Справочник по практическому металловедению
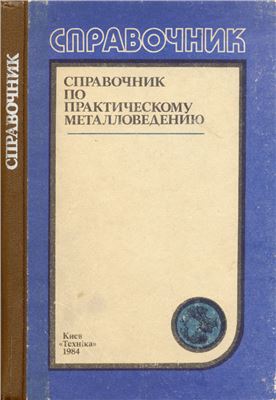
Пилюшенко В.Л., Винокур Б.Б. и др.
Киев Техника, 1984 г.
ОБЕЗУГЛЕРОЖЕННЫЙ СЛОЙ
Глубина обезуглероженного слоя зависит от состава стали и газовой среды, а также от температуры нагрева.
В соответствии с ГОСТ 1763—68 глубину обезуглероженного слоя определяют методами: металлографическими (М, Ml, М2), замера термоэлектродвижущей силы (термоЭДС), замера твердости, химическим (X).
Сущность металлографических методов заключается в определении глубины обезуглероженного слоя по микроструктуре. Металлографический метод М применяют при определении глубины обезуглероженного слоя конструкционных — углеродистых и легированных сталей с содержанием углерода не менее 0,3 %, для инструментальных — углеродистых и легированных, а также для рессорно-пружинных и подшипниковых, метод Ml (метод карбидной сетки) — для заэвтектоидной стали и метод М2 (метод Садовского) — для быстрорежущей.
Различают зоны полного и частичного обезуглероживания. Зона полного обезуглероживания характеризуется структурой чистого феррита. Зона частичного обезуглероживания имеет структуру, отличную от структуры основного металла. Общая глубина обезуглероживания измеряется от края шлифа до основной структуры металла. Если зона полного обезуглероживания отсутствует, то измеряют зону частичного обезуглероживания металла от края шлифа до основной структуры металла.
Общую глубину обезуглероженного слоя (мм) определяют в месте наибольшего развития под микроскопом при увеличении 63—150 с точностью до ±0,02 мм. Допускается увеличение 200—500. Глубину обезуглероживания х можно определить по формуле, %,
x =100 a/b,
где а — глубина обезуглероженного слоя при одностороннем измерении, мм; b — толщина проката или полуфабриката, мм.
Шлиф изучается по периметру, соответствующему поверхности проката. На образцах, вырезанных из полосы и ленты, исследуют широкую сторону на расстоянии не менее 2 мм от кромки. Из прутков (методы Ml и М2) вырезают образцы длиной 5—12 мм. Если диаметр прутка меньше 25 мм, то на образце сошлифовывают площадку до полного удаления обезуглероженного слоя.
При определении глубины обезуглероженного слоя методом М образцы исследуют в состоянии поставки. При исследовании методом Ml образцы подвергают специальной термообработке и окрашивающему травлению. Образцы нагревают до 950 °С в ваннах с различными расплавами, чтобы исключить обезуглероживание, например, в расплаве поваренной соли с добавлением 0,5—2,0 % активированного угля. Выдерживают их 5—7 мин и охлаждают со скоростью 15—30 °С в 1 мин до температуры на 30—50° ниже Arj, затем охлаждают на воздухе.
При использовании метода М2 образцы предварительно нагревают до 820— 840 °С, затем переносят в хорошо раскисленную хлорбариевую ванну и выдерживают в ней 1—3 мин. В зависимости от марки стали температура ванны 1210—1290 °С. Образцы охлаждают сначала в масляной или соляной ванне в течение 10 мин. Температура этой ванны также зависит от марки стали и находится в пределах 160—220 °С. После этого образцы переносят в другую соляную или свинцовую ванну с температурой 580—560 °С, выдерживают 10 мин и охлаждают на воздухе.
По методам М и М2 шлифы травят в 2—4%-ном растворе азотной или пикриновой кислоты в этиловом спирте (можно и в других реактивах) до четкого выявления структурных составляющих. Если шлиф травят в 4%-ном растворе азотной кислоты в метиловом спирте, то после промывки его необходимо просушить теплым воздухом. По методу Ml шлифы травят в течение 5—30 мин в кипящем реактиве, окрашивающем карбидную сетку. Для метода Ml зона частичного обезуглероживания имеет ферритно-перлитную структуру без окрашенной в темный цвет карбидной сетки; для метода М2 — темно-травящуюся трооститную или игольчатую троосто-мартенситную структуру.
МЕЖКРИСТАЛЛИТНАЯ КОРРОЗИЯ
Одним из серьезных недостатков нержавеющих ферритных, аустенито-мартенситных, аустенито-ферритных и аустенитных хромоникелевых сталей и сплавов является склонность их к межкристаллитной коррозии [61]. Она представляет наибольшую опасность для химической аппаратуры, так как при действии коррозионной среды разрушение металла происходит преимущественно по границам зерен, и при благоприятных условиях может идти с очень большой скоростью. Скорость коррозии зависит от химического состава стали, структурного состояния и агрессивности коррозионной среды [72].
