Сварка в смеси активных газов
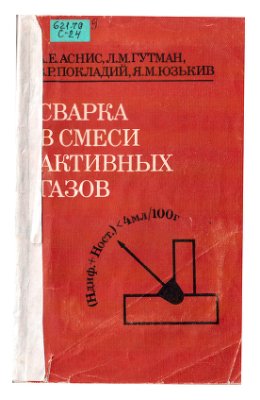
Аснис А.Е., Гутман Л.М. и др.
Наукова думка, 1982 г.
ПРОМЫШЛЕННОЕ ВНЕДРЕНИЕ СВАРКИ В СМЕСИ УГЛЕКИСЛОГО ГАЗА И КИСЛОРОДА
Сварка в смеси СO2 + O2 с обычным и удлиненным вылетом электрода применяется взамен ручной сварки покрытыми электродами и вместо полуавтоматической в углекислом газе проволокой сплошного сечения.
Освоение сварки в смеси СO2 + O2 с удлиненным вылетом в заводских условиях не связано с изменением технологического процесса изготовления металлоконструкций, машин, станков, вагонов и других изделий. Это позволяет осуществить переход от применявшегося ранее способа сварки к новому в" кратчайшие сроки. Если при замене ручной сварки механизированной требуется освоение нового сварочного оборудования и подготовка кадров, то замена полуавтоматической сварки в углекислом газе сваркой в смеси СO2 + O2 сводится практически к замене вида защиты дуги и минимальной переделке держателя. На заводах такая замена осуществляется полностью в течение 3—5 дней.
С применением сварки в смеси СO2 + O2 требования к подготовке поверхности металла и к сборке конструкций сохраняются прежними. Однако сварка в смеси менее чувствительна к ржавому металлу.
Основными преимуществами сварки в смеси СO2 + O2 с увеличенным вылетом по сравнению со сваркой в углекислом газе с обычным вылетом являются повышение производительности процесса (в среднем на 25—30%), сокращение затрат на зачистку швов от брызг, улучшение внешнего вида и качества металлоконструкций.
2. Неметаллические включения в швах.
В результате взаимодействия жидкого металла, с защитным газом и продуктами его диссоциации в зоне плавления происходит окисление металла. Особенно интенсивно этот процесс протекает при сварке в окислительных защитных газах и смесях: СO2, Аr + СO2, Аr + O2, Аr + СO2+O2, СO2 + O2. Вместе с окислением сплавы на основе железа обладают способностью, хотя и ограниченной, растворять кислород. Растворимость его возрастает с повышением температуры.
При снижении температуры в хвостовой части ванны происходит раскисление металлов. Этот процесс представляет собой растворение в жидком металле элементов-раскислителей, содержащихся в проволоке алюминия, кремния, марганца. Они соединяются с кислородом и образуют нерастворимые соединения — продукты реакций раскисления. Часть продуктов раскисления удаляется с дымом и брызгами, другая — формирует шлаковую корку на поверхности валика, при этом содержание кислорода в металле уменьшается. Раскисление никогда не проходит до конца, так как часть продуктов раскисления не успевает всплыть на поверхность и остается в закристаллизовавшемся металле в виде окисных включений.
Кроме окисных включений в шве всегда имеются и сульфидные включения, количество которых зависит от содержания серы. При сварке проволоками, содержащими сильные карбидо- и нитридообразующие элементы, или при сварке сталей с нитридной или карбонитридной фазой в металле шва можно обнаружить нитриды.
Неметаллические включения заметно влияют на структуру и свойства металла шва. Степень влияния зависит от их формы, размеров и расположения. Наиболее неблагоприятное воздействие оказывают неметаллические включения, располагающиеся по границам зерен в виде пленок или цепочек, а также включения остроугольной формы, являющиеся концентраторами напряжений и могущие служить очагами зарождения микротрещин.
Процессы образования неметаллических включений, их подробное описание и характеристики, а также влияние на свойства металла шва приведены в ряде работ [59, 60, 82, 140].
Изучение неметаллических включений при сварке сталей в смеси СO2 + O2 проводили металлографическим методом с использованием оптического и электронного микроскопов, а также методом электролитического растворения образцов, вырезанных из швов, и определения окислов, содержащихся в металле шва. Наиболее универсальным методом исследования неметаллических включений является металлографический, позволяющий определить вид, размеры, форму и количество включений, а также характер их расположения. Для проведения исследований из наплавок и стыковых швов вырезали темплеты перпендикулярно к оси шва и изготавливали микрошлифы. Нетравленые шлифы исследовали под микроскопом при различных увеличениях и определяли количество, форму и расположение неметаллических включений.
