Справочник механика заводов цветной металлургии
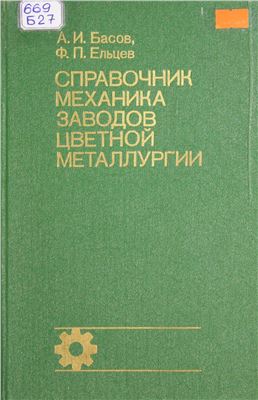
Басов А.И., Ельцев Ф.П.
Металлургия, 1981 г.
ОТРАЖАТЕЛЬНЫЕ ПЕЧИ
Основная область применения отражательных печей — плавка медной и медно-никелевой шихты и рафинирование черновой меди. Отражательная печь — плавильный агрегат (рис. VIM и VI1-2) с горизонтально расположенным рабочим пространством. Основные части печи; подина (лещадь), фундамент, стены, свод, подпятовые балки, загрузочные устройства, газоход и каркас (металлическое крепление). Отличительной особенностью отражательной печи является наличие ванны, заполняемой расплавом, и свода, участвующего в теплообмене между факелом и сводом шихты.
Шихта, загруженная в печь, располагается по обеим сторонам свода около продольных (боковых) стен печи откосами. Откосы обращены к центру печи, к факелу пламени. Раскаленный свод как бы отражает тепло, полученное им от топочных газов.
Современные отражательные печи характеризуются большими габаритами — площадь пода составляет 300—400 м2. Печи для медной плавки площадью пода 170 240 м2 имеют следующие основные размеры, м:
Длина по ванне..... 30,0—32,8
Ширина по ванне .7,2—8.0
Высота от лещади до свода 2,4—3.8
Глубина ванны.... 0,8—1,1
При глубине ванны около 1000 мм масса расплава достигает 1000—1200 т. Общая масса крупной печи может превысить 3000 т.
Горелки (форсунки) устанавливают на передней торцовой стене. Наибольшая температура газов 1450—1550° С в головной части печи, в плавильной зоне. В конце печи температура снижается до 1220— 1280° С, при выходе из печи составляет около 1100° С.
Продукты плавки: штейн (соединение меди с серой, железом, цинком, никелем, свинцом и др.) и шлак (содержит главным образом кремнезем, оксид железа (II), оксид кальция и др.) скапливаются в ванне по всей площади подины. Штейн выпускают со дна ванны из шпуров, расположенных на боковых стенах печи, примерно на 1/3 длины печи от задней стенки. Шлак выпускают с поверхности ванны из хвостовой части печи.
Использование тепла в печи низкое, в пределах 30—40%, что обусловлено высокой температурой отходящих газов и большими размерами печи. Потеря тепла с отходящими газами составляет 40—60%. Около 15% общего тепла теряется в окружающую среду через стенки, свод и лещадь. Установка котлов-утилизаторов обеспечивает утилизацию тепла отходящих газов на 30—40%.
Почти все отечественные отражательные печи работают на природном газе или смеси его с мазутом. Расход условного топлива при переработке сырой шихты составляет 16—20%, а при переработке обожженной шихты 8,8—14,0% от массы шихты. Удельный проплав при работе на сырой шихте 4,5—5,1 т/(м2-сут), а при работе на обожженной — до 8,7 т/(м2-сут). Причины сравнительно низкого проплава: контакт раскаленных газов с расплавленным материалом происходит только по поверхности расплава; значительнаν часть печи является отстойником. Большая зона отстаивания расплава обеспечивает получение в печи сравнительно бедных шлаков и высокой степени извлечения меди—в пределах 96—99%. К числу достоинств отражательной печи относят также следующее: возможность переплавлять разнообразные материалы (концентрат, мелкую руду) без предварительной обработки, а также обожженный материал — огарок; возможность использования различного топлива; простота конструкции и технологического процесса плавки, возможность его автоматизации. Кроме низкого проплава, недостатками печи являются: весьма низкое содержание в отходящих газах сернистого ангидрида (SO2) в пределах 3—5%, что не позволяет использовать их для производства серной кислоты.
Для интенсификации процесса плавки рудного сырья и повышения технико-экономических показателей широко используют подогрев вдуваемого воздуха (за счет тепла отходящих газов) до 200—350° С и воздушное дутье, обогащенное кислородом. Применение обогащенного дутья, содержащего 25% кислорода, позволяет повысить производительность печи на 10,3%, снизить расход топлива на 9,2% и сократить вынос пыли с топочными газами. Подсчитано, что при использовании подогретого до 500° С дутья производительность печи повышается на 27—29% и расход топлива снижается на 35—38% по сравнению с этими показателями при холодном дутье.
Фундамент современной отражательной печи сооружают из железобетона (по периметру) с заполнением бетоном. Фундамент устанавливают на плотном грунте, исключающем возможность появления почвенных вод; от случайного подхода грунтовых вод фундамент и стены печи тщательно изолируют. Около печи не допускается расположение водопроводов н паропроводов. В фундаменте предусматривают вентиляционные каналы и проходы для охлаждения и осмотра подины.
