Технология литейного производства. Специальные виды литья
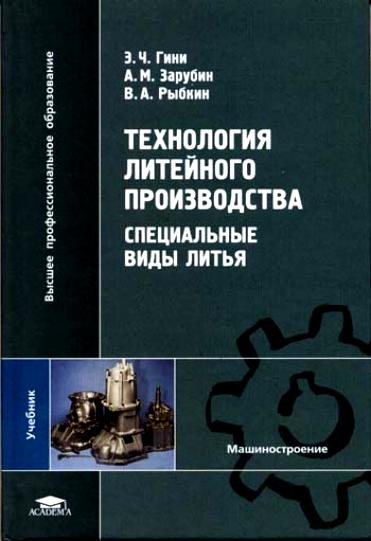
Гини Э.Ч., Зарубин А.М., Рыбкин В.А.
Академия, 2005 г.
Глава 1. Литье по выплавляемым моделям
1.1. Суть процесса. Основные операции. Область использования
1.2. Пресс-формы
1.3. Технология изготовления моделей
1.4. Изготовление оболочковых форм
1.5. Заливка форм, выбивка и очистка отливок
1.6. Изготовление керамических форм по постоянным моделям и керамических стержней
1.7. Автоматизация технологического процесса
1.8. Проектирование технологического процесса
Глава 2. Литье в кокиль
2.1. Суть процесса. Основные операции. Область использования
2.2. Кокили
2.3. Технология литья в кокиль
2.4. Кокильные машины и автоматизация литья в кокиль
2.5. Проектирование технологического процесса
Глава 3. Литье под давлением
3.1. Суть процесса. Основные операции. Область использования
3.2. Технология литья под давлением
3.3. Пресс-формы
3.4. Машины для литья и автоматизация литья под давлением
3.5. Проектирование технологического процесса
Глава 4. Литье под регулируемым давлением
4.1. Общие сведения
4.2. Литье под низким давлением
4.3. Литье с противодавлением
4.4. Литье вакуумным всасыванием
4.5. Вакуумно-компрессионное литье
Глава 5. Центробежное литье
5.1. Суть способа. Основные операции. Область использования
5.2. Технология изготовления отливок
5.3. Машины и автоматизация центробежного литья
5.4. Проектирование технологического процесса
Глава 6. Другиеспециальные виды литья
6.1. Литье по газифицируемым моделям
6.2. Литье по моделям, полученным методом лазерной стереолитографии
6.3. Непрерывное и полунепрерывное литье
6.4. Литье с последовательным заполнением и кристаллизацией
6.5. Литье выжиманием
6.6. Кристаллизация под давлением и штамповка из расплава
6.7. Электрошлаковое литье
6.8. Особенности изготовления отливок из титановых сплавов
6.9. Технология изготовления лопаток газотурбинных двигателей
6.10. Особенности технологии литья по выплавляемым моделям отливок художественного назначения
6.11. Литье в оболочковые формы
Список литературы
ЛИТЬЕ ПО ВЫПЛАВЛЯЕМЫМ МОДЕЛЯМ
1.1. Суть процесса. Основные операции. Область использования
Литье по выплавляемым моделям — это процесс, в котором для получения отливок применяются разовые точные неразъемные керамические оболочковые формы, получаемые по разовым моделям с использованием жидких формовочных смесей. Перед заливкой расплава модель удаляется из формы выплавлением, выжиганием, растворением или испарением. Для удаления остатков модели и упрочнения формы ее нагревают до высоких температур. Прокалкой формы перед заливкой достигается практически полное исключение ее газотворности, улучшается заполняемость расплавом.
Основныеоперации технологического процесса можно проследить по рис. 1.1. Модель или звено моделей 2 изготовляют в разъемной пресс-форме 7, рабочая полость которой имеет конфигурацию и размеры отливки с припусками на усадку (модельного состава и материала отливки) и обработку резанием (рис. 1.1. а). Модель изготовляют из материалов, либо имеющих невысокую температуру плавления (воск, стеарин, парафин), либо способных растворяться (карбамид) или сгорать без образования твердых остатков (полистирол). Готовые модели или звенья моделей собирают в блоки 3 (рис. 1.1,5), имеющие модели элементов литниковой системы из того же материала, что и модель отливки. Блок моделей состоит из звеньев, центральная часть которых образует модели питателей и стояка. Модели чаши и нижней части стояка изготовляют отдельно и устанавливают в блок при его сборке. Блок моделей погружают в емкость с жидкой формовочной смесью — суспензией для оболочковых форм, состоящей из пылевидного огнеупорного материала, например пылевидного кварца или электрокорунда, и связующего (рис. 1.1, в). В результате на поверхности модели образуется тонкий (менее I мм) слой 4суспензии. Для упрочнения этого слоя и увеличения толщины на него наносят слои огнеупорного зернистого материала 5(мелкий кварцевый песок, электрокорунд, зернистый шамот) (рис. 1.1, г). Операции нанесения суспензии и обсыпки повторяют до получения на модели оболочки требуемой толщины (3— 10 слоев).
