Структура и свойства тугоплавких металлов
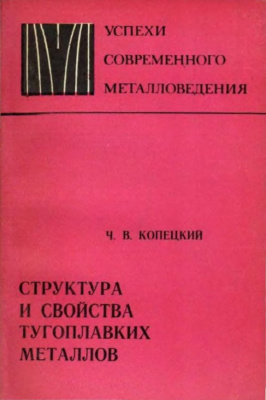
Копецкий Ч.В.
Металлургия, 1974 г.
Сплавы молибдена
Как и в случае вольфрама, разработка жаропрочных сплавов молибдена преследует в основном две цели: с одной стороны, повышение характеристик прочности и сопротивления ползучести, а с другой — повышение низкотемпературной и технологической пластичности. Это достигается .в большинстве случаев комбинацией механизмов твердорастворного я дисперсного упрочнений. Были исследованы также сплавы молибдена, в которых используется один из этих механизмов упрочнения.
Интенсивные исследования R области разработки сплавов молибдена были начаты в первой половине 50-х годов. За это время изучено значительное количество двойных и тройных композиции сплавов, полученных методами вакуумно-дуговой и электроннолучевой плавок, а также методом порошковой металлургии. Как показали результаты многочисленных исследований, легирование молибдена добавками различных элементов в значительных количествах ухудшает его технологическую и низкотемпературную пластичность, что ограничивает степень легирования. Исключение составляет рении, легирование .которым вплоть до 50%(ат.) резко повышает характеристики пластичности молибдена. Сравнительно мало снижают технологическую пластичность молибдена и добавки вольфрама, что позволяет получать изделия из сплавов молибдена, высоколегированных вольфрамом (около 30%) [107, с. 149—175]. Оптимальные результаты при разработке сплавов молибдена были получены при легировании его небольшими добавками углерода совместно с одним пли несколькими элементами IVA группы. В этом случае повышение прочности достигается в результате совместного действия механизмов дисперсного и твердорастворного упрочнения. Этот принцип легирования положен в основу при разработке .важнейших промышленных и опытных сплавов молибдена, выпускаемых в нашей стране и за рубежом. Химический состав и некоторые характеристики механических свойств этих сплавов .приведены в. табл. 8.
Обращает на себя внимание большой разброс значений прочности в интервале температур 800—1400°С, что может быть связано с различным структурным состоянием образцов вследствие разной обработки, которой образцы подвергли до испытания, неодинаковыми условиями испытания и, наконец, разницей в .содержании углерода. Так, в стандартах США содержание углерода в сплаве TZM даже не нормируется [70]; это приводит к сильному разбросу свойств.
Нa рис. 76 приведена прочность некоторых молибденовых сплавов при испытании на растяжение в условиях разных температур. Как правило, атмосфера, при которой проводили испытания, — вакуум. Из рисунка видно, что характер изменения предела прочности сплавов .молибдена с ростом температуры в целом сходен с таковы для чистого молибдена.
Действительно, здесь также для большинства сплавов наблюдаются три интервала в ходе изменения предела прочности с температурой, как это отмечено для молибдена А. П. Гуляевым и Η. Н. Моргуновой [102]. Первый интервал — примерно до 600°С—характеризуется резким падением прочности, сопровождающимся столь же резким ростам пластичности. Второй интервал—средних температур от 600 до 1400—1600°С — характерен слабой зависимостью прочности и пластичности от температуры. В этом интервале наиболее сильно сказывается влияние состава сплава и его структурного состояния на механические свойства. И, наконец, третий интервал — выше 1600—1800°С, когда прочность всех малолегированных сплавов молибдена почти не различается, а зависимость прочности от температуры для некоторых сплавов более резкая, чем во втором интервале. Для этого интервала температур наибольшую прочность показывают сплавы, легированные значительным количеством элементов, вызывающим повышение температуры плавления сплавов.
Поведение сплавов, упрочненных добавками нитрида циркония или добавками рения, отличается сохранением высоких значений прочности до более высоких температур.
Исследованные и производимые в настоящее время жаропрочные сплавы молибдена могут быть разделены на несколько групп.
