Справочник токаря (5-е издание)
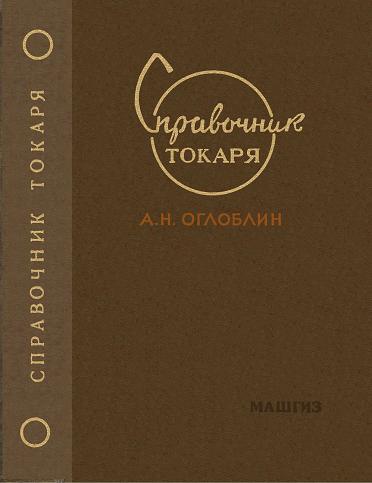
Оглоблин А.Н.
Машгиз, 1960 г.
II. ОБРАЗОВАНИЕ СТРУЖКИ И ЯВЛЕНИЯ ЕГО СОПРОВОЖДАЮЩИЕ
1. ВИДЫ СТРУЖКИ
Процесс образования стружки при резании металлов впервые исследовал в 1870 г. русский ученый, проф. И. А. Тиме.
Он установил, что каждый элементстружки (фиг. 5), образующийся при обработке резцом Rстали, отделяется от основной массы металла по плоскости, условно показанной на фиг. 5 линией РР и называемой плоскостью скалывания.
По данным опытов И. А. Тиме, величина угла А,образуемого плоскостью скалывания с направлением движения резца, лишь незначительно зависит от величины угла резания 6 и изменяется в весьма узких пределах — от 145 до 155°.
Продолживший работу И. А. Тиме и углубивший ее результаты русский исследователь Я. Г. Усачев доказал, что при резании вязких, но твердых материалов, например твердой стали и стали средней твердости, кроме
скалывания элементов стружки, происходят еще сдвиги частиц металла в каждом элементе по плоскостям NN(фиг. 6). Направление этих сдвигов составляет с плоскостью скалывания угол от 0 до 30°, в зависимости от вязкости металла: чем вязче металл, тем ближе этот угол к 30°, и наоборот.
Я. Г. Усачев установил также, что при резании более мягкой и вязкой стали перемещения частиц стружки происходят лишь по плоскостям, параллельным плоскости NN.
В результате указанных особенностей процесса резания вязких материалов образуется стружка скалывания. В зависимости от механических свойств обрабатываемого металла и некоторых других факторов процесса резания стружка скалывания бывает трех видов: элементной, ступенчатой или сливной.
Элементная стружка образуется при обработке материалов малой вязкости, но твердых. Элементы этой стружки сразу же после образования отделяются один от другого (фиг. 7, а) или сохраняют между собой слабую связь.
Ступенчатая стружка получается при обработке материалов средней твердости со средней скоростью резания, причем элементы ее сохраняют между собой более или менее прочную связь (фиг. 7, б). Поверхность этой
Фиг. 5.
Фиг. 6.
Фиг. 7.
стружки, соприкасающаяся с передней поверхностью резца, получается гладкой, а противоположная ей — ступенчатой.
Сливная стружка (фиг. 7, в), образующаяся при резании вязких и мягких материалов (мягкая сталь, латунь) с высокой скоростью резания, имеет вид завивающейся ленты. Поверхность такой ленты, скользящая по передней поверхности резца, получается гладкой, а противоположная ей — шероховатой, иногда с едва видимыми, но в некоторых случаях с вполне заметными сдвигами элементов, характерными для ступенчатой стружки скалывания.
Вид стружки зависит не только от обрабатываемого металла, но и от других условий процесса резания. Так, например, при точении стали средней твердости резцом с большим углом резания может образоваться не сливная, а элементная стружка. При повышении скорости резания элементы стружки не успевают настолько деформироваться, чтобы отделиться один от другого, вследствие чего вместо элементной может получиться сливная стружка.
Стружка надлома (фиг. 7, г) образуется иначе. Вследствие хрупкости металла (чугун, бронза), разрушение его в процессе отделения стружки происходит без заметной пластической деформации. Элементы стружки, в этом случае отделяющиеся от основной массы металла по произвольной поверхности, имеют различную величину и форму.
2. НАРОСТ И ЕГО ВЛИЯНИЕ НА ПРОЦЕСС РЕЗАНИЯ
Явление нароста, образующегося при резании вязких металлов, установленное и объясненное русским ученым Я- Г. Усачевым, состоит в следующем. При скольжении стружки по передней поверхности резца возни-
Фиг. 8.
кают силы трения, задерживающие ее движение. Вследствие этого деформации в слоях металла, расположенных ближе к передней поверхности, увеличиваются. Частицы металла этих слоев отделяются от непрерывно движущихся слоев стружки и прилипают (привариваются) к передней поверхности резца (фиг. 8, а). Большое давление резания способствует упрочнению металла нароста. С течением времени нарост увеличивается (за счет наращивания новых слоев металла), причем часть нароста нависает над задней поверхностью резца (фиг. 8, б). В некоторый момент эта часть нароста отрывается от его основной массы и, попадая между задней поверхностью резца и обработанной поверхностью (фиг. 8, в), вдавливается в последнюю (фиг. 8, г).
