Технологические процессы обработки металлов давлением с локальным нагружением заготовки
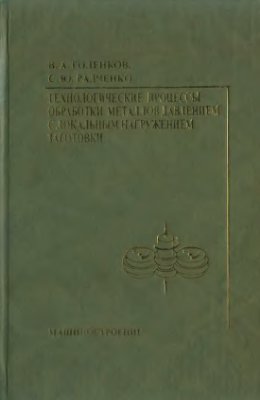
Голенков В.А., Радченко С.Ю.
Машиностроение, 1997 г.
1.2. ТЕХНОЛОГИЯ И ОБОРУДОВАНИЕ ДЛЯ ИЗГОТОВЛЕНИЯ ПРИБОРОСТРОИТЕЛЬНЫХ ДЕТАЛЕЙ
Применение осесимметричных деталей со ступенчатой наружной и внутренней поверхностью, имеющих высокую стенку стакана, наружную или внутреннею резьбу, обусловлено наиболее рациональным распределением нагрузочных напряжений в них при минимальной материалоемкости.
Большое значение при выборе варианта изготовления имеют точность детали, программа выпуска, сложность, геометрические размеры заготовки и детали, состав применяемых материалов, возможности имеющегося оборудования, степень научной обоснованности, разработки и экспериментальной проверки выбранного технологического процесса. Выбор технологии зависит во многом от требований, предъявляемых к конечному изделию, особенностям его эксплуатации.
Технология изготовления осесимметричных деталей включает процессы обработки резанием и обработки давлением.
При высоком качестве основным недостатком обработки резанием является низкий коэффициент использования материала (0,2...0,6) и низкая производительность.
Применением обработки металлов давлением (ОМД) достигается деформационное упрочнение, отсутствие надрезов, улучшение макроструктуры, увеличение коэффициента использования металла до 0,8 и более. Известны следующие основные способы ОМД[1 -3]:
- ковка и штамповка на молотах и гидравлических прессах;
- горячая штамповка на кривошипных горячештамповочных прессах (КГШП) и горизонтально-ковочных машинах (ГКМ);
- холодная объемная штамповка;
- поперечно-клиновая и поперечно-винтовая прокатка.
Ковкой [4, 5] можно получать высококачественные крупные заготовки под последующую обработку. Ковка является одним из наиболее экономичных способов получения высококачественных заготовок в единичном производстве и единственно возможным способом получения заготовок большой массы.
Однако, для изготовления деталей приборостроительной номенклатуры (малой массы) ковка практически не применяется вследствие невысокой геометрической точности получаемых изделий; что требует значительных доводочных операций и повышенного расхода металла, а также сравнительно низкой производительности.
Широкое распространение горячей штамповки [6, 7] обуславливается ее преимуществами перед ковкой, а именно:
- более высокой производительностью;
— штампованные поковки имеют значительно меньшие припуски и допуски, вследствие чего уменьшается расход металла.
К недостаткам горячей объемной штамповки следует отнести приложение больших, чем при ковке, сил деформирования, так как при штамповке одновременно деформируется вся поковка, а течение металла затрудняется сопротивлением стенок полости штампа.
Кроме того, при нагреве заготовки, особенно малого размера, поверхностные явления (окалинообразование, обезуглероживание, выгорание) приводят к существенному снижению качества получаемых поковок и необходимости последующей обработки резанием.
Таким образом, наиболее рациональной для получения выделенного класса деталей является холодная объемная штамповка [8 - 11]. Холодная объемная штамповка на холодновысадочных автоматах, роторных и роторно-конвейерных линиях успешно применяется для выпуска широкой номенклатуры стандартизованных деталей (крепеж, гильзы и т. д.), однако, в мелкосерийном производстве применение такого оборудования не всегда экономически целесообразно из-за высокой трудоемкости изготовления инструмента и большой длительности переналадки оборудования. Кроме того, на оборудовании данного класса трудно получать детали со сложной ступенчатой формой боковой поверхности, а также детали с высокой тонкой стенкой стакана (для изготовления которых применяется обратное выдавливание) вследствие весьма значительных сил деформирования и низкой стойкости инструмента.
Расширение области применения холодной объемной штамповки может быть достигнуто улучшением эксплуатационных свойств и усложнением формы штампуемых деталей. Значительным резервом технологии изготовления ступенчатых по наружной и внутренней поверхности осесимметричных деталей является сочетание холодной объемной штамповки с другими видами холодного деформирования — специальными видами обработки с локальным нагружением, в частности, поперечно-клиновая и поперечно-винтовая прокатка, раскатка.
В процессе поперечно-клиновой прокатки [12] заготовку деформируют парой клиновых инструментов, которые по мере движения перемещают очаг деформации вдоль оси заготовки в соответствии с углом наклона деформирующих клиньев. Заготовка при этом вращается под действием инструмента вокруг своей продольной оси, расположенной перпендикулярно движению клиньев. В результате обжатия и раскатывания металла наклонными гранями инструмента происходит уменьшение диаметра деформируемого участка заготовки и увеличение ее длины. Поперечно-клиновой прокаткой можно получать изделия типа ступенчатых валов с разнообразной формой поверхностей, с продольными и поперечными канавками, с резкими и плавными переходами между ступенями. Размеры обрабатываемых изделий ограничиваются возможностями оборудования и, как правило, не превышают 100 мм по диаметру и 800 мм по длине при обработке штучных заготовок.
Процесс поперечно-клиновой прокатки позволяет получать точные заготовки с припуском под шлифовку либо с окончательными размерами. Так, для диаметров до 30 мм допуск может составлять ± 0,1 мм, а для диаметров до 100 мм - ± 0,4 мм.
Однако обеспечение такой точности связано с высокими и зачастую невыполнимыми требованиями к инструменту, технологии и оборудованию. Поэтому заготовки, получаемые клиновой прокаткой, как правило, обрабатывают резанием с применением обточки по наружным поверхностям.
Недостатком является также невозможность получения отверстий в деталях. Кроме того, из-за наличия холостого хода плоского клинового инструмента процесс прокатки имеет меньшую производительность по сравнению с прокаткой по другим схемам, а ограниченность хода деформирующих клиньев сужает технологические возможности процесса.
При поперечно-винтовой прокатке [13 - 15] происходит последовательное обжатие различных участков длинной прутковой заготовки, перемещающейся в винтовых калибрах. В результате образуется периодический круглый профиль. Помимо фасонных периодических профилей, шаров и цилиндрических заготовок, поперечно-винтовой прокаткой изготавливают кольцевые и втулочные изделия, профилированные по наружному диаметру трубы. Кольцевые и втулочные изделия получают из прутковых заготовок, предварительно прошиваемых на прошивном стане. В результате прокатки могут быть получены штучные изделия.
Однако, на получаемых деталях могут возникнуть различные дефекты: в первую очередь, торцовая утяжина и осевая рыхлость, а также поперечные и продольные закаты, спиралевидные гребешки.
Кроме того, недостатком данного способа получения полых ступенчатых деталей является то, что применение оборудования нескольких наименований удорожает и удлиняет технологический процесс, а также повышает стоимость проектирования и изготовления рабочих калибров валков.
При холодной торцовой раскатке [16] деформирование осуществляют вращающимся пуансоном, причем ось его вращения расположена под некоторым углом коси вращения заготовки.
Особенности формоизменения заготовок при раскатке, возможность потери устойчивости заготовки и предельная деформация материала, которая может быть достигнута в условиях локального деформирования, ограничивают технологические возможности холодной торцовой раскатки при изготовлении деталей с фланцами. Недостатком способа также является необходимость использования трубной заготовки для изготовления полых деталей.