Спецэлектрометаллургия сталей и сплавов
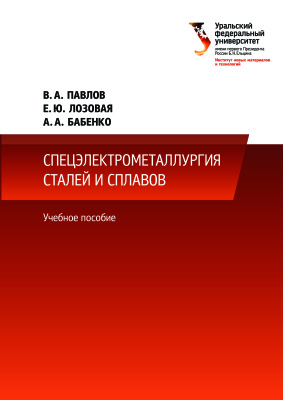
Павлов В.А., Лозовая Е.Ю., Бабенко А.А.
Екатеринбург: Уральский федеральный университет, 2018 г.
7.4. Технология выплавки стали и сплавов в индукционной печи
- Выбор футеровки
Для многих сталей кислая футеровка индукционной печи является вполне подходящей. Некоторые стали необходимо плавить в основных печах. К ним относятся стали и сплавы с высоким содержанием марганца, никеля, титана и алюминия. При выплавке высокомарганцовистых сталей кислая футеровка быстро разрушается, так как закись марганца реагирует с кремнеземом футеровки, образуя легкоплавкий силикат марганца. Алюминий и титан восстанавливают кремний из футеровки, и сталь из кислой печи с высоким содержанием алюминия или титана оказывается некондиционной по кремнию. Труднее объяснить низкое качество сталей и сплавов с высоким содержанием никеля или никеля и хрома — нержавеющих хромоникелевых сталей, сплавов типа нихромов (60— 80 % Ni и 14—20 % Cr) [24].
Высказывается предположение, что стали, выплавленные в кислой печи, загрязнены мелкодисперсными включениями кремнезема и монооксида кремния. Эти выделения не всегда различимы под микроскопом. Мелкодисперсная кремнистая муть ухудшает не только ударную вязкость, особенно «поперечную», но располагаясь между первичными кристаллами, в значительной степени и ковкость стали. Обработка металла высокоосновным шлакам снижает количество кремнистых включений.
Уход за тиглем в процессе эксплуатации. После выпуска плавки тигель очищают от оставшегося металла и шлака. По возвращении печи в нормальное положение рекомендуется сделать контрольные промеры тигля — нутромером измеряют диаметр в трех местах по высоте, линейкой — толщину подины. Когда стенка становится тонкой в каком-либо месте, это обнаруживается по быстрому потемнению футеровки в этом месте после выпуска плавки. Для подварки дна кислого тигля на поврежденное место насыпают смесь из кварцита и борной кислоты, слегка утрамбовывают ее, накрывают листом котельного железа и загружают шихту. Для подварки стен, когда толщина их уменьшится на 1/3, вставляют шаблон из двухмиллиметрового железа (без дна) и заполняют его шихтой. В образовавшееся между стенками тигля и шаблоном пространство засыпают кварцитовую массу и уплотняют ее стальным прутком диаметром 8— 10 мм. Продолжительность плавления после подварки увеличивают на 1— 4,5 часа для спекания засыпанного слоя.
При образовании небольших трещин на внутренней поверхности магнезитового тигля или ямок поврежденное место замазывают массой из мелкого магнезитового и магнезитохромитового порошка (1:1) с 10 % глины, увлажненной жидким стеклом. Стойкость магнезитового тигля повышается, если свести до минимума перерывы между плавками.
2. Загрузка шихты
Загрузка шихты в этих печах при большой их емкости легко механизируется и производится обычно в несколько минут.
При составлении шихты необходимо учитывать, что при плавке сталей в индукционных печах с кислой футеровкой весьма трудно освободить металл от серы и фосфора, поэтому содержание серы и фосфора в шихтовых материалах следует допускать как можно меньше (не выше 0,05%). В особенности это относится к чугуну, который иногда используют для повышения содержания углерода в шихте. Такой чугун должен содержать минимальный процент фосфора. Хотя из жидкой ванны сравнительно легко можно удалить избыток углерода, марганца и кремния, тем не менее содержание углерода в шихте не рекомендуется иметь более 0,1% против того количества, которое допускается в готовой стали. При большем избытке углерода в шихту добавляется железная руда (до 0,5% к весу шихты) или соответствующее количество окисленного скрапа. При плавке сталей в печах с кислой футеровкой необходимо учитывать, что шлак образуется частично за счет приставшего к скрапу песка, а также кремнезема футеровки печи. Плавка в печах с основной футеровкой имеет то преимущество, что она позволяет применять любой скрап, так как при этом процесс выгорания углерода, марганца и кремния идет довольно быстро.