Малоуглеродистые низколегированные сплавы молибдена
В эту группу могут быть включены сплавы Mo — 0,5 Ti, TZM, ЦМ-2А, BM-1 и ВМ-2 с содержанием углерода в них 0,004—0,05% (по массе). При этом у сплавов ЦМ-2А, BM-1 и ВМ-2 нижний предел содержания углерода не лимитируется, а в технических условиях на сплавы TZM и Mo —0,5Ti номинальное содержание углерода не определено вообще. Содержание легирующих добавок (элементов IV группы—титана и циркония) колеблется в пределах 0,07—0,5 и 0,007—0,4% (по массе) соответственно (сплав Mo — 0,5 Ti легирован только титаном). Высокая прочность и жаропрочность этих сплавов определяются механизмом твердорастворного упрочнения вследствие образования твердых растворов титана и циркония в .молибдене, а также дисперсного упрочнения, связанного с выпадением дисперсных частиц карбида титана и циркония. По мнению А. П. Гуляева и Η. Н. Моргуновой, в минимально легированном сплаве ЦМ-2А повышенная прочность определяется главным образом твердорастворным механизмом упрочнения [102]. Вилкокс и Гилберт показали [136], что упрочнение молибденовых сплавав типа TZM в результате выделения карбидных частиц находится ® хорошем· соответствии с механизмом упрочнения Орована, описывающим упрочнение как результат влияния тонкодисперсных недеформируемых выделений в структуре.
Природа структурных составляющих в .молибденовых сплавах этой группы и их устойчивость рассмотрены во многих работах. Электролитическое выделение карбидов из сплавов на молибденовой основе, легированных 0,2% Zr при содержании 0,025—0,03% (по массе) С, показало, что в результате отжига при 2000аС, 3 ч основу образцов осадка составляет карбид Mo2C. Отжиг этих же образцов при 1600°С. в течение 1 ч приводит к тому, что остаток почти полностью состоит из карбида ZrC с небольшой примесью Mo2C [ПО]. Существенное изменение количества выделившихся карбидных фаз, их распределения, формы и размеров в зависимости от термической обработки наблюдается в сплаве TZM [9G, с. 248—274].
На рис. 77 представлены температурные области стабильности карбидов в сплаве TZC, содержащем 1,25% Ti; 0,15% Zr и 0,15% С. Видно, что карбид титана TiC устойчив в интервале температур до 1650°С, выше этой температуры находится интервал устойчивости карбида ZrC и, наконец, выше 1800—1900°С до температуры эвтектики устойчив карбид Mo2C.
В сплавах .молибдена с углеродом, содержащих от 0,014 до 0,07% С, наблюдаются включения Mo2C эвтектического происхождения и вторичные карбиды, образовавшиеся при распаде твердого раствора. При наличии эвтектики, как показано в работе [III], распад носит гетерогенный характер с преимущественным образованием выделений на дислокациях и -границах зерен. Вилкокс и Гилберт [136] наблюдали, что частицы (по-видимому, Mo2C) выделяются в местах скоплений дислокаций —размеры выделений -порядка 50 нм (500 А), расстояние между выделившимися частицами ~ 300 нм (3000 А).
Η. H. Моргунова нашла, что часть карбидов молибдена, образовавшихся за счет избыточного против предела растворимости количества углерода при температуре обработки, располагается в виде цепочки на существующих границах раздела фаз и зерен. Карбиды молибдена. выпадающие из жидкой фазы по эвтектической реакции при содержании углерода в сплаве более 0,02%, также располагаются .почти сплошной цепочкой крупных включений по границам зерен, резко снижая пластичность сплавов [112].
Карбиды титана и циркония выпадают в виде значительно более мелких включений и находятся главным образом, в объеме зерна. Резкое изменение растворимости углерода с температурой к наличие температурных интервалов устойчивости различных карбидов определяют возможность использования термической обработки сплавов молибдена с целью изменения их структуры и свойств. При этом в первую очередь используется возможность дисперсионного твердения в низколегированных молибденовых сплавах.