Структура и свойства никельмолибденовых коррозионностойких сплавов (с атласом микроструктур)
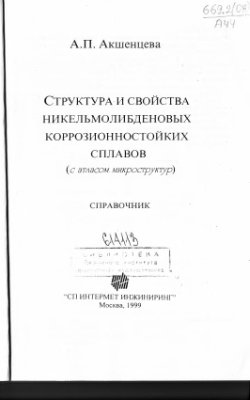
Ашкенцева А.П.
М.: Интермет Инжиниринг, 1999 г.
ДВУХСЛОЙНЫЙ МЕТАЛЛ 20К + 0Х15Н65М16В (ЭП 567)
В химическом машиностроении широкое применение находят сплавы на никелевой основе. Сплав 0Х15Н65М16В (ЭП 567) вошел в ГОСТ 5632-72 и имеет новое обозначение ХН65МВ. Из данного сплава изготовлена серия аппаратов (ректификационная колонна, тарелки ректификационной колонны, пленочный испаритель, реактор). Однако высокая стоимость сплава, трудности производства крупногабаритных листов, а также экономическая нецелесообразность применения листов толщиной более 5-6 мм сдерживают внедрение сплава в промышленность.
В ЦНИИЧМ была разработана технология пакетной прокатки двухслойных листов 20К + ЭП 567 и опробована в условиях Ашинского металлургического завода. Перед сборкой пакетов все заготовки были подвергнуты дробеструйной обработке, после чего на пластины из сплава ХН65МВ металлизационным способом был нанесен с одной стороны соединительный слой никеля толщиной 80 мкм и с другой - разделительный слой алюминия.
Нагрев пакетов проводили в кольцевой нагревательной печи стана. Прокатку осуществляли с одного нагрева. Температура пакетов на выдаче из печи по замеру оптическим пирометром составляла 1150 - 1160 °С, перед клетью 1100 - 1120 °С, конца прокатки 920 - 960 X. Полученные двухслойные листы термической обработке не подвергались. Полученная опытно-промышленная партия двухслойного металла была использована в НИИХИММАШе для исследования свариваемости, обрабатываемости давлением, термической обработки и коррозионной стойкости Г
Структура двухслойного металла
В горячекатаном состоянии плакирующий слой из сплава ХН65МВ (ЭП 567) имел структуру, состоящую и5 мелких зерен У-твердого раствора (№ 8 - 7) и карбидов, расположенных по границам зерен. Химический состав сплава ХН65МВ (ЭП 567) следующий, %: 0,02 С; 0,13 Si; 0,19 Fe; 15,47 Сг; 15,94 Мо; 4,14 W. Вблизи никелевой прослойки имелся сильно травящийся диффузионный слой толщиной 0,05 мм, содержащий большое количество крупных первичных карбидов. Сталь 20К около никелевой прослойки имела ферритноперлитную структуру с мелким зерном (№ 8 - 9) на глубину 0,32 мм, далее наблюдалось укрупненное зерно с видманштеттовой структурой. Толщина никелевой прослойки составляла 9-10 мкм.
Закалка образцов двухслойного металла 20К + ЭП 567 от 1050 °С, выдержка 60 мин, охлаждение на воздухе не вызвала роста зерна в плакирующем слое, но способствовала равномерному выделению дисперсных карбидов на границах зерен в виде изолированной цепочки. После закалки в воде от 1050 °С углеродистая сталь 20К приобретает мартенситную структуру крупноигольчатого строения. При этом происходит повышение твердости с 136 до 346 ЯВ, поэтому закалка в воде от 1050 °С для углеродистой стали недопустима. Измерение твердости образцов после нагрева в интервале 600 - 1150 °С, выдержка 1 ч, охлаждение на воздухе показало, что твердость плакирующего слоя из сплава ХН65МВ не изменяется и равна 238 НВ. Более длительные выдержки в течение 5 ч в указанном интервале температур также не вызывают повышения твердости плакирующего слоя из сплава ХН65МВ, что подтверждает отсутствие выделений упрочняющих фаз в структуре сплава. Интерметал- лидные фазы Ni4Mo и Ni3Mo в плакирующем слое из сплава ХН65МВ после выдержки 5 ч при 600 - 850 °С не выделяются, поэтому и охрупчивания сплава при нагреве не происходит, твердость равна 235 - 241 НВ.
