Справочник прокатчика: машиностроение и металлургия
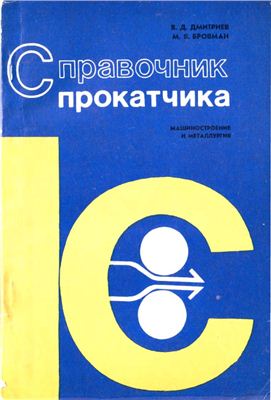
Дмитриев В.Д., Бровман М.Я.
Донецк, 1986 г.
РЕЖИМЫ ДЕФОРМАЦИИ И КАЛИБРОВКА
Выбор режимов обжатий и калибровка валков должны обеспечивать наибольшую возможную производительность стана и качество проката. Величины обжатий могут быть ограничены условиями пластичности металла (особенно для некоторых малопластичных металлов и сплавов), допустимыми величинами углов захвата и нагрузками в клетях. Для углеродистых сталей преобладают второй и третий факторы, что вынуждает применять все более мощные прокатные клети.
На обжимных станах осуществляют обжатия на гладкой бочке или в ящичных калибрах (в 2- и 3-валковых клетях). Режимы прокатки слитков на блюмингах приведены ниже (буквой «К» обозначена кантовка). Чем больше число кантовок, тем выше и качество, но зато меньше производительность.
Схема обжатий | Число проходов | Схема обжатий | Число проходов |
4К4К1 | 9 | 6К4К2К1 | 13 |
2К4К4К1 | 11 | 2Κ6Κ4Κ2ΚΙ | 15 |
6К4К1 | 11 | 4К4К4К2К1 | 15 |
2К6К4К1 | 13 | 2К4К4К2К2К1 | 15 |
4К4К4К1 | 13 | 6Κ4Κ2Κ2ΚΙ | 15 |
2К4К2К1 | 9 | 2К6К4К2К2К1 | 17 17 |
4К4К2К1 | 11 | 4К4К4К2К2К1 | |
2К4К4К2К1 | 13 |
|
|
•
В 3-валковых клетях ящичные калибры располагают один над другим и после прокатки в первом калибре (между нижним и средним валками) заготовки кантуют на 90° и подают в следующий калибр. При этом все нечетные калибры образованы средним и нижним, а четные — средним и верхним валками. Обычно при скорости прокатки 1 м/с задают обжатия так, чтобы углы захвата не превышали 28,5 , а при увеличении скорости до 3 м/с — 23°. Применяя валки с насечкой, можно увеличить эти углы соответственно до 33 и 25,5°. Выпуск ящичных калибров принимают равным 5—15°, что облегчает переточку валков, уменьшает износ и момент прокатки, но ухудшает устойчивость проката. На станах 3-валковых обычно скорости верхнего валка выше на 1—3 %, а в чистовых проходах на 0,2—0,8 %. В черновых1 калибрах их поверхность выполняют с волновой профилировкой, что повышает устойчивость заготовок. Верхнее давление несколько снижает расход! энергии и согласно принципу экстремума полной фрикционно-пластической мощности способствует равномерности распределения нагрузки между рабочими и шестеренными валками.
Ящичные калибры применяют и в первых группах непрерывно-заготовочных станов. Ранее (на станах 850/700/500) применяли глубокие врезы калибров. Наличие больших врезов на валках приводит к тому, что катающий диаметр значительно меньше номинального. Так, если номинальный] .диаметр валков 850 мм, то катающий 640 мм, т. е. меньше на 33%.
Это уменьшает допускаемые обжатия по углу захвата и приводит к тому, что не используются полностью возможности стана. Кроме того, глубокие врезы уменьшают прочность валков. Недогрузка клетей 850 иногда приводит кперегрузке последующих клетей 700, особенно с вертикальным расположением валков, что весьма нежелательно.
