Структура и свойства полуфабрикатов из алюминиевых сплавов
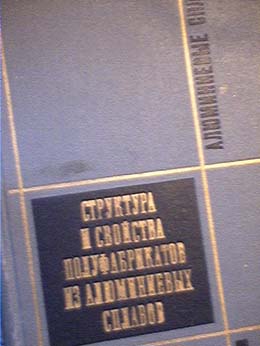
Арчакова 3.Н., Балахонцев Г.А., Басова И.Г.
Металлургия, 1984 г.
Глава XXII
СТРУКТУРА И СВОЙСТВА ПРОВОЛОКИ ДЛЯ КРЕПЕЖНЫХ ДЕТАЛЕЙ
Основным видом соединений узлов и агрегатов различных конструкций из алюминиевых сплавов являются заклепочные и болтовые соединения.
Для повышения надежности, ресурса и герметичности соединений потребовалось создание и применение таких новых видов крепежа, как стержневые заклепки, заклепки с компенсатором, заклепки с сердечником, болт-заклепки и др. Возникшие новые требования к свойствам и качеству проволоки для крепежных деталей удовлетворены путем соответствующего подбора марки сплава, корректировки технологического процесса производства проволоки и термической обработки крепежных деталей.
Наибольший объем из применяемого алюминиевого крепежа приходится на долю различных видов заклепок. В планере самолета соединения с заклепками из алюминиевых сплавов достигают — 70—80 % от общего количества крепежных точек. Например, в самолете ИЛ-86 58,8 % составляют соединения с обычными заклепками, 30,8%—с заклепками с компенсатором, 8,4% — с болт-заклепками, 1,5%—с заклепками одностороннего подхода и 0,5 %—со стержневыми заклепками [1].
Основными факторами, определяющими технологию клепки, являются свойства материала заклепок, от которых, в конечном счете, зависит способ постановки заклепок в конструкцию и конструктивная прочность заклепочных соединений. Известно, что при постановке заклепок в конструкцию они подвергаются большим степеням холодной деформации (до ~70 %). Это обстоятельство необходимо учитывать при выборе сплава.
Сплавы для заклепок должны обладать высокой пластичностью в состоянии постановки их в конструкцию. Это обусловливается пониженным содержанием легирующих элементов и примесей, высокой чистотой металла по неметаллическим и газовым включениям, мягкими режимами старения (Τ, ТЗ).
1. МЕХАНИЧЕСКИЕ СВОЙСТВА
Учитывая условия работы заклепок в шве, считают, что основной определяющей характеристикой для проволоки и заклепок является сопротивление срезу. Гарантируемые значения сопротивления срезу проволоки и заклепок, а также рекомендуемые состояния постановки заклепок в конструкцию приведены в табл. XXII.1.
Наибольшее количество сплавов для крепежных деталей относится к системе А1—Си—Mg. В зависимости от химического состава сплавов этой системы изменяются прочностные и пластические свойства заклепок, а это в свою очередь определяет состояние постановки их в конструкцию. Так, сплав Д18, содержащий пониженные количества легирующих элементов (2,5 % Си и 0,35 % Mg), обладает пониженными значениями сопротивления срезу (190 МПа) и высокой пластичностью. Заклепки из этого сплава ставят в конструкцию в закаленном и естественно состаренном состоянии без ограничения времени с момента закалки.
Сплав В65 содержит значительно большее количество меди (4,3 %) и меньшие количества примесей железа и кремния и поэтому сочетает высокие показатели сопротивления срезу с хорошей пластичностью в состоянии полной термической обработки. Заклепки из него также ставят в конструкцию после закалки и старения без ограничения времени.
Сочетание высокой прочности с хорошей пластичностью в состоянии полной термической обработки способствует широкому применению заклепок из этого сплава. В настоящее время сплав В65 является основным заклепочным алюминиевым сплавом как в самолетостроении, так и в других отраслях промышленности, где применяются конструкции из алюминиевых сплавов.
В сплавах Д1П и Д16П для повышения пластичности сужены пределы содержания легирующих элементов и понижены допустимые количества примесей по сравнению со сплавами Д1 и Д16. Постановку заклепок из этих сплавов в конструкцию производят только в свежезакаленном состоянии.
В закаленном и состаренном состоянии заклепки из этих сплавов обладают высокими прочностными свойствами и пониженной пластичностью при осадке и не допускают больших деформаций, имеющих место при расклепывании заклепок. С учетом длительήости инкубационного периода при старении заклепки из сплава Д1П можно клепать в течение 2 ч после закалки, а из сплава Д16П — в течение 20—30 мин.