Каждый слой покрытия высушивают на воздухе или в парах аммиака б, что зависит от связующего (рис. 1.1, д). После сушки оболочковой формы модель удаляют из нее выплавлением, растворением, выжиганием или испарением. Например, в процессе удаления выплавляемой модели в горячей воде 7 (/иолы £ 100 °С) получают многослойную оболочковую форму по выплавляемой модели (рис. 1.1, б). С целью упрочнения перед заливкой ее (форму) помещают в металлический контейнер и засыпают огнеупорным материалом 8 (кварцевым песком, мелким боем использованных оболочковых форм) (рис. 1.1, ж). Для удаления остатков моделей из формы и упрочнения связующего контейнер с оболочковой формой помещают в печь для прокаливания (рис. 1.1, з). Прокалку формы ведут при температуре 900... 1100 °С, далее прокаленную форму 10извлекают из печи и заливают расплавом (рис. 1.1, и). После затвердевания и охлаждения отливки до заданной температуры форму выбивают, отливки очищают от остатков керамики и отрезают от них литники.
Во многих случаях оболочки прокаливают в печи до засыпки огнеупорным материалом, а затем для упрочнения их засыпают предварительно нагретым огнеупорным материалом. Это позволяет сократить продолжительность прокаливания формы перед заливкой и сократить энергозатраты. Так, например, организуется технологический процесс на автоматических линиях для массового производства отливок (см. подразд. 1.7).
Малая шероховатость поверхности формы при достаточно высокой огнеупорности и химической инертности материала позволяет получать отливки с поверхностью высокого качества. После очистки от остатков оболочковой формы шероховатость поверхности отливок составляет от Rz= 20 мкм до Ra= 1,25 мкм.
Отсутствие разъема формы, использование для изготовления моделей материалов, позволяющих не разбирать форму для их удаления, высокая огнеупорность материалов формы, нагрев ее до высоких температур перед заливкой — все это способствует улучшению заполнясмости, дает возможность получать отливки сложнейшей конфигурации, максимально приближенной или соответствующей конфигурации готовой детали, практически из всех известных сплавов. Достигаемый коэффициент точности отливок по массе (КТМ = 0,85 ...0,95) способствует резкому сокращению объемов обработки резанием и отходов металла в стружку. Точность отливок может соответствовать классам точности 2 —5 по ГОСТ 26645 — 85 (изм. № 1, 1989), припуски на обработку резанием для отливок размером до 50 мм обычно не превышают 1 мм, а для отливок размером до 500 мм — около 3 мм. Поэтому литье по выплавляемым моделям относится к прогрессивным материале- и трудосберегающим технологическим процессам обработки металлов.
Краткие исторические сведения. Прообразом современного процесса литья по выплавляемым моделям является литье в формы, полученные по восковым моделям. Уже в Древнем Эламе И Вавилоне около 4 тыс. лет назад использовали восковые модели для изготовления литых украшении и других предметов быта. Этот способ был известен в Древнем Китае и Древней Индии. Позже он получает распространение в Европе. Находки отливок свидетельствуют о поразительном расцвете художественной обработки металлов у древних племен Кавказа 2,5... 3 тыс. лет назад.
В эпоху Возрождения великие художники и скульпторы использовали восковые модели для отливок художественных изделий — скульптур, украшений.
Восковые модели использовались и мастерами России как в статуарном литье, так и при литье колоколов, пушек, церковной и домашней утвари. Примерами высокого мастерства литейщиков прошлого является статуя Персея с головой Медузы в руке во Флоренции, исполненная скульптором Бенвенуто Челлини, или скульптурная группа в Санкт-Петербурге «Укротители коней», модели и отливки которой выполнил скульптор П.К.Клодт (с его именем связаны первые в истории отечественного литейного искусства статуарные работы; литейное дело изучал у известного мастера В. П. Екимова).
Позже литейный процесс стал использоваться в зубопротезном и ювелирном производствах. Его использованию в промышленности препятствовала низкая огнеупорность использовавшихся тогда формовочных материалов (скульптурной глины, которая наносилась слоями на модель и служила материалом формы).
Лишь в 1929 г. К. Прангль и Р. Ердл впервые применили огнеупорную суспензию, в которой в качестве связующего они использовали спиртовой коллоидный раствор кремниевого ангидрида. Сначала этот процесс нашел применение в стоматологии США, а позже — в массовом производстве мелких отливок из стали и тугоплавких сплавов.
