Технологические основы получения ультрамелкозернистых металлов
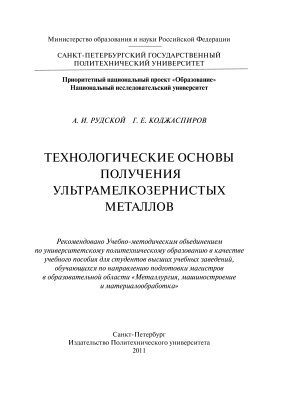
Рудской А.И., Коджаспиров Г.Е.
СПб.: Изд-во Политехн. ун-та, 2011 г.
6. ПЕРСПЕКТИВНЫЕ УЛЬТРАМЕЛКОЗЕРНИСТЫЕ МАТЕРИАЛЫ И ОБЛАСТЬ ИХ ПРИМЕНЕНИЯ
Разработка ультрамелкозернистых металлических материалов открывает перспективы их практического использования в машиностроении, медицине, транспортной, аэрокосмической и других областях промышленности.
УМЗ материалы могут найти применение практически в любом секторе народного хозяйства, где решающую роль играют высокие механические (сверхпрочность, ударная вязкость, усталостная выносливость) и функциональные (магнитные, сверхупругие, эффект памяти формы) свойства. Согласно прогнозам [78, 79] особого внимания заслуживают перспективы применения наноструктурных материалов в технике и медицине, при использовании технологии высокоскоростной штамповки с использованием эффекта сверхпластичности и изготовлении сложных деталей автомобилей и аэрокосмической техники.
- Титановые сплавы в технике и медицине
Титановые сплавы являются одними из наиболее распространенных конструкционных материалов, используемых в аэрокосмической и химической промышленности, специальном машиностроении и медицине, поэтому повышение механических свойств титановых сплавов [80-82]. Большой интерес представляет использование наноструктурных титановых сплавов в медицине и, в частности, травматологии и стоматологии в качестве материалов для имплантатов из-за сочетания высоких физических, химических и механических свойств 182]. Это связано с тем, что, во-первых, титан и его сплавы имеют высокую коррозионную стойкость во многих средах. Во-вторых, титановые сплавы обладают исключительной биосовместимостью с человеческими тканями и не провоцируют аллергических реакций, воспалений, как, например, нержавеющие стали или кобальтохромовые сплавы. В-третьих, титан и титановые сплавы имеют высокую прочность и низкий модуль упругости, которые наиболее предпочтительны для применения в ортопедии и травматологии [82]. Однако разработки современных медицинских имплантатов предъявляют требования не только к дальнейшему увеличению прочности, но и повышению сопротивляемости материала имплантата высоким усталостным нагрузкам.
Традиционными способами упрочнения титановых материалов являются легирование, термическая и термомеханическая обработка 180, 81]. Однако введение дополнительных легирующих элементов в титановый сплав и создание новых высоколегированных композиций ограничивают использование титановых материалов в медицине в связи с вредным воздействием некоторых химических элементов на человеческие ткани. Упрочнение с использованием традиционной термической обработки за счет управления морфологией фазовых составляющих, выделения дисперсных вторых фаз применяется только для ряда титановых сплавов, и во многом возможности этого подхода уже исчерпаны [81]. Деформационные методы обработки материалов, такие как прокатка, протяжка, ковка, волочение и другие, могут существенно повлиять на их структуру и механические свойства, приводя к повышению уровня прочностных характеристик. Однако при этом снижается пластичность материалов, которая является из важнейших характеристик, учитывающихся при разработке новых конструкционных материалов [83].
В данном разделе будут рассмотрены способы улучшения свойств титана и его сплавов на его основе за счет формирования в них ультрамелкозернистой структуры с помощью технологических процессов на основе ИПД: пластической деформацией кручением, равноканальным угловым прессованием, всесторонней многоступенчатой ковкой.
