Специальные стали. Том 2
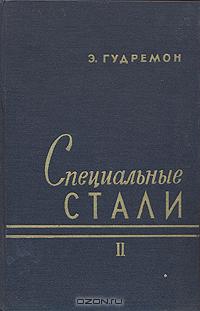
Гудремон Э.А.
Металлургия, 1966 г.
Технология азотирования
Преимущества применения азотированной стали заключаются в экономичности процесса азотирования. Технология процесса состоит в следующем. После улучшения на желаемую прочность заготовки обрабатывают до окончательных размеров, обязательно полностью удаляя окисленный или обезуглероженный слой. Затем детали азотируют в газовом разряде или загружают в печь и медленно нагревают в струе аммиака до 500° С, иногда в условиях газового разряда, выдерживают при этой температуре обычно от одних до четырех суток и медленно охлаждают в потоке аммиака. Выгружаемые из печи детали должны обладать конечной прочностью и твердостью. Азотированные детали, очевидно, не требуют никакой закалки, в противоположность цементированным. Азотирование не приводит к какому-либо короблению при условии, если подлежащие такой обработке детали не будут иметь остаточных напряжений.
Улучшенные, свободные от напряжений и обработанные в размер детали благодаря увеличению объема в процессе поглощения азота увеличивают толщину на 0,02—0,03 мм, что можно заранее учесть. При одностороннем азотировании очень тонкие детали могут получить искривление. Это незначительное формоизменение более или менее равномерно.
Быстрорежущую сталь обычно азотируют не в струе аммиака, а в жидкой цианистой ванне (см. стр. 869). При этом процессе закаленная сталь подвергается отпуску. В зависимости от желаемой толщины слоя и поверхностной твердости азотирование длится 1—10 ч при 500— 550° С. Образующийся при этом слой имеет глубину до 0,1 мм.
Покрывая отдельные участки деталей оловом, никелем и т. д., можно защитить их от азотирования. Можно также лудить всю деталь и снять полуду в местах, подлежащих азотированию. О добавке активирующего газа при азотировании коррозионностойких аустенитных сталей уже было сказано выше.
Указания о применении азотирования
Преимущества азотированной стали побуждают применять ее в тех случаях, когда нужно ожидать сильного, истирания, например в плунжерах и поршневых штоках, особенно в машинах, работающих при повышенных температурах, когда действие смазки часто бывает недостаточным. Эти соображения справедливы для любых скользящих частей. Широкое применение азотированная сталь получила в первую очередь в точном машиностроении (производство станков) благодаря ничтожному износу в эксплуатации. Ее применяют и для деталей масляных насосов, например автомобилей, куда попадают мелкие частицы пыли, для коленчатых валов, в сельскохозяйственных машинах, которые работают в условиях сильной пыли при недостаточном уходе (например, смена смазки), для зубчатых колес.
При переходе с цементации на азотирование необходимо учитывать небольшую глубину и большую твердость азотированного слоя и, разумеется, проверять, подходит данная конструкция для азотирования или необходимо приспособить ее для этого процесса.
Устойчивость твердости и сопротивления износу до 500° С открывает для азотированной стали широкие возможности применения в технике пара высокого давления для шиберов, вентилей и т. д., а также цилиндров двигателей внутреннего сгорания, кокилей для центробежного литья, пулеметных стволов и т. д. Все эти детали благодаря азотированию обнаруживают также высокий предел усталости. Выше уже указывалось на азотирование быстрорежущей и других инструментальных сталей. Наконец, крайне малая поводка и возможность производить азотирование отдельных участков обусловили применение азотирования еще в ряде случаев. Сказанное относится и ко всем случаям, когда применение цементации сталкивается с большими трудностями, например при обработке сложных зубчатых колес с винтовым профилем (шестерни дифференциалов в автомобилях и т. п.), шлифовка которых после цементации чрезвычайно усложняется и удорожается. Процесс же азотирования может быть построен настолько точно, что практически не получится никакой поводки. Такие же условия возникают при изготовлении некоторых деталей текстильных машин, например игольных зажимов. Твердость и сопротивление износу этих деталей, часто имеющих тонкие борозды и углубления, вообще могут быть повышены только азотированием.