В целях снижения расхода электроэнергии на 1 т металла ускорения процесса плавки шихту необходимо составлять с учетом рационального подбора размеров кусков шихты и плотной укладки в печи с учетом частоты тока, подаваемого в печь, так, например, при частоте тока 500—1000 Гц шихта не должна быть чрезмерно мелкой и окисленной, так как в этом случае может быть плохой электрический контакт вследствие недостаточной удельной мощности, генерируемой в кусках шихты с малым поперечным сечением. Чем меньше частота тока, тем крупнее должна быть шихта.
Так, при частоте тока до 500 Гц диаметр кусков шихты должен быть 20 мм и выше, при 1000 Гц этот размер может быть уменьшен до 10 мм, при 10000 Гц — до 5 мм и при большей частоте — меньше 5 мм.
На величину мощности, передаваемой в садку, оказывают влияние не только размеры и форма кусков, но и их расположение и укладка в тигле. Особенно большое значение эти факторы приобретают при плавке в больших печах (емкостью 1000 кг и выше), работающих, как правило, на относительно небольшой частоте (500—3000 Гц). В малых печах, работающих на высоких частотах, подбор шихты в основном производится лишь с точки зрения удобства ее загрузки, а также получения наибольшей плотности.
Опыт показывает, что максимальный магнитный поток концентрируется по высоте 2/3 тигля. Поэтому в этой зоне рекомендуют укладывать шихту с максимальной плотностью. В верхней же части шихту не следует укладывать очень плотно, чтобы обеспечить по мере оплавления свободное ее опускание вниз.
В соответствии с указанными выше требованиями, а также с заданным химическим составом выплавляемой стали, подготавливается шихта, которую необходимо загружать в печь с максимальной быстротой.
При этом рекомендуется соблюдать следующий порядок загрузки:
- на дно тигля укладывают часть мелкой шихты в виде стружки и скрапа, немного шлака и по I % ферромарганца и ферросилиция (чтобы не допустить переокисления и вскипания металла), а также такие тугоплавкие металлы, которые не склонны к сильному угару;
- крупную часть шихты рекомендуется укладывать у стенок тигля перпендикулярно направлению магнитных силовых линий, что создает более благоприятные условия для быстрого расплавления шихты;
- остальную часть шихты загружают так, чтобы добиться максимальной плотности ее укладки в тигле, поэтому мелкая часть шихты располагается между крупными кусками и в средней части тигля; в печах большой емкости (несколько тонн) рекомендуется загрузку шихты осуществлять при помощи бадьи, чтобы время загрузки довести до 1—2 мин.
Мелкой шихты желательно иметь не более 15 %, т. к. чем крупнее куски шихты и чем плотнее их укладка, тем быстрее идет плавка. В небольших печах, которые работают на высокой частоте тока, значение размеров кусков шихты, как было указано, уменьшается. Загружать тигель выше уровня индуктора не рекомендуется, так как это замедляет плавку.
Следует особо отметить, что чем плотнее укладывать шихту, тем быстрее идет плавка и тем меньше расход электроэнергии. После окончания загрузки шихты тигель следует закрыть керамической крышкой и включить ток [24].
3. Расплавление шихты
В течение первых минут пуска печи (до прекращения толчков) генератор необходимо держать не на полной мощности. После прекращения толчков генератор переводят на полную мощность. Так как оплавление шихты происходит в первую очередь в средней по высоте, а затем в нижней части печи, то в верхней ее части сравнительно легко может образоваться зависание частично сваренной шихты (образование «моста»). Это явление крайне нежелательно. Во-первых, оно способствует удлинению времени плавки, во-вторых, вызывает сильный перегрев расплавленного металла и сильное разъедание футеровки. Для того чтобы не допустить этого, необходимо тщательно следить за ходом плавки шихты и применять своевременные меры к опусканию верхних слоев шихты посредством ломика, имеющего ручку с резиновой изоляцией (толстостенный резиновый шланг).
