Технология получения качественной стали
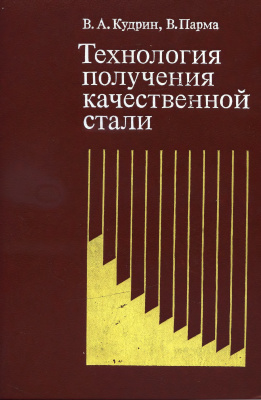
Кудрин В.П., Парма В.
Металлургия, 1984 г.
5. ОБРАБОТКА МЕТАЛЛА СИНТЕТИЧЕСКИМ ШЛАКОМ
Перемешивание металла со специально приготовленным ("синтетическим”) шлаком позволяет интенсифицировать процесс перехода в шлак тех вредных примесей, которые удаляются в шлаковую фазу (сера, фосфор, кислород). В тех случаях, когда основная роль в удалении примеси принадлежит шлаковой фазе, скорость процесса пропорциональна величине площади межфазной поверхности. Чаще всего этот способ используют для удаления серы, поэтому основным компонентом синтетического шлака является известь (иногда также плавиковый шпат); поскольку в таком шпаке практически нет окислов железа, он является одновременно хорошим раскислителем. В тех случаях, когда ставится задача очистить металл от неметаллических включений определенного состава, соответственно подбирают состав и синтетического шлака. На практике задача заключается, во-первых, в получении шлака нужного состава и температуры и, во-вторых, в разработке способа получения максимальной поверхности контакта шлаковой и металлической фаз. Естественно, что при этом должны быть обеспечены условия, необходимые для последующего отделения шлака от металла.
Обработка стали в ковше жидкими синтетическими шлаками, как способ очищения металла от нежелательных примесей, был предложен в 1925 г. советским инженером А.С.Точинским; в 1933 г. способ обработки металла жидкими известково-глиноземистыми шлаками был запатентован французским инженером Р.Перреном.
Из прошедших проверку способов обработки металла шлаками широкое распространение получили:
а) обработка стали при ее выпуске твердыми смесями (состоящими обычно из CaO и CaF2) расплавляющимися за счет тепла жидкой стали с целью десульфурации;
б) обработка стали жидкими известково-глиноземистыми шлаками с целью десульфурации и раскисления металла;
в) обработка металла во время разливки и кристаллизации шлаками различного состава с целью удаления вредных примесей и получения хорошей поверхности слитка;
г) введение на жидкий металл в ковше синтетических твердых смесей (состоящих из CaO, SiO2 и Al2O3), расплавление их за счет тепла дуг от электродов, вводимых через крышку ковша, и продувка металла снизу аргоном (или азотом) для перемешивания со шлаком с целью десульфурации и удаления неметаллических примесей.
В 1927 г. А.С.Точинский впервые в мире провел промышленные эксперименты по дефосфорации бессемеровской стали известково-железистым шлаком, а в 1928—1929 гг. рафинировал основную мартеновскую сталь кислым шлаком для раскисления (содержание кислорода в металле удалось снизить на 30—55 %). Позднее известково-железистые шлаки (60— 65 % CaO и 20—35 % окислов железа) неоднократно применяли для обработки конвертерной стали, получая высокую степень дефосфорации. Так, содержание фосфора в томасовской стали удавалось снизить с 0,060 до 0,010 %, а в рельсовой бессемеровской стали с 0,05-0,09 до 0,01-0,03 %. Опыт показал, однако, что обработка известково-железистым шлаком углеродистого металла приводит к бурному вскипанию и выбросам, Кроме того, обработка железистым шлаком затрудняла проведение операции раскисления металла.