То же относится к производству сложных мерительных инструментов — калиберных колец, пробок и лекал. В азотированных инструментах отсутствуют закалочные напряжения, вследствие чего они даже при длительном хранении не обнаруживают сколько-нибудь существенных изменений размеров. В этом отношении азотированные детали ведут себя намного лучше закаленных и низкоотпущенных, так как в процессе азотирования при температуре выше 500° С снимаются даже те незначительные напряжения, которые существовали до азотирования или возникли в начальной его фазе.
При изготовлении инструмента, деталей и т. п. нужно обращать внимание на то, чтобы они не имели особенно острых кромок, так как кромка будет состоять лишь из твердого азотированного слоя и потому будет легко выкрашиваться.
Следует отметить особый способ получения твердой поверхности, который, однако, еще находится в стадии разработки. Он заключается в нанесении на поверхность деталей из железа и стали слоя нитридов титана 2 посредством реакции тетрахлорида титана с водородом и, азотом. Такой слой прочно удерживается на поверхности железа и при достаточной продолжительности процесса достигает толщины 100 мк. Слой очень тверд и настолько нехрупок, что даже может быть подвергнут деформированию вместе с основой без нарушения. Подобные слои на стали можно получать также и из карбида титана.
Повышение поверхностной твердости путем одновременного насыщения азотом и углеродом
Как уже упоминалось в разделе «Цементация» (см. стр. 276, т. I), в результате поглощения азота поверхностью образца процесс цементации ускоряется, что достигается либо обработкой стали в цианистой ванне, либо при добавке аммиака к твердым или газообразным карбюризаторам.
В вопросе о влиянии азота на процесс цементации нет еще полной ясности. Во-первых, возможно, что аммиак оказывает благотворное влияние на ход газовой реакции на поверхности стали вследствие образования цианистого водорода, а также препятствует образованию водяного пара и двуокиси углерода, во-вторых, в присутствии азота увеличивается скорость диффузии углерода в железе (см. рис. 233). Рис. 237 показывает, что поверхностное насыщение углеродом при добавке аммиака к смеси древесного угля со светильным газом повышается. Содержание азота в наружной зоне получается тем выше, чем ниже температура цементации. Выше 850° С из-за сильной диссоциации нитридов железа не удается получить азота больше 0,3%- Несмотря на это активация процесса цементации азотом позволяет достичь повышенного содержания углерода и при температуре около 900° С.
Путем добавок азота в различном состоянии и количестве к карбюризаторам при различных температурах процесса можно осуществить постепенный переход от чистой цементации до чистого азотирования. Этот переход начинается с добавки аммиака к твердым карбюризаторам. Далее идет применение расплавленных цианистых солей, в которых при сравнительно низкой температуре и коротком времени получается тонкий 'Слой со сравнительно высокой твердостью. Следующим этапом является газовое цианирование, т. е. одновременное насыщение углеродом и азотом из газообразной смеси углеводородов и аммиака. Конечной точкой этой цепи является азотирование посредством чистого аммиака (табл.242).
Из всех перечисленных способов техническое значение имеют жидкое цианирование и газовое цианирование (карбонитрирование). Оба процесса проводят обычно при несколько более низких температурах, чем нормальную цементацию. Так, в течение 30—40 мин, в жидком цианистом калии или железосинеродистом калии [K4Fe(CN)6] при 600 и 670° С достигается содержание углерода в наружном слое от 1,1 до 1,4% и азота от 1,1 до 1,3% при глубине цементации от 0,3 до 1 мм.Благодаря низкой температуре образования азотистого перлита железо при 600° С находится еще в состоянии и хорошо растворяет углерод и азот. Поэтому возможно проводить закалку с более низкой температуры, что уменьшает коробление. Кроме того, в сердцевине прошли уже все превращения и она находится в высокоотпущенном состоянии с максимальной вязкостью. Азот снижает также критическую скорость охлаждения, так что становится возможным закаливать чисто углеродистую сталь не в воде, а в масле. Правда, при таких условиях повышается количество остаточного аустенита. Вследствие большой инертности аустенитного превращения в поверхностном слое хорошие результаты после газового цианирования получаются при закалке в горячую ванну с температурой, немного превышающей точку сердцевины, которая при этом испытывает полное превращение. В то же время поверхностный слой при после дующем охлаждении на воздухе приобретает чисто мартенситную структуру. При такой закалке коробление почти полностью отсутствует (I способ, табл. 242), однако увеличивается количество остаточного аустенита в высоколегированных сталях.