Специальные способы сварки и резки
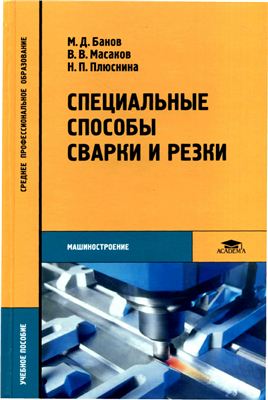
Банов М.Д., Масаков В.В.
Издательский центр Академия, 2009 г.
МИКРОПЛАЗМЕННОЙ СВАРКОЙ называют сварку сжатой дугой на малых токах (0,1... 15 А). При таких токах сваривают детали с толщиной кромок 0,025... 0,8 мм. По сравнению со сваркой открытой дугой изменение длины малоамперной сжатой дуги оказывает значительно меньшее влияние на качество сварного соединения. Устойчивого и стабильного горения такой дуги на малых токах достигают благодаря высокой степени сжатия столба дуги каналом сопла малого диаметра (менее 1 мм). При этом возрастает пространственная устойчивость дуги. При микроплазменной сварке используют плазмообразующий газ аргон. В качестве защитных газов — аргон, гелий, азот; смеси аргона с водородом или гелием и другие газы в зависимости от свариваемого металла. Катодная область малоамперной сжатой дуги постоянного тока находится в атмосфере плазмообразующего газа, а столб дуги и анодная область — в атмосфере защитного газа. Применение в защитной смеси молекулярных газов (азота, водорода) повышает напряжение дуги, увеличивает ее проплавляющую способность. В столбе дуги молекулы этих газов диссоциируют, поглощая энергию, что приводит к дополнительному сжатию дуги. При микроплазменной сварке дуга может принимать конусообразную форму или приобретать форму иглы, сходящейся к свариваемой детали. Плотность тока на острие этой иглы достигает 5 ООО А/см2. Высокая концентрация энергии и иглоподобная форма малоамперной сжатой дуги обеспечивают получение узкого шва и малой зоны термического влияния, что снижает деформацию изделий на 25... 30% по сравнению с аргонодуговой сваркой. Микроплазменную сварку применяют для соединения особо тонких материалов, исправления микродефектов (царапин, микротрещин) миниатюрных деталей, резки металлов и неметаллов, прецизионной наплавки. Малоапер-ная сжатая дуга нашла применение в радиоэлектронике и приборостроении при изготовлении полупроводников, термопар, мембран с арматурой, миниатюрных трубопроводов, сильфонов.
СУЩНОСТЬ ЭЛЕКТРОННО-ЛУЧЕВОЙ СВАРКИ (ЭЛС) состоит в использовании кинетической энергии направленного потока электронов, движущихся в вакууме (рабочий вакуум 10 2... Ю-3 Па) без столкновений с остаточными молекулами воздуха. При достижении потоком электронов, ускоренных электрическим полем с разностью потенциалов 10... 100 кВ и более, поверхности свариваемой детали подавляющая часть кинетической энергии электронов превращается в тепловую. Вакуум применяют как для эффективной генерации электронного пучка и беспрепятственного прохождения его до свариваемой детали, так и для создания инертной среды без вредных примесей (кислорода, азота и водорода).
Это позволяет получать сварные соединения высокого качества при сварке таких химически активных сплавов, как титановые, циркониевые, ниобиевые, молибденовые.
При выходе электронного луча в атмосферу рассеяние пучка электронов столь велико, что не удается увеличить рабочее расстояние от пушки до изделия больше чем на 30 мм, поэтому сварку с использованием электронного луча производят только в вакуумных камерах.
Электронный луч в зоне сварки обладает высокой мощностью, превосходящей традиционные сварочные источники нагрева, уступая только лучу лазера.
Взаимодействие электронного луча с обрабатываемым металлом вызывает ряд явлений, оказывающих влияние на технологию сварки и конструкцию сварочных установок. Тепловое и рентгеновское излучения, отраженные, вторичные и тепловые электроны снижают эффективно используемую долю энергии электронного луча.
Значения эффективного КПД при ЭЛС составляют 0,85 ...0,95. Таким образом, электронный луч, по сравнению с другими сварочными источниками энергии, самый эффективный. Проплавление существенно ограничено по глубине и в поперечном сечении близко по форме к полусфере. Такой процесс применяют для сварки металлов малых толщин (до 3 мм).
ЛАЗЕРНАЯ СВАРКА
В отличие от электронного луча, обеспечивающего высокую концентрацию энергии и используемого для сварки ответственных деталей, узлов и конструкций, лазерная сварка не требует вакуумных камер. Процесс лазерной сварки осуществляется на воздухе или в среде защитных газов, благодаря этому лазерную сварку можно применять для соединения элементов крупногабаритных конструкций. Лазерный луч с помощью оптических систем легко транспортировать и направлять в труднодоступные места сварных соединений. При этом обеспечивается надежное и оперативное управление процессом сварки с регулируемыми энергетическими характеристиками. Магнитные поля свариваемых деталей и приспособлений для сборки и сварки (технологической оснастки) воздействуют на электрическую дугу, плазму и электронный луч, но не влияют на лазерный луч. Это способствует получению устойчивого формирования сварного соединения по всей его протяженности. Для сварки металлов используют твердотельные и газовые лазеры импульсного и непрерывного действия. Лазерную сварку осуществляют в широком диапазоне режимов, обеспечивающих высокую производительность процесса сварки деталей толщиной от нескольких микрометров до десятков миллиметров. Сварка лазером дает шов «кинжального» типа с незначительными деформациями свариваемых деталей. Импульсные твердотельные лазеры применяют для сварки малых размеров деталей в изделиях микроэлектроники и приборостроения, где важно получать швы с малым объемом расплавленного металла и незначительными размерами околошовной зоны термического влияния. Сварку можно производить как отдельными точками, так и герметичными швами при последовательном наложении точек с их перекрытием.
Мощные газовые лазеры позволяют проплавлять за один проход детали толщиной более 10 мм. При этом имеются некоторые особенности: так для стали глубина проплавления до 5 мм требует 1 кВт мощности излучения на один миллиметр толщины металла. При дальнейшем увеличении мощности лазерного луча глубина проплавления увеличивается незначительно и для сварки металла толщиной 20 мм и более требуются очень мощные лазеры, потребляющие из сети сотни киловатт электрической энергии. Электронно-лучевая сварка позволяет сваривать за один проход гораздо большие толщины (до 200 мм) при значительно меньшем потреблении энергии от сети. Сварка лазером неметаллических материалов, таких как стекло и керамика, основана на том, что излучение лазера на углекислом газе с длиной волны 10,6 мкм хорошо поглощается этими материалами и может быть использовано для их нагрева, плавления, сварки и резки. По сравнению с газопламенным нагревом, традиционно используемым для сварки стекла, лазерный луч позволяет увеличить интенсивность нагрева места сварки или пайки (но не более 80... 100 К/с из-за опасности термического растрескивания стекла). Для успешного соединения свариваемых деталей необходимо уменьшить зону нагрева, что позволит создавать миниатюрные сварные конструкции из стекла.