Что касается метода обработки стали известково-глиноземистым шлаком, то в СССР соответствующие исследовательские работы были широко развернуты, начиная с 1959 г. в Центральном научно-исследовательском институте черной металлургии (ЦНИЦЧМ) и на ряде заводов. В процессе опытных работ были определены оптимальные составы шлаков для различных марок стали и сконструированы агрегаты для их расплавления и подачи к сталеплавильному агрегату. По технологии ЦНИИЧМ шпаки с высоким содержанием CaO и добавками Al2O3 (для снижения температуры их плавления и обеспечения необходимой жидко- текучести) расплавляют в специальной электропечи и заливают в сталеразливочный ковш при выпуске стали из сталеплавильной печи или из конвертера. При сливе металла на находящийся в ковше синтетический шлак обе реагирующие фазы (сталь и шлак) интенсивно перемешиваются, шлак эмульгирует в металле и в какой-то степени эмульгирует металл в шлаке с последующим разделением фаз. Интенсивность и глубина протекания процесса определяются высотой падения струи металла, массой металла и шпака, физическими характеристиками и составом шлака и др. Задача заключается в том, чтобы обеспечить в процессе обработки максимальную величину межфазной поверхности. Наибольшее влияние при этом имеет высота падения струи металла, а также вязкость шлака.
Разновидностью метода обработки стали жидкими синтетическими шлаками является так называемый метод смешения, когда в сталеразливочном ковше одновременно смешиваются и сталь,и синтетический шлак,и жидкая лигатура (расплавленные ферросплавы). В СССР метод смешения в сталеразливочном ковше полупродукта с жидкой лигатурой с одновременной обработкой синтетическим шлаком используется для производства высококачественной шарикоподшипниковой стали. Полупродукт состава ~ 0,35 % С; ~0,10 % Mn и следы Si выплавляют в мартеновской печи. Лигатуру состава — 3,2 % С; 0,6-2,0 % Mn; 1,3-3,4 % Si и 6,0- 6,5 % Cr получают в дуговой электропечи. Соотношение масс полупродукта и лигатуры ~4:1.
Малоуглеродистый полупродукт, не содержащий практически марганца и кремния, по отношению к составу лигатуры переокислен. Поэтому в момент смешения происходит быстрое раскисление полупродукта углеродом, содержащимся в лигатуре, с образованием газообразных продуктов раскисления, полностью удаляющихся из расплава. Все это происходит одновременно с воздействием на расплав залитого в ковш синтетического шлака, благодаря чему обеспечивается очищение металла от серы и неметаллических включений. В результате, например, из 100-т мартеновской плавки и 20-т плавки из ДСП получают 120 т высококачественной стали. Иногда плавку лигатуры совмещают с расплавлением синтетического шлака, т.е. в одной электропечи плавят и лигатуру и необходимое количество синтетического шлака; полученные таким образом лигатуру и шлак сливают в ковш, куда затем выпускают плавку из мартеновской печи или конвертера. Такой процесс называют "совмещенным” (рис. 84).
Метод смешения был разработан в 1970—1975 гг. на Ижевском металлургическом заводе. Он обеспечивает получение металла высокого качества. Так, по данным работы [ 52] долговечность подшипников из стали ШХ15, выплавленной по методу смешения, в 2,9 раза превышает обычную.
Такие способы, как метод смешения или совмещенный процесс позволяют, в необходимых случаях, обеспечить производство в мартеновском или конвертерном цехе высококачественной стали с использованием относительно простого оборудования. Общим и в том и в другом случаях является использование синтетического шлака, как доступного способа снижения содержания в стали серы и неметаллических включений и соответствуюшего повышения качества и надежности металла. Очень важным обстоятельством при этом является также возможность добиться при обработке металла синтетическим шлаком более стандартных показателей качества от плавки к плавке.
Расход синтетического шлака относительно невелик: 3—5 % от массы металла. При относительно малом количестве шлака легче обеспечить стандартность его состава и свойств. Поэтому обработка стали (с некоторыми неизбежными колебаниями состава и свойств от плавки к плавке) синтетическим шлаком строго стандартного состава и температуры позволяет решать очень важную задачу выпуска металлургическим заводом надежной и стандартной продукции. Дополнительные затраты на получение синтетического шлака оправдываются теми выгодами, которые получает народное хозяйство, используя более качественную сталь.