- Технология получения длинномерных прутков нанотитана для медицинских применений
В последние годы титан и его сплавы находят все более широкое применение в медицине: при замене костей и суставов, в качестве зубных имплантатов, при лечении челюстно-лицевой и черепно- лицевой области, в качестве материала приспособлений при сердечнососудистых заболеваниях, наружных протезов, хирургических инструментов [85]. Порядка 1000 тонн изделий различных наименований и назначения из титана и его сплавов имплантируется каждый год по всему миру. Потребности в замене природных элементов живых организмов продолжают расти в связи с повышением уровня медицинского обслуживания и продолжительности жизни людей, а также ускорением техногенных процессов, приводящих к возрастанию транспортных и промышленных аварий. Массовое развитие экстремальных видов спорта также приводит к возрастанию серьезных травм. Легкий и прочный титан считается абсолютно неактивным и устойчивым к коррозии в физиологической среде, а потому имеет высокую биосовместимость с человеческим организмом. Высокая удельная прочность титана и титановых сплавов медицинского назначения превосходит, ранее используемые для этих целей нержавеющие стали. Разнообразие существующих титановых сплавов позволяет специалистам и разработчикам в области медицины выбирать материалы и формы, которые наилучшим образом приспособлены к потребностям конкретной области применения. При этом следует учитывать, что наибольшую биосовместимость с человеческим организмом демонстрирует технически чистый титан, но, к сожалению, его прочностные свойства не достаточно высоки, что сдерживает его более широкое применение при создании надежных имплантатов. Наиболее перспективным решением этой проблемы представляется создание ультрамелкозернистых, а конкретнее, наноструктурных состояний в технически чистых марках титана [85]. Как отмечалось выше, в НС состоянии большинство металлов, в том числе и титан, обладают повышенными, в 1,5 — 2 раза большими исходных механическими свойствами. Это позволяет не только более широко применять технически чистый титан в медицине, но и минимизировать геометрию титановых имплантатов, с целью снижения травмирования костных и мышечных тканей. К тому же в ряде работ показано, что у наноструктурного титана намного быстрее проходит процесс интеграции с костными тканями [86]. В этой связи большой интерес для практики представляет использование нанотитана при производстве медицинских имплантатов. В частности известно, что значительные перемены в стоматологической восстановительной практике оказались возможными благодаря применению титановых имплантатов. Титановый имитатор корня вживляется в челюстную кость, после чего в течение некоторого времени происходит процесс интеграции с костной тканью. Затем на имплантат наращивается верхняя часть зуба, что обеспечивает эффективное замещение. При использовании крупнокристаллического титана, процесс лечения занимает до 3 месяцев. Использование же НС титана сокращает этот срок до 2 недель, что значительно упрощает внедрение такой технологии в стоматологической практике. Наиболее часто используются конструкции зубных имплантатов представленные на рис. 6.1 и состоящие из двух или одной титановых деталей.
Наряду с медицинскими требованиями большая роль отводится механическим свойствам этих изделий, особенно уровням предельной статической и усталостной прочности используемых материалов. Например, повышение σΒ до значений 1250-1300 МПа позволяет минимизировать размеры имплантата и проводить имплантацию передних зубов [87].
Достичь таких значений прочности возможно при использовании комбинированных технологий. Такие технологии, как правило, включают операции ИПД и последующее формоизменение методами ОМД - ковкой, прокаткой, волочением. Одна из таких технологий разработанная в научной школе профессора Валиева Р. 3. совместно с д.т.н. Раабом Г. И. и коллегами из США использует метод РКУП по схеме «Конформ» и последующее волочение. Полученные длинномерные полуфабрикаты из технического УМЗ титана марки Grade 4 в виде прутков или проволоки круглого сечения демонстрируют сверхвысокую прочность, превышающую исходную в два раза при довольно высоких значениях пластичности табл. 6.1.
На предприятии Basic Dental (США) изготовлена серия стоматологических имплантатов из полученных высокопрочных прутков УМЗ Ti (рис. 6.2). Клинические испытания подтвердили заключение об ускоренной интеграции НС Ti имплантатов с костными тканями. Оценивая технические преимущества разработанного технологического процесса получения высокопрочных полуфабрикатов, следует отметить, что в его составе используются высокопроизводительные процессы - РКУП-К и волочение, где скорости обработки составляют от 0,5 до нескольких метров в секунду [881.
- Разработка технологии получения ульрамелкозернистых титановых сплавов для изделий промышленного назначения
Известно, что титан и его сплавы широко используются в различных видах летательных аппаратов, специальных изделиях спортивного назначения и ряде других. В этих конструкциях титановые детали работают, как правило, в диапазоне предельных и часто знакопеременных нагрузок. Коэффициенты запаса таких деталей тоже низкие, что связано с ограничениями по весу таких изделий. Повышение прочностных характеристик (предела прочности и усталости) таких деталей без изменения исходной геометрии позволяет значительно повысить надежность всего изделия.
Одним из объектов применения УМЗ титановых сплавов являлась лопатка газотурбинного двигателя из титанового сплава ВТ-6. Лопатки при работе испытывают сложное нагружение - кручение и изгиб от набегающего потока воздуха и растягивающие нагрузки от центробежных сил. К тому же они испытывают вибрационные нагрузки и подвержены абразивному износу. Повышение прочности и пластичности такой лопатки может существенно повысить надежность изделия в целом.