По мере плавления и оседания шихты загружается остальная часть шихты, при этом не следует опускать в расплавленный сплав холодную шихту, так как в этом случае может произойти вскипание сплава, который зальет промежутки между кусками вверху тигля и тем самым создаст мост. При оплавлении шихты в печь дается первая порция шлакообразующих веществ, например, при кислом тигле подается смесь: 70 % формовочной земли, 25 % молотой извести и 5 % молотого плавикового шпата или бой оконного стекла и т.д.
При основном тигле в качестве шлакообразующих веществ применяется известь, плавиковый шпат и шамот. Такой шлак имеет следующий состав: 24-26% SiO2; 34-36% Al2O3 и 38-42% CaO с добавкой ферросилиция и алюминия.
В целях уменьшения степени окисления и достижения большей точности химического состава выплавляемой стали рекомендуется на дно тигля засыпать небольшое количество шлака, который расплавляется от тепла, передаваемого металлом, и всплывает на поверхность жидкого металла. Это мероприятие является особенно важным при плавке в больших печах, где процесс расплавления шихты занимает сравнительно большое время [24].
Для того чтобы улучшить взаимодействие между металлом и шлаком необходимо следующее:
- Повысить уровень жидкого металла в тигле за пределы индуктора. Это обеспечит уменьшение мениска зеркала ванны и тем самым уменьшит возможность сползания шлака к стенкам тигля.
- He допускать сильного захолаживания шлака. Для этого следует тигель по возможности все время закрывать керамической крышкой.
- Специально подогревать шлак, применяя для этого крышку из графита, которая в этом случае будет нагреваться от индуктированного в ней тока и излучать тепло на поверхность ванны, покрытую шлаком, или непосредственно подогревать шлак по принципу электросопротивления, ддя чего на расстоянии друг от друга 30 мм опускают в шлак на 50 % их толщины два графитовых электрода диаметром 30 мм и через них пропускают ток 100—150 А, при напряжении 50 В. Дуга при этом не должна возникать.
Шлак наводится в течение всего периода плавки в соответствии с технологией, установленной для данного сплава. Шлак не должен быть очень густым. В случае загустения его следует снять до того, как расплавится вся шихта, и вместо снятого шлака сейчас же дать свежую порцию шлакообразующих веществ. Поверхность шлака рекомендуется покрывать тонким слоем древесного угля, так как это способствует понижению концентрации кислорода над ванной, а следовательно, и уменьшению окисляемости металла.
Следует заметить, что наведение шлака рекомендуется проводить только в больших печах или при плавке специальных легкоокисляе- мых сплавов. В малых печах процесс плавки сталей идет весьма быстро и поэтому окисляемость незначительная. В этом случае шихту составляют с таким расчетом, чтобы не производить специальных операций по удалению примесей.
После расплавления всей шихты мощность печи снижают примерно на 80 % и берут пробу на полный анализ. Затем снимают старый и заводят новый шлак необходимого состава.
Для получения определенной марки стали применяют соответствующие ферросплавы, которые вводят через обнаженную от шлака поверхность ванны. После присадки каждой порции добавок металл нужно перемешивать, что обычно делают при помощи ломика.
Присадка ферросплавов в зависимости от степени их угара и других особенностей должна производиться в разное время. Так, например, ферромарганец и ферромолибден обычно присаживают за 10 мин до выпуска металла, поскольку марганец и молибден подвергаются значительному угару (до 30% за весь цикл плавки). Ферровольфрам и феррохром загружают в начале, так как вольфрам и хром угорают в небольших количествах.
Ферросилиций, так же как и ферромарганец, обычно присаживают за 10 мин. до выпуска; ферротитан присаживают за 2—3 мин до выпуска металла. Алюминий присаживают непосредственно в ковш, так как степень его угара чрезвычайно велика. После введения добавок необходимо удалить шлак, перемешать ванну и взять вторую пробу на экспресс-анализ. He дожидаясь окончательных результатов химического анализа о готовности металла к разливке, судят по поведению пробы в стаканчике.
