Станы холодной прокатки труб
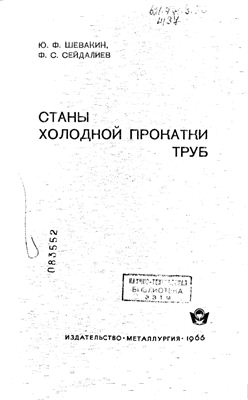
Шевакин Ю. Ф. , Сейдалиев Ф. С.
Металлургия, 1966 г.
Модернизация станов
Наиболее целесообразной представляется следующая характеристика станов промежуточных типоразмеров; ХПТ-32 с допустимым давлением 0,29—0,34 Мн (30—35 тс), ХПТ-55 0,49— 0,59 Мн (50—60 тс), ХПТ-75 1,2—1,3 Мн (120—130 тс).
Рассмотрим возможность модернизации действующих станов и оценим ее эффективность.
Модернизации действующих станов должна осуществляться с минимальными переделками деталей и узлов стана. Этому требованию удовлетворяет такая модернизация, при которой конструктивным изменениям подвергается рабочая клеть и ее узлы, остальные механизмы стана остаются без изменения. По объему и сложности производимой реконструкции, а также по эффективности ее могут быть предложены два варианта модернизации.
Первый вариант связан с минимальными переделками: рабочие валки вместе с опорными подшипниками, кассетами, комплектом шестерен и другими деталями остаются без изменения, а станину рабочей клети отливают из легкого сплава.
Второй вариант требует проведения большого объема работ: рабочие валки изготавливают меньшего диаметра, соответственно изменяют размеры кассет, шестерен и т. д.; рабочую клеть (станину) отливают из легкого сплава, при этом в зависимости от принятого типа крепления калибров конструкция станины рабочей клети может быть изменена.
Общим для обоих вариантов модернизации станов ХПТ является то, что длина хода клети остается постоянной (LKJl = = const). Отличительной особенностью второго варианта по сравнению с первым является его большая эффективность, так как при этом достигается большее снижение массы подвижных частей стана.
5. СИЛОВЫЕ ПАРАМЕТРЫ ПРОЦЕССА ПРОКАТКИ . Удельное и полное давление металла на ролики
Роликовая прокатка труб характеризуется значительной неравномерностью деформации металла. Из-за использования на стане ХПТР ручья постоянного радиуса на большей длине рабочего конуса калибр, образованный роликами, не является замкнутым. Чем ближе к началу рабочего конуса, тем больше зазор между ребордами соседних роликов. Последнее приводит к тому, что объемы металла, заключенные, между роликами, подвергаются, внеконтактной деформации. Это увеличивает удельное давление в очаге деформации, приводит к возникновению значительных растягивающих напряжений во внеконтактных зонах деформации, а следовательно, и к снижению пластичности деформируемого металла. Условия пластической деформации в очаге усугубляются также неравномерностью ее по периметру ручья. Вследствие несовпадения кривизны ручьи и рабочего конуса на большей длине его обжатие металла по дну ролика меньше, чем боковыми поверхностями. Последнее также приводит к росту удельного давления.
Таким образом, при всех, прочих равных условиях деформация металла на роликовых станах сопровождается большими удельными давлениями и протекает, в условиях менее благоприятных, чем на валковых станах.
1. краткая характеристика станов
В течение последних 5—8 лет в ряде стран [27—32] для изготовления тонкостенных труб большого диаметра применяют способ поперечной прокатки. Процесс осуществляется на цилиндрической (рис. 49, а) или на конической (рис. 49, б) оправке профильными -валками, располагающимися на равном расстояний друг от друга по периметру трубы.
При прокатке происходит утонение трубной заготовки. Смещаемый металл в одном случае (рис. 49, а) расходуется на увеличение длины трубы, а в другом (рис. 49, б) — на увеличение диаметра.. По характеру деформации металла процесс называют прокаткой с вытяжкой (рис. 49, а) или валковым расширением труб (рис. 49, б).
Основным рабочим усилием при поперечной прокатке является осевое усилие, которое прикладывается к переднему или заднему концу трубы. В связи с этим процесс часто в технической литературе называют процессом ротационного выдавливания.
Помимо- продольного перемещения, заготовка получает также вращательное движение, которое сообщается ей или оправке, или валкам. При холодной поперечной прокатке, как правило, оси валков лежат в одной плоскости с осью трубы. Иногда Оси валков оказываются' повернутыми на некоторый „угол, называемый углом подачи. В случае приводных валков наличие угла подачи обусловливает появление осевой втягивающей силы, которая может быть достаточной для непрерывного осуществления процесса. Если валки неприводные, то угол подачи снижает осевое сопротивление перемещению металла и для осуществления процесса требуется приложение меньшего рабочего усилия.