На основе разработок ЦНИИЧМ метод обработки металла синтетическим шлаком получил в СССР широкое распространение. ЦНИИЧМ разработана группа синтетических шлаков, в основном состоящих из извести и глинозема с содержанием кремнезема до 10-15 %, обладающих достаточной жидкоподвижностью при температурах жидкой стали; созданы шлакоплавильные печи непрерывного действия типа ОКБ-1320, позволяющие выплавлять шлак в количестве, достаточном для обработки 600— 800 тыс.т стали в год при расходе его 4-5 % по отношению к массе металла. В перспективе производительность этих печей может быть повышена более чем вдвое [ 53].
Основное требование, предъявляемое к синтетическим известковоглиноземистым шлакам — минимальная' окисленность (это обеспечивает хорошие условия для раскисления стали и ее десульфурации) и максимальная активность CaO. Поэтому в синтетических известково-глиноземистых шлаках не должно содержаться окислов железа вообще, а содержание кремнезема должно быть ограничено. Понятно, что наличие фосфора в таких шлаках исключается, так как при обработке он перейдет в металл. В тех случаях, когда в шихте, из которой плавят шлак, содержится некоторое количество кремнезема, в состав шлака вводят магнезию, образующую силикаты магния и уменьшающую, таким образом, вредное воздействие кремнезема, снижающего активность CaO. Обычный состав синтетического шлака, используемого на заводах СССР, следующий, %: 50-55 % CaO; 37-43 Al2O3; до 7 SiO2 (в некоторых случаях до 10-15 SiO2); до 7 MgO. Температура плавления шлака в зависимости от состава изменяется от ~ 1400 (в шлаке 50—55 % CaO; 38—43 % Al2O3 и <4,0 % SiO2) до ~ 1300 0C (в шлаке до 6-7 % SiO2 и 6-7 % MgO).
Для того, чтобы капельки шлака сами легко отделялись и всплывали, необходимо подбирать такие шлаки, величина межфазного натяжения которых на границе с металлом после окончания обработки металла была бы максимальной. Практика показала, что общее содержание неметаллических включений после обработки синтетическим шлаком уменьшается примерно в два раза.
Большим достоинством такого технологического приема, как обработка стали синтетическим шлаком, является ее кратковременность. Вся операция полностью осуществляется за время выпуска (слива) металла из агрегата в ковш, производительность агрегатов при этом возрастает, так как такие технологические операции, как десульфурация и раскисление, переносятся в ковш.
При проведении операции обработки металла шлаком приходится учитывать нежелательность попадания в ковш, в котором производится обработка, вместе с металлом также и шлака из печи или из конвертера, между тем задача отсечки шлака при выпуске металла из конвертера или мартеновской печи практически весьма сложна.
Сама обработка синтетическим шлаком позволяет несколько уменьшить окисленность металла, однако не настолько, чтобы полностью отказаться от применения раскислителей. Поэтому помимо шлака в ковш вводится необходимое количество раскислителей. Учитывая низкую плотность ферросилиция, необходимое его количество загружают на дно ковша еще до заливки в ковш синтетического шлака. После выпуска плавки на струю падающей в ковш стали присаживают такие материалы, как ферромарганец и феррохром. Вслед за этим присаживают сплавы, содержащие титан, ванадий, цирконий и т.п. Алюминий вводят в глубь ковша на штангах после окончания выпуска плавки.
В процессе перемешивания металла со шлаком состав шлака претерпевает определенные изменения; Эти изменения связаны со следующим:
а) при перемешивании шлак взаимодействует с футеровкой ковша, часть футеровки переходит в шлак;
б) из металла удаляется и переходит в шлак сера;
в) вводимые в ковш раскислители частично окисляются, образующиеся окислы переходят в шлак;
г) какая-то часть конечного шлака все же обычно попадает в ковш; содержащиеся в конечном шлаке окислы железа затрудняют протекание процессов раскисления. Особенно опасно попадание в ковш конечного шлака из-за содержащегося в нем фосфора: в процессе раскисления почти весь фосфор, содержащийся в конечном шлаке, восстанавливается и переходит в металл.