ТЕХНОЛОГИЯ СВАРКИ ДВУХСЛОЙНОГО МЕТАЛЛА
К сварке двухслойного металла 20К + ЭП 567 допускаются дипломированные сварщики, имеющие опыт работы со сплавом ХН65МВ (ЭП 567), по сварке в среде защитных газов. Листы двухслойного металла разрезают на гильотинных ножницах или на металлорежущих станках, причем резка должна производиться при расположении листа плакирующим слоем вверх. После резки на гильотинных ножницах или плазменной дугой кромки заготовок следует обязательно обработать механическим способом на глубину 2-3 мм. Газовую и электродуговую резку применять не разрешается. Подготовка к сварке заключается в следующем. Кромки под сварку следует разделывать только механическим способом (строганием, фрезерованием, точением). Форма разделки кромок показана на рис. 47.
Металл сварного шва является высокочувствительным к воздействию воздушной атмосферы, оксидов, масел и прочих загрязнений, которые могут приводить к образованию пор, горячих трещин, снижению пластичности и коррозионной стойкости. Это относится также к околошовной зоне и корню шва. Поэтому сварка двухслойного металла 2К + ЭП 567 требует примерно тех же мер предосторожности, которые применяются при сварке титана, и строгого соблюдения режимов и технологии. Кромки свариваемого металла и прилегающие к ним поверхности металла на ширине 20 - 25 мм, а также присадочную проволоку необходимо тщательно очистить от следов смазки, загрязнений и т.п., а затем обезжирить растворителями (ацетоном или четыреххлористым углеродом). Применение надежных способов зачистки перед обезжириванием обязательно; предпочтительные способы - шабровка и обработка абразивным кругом. Зачистка металлическими щетками не может быть рекомендована, так как она не обеспечивает удаления прочной сульфидной пленки и других пленок.
Необходимо обеспечить хорошую защиту сварочной ванны и обратной стороны шва.
Сборку под сварку следует проводить на прихватках - со стороны плакирующего слоя в среде аргона с присадочной проволокой 311 567, защищая аргоном обратную сторону шва; со стороны углеродистого слоя - электродами ЦТ-28 на сварочной проволоке Х15Н50М6 и электродами УОНИ-13/45.
Сварку необходимо осуществлять с использованием короткой дуги. При сварке плакирующего слоя колебательные движения горелки не допускаются. Каждый последующий шов необходимо накладывать после полного охлаждения предыдущего и зачистки его от шлака и обезжиривания. Сварку следует проводить с применением 1аходных и выходных планок [45 - 47].
Сварные соединения необходимо контролировать: внешним осмотром, рентгенопросвечиванием, испытанием на плотность и прочность, механическим и коррозионным испытанием образцов- свидетелей; металлографическим исследованием шлифов, вырезанных из образцов-свидетелей после коррозионных испытаний. Механические испытания образцов-свидетелей необходимо проводить при 20 °С в соответствии с ГОСТ 6996-54.
Результаты механических испытаний сварных образцов считаются удовлетворительными, если временное сопротивление при растяжении не ниже 380 МПа, угол изгиба плакирующим слоем внутрь не ниже 100°, ан > 0,58 МДж/м2.
В ходе работ по исследованию свариваемости и разработке технологии сварки двухслойного металла были проанализированы и экспериментально проверены существующие у нас в стране и за рубежом способы сварки.
Наиболее широко применяемая технология сварки двухслойных сталей основана на следующей последовательности сварочных операций:
сварка основного слоя ручной электродуговой сваркой электродами типа Э-42 или автоматической под флюсом АН-348А или ОСЦ-45 проволокой Св. 08, Св. 08А и др.; наложение разделительного шва с применением присадочных материалов, по возможности предотвращающих в результате разбавления снижение коррозионной стойкости сварных швов, обращенных к агрессивной среде, и обеспечивающих получение пластичного металла разделительного шва; сварка плакирующего слоя.
Рекомендуется способ сварки стыковых соединений с V-образной разделкой кромок. Сначала сваривается основной слой присадочным материалом такого же состава, затем подготавливаются кромки (на металлорежущих станках, вырубкой, шлифовкой) с таким условием, чтобы захватить металл сварного шва основного слоя и удалить шлаковые включения и возможные трещины в корне шва. После этого накладываются разделительный шов и облицовочные швы, перекрывающие разделку.
Все эти способы характерны тем, что плакирующий слой сваривается, как правило, в последнюю очередь и неизбежно изменение химического состава облицовочного шва за счет частичного разбавления углеродистой или другой сталью основного слоя с соответствующим снижением коррозионной стойкости.
Известно, что действующая стандартная технология сварки не всегда обеспечивает требуемый срок эксплуатации аппаратов из двухслойных сталей, сварные швы которых часто преждевременно разрушаются.