Начало широкого освоения данного способа в промышленности России связано с необходимостью получения лопаток авиационных двигателей. Первая промышленная партия таких отливок из сплавов на кобальтовой и никелевой основе была получена в 1944 г. В конце 1940-х гг. освоено производство литых стальных деталей стрелкового оружия, швейных машин, бурового и металлорсжущсго инструментов. Дальнейшее развитие этого процесса способствовало его использованию в других отраслях машиностроения и в приборостроении. Таким способом стали получать отливки из разных сплавов, толщина стенки которых была менее 1 мм, а шероховатость поверхности и точность размеров позволяли значительно сократить объем обработки резанием или отказаться от нее. С этой целью стали производиться средства механизации и автоматизации процесса, на базе которых созданы автоматизированные литейные цехи по производству точных отливок.
Однако литье по выплавляемым моделям — процесс многооперационный. Манипуляторные операции при изготовлении и сборке моделей, нанесении суспензии на модель и другие достаточно сложны и трудоемки, что осложняет автоматизацию процесса. Процесс состоит из ряда длительных операций, определяющих производительность, таких, как послойное формирование и сушка слоев оболочковой формы на модели, прокалка формы. Из-за большого числа операций и технологических факторов, влияющих на размеры полости формы и соответственно отливки, может снижаться точность отливок. Качество отливок, получаемых данным способом, существенно зависит также от стабильности свойств исходных материалов для изготовления моделей, суспензии, формы и режимов технологического процесса. Это осложняет автоматизацию управления технологическим процессом.
Указанные особенности технологического процесса изготовления отливок в керамических оболочковых формах определили три основные проблемы его развития: 1) сокращение числа операций технологического процесса и их длительности наряду с упрощением манипуляторных операций с целью их автоматизации; 2) реализация резервов повышения точности моделей, форм и отливок, которыми обладает данный процесс; 3) создание систем автоматизированного управления технологическим процессом. 1
Особенности формирования отливок и их качество. Получение отливок в оболочковой форме сопряжено с рядом особенностей, в частности, перед заливкой форму нагревают до сравнительно высоких температур. Это определяет следующие технологические моменты.
Небольшие теплопроводность, теплоемкость и плотность материалов оболочковой формы и повышенная температура формы снижают скорость отвода теплоты от расплава, что способствует улучшению заполняемости формы. Благодаря этому возможно получение сложных стальных отливок с толщиной стенки 0,8...2 мм со значительной площадью поверхности. Улучшению заполнясмости формы способствуют также и малая шероховатость ее стенок, возможность использования внешних воздействий на расплав, таких, как поле центробежных или электромагнитных сил, заливка с использованием вакуума и др.
Невысокая интенсивность охлаждения расплава в нагретой оболочковой форме приводит к снижению скорости затвердевания отливок, укрупнению кристаллического строения, возможности появления в центральной части массивных узлов и толстых (6...8 мм) стенок усадочных дефектов — раковин и рыхлот. Тонкие же стенки (1,5... 3 мм) затвердевают достаточно быстро, и осевая пористость в них не образуется. Для уменьшения усадочных дефектов необходимо создавать условия для направленного затвердевания и питания отливок. Для улучшения кристаллического строения отливок используют термическую обработку.
Повышенная температура формы при заливке способствует развитию на поверхности контакта отливка —форма физико-химических процессов, результатом которых может быть как желательное изменение структуры поверхностного слоя отливки, так и нежелательное, т.е. приводящее к появлению дефектов поверхности.
Например, на отливках из углеродистых сталей характерным дефектом является окисленный и обезуглероженный поверхностный слой глубиной до 0,5 мм. Причина окисления и обезуглероживания отливок заключается во взаимодействии кислорода воздуха с металлом отливки при ее затвердевании и охлаждении. Эти процессы достаточно подробно рассмотрены в работах [10, 13]. Основные факторы, влияющие на процесс обезуглероживания, — это состав газовой среды, окружающей отливку, температура отливки и формы, содержание углерода в отливке. С увеличением содержания в среде, окружающей отливку, газов-окислителей 02, CO2 и паров Н2O при высоких температурах отливки и формы процессы обезуглероживания интенсифицируются. Поэтому небольшая скорость охлаждения отливки в нагретой оболочковой форме способствует увеличению глубины обезуглероженного слоя отливки. Увеличение содержания углерода в стали повышает интенсивность обезуглероживания поверхностного слоя отливки. Для уменьшения глубины обезуглероженного слоя используют специальные технологические приемы, основанные на предотвращении или уменьшении контакта кислорода воздуха с затвердевающей отливкой, на создании вокруг отливки восстановительной газовой среды и на быстром охлаждении, т.е. сокращении длительности реакции.
