Теория и технология производства ферросплавов
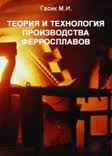
Гасик М.И.и др
Металлургия, 1988 г.
ОБЩИЕ ТРЕБОВАНИЯ К КАЧЕСТВУ ФЕРРОСПЛАВОВ
Качество ферросплавов характеризуется содержанием в пределами колебаний ведущего элемента, концентрацией регламентируемых сопутствующих примесей (С, S, Р, цветные металлы, N и др.), гранулометрическим составом, плотностью, состоянием поверхности кусков, слитка, температурой плавления, содержанием неметаллических включений, кислорода, водорода и др. Основным показателем качества ферросплавов является его химический состав и, прежде всего, содержание в нем ведущего элемента. В соответствии с требованиями изготовителей стали, заинтересованных в малой массе легирующей присадки, ферросплавная промышленность выпускает преимущественно сплавы с высокой концентрацией ведущего элемента. При этом важно постоянство содержания легирующего элемента в ферросплаве отдельных плавок, объединяемых в одну партию. Однородность химического состава ферросплавов характеризуется максимально допустимым отклонением от среднего содержания ведущего элемента в партии. Для большинства ферросплавов это отклонение устанавливается равным ±2%, что обеспечивает получение стали узкими заданными пределами содержания легирующих элементов.
Присадка ферросплавов в стальную ванну осуществляется, как правило, в заключительный период плавки, когда возможности рафинирования металла от примесей, внесенных ферросплавами, ограничены. В связи с этим стандарты на ферросплавы нормируют содержание примесей, вредное влияние которых на свойства стали установлено.
В первую очередь это относится к фосфору, сере и углероду. В настоящее время в стандарты на ферросплавы введены нормы содержания таких остаточных элементов, как титан, алюминий, ванадий, вольфрам, молибден и другие, контроль которых ранее не предусматривался.
Особо вредными в ферросплавах являются примеси цветных металлов (Сu, Pb, Zn, Sn, Sb, As, Bi, Cd), которые практически не удаляются из металла в процессе плавки. В связи с этим содержание цветных металлов в металлическом шихте, в первую очередь, в ферросплавах ограничивают. Особую актуальность этот вопрос приобрел в последнее время, поскольку в условиях вынужденного использования бедных и комплексных руд не всегда можно гарантировать постоянство химического состава.
Важной характеристикой качества ферросплавов является его гранулометрический состав, поскольку при правильном его выборе ускоряется процесс расплавления, обеспечивается высокое усвоение легирующего элемента и уменьшаются потерн ферросплавов при транспортировке. Допустимый размер кусков в стандартах характеризуется габаритными размерами (300 мм) или максимальной массой куска (5—45 кг). Для снижения потерь сплава специально оговаривается допустимое количество мелочи определенного класса крупности (3—10% фракции <20 мм). По требованию потребителей осуществляется поставка ферросплавов со строго заданным гранулометрическим составом. Внешний вид кусков сплава также дает представление о его качестве. Высококачественные ферросплавы не должны иметь окисленной поверхности, приварок шлака и обмазки изложниц, представляющих дополнительный источник газов и включений в стали. Практика сталеплавильных заводов свидетельствует о необходимости учета при оценке качества ферросплавов не только их химического состава, но и физических свойств (температуры плавления, плотности и др.), которые в значительной мере определяют эффективность процесса легирования стальной ванны. Недопустимо большое различие плотностей ферросплава и легируемого металла. Стандарты на ферросплавы пока не оговаривают уровень их физических свойств, хотя такие данные существенно облегчают выбор типа легирующей добавки при выплавке стали и сплавов различных марок. Важное значение имеют также механические свойства легирующих добавок, поскольку на их основе производится выбор дробильных устройств для получения заданного гранулометрического состава сплавов.
Выплавка ферросплавов сопровождается их загрязнением неметаллическими включениями. Это связано с повышенной концентрацией в ферросплавах элементов, обладающих значительным химическим сродством к кислороду. Поскольку непосредственная оценка количества включений в ферросплавах путем их подсчета или выделения с последующим анализом по массе в настоящее время встречает затруднения, целесообразно контролировать их по содержанию в сплаве кислорода, азота, серы и углерода. Растворимость этих элементов в ферросплавах определяет количество и форму содержащихся в них включений. Важным фактором, влияющим на качество стали и сплавов, является содержание в ферросплавах газов, в особенности водорода и азота. Наиболее опасен водород в ферросплавах на основе высокореакционных металлов (Ti, V, Nb, Са, Si), концентрация водорода в которых достигает 200 см3 на 100 г. Присадка таких ферросплавов в ковш приводит к рослости слитков. Более низкий уровень содержания водорода в ферросплавах особенно желателен при использовании дегазации стали под вакуумом. Прокаливание ферросплавов малоэффективно, так как позволяет удалить только влагу и не снижает, а иногда даже повышает, концентрацию кислорода и азота. Феррохром, например, вносит до 50% азота, содержащегося в коррозионностойкой стали. Хотя контроль газонасыщенности ферросплавов не предусмотрен действующими стандартами, ограничения по содержанию газон оправданы.
Очевидно, что требования к качеству ферросплавов должны устанавливаться в зависимости от их технологического назначения.