Специальные технологические процессы и оборудование обработки давлением
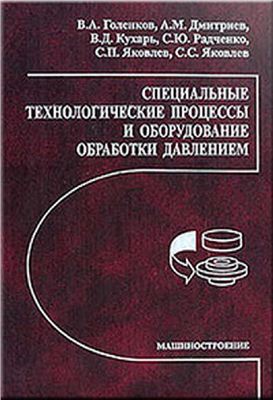
Голенков В.А., Дмитриев А.М., Кухарь В.Д., Радченко С.Ю.
Машиностроение, 2004 г.
ЧАСТЬ 1. ВАЛКОВАЯ ШТАМПОВКА
Глава 1. Сущность и классификация процессов валковой штамповки
Основные схемы валковой штамповки
Валковая штамповка формоизменяющая операция обработки металлов давлением, получения осесимметричных деталей из цилиндрической заготовки за счет одновременного приложения к ней осевых и радиальных нагрузок. Осевое нагружение заготовки при валковой штамповке создается за счет перемещения
пуансона, а радиальное - за счет обкатки ее боковой поверхности в роликах или валках. Таким образом, валковая штамповка [ 1 ] представляет собой способ комплексного локального деформирования, в котором в одном технологическом процессе происходит совмещение одной из основных кузнечных операций -прошивки или осадки (высадки) с поперечной прокаткой или обкаткой (рис. 1.1,1.2).
Новый способ деформирования позволяет изготавливать круглые в плане сплошные и полые детали, тонкостенные и толстостенные изделия малых размеров, применяемые в приборостроении, а также крупногабаритные детали с высокой точностью и качеством при технологической силе на порядок меньшей, чем для традиционных методов объемной штамповки. Комплексное нагружение очага пластической деформации локальным периодическим воздействием с одновременным воздействием через постоянно фиксируемую зону позволяет получить новый технологический эффект, недостижимый другими методами деформирования. Валковая штамповка способствует улучшению физико-механических свойств обрабатываемого металла, обеспечивает требуемое расположение его волокон, что повышает эксплуатационные свойства получаемых деталей. Относительно низкая стоимость оснастки, незначительное время подготовки производства, возможность быстрой переналадки на другой типоразмер детали, использование оборудования небольшой мощности позволяют применять валковую штамповку как в крупносерийном, так и в средне- и мелкосерийном производствах.
За счет возможности концентрировать формоизменение заготовки на позиции выдавливания внутренней полости с одновременным обкатыванием и последующей осадкой, величина пластического деформирования и смещенные объемы металла на последующих позициях обработки малы, как малы и необходимые силы деформирования. Это позволяет на последующих операциях вести доводку детали до требуемой формы и точности.
1.2. Классификация процессов валковой штамповки
Процессы валковой штамповки можно классифицировать по следующим признакам:
- по геометрической форме исходной заготовки и получаемых деталей;
- по способу привода вращения заготовки;
- по количеству роликов или валков.
1. По геометрической форме исходной заготовки и получаемых деталей.
Общим признаком деталей, возможности изготовления которых открывает валковая штамповка, является симметрия всех поперечных размеров относительно оси заготовки. Согласно предлагаемой схеме (рис. 1.3) из класса получаемых валковой штамповкой осесимметричных деталей можно образовать две большие группы, отличающиеся друг от друга наличием осевого отверстия.
К первой группе относятся простые в изготовлении детали без отверстия с одним или несколькими наружными утолщениями, расположенными на различных участках заготовки (пробки, заглушки и т.д.). Ко второй группе относятся детали с отверстием, как с глухим (с полостью), так и сквозным. Геометрия наружной поверхности деталей этой группы совпадает с формой поверхности деталей без отверстия. Это ступенчатые детали с одним или несколькими наружными утолщениями (фланцы, втулки и т.п.) и детали без наружных утолщений (гильзы, стаканы).
Возможность изготовления валковой штамповкой осесимметричных деталей со сквозным осевым отверстием, в отличие от остальных известных способов объемной штамповки, объясняется особенностями пластического течения материала в условиях комплексного локального деформирования.
2. По способу привода вращения заготовки.
Технология валковой штамповки может осуществляться по одной из двух кинематических схем, отличающихся друг от друга способом привода вращения заготовки. В первом случае вращение заготовки осуществляется посредством передачи ей крутящего момента приводными валками [2], во втором крутящий момент заготовке передается от упора и пуансона [3], а валки, или в этом случае ролики, являются неприводными.
Схема с приводом от валков имеет ряд недостатков, один из которых заключается в том, что момента трения при большом радиальном обжатии может оказаться недостаточно для преодоления сопротивления деформированию, что приводит к заклиниванию заготовки и приводных валков.
Валковая штамповка, осуществляемая по данной схеме, сложнее валковой штамповки с приводом вращения от упора и пуансона, которая с точки зрения повышения качества получаемых деталей, снижения энергосиловых затрат, увеличения производительности и технологичности оснащения предпочтительнее, поскольку обеспечивает развитие тангенциальных сжимающих напряжений в локальной зоне, исключает возможность проворота роликов относительно заготовки, позволяет увеличить скорость деформирования и применять смазку контактной поверхности роликов.
Аналогом такой кинематической схемы является случай, когда деформирование боковой поверхности заготовки осуществляется вращением вокруг нее роликовой матрицы, а не упора и пуансона. При этом очевидно, что выбор упомянутой схемы не обеспечивает дополнительных преимуществ, а лишь усложняет конструкцию технологической оснастки, в частности делает практически неосуществимым контролируемое сведение-разведение роликов в процессе обработки, однако для изготовления крупногабаритных деталей такой способ привода представляется единственно возможным.
3. По количеству роликов или валков.
Валковая штамповка может осуществляться по двух-, трех- и многороликовой (или многовалковой) схемам. При штамповке в двухроликовой матрице по схеме с передачей крутящего момента от приводных валков для удержания заготовки на позиции обработки необходимо применение специальных захватно-ориентирующих устройств (рис. 1.4, а). При этом необходимо обеспечить включение привода вращения валков только после возникновения на поверхности пуансона и заготовки сил, достаточных для ее удержания на позиции обработки. В противном случае в начальный момент штамповки заготовку может вытолкнуть из роликовой матрицы (рис. 1.4,6). При валковой штамповке в двухроликовой матрице по схеме с приводом вращения от упора и пуансона применения захватно-ориентирующих устройств не требуется.
С дальнейшим увеличением количества роликов их максимальный радиус уменьшается, при этом изменяется глубина проработки заготовки в радиальном направлении и нагрузка, воспринимаемая каждым из роликов. Устойчивость заготовки повышается, однако усложняется процесс ее позиционирования и извлечения с позиции обработки. Таким образом, наиболее приемлимым представляется использование трехроликовой матрицы. В дальнейшем все теоретические расчеты и экспериментальные исследования будут проводиться только для такой схемы.
Наиболее значимое влияние на процесс валковой штамповки оказывают следующие технологические параметры и режимы обработки: отношения радиусов пуансона и заготовки (Rn/R), заготовки и роликов (R/RK), форма торцовой поверхности пуансона, относительная скорость деформирования заготовки и количество роликов или валков. Относительная скорость деформирования при валковой штамповке учитывается отношением скорости перемещения пуансона к частоте вращения заготовки и определяет величину радиального обжатия заготовки и производительность процесса. Определение технологических параметров и режимов обработки с учетом характерных особенностей напряженно-деформированного состояния и пластического течения металла в процессе деформирования является основной задачей при проектировании технологических процессов валковой штамповки.