’’Разбавление” синтетического шлака в результате всех этих процессов может достигать 30—40 %. Однако и в том случае, когда определенная доля конечного шлака все же попадает в ковш, воздействие синтетического шлака на попадающий в ковш металл даже за те несколько минут, которые продолжается выпуск, оказывается положительным и обеспечивает заметное улучшение состава и свойств металла. И в этом случае полезным оказывается одновременное воздействие и шлака и раскислителей.
Примером технологии, когда печной шлак попадает в ковш и ’’разбавляет” залитый туда синтетический шлак, может служить технология, разработанная ЦНИИЧМ и OXMK [ 54] для 400-т мартеновских печей, работающих скрап-рудным процессом. Синтетический шлак из передаточного ковша заливают во время выпуска плавки на струю металла поочередно в сталеразливочные ковши, установленные под раздвоенным желобом. Шлак начинают сливать после выпуска в ковш части металла (5—20 %) и продолжают слив в течение 20—40 с. Окончание операции заливки шлака соответствует наполнению ковша металлом не более чем на одну треть. Максимальное количество ферросплавов вводят в ковш. После выпуска металла печной шлак не отсекают, а перепускают через сталеразливочные ковши. Расход синтетического шлака 17-22 кг/т при выплавке сталей типа 10ХСНД, 15ХСНД и до 53 кг/т для стали 12ГН2МФАЮ. Содержание серы в готовой стали составляет (в среднем) соответственно 0,015 % и < 0,012 %.
Практика показала, что при обработке шлаком стали с более низким содержанием углерода (имеющей, как правило, и более высокую окисленностъ) эффект рафинирования от кислорода проявляется в большей степени. Соответственно снижается расход раскислителей. Опыт показал, что рафинирование известково-глиноземистым шлаком низколегированной листовой конструкционной стали с низким содержанием углерода, выплавленной в 400-т мартеновских печах, позволяет стабилизировать угар раскислителей и легирующих и более надежно получать требуемый химический состав, а существенное повышение ударной вязкости стали позволяет расширить производство конструкционного металла, предназначенного для использования в северных районах страны, и получить экономический эффект при эксплуатации изделий из металла улучшенного качества.
Следует иметь в виду, что метод обработки металла синтетическим шлаком обеспечивает стандартные результаты десульфурации до известных пределов (обычно не более чем до 0,005—0,007 %). В тех случаях, когда необходимо устойчиво получать более низкие концентрации серы, используют другие способы, например обработку 1Целочно-или редкоземельными металлами. Так, например, в условиях Новолипецкого металлургического завода (НЛМЗ) при производстве стали для труб большого диаметра в северном исполнении, одного только рафинирования синтетическим шлаком оказалось недостаточно для получения требуемой ударной вязкости стали при низких температурах. Для этого оказалось необходимым понизить содержание серы до 0,003—0,005 %, что было достигну
то благодаря созданию комплексной технологии обработки металла синтетическим шлаком с отсечкой на выпуске конвертерного шлака и последующей обработки металла аргоном с одновременным вдуванием порошкообразных кальцийсодержащих материалов или редкоземельных металлов. Наряду с требуемым уменьшением содержания серы при такой технологии была снижена (примерно в три раза) и общая загрязненность металла включениями всех видов; включения в основном принимают глобулярную форму [ 53].
Широкое распространение метода обработки металла синтетическим шлаком на заводах СССР обусловлено рядом обстоятельств. Определенную роль играет то обстоятельство, что на значительной части территории страны условия эксплуатации металлоизделий в зимний период существенно осложняются. Для повышения вязкостных свойств и хладостойкости стали требуется снижение содержания серы. Снижение содержания серы не только повышает вязкостные свойства металла, но и заметно улучшает его свариваемость, что особенно важно при эксплуатации сварных конструкций.