Межкристаллитная коррозия у хромистых и хромоникелевых сталей проявляется в горячих растворах азотной кислоты, ее смесях с серной кислотой, в сернистокислых растворах в присутствии меди и железа, в смеси плавиковой и азотной кислот, в органических кислотах, в атмосферных условиях и многих других средах. Очень часто межкристаллитное разрушение возникает в сварных соединениях на некотором расстоянии от наплавленного металла там, где основной металл подвергался сравнительно длительному разогреву при 400—800°С.
Методы испытания на межкристаллитную коррозию приведены в ГОСТ 6032—75. Стали и сплавы в зависимости от их химического состава и назначения испытывают по следующим методам: AM, АМУ — в водном растворе меди сернокислой и серной кислоты с добавлением медной стружки; В — в водном растворе меди сернокислой и серной кислот с добавлением цинковой пыли; ВУ — в водном растворе железа сернокислого окисного и серной кислоты; ДУ — в водном растворе азотной кислоты; Б — анодным травлением в водном растворе серной кислоты. В стандарте приведены варианты термической обработки образцов сталей различных классов перед испытанием на межкристаллитную коррозию. Как правило, это дополнительный провоцирующий нагрев, который может вызвать склонность стали или сплава к межкристаллитной коррозии.
Из заготовок сталей аустенитного класса вырезают по два образца, а из стали ферритного, аустенито-ферритного и аустенито-мартенситного класса — по четыре, из которых два — контрольных. Контрольные образцы изгибают на 90° и в растворе не испытывают.
После термообработки или сварки поверхность образцов очищается химическим травлением. Для сталей аустенитного и аустенито-ферритного классов его проводят в растворе, содержащем 475 г/дм3 азотной кислоты и 75 г/дм3 фтористого аммония при температуре 20±5°С до удаления окалины.
Межкристаллитная коррозия по методу AM для большинства коррозионно-стойких сталей исследуется в растворе, содержащем 160 г сернокислой меди, 100 мл серной кислоты плотностью 1,835 г/см3 и 1000 мл воды, в присутствии медной стружки, причем при приготовлении раствора следует растворить необходимое количество сернокислой меди в воде, а затем небольшими порциями добавить серную кислоту. Испытания проводят в колбе с обратным холодильником или в бачке из хромоникелевой стали, стабилизированной титаном или ниобием, с крышкой, снабженной холодильниками. На дно реакционного сосуда насыпают слой медной стружки, поверх которой загружают образцы. Реакционный сосуд заполняют раствором примерно на 20 мл выше поверхности образца или слоя стружки. Раствор с образцами кипятится непрерывно в течение 15— 24 ч в зависимости от группы сталей. После испытания образцы промывают водой и просушивают. При осаждении на них слоя меди, не смываемого струей воды, ее удаляют промывкой в 20—30%-ном растворе азотной кислоты.
Для обнаружения межкристаллитной коррозии по окончании испытаний образцы должны быть загнуты на 90°. При испытании образцов, толщина которых не превышает 5 мм, рекомендуется проверять обе поверхности. Для этого изгибом образцу придают Z-образную форму. Осматривают такие образцы с помощью лупы с увеличением 8—12. Наличие трещин на поверхности изогнутых образцов свидетельствует о склонности к межкристаллитной коррозии. В этом случае испытание повторяется на двойном количестве образцов. При получении даже на одном из них трещин при изгибе металл считается не выдержавшим испытание на межкристаллитную коррозию.
В тех случаях, когда невозможен изгиб образца, склонность к межкристаллитной коррозии допускается оценивать металлографическим способом. Для этого из образца, прошедшего коррозионные испытания, вырезают шлиф, причем плоскость разреза должна быть плоскостью шлифа. Наличие и глубина межкристаллитной коррозии устанавливаются на протравленных шлифах при увеличении 400. Травление проводится лишь до слабого выявления границ зерен. Режимы травления шлифов и реактивов для выявления межкристаллитной коррозии приведены в ГОСТ 6032—75. Шлиф просматривается с двух сторон (по ширине коррозионного образца); в сварных образцах — со стороны контрольной поверхности. Среднюю глубину разрушения определяют по максимальным значениям, выявленным в 6 полях зрения, в которые включаются участки с наибольшей глубиной межкристаллитной коррозии. Свидетельством склонности к межкристаллитной коррозии является разрушение границ зерен на глубину более 30 мкм.
Испытание на межкристаллитную коррозию по методу АМУ проводится аналогично ускоренному методу AM в течение 8 ч при температуре кипения.