Установлено, что в шве, сваренном в смеси СO2 + O2 преобладают очень мелкие включения, главным образом в виде глобулей, равномерно расположенные по всему шлифу. Включения остроугольной формы или продолговатые встречаются очень редко. Крупные включения единичны, и их размер редко превышает 2—3 мкм.
Выявленные металлографическим методом неметаллические включения в швах по минералогическому составу можно разделить на несколько главных типов: железомарганцевые силикаты — серые включения с вкраплениями шариков более темного цвета; силикаты железа (фаялит) — темно-серые резко очерченные глобули с кольцевым отсветом; кварцевые стекла — характерные глобули различных размеров черного цвета с блестящей точкой в центре и кольцевым отсветом. Реже в металле шва встречаются смешанные железомарганцевые окислы, окись алюминия, закись железа. В швах на стали 16Г2АФ с помощью электронного микроскопа обнаружены нитриды ванадия, имеющие кубическую форму. Они очень дисперсны, расположены чаще всего внутри зерен, что благоприятно сказывается на свойствах металла шва.
Влияние содержания кислорода и длины вылета на количество неметаллических включений в швах изучали на установке «Quantimet-720». Для проведения исследований в канавку, простроганную в пластине из стали Ст. Зсп, были наплавлены валики. Сварку выполняли проволокой Св-08Г2О диаметром 2,0 мм в три прохода на токе 400 А. Перед каждые проходом пластина остывала до комнатной температуры. Из наплавленного валика вырезали темплеты для металлографических исследований, образцы для определения химического состава металла и неметаллических включений.
Исследования показали, что минимальное количество окисных включений наблюдается при сварке в углекислом газе. С удлинением вылета электрода несколько увеличивается количество включений. По-видимому, это можно объяснить снижением температуры капель и металла сварочной ванны. При этом уменьшается жидкотекучесть металла, что затрудняет всплывание неметаллических частиц.
Несмотря на большую окислительную способность атмосферы, при сварке в смеси СO2 + O2 с удлиненным вылетом количество неметаллических включений не увеличивается по сравнению со сваркой в углекислом газе и таким же вылетом. Добавка кислорода повышает температуру сварочной ванны, длительность пребывания ее в жидком состоянии, ее жидкотекучесть, что облегчает всплывание окисных включений.
Увеличение количества окисных включений при сварке и смеси СO2 + O2 по сравнению со сваркой в углекислом ι азе с обычным вылетом происходит за счет мелких включений размером до 1,0—1,5 мкм. Необходимо отметить, что при этом снижается количество более крупных включений (см. табл. 10). Это благоприятно сказывается на сгойкости шва против хрупкого разрушения.
Состав окисных включений определяли методом электролитического растворения образцов, вырезанных из швов. Методика обеспечивала суммарное определение окислов, входящих в силикаты и шпинели, а также содержание свободной окиси алюминия. Установлено, что окисные включения в металле шва состоят в основном из окислов марганца, кремния, а также окислов алюминия и в незначительном количестве — из окислов железа. Предполагают, что окислы алюминия, содержащиеся в электродных проволоках, не успевают в процессе сварки выделиться в шлак и переходят в металл шва [61]. Добавка кислорода и удлинение вылета электрода не влияют на состав окисных включений. При сварке в смеси СO2 + O2 несколько увеличивается процентное содержание окислов железа и общее количество включений.
При сварке в смеси СO2 + O2 количество шлака на поверхности швов несколько увеличивается. При многослойной сварке в смеси СO2 + O2 шлаковую корку следуем удалять после наложения пяти-шести слоев. Количество шлака составляет примерно 1—1,5% массы наплавленного металла. Химический состав шлака, %: SiO2 29 — 32; Fe2O8 23 — 25; MnO 40 — 42; Fe2O3 3—4.
Как указано выше, кроме окисных включений в металле шва встречаются и сульфидные. Если в литом металле шва окислы имеют преимущественно форму глобулей или неправильных многогранников, то сульфидные включения могут выделяться в виде пленок по границам зерен. Сульфид железа отличается низкой температурой плавления и, как известно, приводит к образованию кристаллизационных трещин в швах. В металле шва всегда содержится определенное количество серы, поэтому форма и расположение сульфидных включений определяют влияние их на свойства металла шва.
В зависимости от степени раскисленности сульфидные включения могут быть трех типов. При низкой концентрации углерода и малом содержании других элементов-раскислителей в швах преобладают оксисульфидные глобулярные включения. При высоком содержании углерода в присутствии алюминия или других сильных раскислителей образуются пленки или цепочки сульфидов по границам зерен. Добавка алюминия, циркония, титана в количестве, несколько большем, чем необходимо для полного раскисления, приводит к превращению этих включений в сульфиды третьего типа, имеющие неправильную форму и менее вредные, чем сульфиды второго типа.