Структура и свойства цветных сплавов, затвердевших под давлением
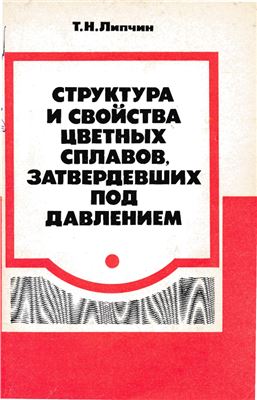
Липчин Т.Н.
Металлургия, 1994 г.
Влияние давления, действующего в процессе кристаллизации, на макроструктуру отливок зависит от целого ряда факторов: величины и вида давления (поршневого или пуансонного), температуры формы и расплава, продолжительности выдержки до приложения давления и под давлением, интервала кристаллизации сплава, габаритов и конфигурации отливок. Практически во всех имеющихся в настоящее время исследованиях по этому вопросу отмечается положительное воздействие давления на изменение макроструктуры сплавов.
Эти изменения заключаются в устранении газоусадочных дефектов отливки (раковин, пор), уменьшении или полном исчезновении зоны столбчатых кристаллов и образовании более мелких равновесных кристаллов, устранении зональной ликвации. Эти факторы способствуют повышению целого комплекса свойств сплавов.
Чистые металлы затвердевают с образованием значительной зоны столбчатых кристаллов. Исследования показали, что с ростом давления при кристаллизации ширина зоны столбчатых кристаллов вначале возрастает, а при дальнейшем повышении давления— уменьшается. Первоначальное увеличение зоны столбчатых кристаллов при переходе от литья в кокиль к затвердеванию под давлением 100 МПа связано с ростом скорости охлаждения в результате воздействия давления. При последующем возрастании давления скорость охлаждения практически не меняется, и повышение давления приводит к расширению центральной зоны равноосных кристаллов.
Характер макроструктуры резко меняется при переходе от чистого металла к сплаву. Так, уже небольшая добавка второго компонента к алюминию или магнию (например, одного процента магния или меди к алюминию или одного процента цинка к магнию) приводит к получению по всему сечению отливки мелких равновесных кристаллов (зерен), сохраняющихся при увеличении концентрации легирующего компонента. Такое изменение макроструктуры с учетом неравновесной диаграммы состояния соответствует известному правилу А.А.Бочвара, связывающего тип кристаллов с шириной интервала кристаллизации. Давление при кристаллизации мало влияет на макроструктуру данного типа отливок, способствуя лишь некоторому измельчению кристаллов. Такое изменение размеров кристаллов отмечается практически во всех исследованиях, посвященных изучению структуры затвердевших под давлением сплавов. Степень уменьшения размера зерна зависит от целого ряда факторов — технологических режимов литья (температуры сплава и формы, времени выдержки сплава без давления и под давлением, скорости прессования, величины давления), схемы прессования (поршневого и пуансонного), конструкции и габаритов отливки, типа сплава.
На рис. 12 представлены результаты исследования величины дендритных кристаллов и дендритных ячеек в зависимости от давления при кристаллизации двойных сплавов систем Al—Mg, Al—Сu, А1—Zn, Mg—Аl и промышленных сплавов. Данные рис. 12 свидетельствуют о том, что для большинства сплавов измельчение составляет 30—50 % (в отдельных случаях— 100%). Такое изменение размера кристаллов положительно сказывается на прочностных и пластических свойствах сплава. Эффективность действия давления проявляется до давления 200 МПа, дальнейшее повышение давления вплоть до значений 2500 МПа практически не меняет величину дендритных кристаллов и дендритных ячеек.
В двойных сплавах с ростом степени легированности твердого раствора размер зерна уменьшается до тех пор, пока по границам ячеек не образуется значительное количество эвтектических выделений, дальнейшее легирование изменяет размер зерна незначительно. Это, как отмечалось выше, связано со значительным увеличением количества твердой фазы, кристаллизующейся в этих сплавах при более низких температурах по сравнению с температурами кристаллизации основного количества твердой фазы малолегированных сплавов, и близкими параметрами \ кристаллизации в средне- и высоколегированных сплавах.
Одна из причин измельчения кристаллов в сплаве под действием давления при кристаллизации состоит в ускорении охлаждения в результате устранения газовоздушного зазора между стенкой формы и отливки в процессе усадки и охлаждающего действия прессующего пуансона. Другая и, пожалуй, более важная причина измельчения зерен рассмотрена А.Л.Аптекарем и Д.С.Каменецкой в работе [105]. Известно, что при определенной величине переохлаждения достаточно снижения температуры на несколько градусов, чтобы число зародышей возросло от единиц до весьма большего значения. Это справедливо как для гомогенности, так и для гетерогенного зарождения [106]. Такое переохлаждение может быть достигнуто в результате высокой скорости охлаждения или же наложением давления на кристаллизующийся металл [105], так как температура плавления абсолютного большинства сплавов при этом повышается и сплав оказывается переохлажденным. Авторы работы [105] отмечают принципиальную разницу между переохлаждением из-за высокой скорости охлаждения и действия давления. В первом случае значительное переохлаждение достигается в периферийных слоях отливки, образующееся при этом большое число кристаллов затрудняет переохлаждение внутренних слоев. При переохлаждении расплава в результате давления переохлажденным является весь объем металла, поэтому действие давления более эффективно.