Жидкий металл перемешивают железным прутком или специальной керамической палочкой. Перемешивание в больших печах обычно осуществляют металлическим прутком, хорошо ошлакованном в тугоплавком шлаке. В печах с малым диаметром тигля жидкую ванну перемешивают обычно посредством керамической палочки, например кварцевой трубкой, середина которой заполнена кварцевым песком с 2 % буры. В процессе перемешивания жидкой ванны рекомендуется вводить быстро окисляющиеся или легко испаряющиеся легирующие компоненты. Это позволяет значительно уменьшить процент угара этой части шихты [24].
Печь перед разливкой выключают и выдерживают металл перед выпуском 8—10 мин. Металл из печи выливают в прогретый ковш. Поверхность его в ковше покрывают шлаковой смесью, состоящей из 8—12 частей кварцевого песка и 4—5 частей дробленой извести, после чего ковш подается для разливки металла.
Задача окислительного процесса состоит в окислении углерода и фосфора, также попутно — кремния и марганца.
В печах с кислой футеровкой тигля удалить примеси путем окисления трудно, поэтому для плавки стали в этих печах необходима шихта с минимальным количеством вредных примесей.
В основном тигле необходимо окисление. В индукционной печи процесс окисления протекает с большой скоростью, которая обеспечивается как интенсивным перемешиванием металла в печи, так и возможностью точно регулировать температуру металла. Процесс окисления металла начинается с момента подогрева шихты; процесс окисления примесей (углерода, кремния, фосфора и др.) получает максимальное свое развитие при плавке шихты, в особенности, если шихта содержит большой процент скрапа углеродистых сталей. Окисление примесей происходит в этом случае за счет восстановления железа из оксидов (ржавчины и добавляемой руды).
Окисленный скрап обычно содержит влагу, как в виде адсорбированного слоя, так и в состоянии гидроксидов FeO · 4Fe2 O3 * ZH2O.
Освобождающийся водяной пар взаимодействует с железом (H2O + + Fe = FeCHH2), образуя при этом оксид железа и водорода, которые растворяются в металлической ванне. Оксид железа в свою очередь взаимодействует с углеродом, кремнием, марганцем, фосфором и другими примесями, образуя оксид углерода, кремнекислоту, оксид марганца, фосфористый ангидрид, которые в жидком металле не растворимы. Процесс окисления также может быть проведен при помощи подачи кислорода или обдувкой воздухом поверхности ванны. Полученные продукты окисления как имеющие сравнительно малые удельные веса поднимаются на поверхность ванны.
В печи с кислой футеровкой даже при наличии достаточного количества оксида железа невозможно освободиться от кремния и серы. Для защиты металла от окисления и абсорбции неметаллических частиц применяют в этом случае кислый шлак, который состоит из кварцевого песка (боя динасового кирпича или молотого стекла) и шамота (или извести).
Кремний в печи с основной футеровкой довольно легко выгорает. Для того чтобы достичь высокого процента выгорания углерода, нужно, как указано выше, иметь достаточное количество оксидов железа и хорошо прогретую жидкую ванну. Для успешного удаления из металла фосфора, кроме наличия в жидкой ванне оксида железа, нужно иметь в шлаке достаточное количество оксида кальция. Поскольку оксид кальция в шлаке взаимодействует с кислой футеровкой, очищение металла в печах с кислой футеровкой от кремния, серы и фосфора весьма затруднительно.
Наличие оксида кальция в шлаке необходимо для удаления фосфора и серы. При более высокой концентрации оксида кальция в шлаке и более низкой концентрации оксида железа в нем процесс десульфурации будет происходить успешнее. Для увеличения жидкотекучести шлака следует добавить необходимое количество плавикового шпата. Максимальный эффект десульфурации при этом получается не при окислительном, а при восстановительном процессе, о чем более подробно будет изложено ниже.