Межкристаллитная коррозия по методу В для стали 03X21Н21М4ГБ и сплавов 06ХН28МДТ и 03ХН28МДТ определяется в растворе, содержащем ПО г сернокислой меди, 55 мл серной кислоты плотностью 1,835 г/см3, 1000 мл воды и 5 г цинковой пыли, в стеклянных колбах или бачках из сплавов на железо-никелевой основе или высоконикелевых сплавов, снабженных обратными холодильниками. На дно реакционного сосуда укладывают стеклянные трубки или фарфоровые лодочки, поверх которых загружают образцы. Затем сосуд заполняют раствором на 20 мм выше поверхности образцов и добавляют необходимое количество цинковой пыли. Когда бурная реакция выделения водорода закончится, реакционный сосуд соединяют с холодильником. Продолжительность испытаний — 144 ч при температуре кипения. Межкристаллитная коррозия обнаруживается аналогично методу AM и АМУ.
Межкристаллитная коррозия по методу ВУ изучается у тех же сталей, что и по методу В в водном растворе железа сернокислого окисного и серной кислоты. Требования к реакционному сосуду и к укладке образцов для испытаний те же, что и для метода В. В сосуд с образцами засыпается необходимое количество заранее растертого в фарфоровой ступке железа сернокислого окисного из расчета 40 г на 1000 мл серной кислоты, заливается холодная серная кислота, раствор которой состоит из 389 мл кислоты плотностью 1,835 г/см3 и 611 мл воды. Количество раствора на 1 см2 поверхности образца должно быть не менее 5 мл. Межкристаллитная коррозия обнаруживается так же, как и по методу AM.
Межкристаллитная коррозия по методу ДУ контролируется у сталей 03Х16Н15МЗ, 03Х17Н14М2, 03Х18Н11, 03Х18Н12 в растворе 65%-ной азотной кислоты. После приготовления раствор выдерживается не менее 24 ч. Образцы обезжириваются, промываются, просушиваются и взвешиваются на аналитических весах с погрешностью не более 0,1 мг. Кроме того, образцы измеряют не менее чем в трех точках по длине, ширине и диаметру с погрешностью не более 0,05 мм. Образцы заливаются раствором кислоты из расчета не менее 9 мл на 1 см2 поверхности образца. Колбы с образцами и раствором устанавливаются на нагревательные устройства в вытяжном шкафу, обеспечивающие равномерный нагрев колб. После 48 ч кипячения образцы извлекаются из колб, промываются, просушиваются, взвешиваются и, после смены раствора, загружаются вновь. Продолжительность испытания составляет 5 циклов по 48 ч каждый. При скорости коррозии образцов менее 0,3 мм/год после третьего цикла испытания заканчиваются. Для обнаружения межкристаллитной коррозии определяют скорость коррозии образцов на каждый 48-часовой цикл испытаний. Образцы считаются не выдержавшими испытания, если скорость коррозии стали, сварного соединения или металла шва после любого цикла превышает 0,5 мм/год.
Методом Б контролируется наличие межкристаллитной коррозии изделий и деталей, изготовленных методами сварки, горячей штамповки и гибки из сталей 12Х18Н9, 08Х18Н10, 08Х18Н10Т, 06Х10Н11, 12Х18Н9Т, 04Х18Н10, 12Х18Н10Т, 03Х18Н11, 08Х18Н12Т, 12Х18Н12Т. Металл сварного шва не подлежит контролю этим методом. Анодным травлением контролируются участки шлифованной поверхности детали в водном растворе серной кислоты при плотности тока 0,65 А/см2. Шлифованные контрольные участки обезжиривают и протирают спиртом. В свинцовый сосуд (катод) наливают 3—5 мл электролита, состоящего из 60%-ной серной кислоты и технического 0,5%-ного уротропина. Продолжительность испытания после включения тока — 5 мин. При повышенной травимости продолжительность испытаний сокращается до 1—2 мин. Склонность стали к межкристаллитной коррозии оценивается при просмотре пятна, получаемого на поверхности образца после анодного травления, под микроскопом при увеличении не менее чем 30. При контроле готовых изделий, когда возможность применения микроскопа исключена, допускается использование лупы при увеличении не менее чем 20. Свидетельством склонности к межкристаллитной коррозии является наличие непрерывной сетки в местах анодного травления. В случае отсутствия непрерывной сетки полосчатость в местах анодного травления не является браковочным признаком.
В случае сильного растравливания, связанного с пониженной общей коррозионной стойкостью или с очень высокой склонностью стали к межкристаллитной коррозии, повторные испытания на контрольных образцах проводятся по методу AM и АМУ.
Кроме указанных методов оценки склонности стали к межкристаллитной коррозии, могут быть использованы и физические методы контроля: ультразвуковой, метод вихревых токов и цветной (ГОСТ 6032—75).