Поэтому для сварки двухслойного металла 20К + ЭП 567 были исследованы двенадцать способов сварки, в различных вариантах наложения швов и разделки кромок (от I до XII).
- Структура сварных соединений
Металлографические исследования сварных соединений проводили на образцах, выполненных по различным вариантам сварки. Структуру исследовали в центре каждого валика, а также на границе сплавления шва со сталью 20К и сплавом ХН65МВ. Проводили замер микротвердости структурных составляющих в исследуемых участках на приборе ПМТ-3 с нагрузкой 0,490 Н. Результаты замера микротвердости структуры сварных соединений двухслойного металла 20К + ХН65МВ (ЭП 567), выполненных аргоно-дуговой и электродуговой сваркой, форма разделки кромок, порядок наложения швов и марка присадочного материала приведены в табл. 21. Из табл. 21 видно, что в вариантах сварки I - IV была использована V-образная разделка кромок с наложением разделительного слоя электродом ЭНТУ-3/св. 07Х25Н13 (вариант I); электродом ЦТ28/св. X15НI50M6 (вариант II); электродуговой сваркой проволокой ЭП 567 (вариант III); в варианте IV разделительный шов был выполнен электродом ЭНТУ-3 на проволоке из хастеллоя W, состоящей из сплава хастеллой В с добавкой 5 % Сr (хастеллой В: 0,05 % С; 28 % Мо; 61 % Ni; 1 % Сr; 2,5 % Со; 5 % Fe; другие элементы 3 %). Сварка основного углеродистого слоя была выполнена ручной электродуговой сваркой электродом ЭНТУ-З/св. 07Х25Н13 во всех вариантах (I - IV).
на границах зерен металла и плакирующего слоя у линии сплавления выделились дисперсные карбиды в виде непрерывной цепочки в результате многократных термических воздействий при наложении второго и последующих слоев сварки. В шве обнаружена межкристаллитная коррозия в образце варианта V и МКК в зоне термического влияния в образце, выполненном по варианту VI; скорость общей коррозии составляла 0,51 мм/год при испытании в контрольном растворе НИИХИММАШа (кипячение в течение 96 ч в растворе:
10 % H2S04 + 30 % ΗΝ03 + 60 % Н20).
В разделительном слое первого шва V-образной разделки кромок, I выполненном электродами ЭНТУ-З/св. 07Х25Н13 (вариант I) и ЭНТУ-З/св. хастеллой W (вариант IV), обнаружены участки мартенситной структуры с высокой микротвердостью, равной 4670-5350 МПа. Кроме того, на границе сплавления металла шва первого и второго валиков, выполненного электродами ЭНТУ-З/св. 07Х25Н13, у линии сплавления со сталью 20К была обнаружена серая полоска с мартенситной структурой с высокой микротвердостью 4900 - 5270 МПа. На границе сплавления металла шва третьего валика, выполненного аргоно-дуговой сваркой проволокой ЭП 567 с углеродистой сталью, была обнаружена белая полоска, имеющая аустенитную структуру. Микротвердость белой полоски равна 3410 - 3070 МПа (рис. 48, а, б). I Низкие пластические свойства сварных соединений, выполненных по данным вариантам (угол изгиба плакирующим слоем внутрь составлял 75°, а изгиб наружу 50 - 72 и 20 - 48°),объясняются наличием мартенситной полоски на границе сплавления с углеродистой сталью.
Серая полоска со структурой легированного мелкоигольчатого мартенсита шириной 0,05 мм, очевидно, возникает в результате диффузионных процессов, - диффузии углерода из стали 20К в легированный металл шва. Наибольшую опасность представляет серая хрупкая полоска. Можно предположить, что именно по этой полоске отслаивается металл шва от основного металла из углеродистой стали при загибе образцов углеродистым слоем наружу. Образование трещины происходит строго по границе сплавления стали 20К с металлом шва, выполненным электродами ЭНТУ-З/св. 07Х25Н13.
При исследовании структуры двух сварных образцов, выполненных с Х7образной разделкой кромок (варианты VIII и IX), было установлено, что первый слой, выполненный электродом УОНИ-13/45, имел ферритно-перлитную структуру; зерно феррита мелкое (№ 8), микротвердость феррита в металле шва равна 1880 МПа. Микроструктура второго разделительного шва, выполненного аргонодуговой сваркой проволокой ЭП 567, состояла из столбчатых кристаллов аустенита, по границам которых выделились карбиды.