Технология прокатного производства
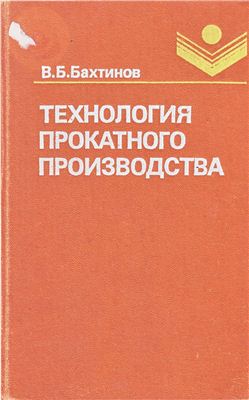
Бахтинов В.Б.
Металлургия, 1983 г.
УВЕЛИЧЕНИЕ СТОЙКОСТИ ПРОКАТНЫХ ВАЛКОВ
ЛЕГИРОВАНИЕ И МОДИФИЦИРОВАНИЕ МЕТАЛЛА
Важнейшей задачей в прокатном производстве является выпуск и освоение новейших профилей проката, поэтому необходимо иметь большое число разнообразных прокатных валков. Эти обстоятельства заставляют изыскивать средства для увеличения их стойкости. Износоустойчивые валки позволяют вести прокатку изделии с жесткими допусками по размерам и получать их с весьма чистой и высококачественной поверхностью.
Стойкость и твердость валков можно повысить, подбирая соответствующим образом их химический состав. Днепропетровским металлургическим институтом и ДЧВЗ проведена работа по выбору оптимальных параметров отливки валков из хромоникевого магниевого чугуна для черновых и предчистовых клетей мелкосортных станов. Установлено, что наиболее высокими прочностными показателями и запасом прочности при твердости HRC 56—60 обладают валки, отлитые из чугуна с содержанием 2,8—3,2 % С и до 0,35 % Сr, выплавленного в печи при скорости охлаждения 2,8°С/с. Результаты эксплуатации валков из хромоникелевого магниевого чугуна в черновых клетях мелкосортного стана 250 Криворожского металлургического завода показали, что стойкость валков, отлитых из такого чугуна, на 20—35 % выше стойкости ранее применявшихся валков из высокоуглеродистого (3,5—3,9 % С), хромоникелевого (0,4—0,8% Сr, 0,8-1,4% Ni) и магниевого чугунов.
На мелко- и среднесортных станах ММК применяют валки из высокохромистого чугуна (2,8—3,2 %С, до 0,6 % Si, до 0,6 % Μn, 14—16% Сr), а па рельсобалочных и крупносортных станах — с содержанием 2,8—3,1 %С, 0,8—1,0 % Si, до 1.0% Μn, 14-18% Сr.
На Енакиевском металлургическом заводе на сортопрокатных станах Енакиевского металлургического завода применяют хромоникелевые чугунные валки, модифицированные магнием и легированные никелем (2,0—2,5%). Увеличение содержания никеля в чугуне позволило придать продуктам эвтектоидного распада трооститную структуру и тем самым повысить износоустойчивость валков на 10 % и уменьшить их поломку на 30 %.
Валки из высокохромистого чугуна применяют на металлургическом заводе «Азовсталь» в чистовых клетях стана для прокатки двутавровых балок, швеллеров и рельсов. При прокатке двутавровой балки № 30 количество прокатанного металла, приходящегося на 1 мм уменьшения дна-метра при переточках, составляет для высокохромистых валков 78 и для хромоникелевых 46 т/мм, т. е. больше в 1,7 раза. Поверхность металла, прокатанного на валках из высокохромистого чугуна, более чистая, чем из хромоникелевого. Исследования, проведенные при прокатке одинаковых профилей на разных станах, показывают, что стойкость валков может быть различной. Так, стойкость валков черновых и предчистовых клетей НТМК в 2 раза выше стойкости таких же валков металлургического завода «Азовсталь».
Одной из причин повышения стойкости валков на НТМК является присутствие меди в прокатываемом металле, которая выходит на поверхность полосы, способствуя омеднению ручьев и их защите от коррозии.
Стойкость валков из хромоникелемедистого чугуна в 1,6 раза выше, чем из обычного хромоникелевого чугуна. Сопротивление износу валков, легированных медью, в 1,5 раза выше, чем обычных хромоникелевых. Положительное влияние на повышение прочностных свойств валков оказывает комплексное легирование хромом, никелем, кремнием, ниобием и другими элементами.