Подина печи должна быть огнеупорной, непроницаемой и стойкой к агрессивному воздействию штейна и шлаков. Набивные подины (прежняя конструкция) изготовляют из кварцевого песка (94—95% кремнезема) слоями толщиной около 100 мм. Каждый слой утрамбовывают, а верхний— наваривают при 1500—1600° С. В последних конструкциях печен подину выкладывают из кирпичей в виде обратного свода (см. рис. VII-2), верхние ряды из прочного, высокоогнеупорного и химически стойкого хромомагнезитового кирпича. ,
Стены печи с внутренней стороны выкладывают на высоту ванны из хромомагнезитового кирпича. Выше уровня ванны кладку выполняют из динасового кирпича. Снаружи стены облицовывают шамотным или легковесным шамотным кирпичом. Для компенсации теплового расширения предусматривают температурные швы размером 25—30 мм через каждые 2—3 м по длине стен. На уровне лещади толщину стен 1200—1500 мм, в верхней части 500— 700 мм. Применение блочной конструкции стен позволяет облегчить механизацию ремонтных работ.
В связи с интенсификацией процесса плавки стены печи подвергаются сильной тепловой нагрузке, снижающей срок их службы. Для повышения стойкости и предупреждения размыва стен и прорыва расплава из печи применяют кессонирование стен до уровня шлакового слоя. Водоохлаждаемые кессоны устанавливают также на передней стене печи над заливочным окном и горелочными окнами.
Свод печи бывает: распорно-арочный, распорно-подвесной и подвесной. Арочный свод прост в изготовлении, но имеет недостаточную стойкость. Большие распорные усилия передаются на подпятозые балки и каркас печи, ограничивают увеличение ширины печи. Арочные своды выкладывают обычно из динаса-огнеупора, сохраняющего свою прочность при очень высоких температурах.
Подвесной свод, как и распорно-подвесной, состоит из отдельных блоков. В усовершенствованных конструкциях печей предусматривают систему воздушного охлаждения подвесного свода и возможность его самоуплотнения. Достоинства этого свода; повышение срока службы в 2—3 раза по сравнению со сроком службы арочно-распорного; освобождение колони каркаса от распорных усилий. Замена арочного свода подвесным в модернизированной печи Норильского комбината (см. рис. V1I-1) позволила удлинить кампанию печи более чем в 2 раза. Каждый блок этой печи собирают из шести магнезито-хромитовых кирпичей с высокой огнеупорностью, превышающей 2000е С. Для повышения стойкости, снижения подсоса воздуха и облегчения работы по замене блоков кирпичи склеивают цементным клеем (70% магнезитового порошка и 30% чугунной стружки).
Каркас печи состоит из колонн (стоек) и горизонтальных связен колонн. Колонны сваривают из швеллеров и двутавровых балок крупных профилей. На колоннах закрепляют подпятовые балки, через которые тепловые распорные усилия от свода передаются на каркас печи. Колонны противоположных стен соединяют вверху стальными тягами (обычно Ст5) диаметром 40— 80 мм. Колонны устанавливают и закрепляют в колодцах фундамента печи (глубиной 500—600 мм) или стягивают, как и вверху колонн, стальными тягами.
Сухую шихту (огарок) в старых печах загружают через вертикальные воронки в своде, в модернизированных конструкциях— через отверстия в боковых стенах.
Это дает возможность снизить унос мелкой дисперсной фракции огарка и
показывающие степень расширения свода. Своды регулярно очищают от пыли обдувкой; следят за состоянием подвесок и тяг, одновременно регулируют нажатие пружин, обеспечивая более или менее равномерное распределение распорного усилия между колоннами каркаса. Предельный износ распорного свода не должен превышать 2/3 его первоначальной толщины; остаточная тол-шина стен в зоне выше ванны не должна превышать 150 мм, в зоне ниже ванны 300 мм.
Максимальная температура в печи не должна превышать: 1550°C при динасовом своде и 1650° С при хромомагнезнтовом. Предельная температура продуктов плавки: 1200° С —штейна и 1300° С — шлака.
В процессе эксплуатации особое внимание должно быть обращено на герметичность свода, загрузочных устройств, шлаковых желобов, являющихся источниками выделения пыли и газа. Загрузочные воронки в местах сопряжения их со сводом или стеной печи следует тщательно уплотнять асбестовой набивкой; внутрь трубы нужно подавать сжатый воздух для создания аэрозатвора. Шлаковые желоба необходимо держать закрытыми; угол их наклона принимают не менее 0,06. Сжатый воздух подводят под свод печи для его охлаждения и повышения долговечности. Свод и стены печи поддерживают в исправном состоянии торкретированием. Горячий ремонт свода проводят со специальных площадок при отключенных подачах топлива и дутья. Начинать ремонт со свода и ходить по своду запрещено.
Капитальный ремонт отражательной печи осуществляют преимущественно по сетевому графику. Перед остановкой на ремонт должны быть опорожнены бункера печи, загрузочные устройства, конвейеры, питатели. Допуск рабочих внутрь печи возможен только после обрушения свода. Разогрев принятой из капитального ремонта печи проводят по специальному графику. После окончания разогрева тщательно проверяют состояние кладки, устраняют выявленные дефекты. Перевод печи на рабочее отопление считается началом ее эксплуатации.