Удалить вредные примеси из жидкой ванны в индукционной печи с основной футеровкой можно было бы в течение нескольких минут, но практически это трудно осуществить, так как большое количество окисленного железа будет вызывать слишком энергичное кипение ванны и выплескивание из печи металла и шлака. Исходя из этого, железную руду рекомендуется присаживать небольшими порциями, каждый раз после успокоения ванны. Кроме железной руды, которой обычно расходуется 3—5 % от веса металлической шихты, присаживается также около 2% извести и 0,2% плавикового шпата, необходимого для повышения жидкотекучести шлака. Чем ниже вязкость шлака, тем энергичнее идет процесс удаления фосфора и серы. Такой шлак весьма успешно воздействует на жидкую металлическую ванну и за 15 мин снижает в ней содержание углерода на 70-80 %, фосфора на 50-60% и серы на 30-40%. Наряду с этим, выгорают также кремний на 40—50 % и немного марганца.
Процесс выгорания примесей может быть еще выше, если поверхность шлака защитить от охлаждения, закрыв тигель крышкой, изготовленной из теплоизоляционных кирпичей, или прогревая шлак. Как было указано выше, процесс удаления примесей начинается с начала плавления шихты. Для ускорения процесса окисления загружать шихту рекомендуется одновременно со шлаковой смесью в следующем порядке: сначала загружают на дно тигля тонкий слой скрапа, затем шлаковую смесь (стенки тигля при этом должны быть изолированы от шлаковой смеси тонким слоем скрапа), после этого укладывают металлическую шихту и на поверхность последней — известь и плавиковый шпат. Такой процесс загрузки и плавки позволяет за 15—20 мин удалить до 80 % С, до 95 % P и до 70 % S.
Из-за наличия в ванне электродинамических сил, вызывающих движение металла, поверхность жидкого металла делается выпуклой. Эта выпуклость сдвигает шлак к стенкам футеровки печи, что вызывает разъедание (или зарастание) футеровки.
В заключение следует указать, что более быстрого и совершенного окисления можно достигнуть в индукционной тигельной печи с основной футеровкой, вдувая на поверхность ванны воздух. В этом случае удается почти полностью удалить из ванны кремний и марганец, а процентное содержание углерода и фосфора довести до 0,02. Одновременно с этим будет происходить и сильное выгорание серы. Метод вдувания воздуха более эффективен в отношении скорости и степени выгорания примесей, чем окисление рудой. Разъедание стенок тигля при этом также уменьшается. Для уменьшения разъедания стенок тигля при основной футеровке рекомендуется добавлять в шлак магнезит в пределах 15—20 % от веса шлака. Шлак при этом не теряет своей жидкотекучести. Естественно, чем больше площадь соприкосновения металла с шлаком, чем выше температура шлака и чем меньше глубина ванны, тем выше скорость очищения металла от примесей, а также механические свойства выплавляемого металла.
Введения специальных легкоокисляющихся легирующих добавок как во время процесса окисления, так и вскоре после него нельзя допускать, поскольку это вызовет большой процент их угара. Такие добавки рекомендуется присаживать лишь после процесса раскисления и рафинирования.
4. Процессы раскисления и рафинирования
Как раньше уже отмечалось, особенностью индукционных печей без сердечника является электродинамическое перемешивание в ванне металла. Такое перемешивание ускоряет процессы раскисления и очищения сталей от неметаллических включений. При этом следует обратить внимание на процентное содержание окислов железа, которые после скачивания окисленного шлака всегда присутствуют в жидкой металлической ванне [24].
Наличие оксидов железа в металле оказывает очень вредное влияние на качество отливок. Это объясняется тем, что оксиды железа могут взаимодействовать с оставшимся в стали углеродом, образуя оксид углерода, который, оставаясь в стали в виде пузырьков газа, дает пористое литье. В процессе кристаллизации оксид железа выходит из раствора, оставаясь в нем в виде неметаллических включений, которые сильно снижают механические свойства литья. Следовательно, основной задачей раскисления является получение стали с минимальным содержанием кислорода. Наряду с этим процессы раскисления и рафинирования также способствуют освобождению стали от газов (водорода).
Существуют следующие методы раскисления ванны:
- раскисление жидкой ванны посредством добавления твердых раскислителей (марганца, кремния, алюминия, титана, ванадия, магния, циркония и др.);
- раскисление ванны углеродом, добавляемым к шлаку (диффузионный метод раскисления);
- фильтрация жидкого металла путем пропускания его через слой шлака.
