Технологическое оборудование металлургических заводов
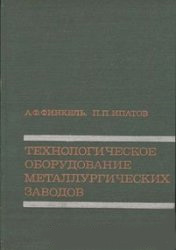
Финкель А.Ф., Ипатов П.П.
Металлургия, 1975 г.
КЛАССИФИКАЦИЯ И ХАРАКТЕРИСТИКА ПРОКАТНЫХ СТАНОВ
Рабочие клети прокатных станов в зависимости от расположения валков и их числа делятся на следующие шесть групп: дуо, трио, кварто, многовалковые, универсальные и клети специальной конструкции.
По направлению вращения валков клети делятся на реверсивные, в которых направление вращения валков меняется после каждого прохода прокатываемого металла, и нереверсивные, т. е. с постоянным направлением вращения валков.
Клети дуо 1 (рис. 115) состоят из двух валков, расположенных один над другим. Валки имеют общий или раздельный привод. В непрерывных станах применяются нереверсивные клети, при этом прокатываемая полоса проходит через клеть один раз. Реверсивные клети дуо применяют в блюмингах, слябингах и толстолистовых станах.
Клети трио 3 состоят из трех валков. Они широко применяются в сортовых станах и являются нереверсивными. Прокатываемая полоса движется в одну сторону между верхним и средним валками, а в другую — между средним и нижним. Для подъема прокатываемой полосы применяют подъемно-качающиеся столы или другие устройства. В клетях трио можно расположить больше калибров, чем в клетях дуо, так как калибры среднего валка являются общими. Существуют также листовые клети трио Лаута 2, которые применяют для прокатки листов толстых и средних толщин небольшой длины. Прокатку осуществляют так же, как и в сортовых клетях трио. Диаметр среднего валка меньше диаметров верхнего и нижнего валков. Средний валок не имеет привода и в процессе прокатки прижимается то к верхнему, то к нижнему валку и вращается в результате трения, возникающего между ними.
Клети кварто 5 имеют четыре валка, расположенные один над другим в вертикальной плоскости. Два средних валки являются рабочими, а верхний и нижний валки — опорными, которые служат для уменьшения прогиба рабочих валков. Клети кварто бывают реверсивными 6 и нереверсивными 5. Они применяются для прокатки толстых и тонких листов, а также полос и броневых плит.
Многовалковые клети бывают шести- 7, двенадцати- 8 и двадцати валковыми 9. Рабочими являются два валка, а остальные — опорные, которые придают жесткость клети. Рабочие валки двенадцати- и двадцативалковых клетей имеют диаметр 10—50 мм, не имеют привода и применяются при прокатке стальной тонкой ленты толщиной 0,002— 0,01 и шириной 100—1500 мм.
Универсальные клети 4 имеют горизонтальные и вертикальные валки. Вертикальные валки осуществляют обжатие полосы с боковых граней. Универсальные клети применяют, как реверсивные клети дуо на слябингах и толстолистовых станах. В этом случае вертикальные валки делают приводными. Для прокатки высоких двутавровых балок с широкими полками применяют универсальные клети 11 с неприводными вертикальными валками.
Рис. 115. Рабочие клети с различным расположением валков:
1— клеть дуо; 2 — клеть трио Лаута листовая; 3 — клеть трио сортовая; 4 — универсальная клеть дуо; 5 — клеть кварто листовая нереверсивная; 6 — клеть кварто реверсивная для прокатки полосы в рулонах; 7 — клеть шестквалковая; 8 — клеть двенадцативалковая; 9—клеть двадцативалковая для прокатки тонкой полосы; 10 — комбинированная многовалковая клеть; 11—клеть универсальная для прокатки двутавровых балок с широкими параллельными полками
Для прокатки колес, колец, шаров и др. применяют клети специальной конструкции.
По взаимному расположению и числу рабочих клетей прокатные станы разделяются на одноклетевые, линейные многоклетевые, последовательные, последовательно-непрерывные (полунепрерывные) и непрерывные.
Одноклетевые станы, как правило, реверсивные. Они имеют одну рабочую клеть, шестеренную клеть, редуктор, главный электродвигатель и соединительные устройства. К этой группе станов относятся блюминги, слябинги, толстолистовые трио Лаута, кварто и универсальные.
Клети линейных станов расположены в одну, две, три и более линий. Первую линию называют обжимной; обычно она состоит из одной клети. Последующие линии соответственно называют черновой и чистовой; они могут состоять из трех, пяти и более клетей. Каждая линия клетей имеет свой привод. На станах этого типа прокатывают рельсы, балки, сортовой профиль и проволоку.
Последовательные станы имеют ряд последовательно расположенных клетей, число которых равно числу проходов полосы, так как она через каждую клеть проходит только один раз. Для уменьшения общей длины стана его клети располагают зигзагообразно (станы кросс-коунтри) или в шахматном порядке. Станы этой группы имеют высокую производительность и применяются для прокатки сортовых профилей.
Полунепрерывные станы применяются для прокатки мелкого сорта, проволоки и полос. Эти станы состоят из двух групп клетей — непрерывного и линейного станов.
Непрерывные станы состоят из ряда последовательно расположенных клетей, в каждой из которых прокатываемая полоса проходит один раз, полоса одновременно прокатывается в нескольких клетях. Скорость вращения валков и обжатия в каждой клети при этом подбирают и регулируют так, чтобы не создавалось чрезмерное натяжение полосы или петлеобразование между клетями. Непрерывные станы используют как заготовочные, широкополосные, мелкосортные, проволочные и станы холодной рулонной прокатки листов.
Станы этой группы позволяют вести прокатку с большой скоростью, организовать непрерывность технологического процесса, механизировать и автоматизировать процесс прокатки и, следовательно, резко сократить ручной труд.
Прокатные станы называют в зависимости от выпускаемой продукции. Так, например, на листовых станах прокатывают листовую сталь, на рельсобалочных станах — рельсы и балки и т. д.
На листовых станах максимальная ширина прокатываемой полосы всегда меньше на 150—300 мм длины бочки валка.
При наличии нескольких клетей основным параметром стана является диаметр валков последней чистовой клети.
Скоростью прокатки стана называют скорость прохождения прокатываемого металла в валках последней чистовой клети, которую измеряют метрами в секунду. На различных станах скорость прокатки колеблется в пределах от 1 до 40 м/с.
Классификация прокатных станов по назначению приведена в табл. 2.