Справочник сварщика: Пособие для сварщиков, мастеров, технологов, конструкторов
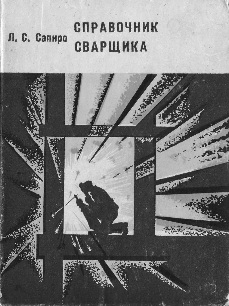
Сапиро Л.С.
Донецк, 1978 г.
Глава VIII. МЕТОДЫ КОНТРОЛЯ КАЧЕСТВА СВАРНЫХ ШВОВ
Для обеспечения условий получения качественных сварных швов необходимо вести контроль за соблюдением технологических процессов до начала сварки, в процессе сварки, а также контроль качества шва и сварного соединения после сварки.
До начала сварки следует проверить: документацию (сертификаты) на основной металл и сварочные материалы (электроды, проволоку, флюсы и т. д.); состояние металлов — наличие ржавчины, окалины и различных дефектов металла, а также состояние сварочных материалов — влажность, загрязненность и пр.; качество подготовки и сборки металлов, прежде всего величину зазоров между свариваемыми элементами, правильность разделки кромки— углы скоса и притупления; исправность аппаратуры; правильность выбранной технологии на образце.
В процессе сварки контролируют правильность ведения процесса: постоянство режимов, стабильность горения дуги, отсутствие видимых дефектов (трещин, пор, подрезов и т. д.), получение сварного шва заданной геометрии.
При сварке ответственных изделий правильность выбора металлов, материалов, режимов и техники сварки проверяют по контрольным образцам, которые сваривают одновременно с изделиями. Часто (исключая сварку кольцевых швов) контрольные пластины представляют собой продолжение сварного соединения изделия. На контрольных образцах проверяют механические свойства сварного соединения и наплавленного металла, макро- и микроструктуру (металлографические исследования), наличие скрытых трещин и микротрещин, газовых пор, шлаковых включений, а также непровар, коррозионную стойкость металла шва и зон термического влияния согласно ГОСТам и техническим условиям.
Методы контроля качества швов сварных соединений устанавливает ГОСТ 3242—69. Стандарт предусматривает выявление наружных дефектов, внутренних и сквозных.
Для выявления наружных дефектов применяют: внешний осмотр и измерения; контроль красками и люминофорами; магнитно-порошковый метод.
Внутренние дефекты выявляют, применяя технологические пробы, металлографический метод, контроль просвечиванием проникающими излучениями (радиографический метод), метод ультразвуковой дефектоскопии, магнитно-порошковый, магнитно-индукционный и магнитно-графический методы, контроль вскрытием.
Сквозные дефекты обнаруживают с помощью таких способов: смачивание керосином; обдув сжатым воздухом; контроль воздушным давлением; контроль аммиаком; контроль гидравлическим давлением; контроль наливом воды; контроль поливом водой; метод испытания течеискателями.
1. контроль внешним осмотром и измерениями
Внешний осмотр сварных швов применяется во всех случаях, независимо от других методов контроля, после тщательной очистки сварного соединения от шлака, брызг и других загрязнений. При осмотре выявляют: непровар, наплывы, прожоги, незаваренные кратеры, подрезы, трещины в сварных швах и в зоне термического влияния, пористость, смещение свариваемых элементов, правильность формы, размеров и расположения сварных швов, их соответствие чертежам, ГОСТам, нормалям, техническим условиям на изготовление сварного изделия.
Осмотр производят без применения лупы или с помощью лупы с увеличением до 10 раз. Границы трещин выявляют после шлифовки дефектного участка наждачной бумагой и травления.
2. контроль красками и люминофорами
ГОСТ 3242—69 предусматривает выявление красками и люминофорами дефектов, имеющих размеры
0,002—0,500 мм при сварке сталей аустенитного класса, нержавеющих, титана и его сплавов.
В 1973 г. введен ГОСТ 18442—73 «Неразрушающий контроль. Капиллярные методы» для выявления невидимых или слабо видимых глазом дефектов, выходящих на поверхность материалов и изделий любой формы. По способу выявления и регистрации дефектов аппаратуру подразделяют на люминесцентную, цветную и комбинированную (люминесцентно-цветную и т. д.).
Название «Капиллярные методы» связано со способностью некоторых жидкостей (светящихся или окрашенных) проникать в мельчайшие щели или отверстия (капилляры).
