Технология материалов электронной техники
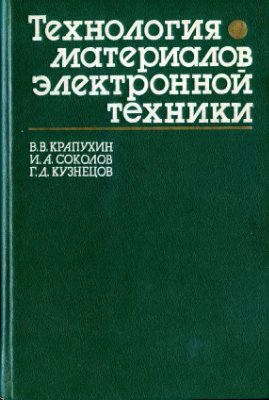
Крапухин В.В., Соколов И.А., Кузнецов Г.Д.
М.: "МИСИС", 1995 г.
ОСНОВНЫЕ ПРОЦЕССЫ ПОЛУЧЕНИЯ ПОЛУПРОВОДНИКОВЫХ МАТЕРИАЛОВ И ИХ МАТЕМАТИЧЕСКОЕ ОПИСАНИЕ
Глава 6. ПРОЦЕССЫ ОЧИСТКИ, ОСНОВАННЫЕ НА ФАЗОВОМ ПЕРЕХОДЕ ЖИДКОСТЬ - ПАР, И ПОЛУЧЕНИЯ ЭПИТАКСИАЛЬНЫХ СЛОЕВ, ПЛЕНОК И МОНОКРИСТАЛЛОВ ИЗ ПАРОВОЙ ФАЗЫ
Процессы очистки, основанные на фазовом переходе жидкость—пар, широко используются при получении высокочистых соединений элементов (чаще всего хлоридов и гидридов), а также высокочистых металлов и других элементов. Наиболее эффективным процессом очистки является ректификация, рассматриваемая в § 6.6. Высокочистые вещества используются в последующем для синтеза (получения) полупроводниковых соединений и выращивания монокристаллов, пленок и эпитаксиальных слоев элементов, полупроводниковых соединений и твердых растворов на их основе. Одним из методов получе¬ния указанных выше материалов является кристаллизация из паровой фазы.
Паровую фазу получают при испарении жидкой фазы и сублимации твердой. К процессам кристаллизации из паровой фазы будем относить такие, которые характеризуются отсутствием в паровой фазе химических реакций между компонентами. Применительно к пленкам процесс кристаллизации из паровой фазы называют также вакуум-термическим напыле¬нием; при этом в паровой фазе, кроме паров конденсирующихся компонентов, находится также достаточное количество оставшегося после откачки воздуха (парциальное давление ~10-3 Па). При выращивании эпитаксиальных слоев обычно используется более глубокий вакуум; этот процесс называется молекулярно-лучевой эпитаксией. Молекулярно-лучевая эпитаксия используется и при получении сверхрешеток.
При очистке веществ обычно используют термин дистилляции (включая в это понятие и процесс конденсации). Также при выращивании монокристаллов обычно используют просто термины дистилляция и сублимация; в этом случае в паровой фазе также может находиться инертный газ (водород, аргон).
§ 6.1. Примеры процессов получения материалов из паровой фазы
Получение тонких пленок и эпитаксиальных слоев
В тонкопленочной и эпитаксиалыюй технологиях наиболее-широко используются процессы, проводимые в вакууме. На рис. 6 показана схема вакуум-термической установки. Испаряемое (или сублимируемое) вещество (или вещества) помещают в испаритель 1 (или испарители, установленные на карусели испарителей 2).
Испаритель нагревают с помощью резистивного или другого типа нагревателя (на рисунке не показаны). Применение карусели испарителя позволяет в едином технологическом цикле испарять одновременно или поочередно различные вещества. Подложки 4, на которых происходит конденсация, укрепляются на карусели подложек 5, что позволяет поочередно устанавливать их над испарителем или испарителями. Под¬ложки нагревают специальным нагревателем 6. Для перекрытия потока пара на подложку используют заслонку 9. В камере 3 устанавливают экраны 8 для уменьшения потерь испаряемого вещества и снижения загрязнения стенок камеры и размещенных в ней деталей. В установке размещена также карусель масок 7, позволяющих получить пленки и эпитаксиальные слои требуемой площади и конфигурации.
Получение монокристаллов
Для получения монокристаллов методом сублимации обычно используются ампулы из кварцевого стекла. Перед проведением процесса испаряемое вещество (загрузку) помещают в ампулу, из которой затем откачивают воздух, и ампулу отпаивают. Для управления начальной стадией зарождения ампулу чаще всего делают с коническим концом, в котором начинается рост монокристаллов. Для переноса вещества от загрузки к месту конденсации ампулу помещают в печь с градиентом тем¬пературы (рис. 6.2). Рост монокристалла желательно проводить при медленном подъеме ампулы или опускании печи со скоростью, равной линейной скорости роста монокристалла.
При выращивании монокристаллов разлагающихся полу¬проводниковых соединений требуемого состава в области гомогенности в процессе сублимации в ампуле поддерживают давление пара летучего компонента, равное давлению диссоциации соединения данного состава при температуре конденсации, часто используя двухтемпературный метод (см. § 2.5). Один из вариантов установки схематично представлен на рис. 6.3. Исходную шихту 6 загружают в кварцевую ампулу 5 с патрубком 7, а селен — в отросток ампулы 1. Ампулу вместе с ее нагревателем 3 Помещают в печь 8 (рис. 6. 3, б), создающую температурный профиль, представленный на рис. 6.3, а. В отростке ампулы нагревателем 2 поддерживается температура, при которой давление насыщенного пара селена равно давлению диссоциации соединения данного состава при температуре конденсации. Для сублимации соединения в ампуле с помощью нагревателя 3 создается температурный профиль, показанный на рис. 6.3, в. Разность температуры шихты и конденсата в 1,5 К позволяет получить качественный монокристалл.
Получение высокочистых веществ
Схема наиболее простой установки для дистилляции веществ с температурой конденсации в твердую фазу ниже тем¬пературы охлаждающей воды (т. е. конденсированная фаза находится в жидком состоянии) представлена на рис. 6.4. Испаряемый раствор находится в кубе-испарителе 1, обогреваемом нагревательным элементом 2. Пар поступает в конденсатор змеевикового типа 3, и образующийся дистиллят стекает в сборник дистиллята 5. Кран 4 позволяет перекрывать сток ди¬стиллята из конденсатора и производить смену сборника дистиллята.
Схема эффективно работающей вакуумной дистилляционной установки непрерывного действия для очистки металлов от легкокипящего компонента показана на рис 6.5. В вакуумируемой камере 1 расположены один под другим полочные испарители 2, на которых задерживается тонкий слой дистиллируемо¬го вещества. Легкокипящий примесный компонент, испаряясь, конденсируется на водоохлаждаемых стенках камеры, которые периодически очищаются. Нагрев испаряемого с полочных испарителей вещества осуществляют резистивными элементами 5, расположенными во внутренней трубе. Непрерывную загрузку исходного расплавленного материала и выгрузку продукта после дистилляции осуществляют с использованием так называе¬мого барометрического затвора.