Экспериментальное исследование, проведенное Южуралмашем и ВНИИметмашем на стане 850/700/500, показало, что часто в первой клети 850 сила прокатки менее 4 МН, а в третьей клети 700 с вертикальным расположением валков доходит до 4,5 МН, т. е., клеть 700 загружена сильнее, чем более мощная клеть 850. Увеличить обжатие в клети 850 и разгрузить тем самым клеть 700 нельзя, так как угол] захвата в первой клети велик (примерно 33—34°) и дальнейшее его увеличение недопустимо. Такой угол захвата имеет место из-за того, что большая глубина врезов уменьшает катающий диаметр. На ранее построенных станах уменьшить глубину врезов калибров не было возможности, так как для этого нужно было бы развести валки на большое расстояние, что не позволяла сделать конструкция клетей. Калибровка поэтому препятствовала полному использованию возможностей непрерывно-заготовочных станов.
На станах 900/700/500 уменьшили глубину вреза калибров и увеличили] расстояние между буртами валков до 100—140 мм. Это особенно необходимо на станах, прокатывающих блюмы больших размеров. В первой клети стана 900/700/500 глубина вреза калибра равна 100 мм, а катающий диаметр равен 700 мм, что обеспечивает надежный захват полосы валками: угод захвата 26° (если бы расстояние между буртами было 50 мм, то угол захвата превысил бы 28°). Уменьшение глубины врезов позволяет более рационально распределять обжатия между клетями и лучше использовать их, но при этом уменьшается точность прокатки и увеличивается возможность появления таких дефектов, как потеря устойчивости полосы, ромбовидность и т. д. Для того чтобы совместить эти требования, глубина врезов должна быть небольшой в первых клетях стана, где она наиболее сильно влияет на допустимые обжатия, и большей в последних клетях. Такая калибровка позволяет сочетать большие обжатия и высокую производительность с высокой точностью прокатки. Если в первых 4 клетях наибольшее расстояние между буртами валков 135 мм, то в последней клети первой группы оно составляет 15 мм. а затем с клети 9 «В» кантуют на 45° и деформируют в ромбических и квадратных калибрах (буквы «Г» и «В» означают горизонтальное и вертикальное расположение валков). В 1-х клетях непрерывной группы обжатия обычно ограничены углами захвата, а во 2-й и последующих клетях их можно увеличить, используя принудительную задачу за счет подпоров от предыдущей клети. Перед 2-й группой стана конец заготовки отрезают. Расплющивание конца при резке на маятниковых ножницах увеличивает длину горизонтальной диагонали. Расплющивание на 10 мм увеличивает угол захвата от 26,5-до 30°. При подаче заготовки в валки со скоростью, превышающей проекцию на горизонталь скорости валков, происходит двойной удар в зубчатых зацеплениях и в шарнирах универсальных шпинделей. Ухудшает условия-захвата и изгиб конца заготовки. Ее кантовка на 90° уменьшает пиковые нагрузки при захвате (расплющенная диагональ оказывается при этом параллельной осям вертикальных валков).
Были проведены эксперименты по прокатке с предварительно обжатым концом заготовки (на длине 300 мм), что уменьшило момент при захвате в 1,3—1,4 раза. При эксплуатации изношенных ножей конец заготовки после реза больше расплющен (иногда на 10—15 мм) и изогнут, что увеличивает угол захвата при вертикальном расположении валков. В последние годы некоторые зарубежные фирмы применяют вместо ящичных так называемые «готические» калибры, показанные схематически на рис. 3.4 дл< прокатки круглых заготовок. Однако они сложнее в изготовлении и хуже обеспечивают устойчивость проката. Во 2-х группах заготовочных станов (а иногда и в двух последних клетях 1-х групп) применяют систему ромб— квадрат. Два варианта такой калибровки показаны на рис. 3.5. На комбинате «Криворожсталь» предусмотрено грани ромбических калибров выполнять не прямолинейными, вогнутыми, что в два-три раза повышает их стойкость. Оптимальная вогнутость равна 0,2—1,5 мм для квадратных и 1,5—4,0 мм для ромбических.