В работах [89 — 91]показано, что использование РКУП сплава при температурах обработки 600 — 700 °С с общим уровнем накопленной деформации более е = 3 приводит к формированию НС состояния сплава ВТ6. После такой обработки формируется двухфазная УМЗ структура с пределом прочности ~ 1200 МПа и пластичностью δ~ 10%. Более того, использование последующих деформационных воздействий позволяет заметно повысить предел прочности. Например, экструзия УМЗ образцов со степенью деформации более 50 % и температуре 300 °С приводит к дополнительному измельчению структуры и повышению предела прочности вплоть до значений ~ 1500 МПа при пластичности 5 = 6-8%, изотермическая деформация (плющение круглой заготовки) при более высоких температурах 600 - 800 °С к повышению свойств до величины σΒ > 1300 МПа при пластичности 5 > 8 %. Следует обратить внимание на тот факт, что, по сравнению с используемой стандартной упрочняющей обработкой [92], прирост прочности сплава ВТ6 в НС состоянии составляет от 300 до 500 МПа при пластичности, соответствующей уровню серийных изделий. При этом заметно повышаются усталостные характеристики [93]. Это является важной составляющей для перспектив внедрения УМЗ титановых сплавов в серийные изделия летательных аппаратов.
В работе [94] отработаны режимы получения исходной заготовки, которые включали изотермическое РКУП прессование заготовок по режиму в температурном интервале 600-700 °С и уровне накопленной деформации е = 3 и последующую прямую экструзию при 300 °С с е = 0,6. Такая обработка позволила получить размер структурных элементов в заготовке ~ 0,5 мкм (рис. 6.2).
Выбор температурного интервала проведения штамповки основывался на исследовании термостабильности УМЗ состояния, при котором выявили, что до температуры 800 — 820 °С рост зерен незначителен и однороден. При проведении исследований выбрали две температуры - 650 °С, т. е. верхний предел, при котором рост зерен еще не наблюдается, и 810 °С, когда рост зерен незначителен. Экспериментальные работы показали, что снижение температуры штамповки с 950 °С (серийная технология) до 810 °С на серийно используемой оснастке обеспечивает полное заполнение гравюры штампа при использовании максимально возможных (в 1.6 раза больше серийных) силах деформирования (табл. 6.2) и отсутствии заметного роста структурных составляющих (см. рис. 6.2, в). При температуре 650 °С и той же силе штамповки полного заполнения гравюры штампа не происходит (см. табл. 6.2), что связано с более высокими напряжениями течения и пределом возможного повышения силы деформирования из-за ограниченной стойкости к смятию материалов, используемых при изготовлении серийных высокотемпературных изотермических штампов.
Для температур штамповки 650—750 °С рекомендовано использование штамповых материалов более стойких к смятию, например, таких как, В11М7К23 и В4М12К23 [95]. Таким образом, развитие новых ИПД технологий [96] для производства серийных изделий приводит к снижению температур штамповки и возможность использования в этих условиях более дешевых штамповых материалов повышенной теплостойкости.
Проведенные исследования механических свойств заготовки лопатки в НС состоянии и полученной по серийной технологии представлены в табл. 6.3.
Таблица 6.3
Механические свойства заготовки лопатки ГТД в НС состоянии
Технология | Структурное состояние | σΒ, МПа | στ, МПа | δ,% | δρ, % |
Серийная | КЗ | 1030 ±18 | 920 ±21 | >8 | >2 |
Предлагаемая | НС | 1260 ±20 | 1180 ±22 | >8 | >2 |
Анализ полученных данных показывает, что использование вышепредставленной технологической цепочки при получении заготовок лопаток из сплава ВТ6 позволяет увеличить их предел прочности с 1000 МПа (серийная технология) до значений 1240 - 1280 МПА при сохранении пластичности на уровне серийных свойств. Экономические преимущества внедрения такой технологии при получении заготовок лопаток обусловлены следующими аргументами:
- Геометрия лопаток не меняется, что не требует дополнительных расходов на разработку конструкции и проведения полного комплекса стендовых и летных испытаний. Такой подход значительно ускорит распространение разработанной технологии на другие типоразмеры лопаток.
- Снижение температуры штамповки до 650-800 °С позволит использовать теплостойкие штамповые стали, которые дешевле сплавов ЖС6, ЖСбу и технологичнее при лезвийной и абразивной обработке.
- Снижение температуры штамповки также снизит затраты на электроэнергию, что скомпенсирует затраты на получение исходных НС заготовок при использовании высокопроизводительной и схемы РКУП в параллельных каналах, позволяющей получать НС состояния в металлах и сплавах за два цикла обработки при высоких показателях КИМ или высокопроизводительную схему РКУП - К.