Частицы нароста, оставшиеся на передней поверхности, также отрываются от резца и уносятся со стружкой (фиг. 8, д). Такие срывы нароста происходят быстро один за другим (70-80 срывов в секунду), что объясняется, по-видимому, вибрациями, возникающими в процессе резания.
При малых скоростях резания (до 5 м/мин) нарост не образуется. Это объясняется тем, что при таких скоростях температура резания получается низкой и недостаточной для приваривания частиц стружки к передней поверхности резца.
При увеличении скорости резания до 10-20 м/мин температура резания получается достаточной для образования нароста, и именно при таких температурах имеет место наибольшая высота нароста. При более высоких скоростях резания (до 60-80 м/мин) стали средней твердости происходит более или менее заметное образование нароста. При скорости свыше 60-80 м/мин нарост наблюдается реже, а при еще более высоких скоростях он совсем не заметен.
Нарост обладает повышенной твердостью и поэтому может резать обрабатываемый материал, защищая режущую кромку от непосредственного воздействия стружки. В этом случае соприкосновение стружки с резцом происходит на площадке передней поверхности его, удаленной от режущей кромки, что улучшает поглощение резцом теплоты резания. С образованием нароста увеличивается передний угол резца, что способствует уменьшению сопротивления металла резанию. Все это создает более благоприятные условия резания при черновых работах.
При чистовых работах нарост вреден: сорвавшиеся и вдавленные в обработанную поверхность частицы нароста (фиг. 8, г) образуют неровности, недопустимые при чистовой обработке деталей. Полезное в данном случае уменьшение образования нароста достигается повышением скорости резания, применением емазочно-охлаждающей жидкости и улучшением путем доводки чистоты передней поверхности резца.
3. УСАДКА СТРУЖКИ
В результате пластической деформации срезаемой стружки длина ее получается меньше длины пути, пройденного резцом по поверхности резания. Это уменьшение длины стружки называется усадкой. Одновременно с усадкой происходит изменение формы, а также увеличение размеров поперечного сечения срезанного слоя, называемое разбуханием стружки. Ширина стружки получается почти равной ширине среза (немного больше), а толщина значительно превышает толщину среза.
В зависимости от условий обработки величина усадки получается различной.
При обработке хрупких материалов (чугуна, твердой бронзы и т. д.), при резании которых получается стружка надлома, усадка ее весьма мала, что объясняется слабым сопротивлением металла резанию в сравнении с сопротивлением его сжатию.
Значительно больше усадка стружки при обработке стали. Здесь в отдельных случаях стружка получается в 4-5 и более раз короче пути, пройденного резцом.
Чем больше передний угол резца, тем меньше усадка стружки, так как с увеличением переднего угла резца уменьшается его угол заострения. Внедрение более «острого» резца в металл происходит при меньшем сопротивлении последнего, что и обусловливает меньшую деформацию стружки.
С увеличением радиуса закругления вершины резца усадка стружки возрастает. Причина возрастания в том, что деформация стружки в зоне криволинейного участка режущей кромки резца сложнее, чем при прямолинейной кромке.
Чем больше скорость резания, тем меньше усадка стружки, так как при более высокой скорости резания элементы стружки «не успевают» деформироваться в такой степени, в какой это происходит при сравнительно низкой скорости.
Нарост, образующийся на передней поверхности резца во время его работы, существенно влияет на усадку стружки. При малых скоростях резания, когда нароста не бывает, усадка стружки получается наибольшей. При повышении скорости резания начинается образование нароста, передний угол резца увеличивается, усадка стружки уменьшается. При дальнейшем повышении скорости резания нарост убывает, действительный передний угол резца уменьшается, усадка стружки увеличивается до тех пор пока нарост не исчезнет полностью. С последующим увеличением скорости резания усадка стружки снова уменьшается. В этом случае, при отсутствии нароста, на процесс усадки стружки основное влияние оказывает скорость резания.
4. НАКЛЕП ПРИ РЕЗАНИИ МЕТАЛЛА
В процессе резания пластическая деформация происходит не только в срезаемом слое, но и в поверхностном слое основной массы металла. Глубина распространения деформации от поверхности резания и от обработанной поверхности зависит от ряда факторов и может достигать соты долей миллиметра, а в отдельных случаях даже целых миллиметров.
Пластическое деформирование вызывает упрочнение металла, его наклеп. Твердость наклепанного слоя в ряде случаев может значительно превышать твердость недеформированного металла.
Чем мягче обрабатываемый металл, тем большему наклепу он подвергается. При резании стали наклепанный слой может быть в З-4 раза тверже основного металла. Чугун упрочняется значительно меньше стали, как по величине твердости, так и по глубине распространения. Чем больше угол резания, радиус закругления вершины резца и подача, тем больше наклеп. При увеличении скорости резания с некоторого ее значения наклеп уменьшается.
Наклеп обработанной поверхности детали повышает ее износостойкость. Но с другой стороны, значительное увеличение твердости поверхности может иногда вызвать затруднения при дальнейшей ее обработке.