Самыми высокими прочностными свойствами обладают твердосплавные валки. Основные элементы твердосплавных валков — это твердые составляющие и связующий металл. Первые придают износоустойчивость и твердость, а связующие металлы — вязкость и прочность. Материал твердосплавных валков получают смешиванием в разных пропорциях различных твердых составляющих и связующих металлов. В качестве твердых составляющих применяют карбиды вольфрама WC, титана TiC, ниобия NbC и тантала ТаС. Связующим металлом обычно служит кобальт, в отдельных случаях никель.
УПРОЧНЕНИЕ ВАЛКОВ
Пробуксовки, которые возникают не только в момент захвата, но и при установившемся процессе прокатки, ведут к увеличению цикла прокатки и ударам. Известны случаи, когда пробуксовки были причиной поломок шпинделей и шестеренных валков. Поэтому стремятся увеличить коэффициент трения между прокатываемым металлом π валками, повышая захватывающую способность валков. На практике для улучшения захвата применяют следующие меры: уменьшают, если возможно, обжатие; снижают частоту вращения валков (уменьшают скорость прокатки); искусственно увеличивают коэффициент трения, нанося на валки насечку, нарубку, фрезеровку, наварку или накатку.
Уменьшение обжатий и скоростей прокатки приводит к снижению производительности прокатных станов. Поэтому наибольшее распространение за последние годы получили накатка π насечка поверхности валков. При нанесении насечек делают выемки круглой или прямоугольной (в виде точек или полосок) формы, при этом поверхность валков делается более шероховатой и захват металла улучшается. В некоторых случаях вместо насечки валков применяют наварку, которая также увеличивает шероховатость валков. Наварка по сравнению с насечкой имеет некоторые преимущества в том отношении, что она может быть выполнена аккуратнее насечки, без острых углов и резких переходов. Эти мероприятия позволяют увеличить обжатие (если они ограничиваются только возможностью захвата) на 20— 40 % и больше (см. рис. 18).
Искусственные меры улучшения захвата, основанные на увеличении коэффициента трения, имеют серьезные недостатки, заключающиеся в том, что насечка, наварка накатка оставляют на прокатанном металле следы и могут стать источником появления плен и рванин на готовом прокате. Поэтому их применяют только при прокатке малоответственных сталей и только в первых проходах на валках черновых клетей.
Встречаются две разновидности накатки: с целью создания шероховатой поверхности валков для повышения их захватывающей способности и уменьшения сетки разгара;
cцелью поверхностного упрочнения валков создаваемая наклепом.
На ММК на блюминге внедрена упрочняющая накатка боковых стенок калибров валков. Стойкость валков, упрочненных накаткой, повысилась в 1,2—1,6 раза, а межремонтный срок службы валков увеличился на 6—8 сут. Уменьшилась величина износа и улучшилось состояние поверхности калибров и прокатываемых полос.
На Енакиевском металлургическом заводе осуществляют рифление наклонных участков овальных калибров валков обжимной клети стана 280 дисковой накаткой и нарубкой. При дисковой накатке для рифления поверхности прокатных валков каждый диск вращается независимо от других, поэтому обеспечивается соответствие окружных скоростей дисков и накатываемой поверхности в каждой ее точке. Дисковая накатка позволяет выполнять рифление прокатных валков любой конфигурации.
БАНДАЖИРОВАНИЕ ВАЛКОВ
В результате многолетнего опыта эксплуатации универсальных клетей на НТМК установлено, что горизонтальные валки целесообразно делать сборными из стальных осей и чугунных бандажей. Это позволяет увеличить не только прочность, но н износоустойчивость валков. Для получения чугунных бандажей чугунные валы соответствующего диаметра разрезают на части и подвергают механической обработке. После расточки отверстия по нему подгоняют диаметр оси с учетом натяга 0,05—0,06 мм на 100 мм диаметра отверстия. Бандаж перед посадкой нагревают до 200—250 °С и в горячем состоянии насаживают на ось.
Составные валки хорошо зарекомендовали себя в работе. Если на валках из стали 60ХН с закалкой рабочей поверхности катали до 1000 τ облегченных двутавровых балок, то на составных валках прокатывают до 3000 τ при меньшем съеме металла при переточках.
