых случаях приближаются к 1000 °С. При указанных высоких температурах оборудование эксплуатируется в течение длительного времени, поэтому к материалам предъявляется требование высокого сопротивления ползучести при повышенных температурах. В прошлом для этих целей использовали литые трубы из стали НК40, однако у этой стали в процессе эксплуатации происходит заметное изменение свойств, сопротивление термической усталости также вызывает определенные проблемы. В установках для очистки нефти применяемые материалы часто работают в атмосфере водорода при высоких температурах и давлениях, поэтому важной проблемой является охрупчивание, вызванное обезуглероживанием и зернограничными трещинами, обусловленными коррозионным воздействием водорода.
1.3.4. Паровые турбины
На электростанциях используются крупные высокомощные паровые турбины (рис. 1.8), конструкция которых является очень сложной с большим количеством различных деталей. К деталям, для которых проблема высокотемпературной прочности имеет наибольшее значение, относятся лопатки, ротор, корпус и болты. В табл. 1.3 указаны типичные стали, применяемые для этих деталей, и приведен их химический состав.
На лопатки турбины, определяющие долговечность всего агрегата, действуют центробежные силы, обусловленные их вращением, усилия статического изгиба под действием давления пара, и вибрационные нагрузки. В связи с этим для лопаток высокотемпературной ступени, находящихся под действием высокого давления, важным является обеспечение высокого сопротивления динамической ползучести, высокотемпературной многоцикловой усталости, термической усталости. К материалам для ступени низкого давления предъявляются высокие требования к прочности при растяжении, сопротивлению усталости и демпфирующей способности.
Важной деталью является ротор, вращающийся вместе с лопатками. К ротору ступени высокого или среднего давления (600— 300 °С) предъявляют требования высокого сопротивления ползучести и высокой длительной прочности, поэтому для него применяют жаропрочную сталь, в частности Сr — Mo— V. Материалы для роторов ступени низкого давления должны иметь высокую вязкость на образцах с надрезом; для них применяют высоковязкую сталь, в частности Ni— Сr — Mo— V. На рис. 1.9 показано распределение температур в высокотемпературной части
ротора. В осевом и в радиальном направлениях существует довольно высокий градиент температур, однако тепловая емкость ротора большая, поэтому при запуске и остановке турбины появляются еще большие температурные градиенты и, следовательно, термические напряжения, в результате циклического изменения которых становится возможной термическая усталость. На внутренних поверхностях ротора в результате повышения температуры при запуске возникают напряжения растяжения, на наружных — напряжения сжатия. Кроме того, наличие канавок под наружные лопатки в зонах, где температура наиболее высокая, обусловливает повышенный коэффициент концентрации напряжений, поэтому для роторов желательно использование материалов, у которых надрез вызывает упрочнение.
Корпус турбины имеет сложную форму с каналами для прохождения пара, поэтому для его изготовления необходимы материалы с хорошими литейными свойствами и свариваемостью. Корпус подвергается воздействию внутреннего давления высокотемпературного пара, также следует учитывать возможность термических скачков деформации и термической усталости из-за напряжений, возникающих при пуске и остановке турбины.
Болты являются важной деталью, применяемой в большом количестве не только для крепления корпуса, но и для фланцевого соединения клапанов и трубопроводов. Если уменьшается усилие затяжки болтов вследствие релаксации напряжений, то происходит утечка пара, поэтому для болтов необходимы материалы в высоким сопротивлением релаксации. Одновременно к болтам предъявляют требование высокой длительной прочности на образцах с надрезом, чтобы не происходило разрушения от углубления резьбы после их повторной затяжки. Необходимо также учитывать возможность охрупчивания материала болтов при длительной эксплуатации турбины. Кроме того, температурные коэффициенты линейного расширения соединяемых деталей не должны значительно различаться.
1.3.5. Газовые турбины
Газовые турбины, имеющие небольшие размеры, небольшую массу, сравнительно высокую мощность и обеспечивающие возможность быстрого запуска, довольно широко применяют для выработки электроэнергии. В будущем появится необходимость в турбинах еще более высокой мощности и с большей долговечностью. Эффективность газовой турбины зависит от температуры газа на входе в нее, поэтому целесообразно повышать насколько возможно указанную температуру. На рис. 1.10 приведена схема газовой турбины, а в табл. 1.4 даны основные материалы, применяемые для ее изготовления, и их химический состав. Состав материалов определяют с учетом жаропрочности и сопротивления высокотемпературной коррозии, вызванной продуктами сгорания. Рабочие температуры в турбине часто достигают 1000 °С. В настоящее время, чтобы повысить [4, 5] рабочие температуры выше 1000 °С, для деталей турбин успешно разрабатывают жаропрочные сплавы на никелевой основе, изготавливают лопатки из направленно затвердевших материалов и монокристаллических материалов. На рис. 1.11 представлена схема, иллюстрирующая прогресс в разработке жаропрочных сплавов и повышении их сопротивления ползучести.
Наиболее важной деталью с точки зрения высокотемпературной прочности является лопатка турбины (рис. 1.12). Вращающиеся лопатки подвергаются воздействию центробежных сил, поэтому к материалам лопаток предъявляют требование высокой длительной прочности. При пуске и остановке турбины в поперечном сечении лопатки возникает определенное распределение температур, показанное на рис. 1.13. На задней кромке лопатки, характеризующейся наибольшей амплитудой циклической деформации, при нагреве возникает деформация сжатия, при охлаждении — деформация растяжения. Вследствие этого возникает состояние, соответствующее термической усталости; в указанной зоне часто появляются трещины. Возникновение трещин в результате термической усталости возможно и в неподвижных лопатках.
В связи с необходимостью обеспечения высокого сопротивления термической усталости, как и для обеспечения высокой длительной прочности, нежелательно огрубление выделений на границах зерен и образование выделений σ-фазы, приводящее к охрупчиванию жаропрочных сплавов при длительной их эксплуатации. Следует указать, что серьезные проблемы вызывает высокотемпературная коррозия материалов, обусловленная присутствием ванадия, натрия и серы в продуктах сгорания. Для ее предотвращения не только подбирают соответствующий химический состав материалов, но и осуществляют обработку топлива и всасываемого воздуха, алитирование поверхности лопаток.