- Повышенные прочностные и усталостные характеристики вы- соконагруженных элементов силовых агрегатов позволят без изменения конструкции повысить их эксплуатационную надежность и ресурс.
- Полученные за счет наноструктурирования новые, значительно повышенные механические свойства титановых сплавов могут стать важным фактором при создании высокоэффективных изделий нового поколения.
- Ультрамелкозернистые сплавы с эффектом памяти формы и область их применения
К настоящему времени одним из наиболее используемых материалов, обладающих эффектом памяти формы (ЭПФ), обусловленным термоупругими мартенситными превращениями, является никелид титана.
Термомеханическое соединение (ТМС) трубопроводов и элементов конструкций — одно из перспективных применений сплавов с эффектом памяти формы (ЭПФ) на основе никелида титана (TiNi) [97]. ТМС находят применение в авиакосмической технике, а в перспективе - в коммуникациях ядерных и термоядерных реакторов. Основные требования, предъявляемые к ТМС — надежность и стабильность, в том числе при изменении температуры и механической нагрузки, а также легкоразборность. ТМС осуществляется с помощью термомеханических муфт из сплавов с ЭПФ Ti-Ni-Fe (рис. 6.3). Функциональным критическим свойством, определяющим надежность и стабильность ТМС, является реактивное напряжение, развиваемое в сплаве в условиях восстановления формы при внешнем механическом противодействии [98 - 100]. Естественной границей, определяющей максимальное реактивное напряжение, является обычный («дислокационный») предел текучести сплава [101].
Поскольку измельчение зерна приводит к повышению предела текучести сплава, то следует ожидать и соответствующего повышения реактивного напряжения, что было установлено нами при исследовании бинарных сплавов с ЭПФ Ti-Ni.
В работе [102] решали задачу повышения функциональных свойств термомеханической муфты и ТМС за счет измельчения зерен методами ИПД и оптимизации состава сплавов. Основной целью измельчения структуры сплавов Ti-Ni-Fe используя РКУП, являлось достижение максимально высокого реактивного напряжения, обеспечивающего несущую способность ТМС. Также, должна быть обеспечена низкотемпературная стабильность и легкоразборносгь ТМС.
Исследовали сплавы Ti - 47, 6 ат. % Ni - 2,4 ат. % Fe (сплав 1), Ti - 47 ат. % Ni - 3 ат. % Fe (сплав 2) и Ti — 4 — 6, 6 ат. % Ni - 3,4 ат. % Fe (сплав 3). Наиболее подробно эти исследования представлены в наших публикациях, где показано, что сплав Ti-47 ат. % Ni-З ат. % Fe (сплав 2) наиболее технологичен при переводе его в УМЗ состояние методом РКУП и обладает наиболее рациональным комплексом функциональных свойств.
При этом наиболее рациональная обработка методом РКУП включала изотермическое прессование в оснастке с углом пересечения каналов 110° при температуре 400 - 450 °С по режиму Вс. После 6-8 циклов прессования в заготовках формировалась структура с размером зерен менее 0,5 мкм и повышалась прочность в ~ 1,5 раза.
Например, деформация методом РКУП, обеспечивает более высокое реактивное напряжение, чем стандартно используемые обработки (табл. 6.4).
Термомеханические муфты, их дорнование, сборка и испытания. ТММ были изготовлены лезвийной обработкой из УМЗ заготовок сплава 2, а также из заготовок после закалки из исходного состояния поставки. Детали муфт отожгли для устранения поверхностных концентраторов напряжений и снятия внутренних напряжений, внесенных механической обработкой: при 450 °С, 1 ч (закаленные муфты) и 550 °С, 1 ч (РКУП муфты). Такой отжиг не приводит к изменению размеров зерен, механических и функциональных свойств.
В результате дорнования, наведенная деформация (без учета упругой отдачи) муфты по диаметру составляла 7.5 %. Это близко к предельной величине полностью обратимой деформации этого сплава, что обеспечивает реализацию максимального реактивного напряжения, т. е. характеризующую несущую способность термомеханической муфты. С другой стороны, при такой большой наведенной деформации вероятно возникновение внутренних напряжений, которые наводят обратимый ЭПФ и облегчают разборку ТМС при охлаждении.
Сборка ТМС в эксперименте осуществлялась в следующей последовательности :
- Дорнование и последующее измерение внутреннего диаметра ТММ в жидком азоте.
- Изготовление стального цилиндрического стержня для осуществления свободной посадки его в термомеханическую муфту.
- Предварительная сборка ТМС при температуре жидкого азота.
- Окончательная сборка происходит при нагреве ТМС до комнатной температуры.
Испытания муфт на несущую способность и ТМС на легкоразборность и низкотемпературную стабильность проводили по стандартным методикам.