На чистовых клетях стана 250-2 ММК внедрены валки с бандажами из сплава 250X24ВЗТ, разработанною Центральным научно-исследовательским институтом технологии машиностроения. Этот сплав содержит 2,3—2.6 % С, до 0,4 % Мn, 20-28 % Сr и 1-4%W.
Такое содержание углерода и хрома обеспечивает стабилизацию аустенита в интервале температур перлитного превращения.
При прокатке низко- и высокоуглеродистой, а также низколегированной стали стойкость валков с бандажами из сплава 250Х24ВЗТ в 4,8 раза превышает стойкость ранее применявшихся валков с бандажами из сплава 30X15. При изготовлении составных валков бандажи, насаживаемые на ось, как и цельнокованые вал кн. изготавливают в основном из стали марок 9Х, 9ХФ, 9X2. Осп составных калиброванных валков можно изготовлять из стали различных марок: углеродистой стали 70, хромистой стали
55Х, стали пружинной группы 55ХГ, сложно-легированной конструкционной стали 45ХНВ.
Для централизованного производства периодических заготовок турбинных лопаток на Ленинградском заводе турбинных лопаток с участием ВНИИметмаша разработан способ изготовления калиброванных валков. Каждая из боковых стенок и дно ручья выполнены в виде насаженных на ось четырех неподвижных бандажей и соединенных между собой ручьевыми секторами, ширина которых определяется длиной элемента периода изделия (рис,134). Бандажи удерживаются от осевого смещения зажимной гайкой, а от поворачивания — шпонкой. Изготовление сборных валков с различной глубиной ручьев позволяет использовать обычное токарное и фрезерное оборудование.
Предлагаемый валок для прокатки периодических профилей можно быстро и точно изготовить, так как его конструкция не требует применения трудоемких и дорогостоящих операций: изготовления ручьев па копировально-фрезерных станках и ручной доводки их геометрических размеров до требуемой точности и шероховатости поверхности.
ЭЛЕКТРОНАПЛАВКА ПРОКАТНЫХ ВАЛКОВ
Восстановление изношенных участков стальных прокатных валков электронаплавкой пол слоем флюса применяют па металлургических заводах страны с начала пятидесятых годов этого столетия. Автоматическая наплавка валков разработана Институтом электросварки им. Патона. Наплавляют также и новые валки, так как это позволяет получать на поверхности валков рабочий слон высокой износоустойчивости независимо от основного металла валков. Этим достигается возможность изготовлять сердцевину стальных прокатных валков из более дешевой стали, а изношенную поверхность восстанавливать неоднократной наплавкой в процессе эксплуатации, что способствует увеличению срока службы валков, а следовательно, сокращению их парка в прокатном цехе.
Применяют четыре способа наплавки стальных валков: легированной проволокой под флюсом, порошковой проволокой из порошка специального состава под нейтральным флюсом, малоуглеродистой сварочной проволокой под керамическим флюсом и металлокерамической электродной лентой. В качестве наплавляемого материала применяют следующее: электродную проволоку диаметром 3,6 мм марок ГШЗХ2В8, ППАН103, АН 104, АН106, ΛΗΙ24, АН 125, АН 170, ПП25Х5ФМС, СВ08; катанку диаметром 6,5 мм из стали 30ΧΓΛ; электродную ленту марок ЛМ-70ХЗМ, ЛМ-534ВЗФ под слоем флюса марок ЖСН-1, ЖСН-2, АН К-18, АН-20, ΛΗ-348Α, АН-28 и др. Наплавка валков под слоем флюса позволяет получать поверхностный слон на валках с твердостью до HS 84.
Сотрудники Криворожского металлургического завода и института электросварки им. Патона провели промышленное опробование наплавки валков в клетях черновой группы штрипсового стана металлокерамической электродной лентой.
Исследования показали, что стойкость валков, наплавленных меаллокерамическими электродными лентами ЛА-70ХЗМ и ЛМ-5Х4ВЗ, возрастает в 2—3 раза по сравнению со стойкостью при наплавке проволокой ППЗХ2В8. Металлокерамические исследования поперечных микро-шлифов, вырезанных из отработанного валка, показали, что на его поверхности сохраняются неизношенные наплавленные слои. Структурой основного металла валка является перлит с ферритной сеткой, а термически обработанного— измельченная перлитно-ферритная структура.