Технология прокатного производства. Книга 2
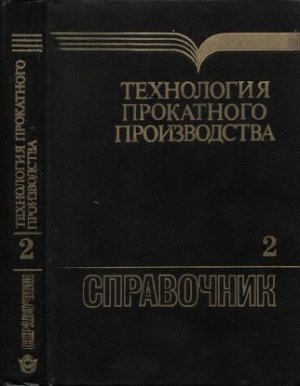
Зюзин В.И.(ред.) и Третьяков А.В. (ред.)
Металлургия, 1991 г.
V.2. ИСХОДНЫЕ ЗАГОТОВКИ И ИХ ПОДГОТОВКА К ГОРЯЧЕЙ ПРОКАТКЕ
V.2.1. Заготовки для производства горячекатаных листов и полос
В мировой практике для прокатки толстых листов на реверсивных станах используют катаные и непрерывнолитые слябы шириной 900 * -5- 3600 мм, толщиной 80 -s- 500 мм, длиной 1000 4000 мм и более. В ряде случаев исходным материалом служат слитки, масса которых достигает 40 - 45 т, а иногда (для прокатки особо толстых листов и плит) 100 и даже 250 т. Выбор типа заготовки определяется в основном размерами и назначением производимых листов, характеристиками оборудования и принятой технологией.
Листовые слитки обычно плоские с минимальной конусностью. В большинстве случаев поперечное сечение листовых слитков характеризуется отношением ширины к толщине 1,9 + 2,8. Другие параметры слитков [96]: отношение высоты к средней толщине 2,2 + 2,8; конусность узких граней 0,9 + 2,2 %, конусность широких граней 3,1 4,9 %, относительный объем прибыльной надставки 17,5 25,5 %. Боковые грани листовых слитков могут быть плоскими или выпуклыми. В последнем случае расход металла за счет боковой обрези снижается на 3 - 5 % от массы слитка Форма поперечного сечения слитков может отличаться от прямоугольной, а поверхность быть гладкой или ребристой. Для получения качественной листовой стали толщина слитков должна в 12 - 18 раз превышать толщину готового проката.
Требования к качеству слитков: отсутствие на поверхности продольных и поперечных трещин глубиной более 4 мм, неметаллических включений и других дефектов глубиной более 4 мм, сетки от разгара изложниц более 3 мм, утолщений слитка от разгара изложниц более 3 мм, утолщений слитка от разгара изложниц более 20 мм, подливов между прибыльной частью и телом слитка, а также подливов в нижней части слитка высотой более 15 мм. Слитки не должны иметь поясов, заворотов, надрывов и кольцевых трещин. В слитках спокойной и кипящей стали глубина залегания сотовых пузырей должна быть более 8 мм [96]. К внутренним дефектам литого металла относятся внутренние горячие трещины, газовые пузыри, осевая пористость, усадочная раковина, осевая ликвация и неметаллические включения. Некоторые виды перечисленных дефектов описаны ниже.
В качестве заготовок для прокатки на широкополосных станах служат только слябы: катаные размером 90 + 350 х 600 + 200 х 1500 + 14000 и литые толщиной 100 350 мм при максимальной ширине до 2340 мм.
Преимущества использования слябов следующие: улучшение качества поверхности и механических свойств готовых листов; более равномерный нагрев и эффективный контроль температуры прокатки; более высокая производительность станов; снижение количества типоразмеров изложниц при одновременном увеличении среднего веса слитков.
По способу производства различают катаные и литые слябы. Основными агрегатами для прокатки слябов являются слябинги. Кроме того, слябы прокатывают на блюмингах-слябингах и блюмингах. Литые слябы получают на машинах непрерывного литья заготовок (МНЛЗ). По сравнению с катаными литые слябы характеризуются большей структурной и химической однородностью, большим выходом годного, меньшими капитальными затратами на производство и себестоимостью. Для цеха с непрерывной разливкой производственные площади сокращаются на 50%, капитальные затраты уменьшаются на 40 %, а себестоимость тонны кипящих и спокойных сталей снижается в 2,7 раза по сравнению с разливкой стали в изложницы и последующей прокаткой на слябинге.
Сортамент и технические требования к катаным слябам из углеродистых и легированных сталей обусловлены ГОСТ 25715-83 и ОСТ 14-17-75. Размеры слябов и допускаемые отклонения, определяемые указанными стандартами, приведены в табл. V.8.
Косина реза слябов не должна превышать 30 мм, величина заусенцев от реза на ножницах - 10 мм, серповидность (кривизна по ширине) -10 мм на 1 м длины, неплоскостность - 20 мм на 1 м. Вогнутость или выпуклость боковых граней слябов не должна превышать 10 мм.
Форма, размеры и предельные отклонения непрерывнолитых слябов должны соответствовать ТУ 14-1-3347-82. Ромбичность (разность диагоналей) слябов в поперечном сечении не должна быть более 10 мм. Требования к косине реза и серповидности литых слябов соответствуют требованиям к слябам катаным.