В качестве исходных заготовок используют катаные, сварные, кованые и штампованные из листовой заготовки трубы (стаканы).
2. КОНТАКТНАЯ ПОВЕРХНОСТЬ МЕТАЛЛА С ВАЛКОМ
В зависимости от схемы пластической деформации металла форма и размеры контактной поверхности существенным образом изменяются
Расчет обжатий в поперечном сечении
Рассмотрим процесс поперечной прокатки труб на цилиндрической оправке валками, имеющими конический профиль (рис. 55). Примем, что оси валка и трубы взаимно параллельны и лежат в одной плоскости
Линией АВ обозначим положение образующей рабочего конуса в момент выхода ее за линию центров валка и оправки'. Для непрерывного осуществления поперечной прокатки необходима непрерывная принудительная осевая подача трубы (или валков).
5. КАЛИБРОВКА РАБОЧЕГО ИНСТРУМЕНТА Валковое расширение труб
Условия формоизменения металла при пластической деформации существенным образом сказываются на силовых параметрах процесса, качестве полученных изделий, их геометрии. Сочетание раздачи и поперечной прокатки при валковом расширении труб обусловливает сложный характер деформации металла.
Было проведено исследование характера пластического формоизменения металла при валковом расширении труб, с помощью штифтов, координатной сетки и др. Валковое расширение предварительно подготовленных заготовок осуществляли на конической оправке с углом наклона образующей к ее оси а = = 0,1396 рад двумя коническими валками.
6. ВЫБОР ОСНОВНЫХ КОНСТРУКТИВНЫХ К ТЕХНОЛОГИЧЕСКИХ ПАРАМЕТРОВ СТАНОВ
Схема процесса
Выбор схемы процесса, определяется назначением и сортаментом проектируемого стана поперечной прокатки труб. Анализ силовых, деформационных и скоростных условий позволяет оценить достоинства и недостатки каждой возможной схемы, процесса. Наиболее предпочтительной можно считать поперечную прокатку труб по схеме растяжения. При прокатке, труб на длинной подвижной оправке усилия деформации оказываются минимальными. Это облегчает условия работы рабочего инструмента, снижает мощности главного-привода и узла подачи, улучшает геометрию труб (так как продольное натяжение способствует посадке трубы на оправку и уменьшению поперечной разностенности), снижает вероятность потери продольной устойчивости тонкостенных труб. Вследствие того что оправка при прокатке перемешается в продольном направлении относительно валков, существенно повышается её стойкость. Это имеет важное значение при прокатке труб большого диаметра. Наряду с преимуществами прокатка на длинной оправке имеет ряд недостатков. Длина прокатываемых труб ограничена, так как она не может быть, больше, длины оправки. Изготовление оправок большой длины сложно и не всегда может быть оправдано. Длина хода подающего устройства увеличивается, что также ограничивает длину прокатываемых труб. В результате усложняется конструкций стана поперечной прокатки или его эксплуатация. При прокатке труб по схеме растяжения на короткой подвижной оправке уменьшаются усилия деформации (по сравнению со схемой сжатия), однако меньшей степени, чем на длинной оправке. Сохраняются также другие положительные особенности процесса по схеме растяжения, выраженные в несколько меньшей степени, чем при прокатке на длинной оправке. В тоже время эта схема не имеет таких недостатков предыдущей схемы, как ограничение Длины прокатываемой трубы. Облегчаются условия изготовления инструмента, снижается длина хода подающего устройства и упрощается конструкции стана.
Прочие параметры станов
Степень пластической деформации металла при прокатке на цилиндрической оправке может быть весьма значительной (до 75—85%) за проход. Это обусловлено высокой дробностью деформации и чередованием деформаций и «отдыха» металла при прокатке Снижение максимальной деформации за проход наблюдается при прокатке по схеме сжатия (не более 75%), а также при высокой неравномерности деформации по толщине трубы из-за остаточных напряжений.
Осевая подача за „оборот трубы на практике колеблется в широких пределах от десятых долей миллиметра и до 2—3 мм и в основном определяется геометрией и качеством поверхности труб. С увеличением подачи возможно появление «винторого следа» на поверхности труб, что свидетельствует о недостаточной полировке металла цилиндрическим пояском или выходным конусом валка. Увеличение длины цилиндрического пояска на валках может вызвать раскатку труб.
Осевая подача за оборот трубы может быть увеличена.при переходе, к большему числу рабочих валков. В то же время увеличение числа валков усложняет конструкцию стана. Оптимальным числом рабочих валков исходя из простоты конструкции стана и удобства обслуживания его следует считать три валка. При прокатке труб большого диаметра (более 700—1000 мм), когда жесткость оправки достаточно высока, можно использовать двухвалковую схему [31]