Первый метод нашел наибольшее применение при плавке стали в индукционных печах без сердечника. При этом большинство раскислителей вводится в жидкую ванну в виде сложных сплавов и лигатур, а алюминий и магний в чистом виде. Ферросилиций, си- ликокальций и карбид кальция иногда вводятся для раскисления металла в виде порошка непосредственно в шлак. В таком случае реакции протекают на поверхности ванны. Это способствует абсорбции шлаком продуктов окисления и очищению сталей от мельчайших включений.
Существенное влияние на удаление примесей оказывает размер и вес их частиц. Перемешивание ванны в индукционной печи способствует соприкосновению мельчайших частиц, их укрупнению, подъему к шлаковой поверхности и абсорбированию. Шлак при этом должен иметь более высокое поверхностное натяжение, чем включения. В индукционной печи зеркало ванны, а также контактная поверхность металла со шлаком небольшие. Однако перемешивание расширяет сферу абсорбции, так как каждая перемещающаяся порция металла, быстро оборачиваясь, подходит к шлаку и увеличивает, таким образом, в несколько раз поверхность соприкосновения со шлаком. Это обеспечивает также более полное раскисление при меньшем количестве раскислителей. В то же время вследствие сокращенной поверхности шлака уменьшается окисление железа в шлаке.
Ниже приводятся (схематично) основные реакции раскисления железа при введении в ванну: силикокальция, ферросиликоциркония, ферросилиция, алюминия, карбида кальция и др.:
FeO + Mn = Fe + MnO; 3FeO + 2 Al = 3Fe + Al2O3; (7.1) 2FeO + Si — 2Fe + SiO2; FeO + Ca = Fe + CaO.
Окислы (SiO2, Al2O3 и др.), образуемые в процессе окисления, в металле не растворяются, за исключением оксида марганца MnO, который в отличие от других окислов обладает значительной растворимостью. Поэтому для удаления оксида марганца из металла в шлак последний необходимо обновлять. Следует заметить при этом, что обновление шлака способствует также и очищению ванны от других примесей, что в свою очередь способствует получению качественного металла.
Второй метод раскисления заключается в добавлении углерода в шлак. Этот способ нашел практическое применение в основных печах. Получаемый в процессе окисления оксид углерода газообразный. Образуясь на поверхности ванны, он легко может удаляться. В этом положительная сторона метода. Недостаток его заключается в необходимости длительное время выдерживать ванну под восстановительным шлаком. Это связано со значительным увеличением расхода энергии.
Третий метод раскисления заключается в обработке металла жидким шлаком. При этом способе жидкие, свободные от FeO шлаки, находясь в металле в состоянии эмульсии, поглощают оксиды и освобождают ванну от кислородсодержащих веществ, а также в значительной мере и от газов. Практически раскисление по этому методу проводится следующим образом: расплавленный шлак помещают на дно глубокого ковша, после чего с большой высоты ковш заполняют металлом. При этом металл, попадая в жидкий шлак, проходит через него, и за счет эмульсирования шлака значительно увеличивается площадь соприкосновения металла с жидким шлаком. Обладая значительной жидкопод- вижностью, частицы шлака будут отделяться от металла и всплывать на его поверхность, увеличивая этим соприкосновение части шлака с металлом. Благодаря активному смешиванию и значительному увеличению за счет этого поверхности соприкосновения шлака с металлом реакция раскисления во всей массе жидкого металла будет происходить с исключительно большой скоростью.
Этот способ заслуживает большего внимания, чем ему уделялось до сих пор. Технический успех его бесспорен, и он должен получить в ближайшие годы значительное распространение.
Ниже приводятся данные, характеризующие зависимость времени плавки стали и расхода электроэнергии от емкости печи и мощности генератора (табл. 7.1) [24].