Ряд исследований свидетельствует о большей точности размеров литых слябов по сравнению с катаными. Так, в работе [96] отмечается, что постоянную толщину по длине имеют ~ 60 % исследованных литых слябов и 35 % катаных, постоянную ширину - соответственно ~ 50 % и 10 %. Большие значения продольной разнотолщинности и разноширин-ности наблюдаются у катаных слябов.
Требования к качеству слябов не допускают на поверхности слябов плены, рванины, неметаллические включения, закаты, продольные и поперечные трещины. Появление и количество дефектов литых слябов определяются условиями разливки, химическим составом разливаемой стали, технологическими условиями выплавки, геометрическими размерами сечения слябов, конструкцией и состоянием оборудования МНЛЗ и т.д.
Все основные виды брака катаных слябов можно разделить на дефекты по вине сталеплавильного или прокатного производства.
Дефекты первого вида происходят главным образом из-за нарушений технологии выплавки и разливки стали. Из подобных дефектов наиболее часто встречаются трещины-расщепления, рыхлость, раскатанные трещины, слиточные плены, раскатанные пузыри, неметаллические включения. Брак по вине прокатного производства возникает в результате нарушения технологии нагрева или прокатки слябов. К основным видам брака по вине прокатного производства относятся рванины пережога, затянутая кромка, вкатанная окалина и раковины от нее, вкатанные металлические частицы или вмятины от них, скворечники, брак по размерам и геометрии слябов, закаты.
V. 2.2. Зачистка заготовок перед прокаткой
Зачистка заготовок с целью удаления поверхностных дефектов является одним из важных условий получения высококачественного листового проката. Поверхностные дефекты слитков и слябов выявляют путем осмотра с применением при необходимости светления или пробной зачистки. Применяют также неразрушающие методы контроля, обеспечивающие регистрацию дефектов различных размеров и глубину их залегания.
Выбор способа удаления дефектов и объем зачистки определяются в зависимости от марки стали, назначения готового проката, а также от особенностей технологии последующих нагрева и прокатки.
Удаление дефектов с поверхности слитков в холодном состоянии не всегда обеспечивает получение качественной продукции и не является эффективным, так как требует увеличения расхода топлива (или инструмента) и может привести к образованию дефектов при нагреве. Более рациональной является зачистка горячих слитков, однако это требует применения специального оборудования и в настоящее время не находит широкого применения. Поверхностные дефекты на слитках удаляют огневой зачисткой, строжкой или фрезерованием и пневматической вырубкой отдельных дефектов. Для зачистки слитков в горячем состоянии термофрезерные станки, позволяющие снимать стружку толщиной 3 - 7 мм в течение 1-2 минут. При удалении дефектов с поверхности слитков глубина зачистки не должна превышать 40 мм. Отраслевой стандарт ОСТ 14-17-75 допускает удаление дефектов с поверхности слябов (за исключением поперечных трещин и рванин от пережога) путем вырубки, абразивной или огневой зачистки (шлифования). Вырубка должна быть пологой, с шестикратным и более развалом (шириной не менее шестикратной глубины). Глубина вырубки или зачистки поверхностных дефектов не должна превышать на широких гранях слябов 25 мм, на узких гранях - 20 мм. Высота заплесков после огневой зачистки не должна быть более 2 мм.
Особо высокие требования предъявляются к качеству поверхности слитков и слябов из легированных и высоколегированных сталей. При этом перед зачисткой слитки могут подвергаться термообработке для снятия внутренних напряжений, устранения грубой структуры и уменьшения твердости. Нагрев и прокатку таких слитков выполняют после тщательного осмотра и зачистки дефектов.
При производстве листов и полос из легированных сталей по схеме слиток - сляб может применяться комбинированная обработка поверхности: огневая зачистка или горячее фрезерование слитков с последующей строжкой (фрезерованием) и абразивной зачисткой слябов. Применяются и другие сочетания способов удаления поверхностных дефектов [97].
Огневая зачистка
Огневая зачистка является наиболее распространенным и эффективным способом удаления поверхностных дефектов. В процессе огневой зачистки поверхностный слой металла, нагретый до высокой температуры, воспламеняется в струе кислорода, сжигается и удаляется с поверхности заготовки. Способ отличается высокой производительностью, высокой степенью механизации и автоматизации. Недостатком являются значительные потери металла.
Огневую зачистку применяют для ремонта слябов главным образом из углеродистых и низколегированных сталей. Огневая зачистка слитков и слябов легированных и нержавеющих сталей выполняется с применением специальных флюсов, повышающих температуру зачистки и образующих легкоплавкие шлаки. В качестве флюса применяется порошок из смеси 15 % магния и 85 % силикокальция [97]. Для трещиночувствительных нержавеющих сталей типа 12Х21Н5Т, 08Х18Т1 огневая зачистка слитков проводится при температуре 150 500 °С. Слябы многих низколегированных и легированных сталей перед зачисткой подогревают до 200 -5- 300 °С. Температура слябов из низкоуглеродистых сталей при зачистке в потоке достигает 600 + 750 °С.
Огневую зачистку слябов производят вручную или на машинах огневой зачистки (МОЗ). Ручную зачистку выполняют специальными кислородно-ацетиленовыми резаками. Ее применяют обычно для удаления местных дефектов при выборочном ремонте слитков и слябов.