Люминесцентный метод контроля основан на способности ультрафиолетовых лучей вызывать свечение некоторых веществ (люминофоров), применяется для обнаружения мелких поверхностных дефектов (трещин, расслоений и т. д.) в ответственных деталях. Для контроля этим методом металл следует очистить от загрязнений и затем нанести на проверяемую поверхность жидкий раствор вещества — люминофора. Это может быть дефектоль, раствор которого в бензине при освещении ультрафиолетовыми лучами светится желто-зеленым светом. В поверхностные трещины за счет капиллярного давления проникает раствор вещества люминофора. После небольшой выдержки (10—15 мин) контролируемую деталь промывают, просушивают и в затемненном помещении облучают ультрафиолетовыми лучами. По свечению раствора на поверхности детали можно судить о наличии и расположении дефектов.
Цветной метод имеет сходство с люминесцентным, но более прост, не требует облучения проверяемой детали в темном помещении. Контролируемая поверхность обезжиривается авиационным бензином, смазывается или окунается в специальный (например, керосино-скипидарный) раствор, в который входит темно-красный анилиновый краситель. Время пропитки составляет 15—20 мин. После пропитки поверхность тщательно протирают и промывают 5%-ным раствором кальцинированной соды. Затем с помощью пульверизатора или кистью на поверхность наносят тонкий слой суспензии магнезии в воде или других суспензий, создающих светлый фон и обладающих способностью адсорбировать проникший в трещины и поры окрашенный раствор.
Дефекты проявляются в виде рисок или красных пятен (если применен темно-красный краситель). Время проявления дефекта — 30 мин.
3. магнитные методы контроля
Магнитные методы контроля основаны на свойстве магнитных силовых линий изменять свое направление в местах дефектов металла. Используя принцип магнитного рассеяния над дефектом металла при намагничивании, можно с достаточной точностью выявить наличие дефектных мест и на поверхности, и внутри металла (ГОСТ 21104—75 и ГОСТ 21105—75).
Магнитные методы контроля применяются для выявления дефектов в сварных швах, выполненных из ферромагнитных материалов (углеродистые, низколегированные и легированные стали).
Существуют три магнитных метода контроля металла: магнитно-порошковый, магнитно-индукционный и магнитно-графический.
Μагнитно-порошковыйметод согласно ГОСТ 3242—69 применим только на стыковых сварных соединениях. Размер выявляемого дефекта — не менее 0,10 мм. Метод заключается в том, что на поверхность контролируемого металла равномерным слоем наносят порошок (сухой метод) или эмульсию (мокрый метод), намагничивают металл и визуально фиксируют наличие дефектов. Порошок или эмульсия, попадая в магнитный поток рассеяния, вызванного дефектом, принимают форму дефекта.
В качестве магнитного порошка при сухом методе применяют измельченную железную окалину или закись-окись железа. Намагничивать металл можно с помощью» (Лектромагнита, соленоида или пропустив ток через контрольный материал (через сварное соединение). При напел» пни магнитного поля контролируемый металл слегка постукивают молотком, чтобы облегчить подвижность порошка, сдувают слабой воздушной струей, а по оставшемуся порошку определяют наличие и расположение дефектов. После контроля металл размагничивают. Дефекты фиксируются на глубину до 25 мм.
При мокром методе вместо порошка применяют магнитную суспензию, состоящую из жидкости (керосин, трансформаторное масло) и магнитного порошка. Дефекты обнаруживаются в местах магнитного рассеяния по скоплению порошка.
Магнитно-индукционный метод отличается тем, что магнитное рассеяние фиксируется с помощью индукционной катушки. Для контроля сварных соединений применяют магнитные дефектоскопы. В промышленности зарекомендовали себя индукционные дефектоскопы, позволяющие определять дефекты сварных, швов в стыковых соединениях толщиной 6—25 мм.
Магнитно-графический метод основан на фиксации потока рассеяния на магнитной ленте, которая плотно прижимается к поверхности шва. Отклонение силовых линий магнитного поля на ленте воспроизводится на специальном дефектоскопе. Используется при толщине швов 1—16 мм.
7. метод ультразвуковой дефектоскопии
Метод ультразвуковой дефектоскопии применяется при толщине металла не менее 6 мм. Он основан на использовании ультразвуковых волн, которые представляют собой упругие колебания материальной среды с частотой колебания выше 20 кГц (выше, чем та, которую способны воспринимать слуховые органы человека).
В этом методе контроля (ГОСТ 14782—69) используется способность ультразвуковых волн отражаться от границы раздела двух сред, обладающих разными акустическими свойствами. Когда при прохождении через сварной шов ультразвуковые волны встречают на своем пути дефекты (трещины, поры, шлаковые включения, расслоения и т. д.), они отражаются ог границы раздела металл — дефект и могут быть зафиксированы при помощи специальных ультразвуковых дефектоскопов.
Классификация дефектности стыковых сварных швов по результатам ультразвукового контроля приведена в ГОСТ 22368—77 (введен с 1.01.1978).