Таблица 7.1
Зависимость времени расплавления стали и расхода электроэнергии от емкости печи
и мощности генератора
Емкость печи, кг | Мощность генератора, кВт | Время расплавления, мин | Расход электроэнергии, кВт-ч/кг |
10 | 30-60 | 20-15 | 1,5-2,0 |
50 | 60-100 | 40-30 | 0,5-1,0 |
250 | 150-250 | 70-50 | 0,7-0,8 |
500 | 250-500 | 70-50 | 0,6-0,8 |
1000 | 500-600 | 80-60 | 0,6-0,7 |
Данные табл. 7.1 показывают, что чем больше мощность генератора и тем самым выше емкость печи, тем больше производительность печи и меньше расход электроэнергии на единицу выплавляемого металла.
5. Разливка стали
Завершающей и весьма ответственной операцией процесса приготовления стали является разливка.
Разливка стали из печей малой емкости в формы обычно производится непосредственно, без применения разливочных ковшей. На больших печах всегда разливают сталь через разливочные ковши, прогретые до температуры выше 850 °С. При этом следует особо отметить, что качество стального слитка и фасонной отсеки зависит от многих факторов. Важнейшие из них следующие:
- температура металла перед разливкой;
- скорость литья;
- состояние разливочных ковшей;
- методика разливки в формы/изложницы.
Высокая температура литья значительно влияет на качество слитка, так как способствует неоднородности химического состава литья (ликвации), образованию крупнокристаллической столбчатой структуры слитка, усадочных раковин, осевой рыхлости слитка, трещин, пористости и т. п.
Низкая температура разливки также отрицательно сказывается на качестве литья и вызывает загрязненность слитка неметаллическими включениями, появление неслитин, заворотов и т. п. Скорость разливки стали зависит от химического состава и массы металла, а также от способа и сложности литья.
Качество отливки зависит от состояния футеровки ковша, температуры его прогрева и состояния стопора. Однако решающее значение для качества отливки имеет способ разливки металла. Для разливки слитков применяют два метода: разливка сверху и разливка снизу (сифонный метод). Последний метод на отечественных заводах при разливке качественных сталей преобладает (более 80%) [24].
6. Технико-экономические показатели работы тигельной печи
Индукционная тигельная печь является экономичной плавильной установкой периодического действия. Расход огнеупорных материалов на тонну выплавленной стали в этих печах является минимальным. Печь с производительностью I т/ч имеет футеровку толщиной не более 100 мм, общий вес огнеупорных материалов составляет около 160 кг. Футеровка дуговой печи той же производительности весит около 7 т. В связи с этим удельный расход энергии на холодной индукционной печи незначительно отличается от расхода энергии на плавку в разогретой печи (табл. 7.2) [25].
Таблица 7.2
Удельный расход энергии
Номер плавки | Продолжительность плавки, мин | Расход электроэнергии, кВт-ч/т |
1 | 85 | 690 |
2 | 75 | 610 |
3 | 65 | 580 |
Для улучшения технико-экономических показателей необходимо следующее [25]:
- установить достаточно мощный генератор;
- конденсаторы располагать близко к печи, так как в цепи конденсаторы — печь протекает ток большой силы;
- увеличить стойкость тигля и уменьшить прослои на ремонтах;
- ставить на один генератор два индуктора;
- подбирать шихту по габаритности и соблюдать правила укладки;
- вести плавку с закрытым сводом;
- покрывать металл шлаком как можно раньше;
- не допускать образования «мостов» во время плавления;
- вести плавку с минимальным количеством проб путем подбора, точного взвешивания и расчета шихты;
- контролировать температуру охлаждающей воды, избегая ненужного расхода;
- ускорять загрузку печи.
Весьма важным показателем работы печи является расход энергии. Мощность, подводимая в индукционную печь средней частоты, при выплавке углеродистой стали распределяется следующим образом, %, на:
- потери:
а) в преобразователе 12-18;
б) конденсаторах и токоподводе 5-6;
в) индукторе 11-16;
г) излучением 8—10;
д) нагрев металла и шлака 52—62.
При общем коэффициенте полезного действия установки, равном 0,57, расход энергии составит около 630 кВт ч на тонну выплавленного металла. Этот расход лишь на 10—30 кВт-ч выше расхода энергии в 3-тонной дуговой печи с кислой футеровкой. Следует учесть более низкий угар легирующих элементов в индукционной печи, отсутствие расхода на электроды, меньшие затраты на рабочую силу.