Сплав Д19П применяют сравнительно недавно и только в изделиях, работающих при повышенных температурах. Благодаря повышенному содержанию магния и более низкому содержанию меди по сравнению со сплавом Д16П инкубационный период у сплава Д19П длится значительно больше, чем у Д16П. Поэтому заклепки
из него могут расклепываться в течение 2—6 ч после закалки (в зависимости от диаметра).
Из алюминиевых сплавов для крепежных деталей сплав В94 обладает самыми высокими значениями сопротивления срезу в состоянии Т1, которое ранее рекомендовали для заклепок [2]. Однако этот сплав не нашел широкого применения в промышленности ввиду повышенной чувствительности к ударным нагрузкам.
В последнее время для крепежных деталей стали использовать высокопрочный сплав В95П. Однако в состоянии Т1 этот сплав из-за пониженной пластичности и повышенной чувствительности к ударным нагрузкам не применяют в качестве заклепок. Для крепежных деталей, обладающих высокой технологической пластичностью в закаленном и состаренном состоянии, а также высокой коррозионной стойкостью, сплав В95П рекомендуется только в состоянии ТЗ.
Типичные значения механических свойств проволоки из алюминиевых сплавов приведены в табл. XXI 1.2.
Сопротивление срезу проволоки, изготовленной из всех алюминиевых сплавов, с повышением температуры значительно понижается (рис. ΧΧΙΙ.1). Наибольшую скорость разупрочнения с повышением температуры имеет сплав В94Т1. Характер изменения прочности сплавов Д18Т и В65Т приблизительно одинаков. Кривая изменения сопротивления срезу сплава Д19ПТ и АМг5П более пологая при температурах до 200 °С, что указывает на большую стабильность их прочностных свойств при этих температурах. Сплав В95ПТЗ сохраняет достаточно высокую прочность до 200 °С.
Важной характеристикой проволоки для крепежных деталей является технологическая пластичность при осадке (расклепываемость). При испытании на расклепываемость образцы, имеющие определенную величину выступающей части, осаживают на прессе до высоты, равной 0,5 диаметра проволоки.
ТаблицаXXII.2. Типичные механические свойства проволоки из алюминиевых сплавов
Марка и состояние | Р. г/см3 | Е*10-3, МПа | G*10-3, МПа | μ | σв МПа | σ0,2 МПа | δ% | φ% | τср МПа | нв, МПа |
АД1Н | 2,71 | 70 | 27,0 | 0,31 | 15 | 10 | 6 | 60 | 70 | 320 |
АМцН | 2,73 | 71 | 27,0 | 0,31 | 22 | 18 | 5 | 50 | ПО | 550 |
АМг2М | 2,68 | 70 | 26,5 | 0,32 | 19 | 9 | 23 | 50 | 130 | 450 |
АМг5ПМ | 2,65 | 70 | 26,5 | 0,30 | 270 | 150 | 23 | — | 190 | 700 |
Д18Т | 2,76 | 71 | 27,0 | 0,31 | 300 | 170 | 24 | 50 | 210 | 700 |
Д1ПТ | 2,80 | 71 | 26,5 | 0,31 | 410 | 250 | 20 | 40 | 260 | 1100 |
B65T | 2,80 | 71 | 26,5 | 0,31 | 400 | 250 | 20 | 50 | 260 | 900 |
Д16ПТ | 2,78 | 71 | 27,0 | 0.31 | 450 | 290 | 18 | 35 | 290 | 1200 |
Д19ПТ | 2,76 | 70 | 26,5 | 0,31 | 460 | 280 | 20 | 40 | 290 | 1200 |
В94Т1 | 2,85 | 71 | 26,5 | 0,31 | 520 | 440 | 15 | 40 | 320 | 1500 |
В95ПТ1 | 2,85 | 72 | 27,5 | 0,31 | 580 | 510 | 8 | — | 340 | 1500 |
В95ПТЗ | 2,85 | 72 | 27,5 | 0,31 | 500 | 360 | 10 | 45 | 310 | — |
Для каждого сплава установлена контрольная величина выступающей части проволоки (выраженная через диаметры проволоки), при которой в процессе осадки не должны появляться трещины на образцах.
Проволока поставляется в нагартованном состоянии, пригодном для высадки головки крепежных деталей.