* На отливках из легированных сталей следствием физико-химического взаимодействия материалов формы и отливки при высоких температурах являются точечные дефекты (питтинги), приводящие к снижению коррозионной стойкости, жаростойкости и жаропрочности отливок и их браку.
Предупредить появление этого дефекта можно созданием восстановительной газовой среды в форме; проведением заливки форм в вакууме, в нейтральной или защитной среде; уменьшением или устранением взаимодействия оксидов отливки и формы; заменой се огнеупорного материала, например кремнезема, высокоинертными основными (магнезитовыми, хромомагнезитовыми).
Наконец, стремление получить отливки с чистой гладкой поверхностью вызывает необходимость использования огнеупорных материалов с малыми размерами зерна основной фракции (менее 0,05 мм). Это снижает газопроницаемость оболочковой формы до нескольких единиц, создаст опасность образования воздушных «мешков» в форме при ее заполнении, приводит к снижению заполняемое™ формы и образованию дефектов отливки из-за незаполнения формы.
Эффективность производства и область применения. Исходя из производственного опыта можно выделить ряд преимуществ способа литья в оболочковые формы по выплавляемым моделям: 1) возможность изготовления практически из любых сплавов отливок сложной конфигурации, тонкостенных, с малой шероховатостью поверхности, высоким коэффициентом точности по массе, минимальными припусками на обработку резанием, с резким сокращением отходов металла в стружку; 2) возможность создания сложных конструкций, объединяющих несколько деталей в один узел, что упрощает технологию изготовления машин и приборов; 3) возможность экономически выгодного осуществления процесса в единичном (опытном) и серийном производствах, что важно при создании новых машин и приборов; 4) уменьшение расхода формовочных материалов для изготовления отливок, снижение материалоемкости производства; 5) улучшение условий труда и уменьшение вредного воздействия литейного процесса на окружающую среду.
Наряду с преимуществами данный способ обладает и следующими недостатками: I) процесс изготовления формы многооперационный, трудоемкий и длительный; 2) большое число технологических факторов, влияющих на качество формы и отливки, и соответственно связанная с этим сложность управления качеством; 3) большая номенклатура материалов, используемых для получения формы (материалы для моделей, суспензии, обсыпки блоков, опорные материалы); 4) сложность манипуляторных операций изготовления моделей и форм, сложность автоматизации этих операций; 5) повышенный расход металла на литники и поэтому невысокий технологический выход годного (ТВГ).
Указанные преимущества и недостатки определяют эффективную область использования литья в оболочковые формы по выплавляемым моделям, а именно:
1) изготовление отливок, максимально приближающихся по конфигурации к готовой детали, с целью снизить трудоемкость обработки труднообрабатываемых металлов и сплавов резанием, сократить использование обработки давлением труднодеформи-руемых металлов и сплавов, заменить трудоемкие операции сварки или пайки для повышения жесткости, герметичности, надежности конструкций деталей и узлов;
2) изготовление тонкостенных крупногабаритных отливок повышенной точности с целью уменьшить массу конструкции при повышении ее прочности, герметичности и других эксплуатационных свойств;
3) изготовление отливок повышенной точности из сплавов с особыми свойствами и структурой.
Производство отливок по выплавляемым моделям находит широкое применение в разных отраслях машиностроения и в приборостроении. Использование литья в оболочковые формы для получения заготовок деталей машин взамен изготовления их из кованых заготовок или проката приводит к снижению в среднем на 34...90% отходов металла в стружку. При этом трудоемкость обработки резанием уменьшается на 25...85%, а себестоимость изготовления деталей — на 20...80%. Однако следует учитывать, что экономическая эффективность существенно зависит от выбора номенклатуры отливок, изготовляемых этим способом. Только при правильном выборе номенклатуры деталей достигается высокая экономическая эффективность данного производства.
Требования к пресс-формам. Пресс-форма — это инструмент для изготовления модели. От требований к точности модели зависит необходимая точность размеров полости формы и соответственно размеров отливки. Поэтому главное требование к пресс-форме заключается в том, чтобы в ней можно было получить модели отливки с заданными точностью размеров и шероховатостью поверхности.
Точность размеров модели и качество воспроизведения се конфигурации зависят от точности размеров полости пресс-формы и ее конструкции; чем меньше разъемов имеет пресс-форма, тем выше точность моделей. Поэтому всегда стремятся использовать минимальное число разъемов. Однако для получения сложных моделей приходится делать несколько разъемов, чтобы модель можно было извлечь из пресс-формы.
Для хорошего заполнения полости пресс-формы модельным составом она должна иметь соответствующие литниковую систему, а также вентиляционную систему, обеспечивающую удаление воздуха из полости пресс-формы при заполнении ее модельным составом.