Современные способы производства слитков особо высокого качества
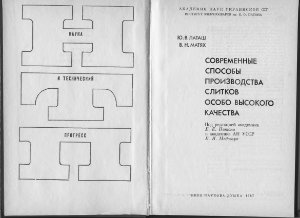
Латаш Ю.В., Матях В.Н.
Киев, Наукова думка, 1987 г.
4. Металлургические особенности, качество и сортамент металла
Рафинирование металла при ЭЛП основано, как и при ВДП, на капельном наплавлении слитка в условиях вакуумирования плавильного пространства печи. Вместе с тем взаимодействие металла с разреженной газовой фазой в условиях ЭЛП отличается по ряду термодинамических и кинетических показателей.
Остаточное давление газов в камере электронно-лучевой печи поддерживается обычно в пределах 1,3 · 10-6 — 1.3 · 10-4 Па. Уровень металлической ванны в ходе ЭЛП сохраняет неизменное положение вблизи верхнего среза кристаллизатора, а расходуемая заготовка, подаваемая сверху либо сбоку, не препятствует удалению выделяющихся из расплава газов и паров. Поэтому указанный диапазон остаточного давления газов характеризует разреженность газопаровой фазы, контактирующей с расплавом металла, которая на 2—4 порядка ниже, чем при ВДП (см. параграф 5 главы 3).
Высокая концентрация энергии электронного луча позволяет обеспечить существенный перегрев поверхности металлической ванны, хотя в реальных плавках температура последней обычно не достигает максимальных значений, характерных для данного металла или сплава (см. табл. 65), но превышает этот показатель для условий ВДП примерно на 100—150 °С.
Независимый источник теплоты при ЭЛП дает возможность в широких пределах регулировать скорость наплавления слитка и, соответственно, продолжительность пребывания металла в жидком состоянии. Понятно, что уменьшение производительности переплава приведет к более длительной выдержке расплава в условиях высоких вакуума и температуры и обязательно скажется на изменении его химического состава.
Наконец, необходимо упомянуть об отличии указанных процессов еще в одном аспекте. Как известно, при переплавах расходуемого электрода или заготовки металл подвергается рафинированию на трех этапах существования его в жидком состоянии: в пленке на оплавляющемся торце, в каплях и на поверхности металлической ванны. При сопоставимых условиях (производительность, диаметр применяемого кристаллизатора) площадь межфазной поверхности газ — металл на двух последних этапах соответственно одинакова для обоих методов переплава. Площади оплавляющегося торца электрода и заготовки при этом могут отличаться в несколько раз. Так, в ходе ВДП торец расходуемого электрода обычно плоский и, следовательно, площадь этой поверхности примерно равна поперечному сечению электрода. При ЭЛП с вертикальной подачей заготовки ее оплавляющийся конец приобретает коническую форму (с углом при вершине от 30 до 60°), а площадь этой поверхности в 2—4 раза превышает площадь поперечного сечения. Заготовка, подаваемая при ЭЛП сбоку имеет плоский торец как и при ВДП. Однако поверхность оплавления расположена вертикально, расплавленный металл перемещается по ней вниз и толщина пленки расплава меньше, чем на плоском горизонтальном торце электрода ВДП. Поэтому полагают [168, 428], что условия рафинирования металла на первом этапе при ЭЛП всегда лучше, чем при ВДП, а наиболее благоприятные — при вертикальной подаче расходуемой заготовки и конической форме поверхности оплавления.
Обобщенно перечисленные отличия можно выразить так: при ЭЛП расплав продолжительнее подвергается воздействию более глубокого вакуума и высокой температуры.
Рафинирующий эффект при вакуумировании расплава обеспечивается за счет дегазации и дистилляции последнего. Принципиальные особенности этих процессов описаны в параграфе 4 первой главы, а применительно к условиям ВДП — в параграфе 5 третьей главы. В данном разделе покажем, в какой мере изменившиеся, в сравнении с ВДП, условия взаимодействия переплавляемого металла с разреженной газовой фазой сказываются на результатах его рафинирования.
Во-первых, понижение давления способствует сдвигу равновесия химических реакций в сторону образования большего числа молей газообразных продуктов. Поэтому большая глубина откачки плавильного пространства печи ЭЛП создает благоприятные термодинамические условия протекания реакций дегазации расплава по механизму экстракции газов, БУР и диссоциации НВ.
Во-вторых, разрежение газопаровой фазы над расплавом улучшает кинетические условия процессов дегазации и дистилляции поскольку при этом увеличивается длина свободного пробега атомов и молекул. При давлении ниже 1,3 · 10-4 Па (10-2 мм рт. ст.) вязкостный режим течения продуктов через газопаровую фазу к месту конденсации или в вакуумную магистраль сменяется молекулярным и эта стадия более не лимитирует в целом скорость указанных процессов.
Повышение температуры расплава металла в общем благоприятно сказывается на условиях его рафинирования. При этом становится более отрицательным изменение свободной энергии реакции углеродного раскисления, диссоциации оксидов, увеличивается упругость паров компонентов расплава. В качестве негативного изменение этого термодинамического фактора можно рассматривать лишь в отношении дегазации железа, никеля и некоторых сплавов на их основе, поскольку растворимость водорода и азота в них увеличивается с повышением температуры (см. (1.5), (1-6)). Однако отрицательное влияние повышения температуры неощутимо сказывается на результатах рафинирования, поскольку с избытком компенсируется уменьшением давления.
Наряду с улучшением термодинамических показателей, повышение температуры влияет на кинетику реакций удаления примесей из расплава. Здесь, однако, уместно выделить два основных момента.
В тех случаях, когда скорость какого-либо гетерогенного процесса лимитируется массопереносом в тонком непромешиваемом слое вблизи межфазных границ, ускорить переход примеси можно увеличением коэффициента диффузии примеси, уменьшением толщины этого слоя или увеличением приведенной поверхности реагирования (см. (1.36)). Если процесс протекает в кинетическом режиме, то интенсифицировать его можно лишь воздействием на акт химического или физического превращения. Поскольку энергия активации диффузии в жидких металлах (40—80 кДж/моль) значительно меньше энергии активации образования молекул веществ (300—500 кДж/ моль), возрастание температуры расплава существенно влияет в основном на интенсификацию процессов, протекающих в кинетическом режиме. К последним в интересующей нас области пирометаллургических процессов можно причислить лишь испарение некоторых элементов, в частности железа, хрома, никеля, титана, ниобия, алюминия, кремния, вольфрама, молибдена из сплавов на основе железа и никеля [168, 293, 428], а также удаление азота после достижения критических концентраций (см. параграф 5 главы 3). Подавляющее большинство гетерогенных физико-химических процессов, имеющих большое практическое значение с точки зрения рафинирования металлов и сплавов, осуществляется в диффузионном режиме, а их скорость лимитируется доставкой реагентов к межфазной границе.
Поэтому основным достоинством ЭЛП в металлургическом отношении, кроме отмеченного позитивного влияния повышения температуры поверхности расплава и более высокой степени разрежения газопаровой фазы, следует считать возможность регулирования продолжительности пребывания металла в жидком состоянии. При этом большое значение для повышения чистоты переплавляемого металла имеет первый этап пребывания его в жидком состоянии.
Перегрев металла над температурой ликвидуса в пленке на оплавляющейся поверхности электрода и заготовки примерно одинаков и обычно не превышает нескольких десятков градусов. Однако развитая межфазная поверхность, площадь которой при ЭЛП может быть даже в несколько раз больше площади зеркала металлической ванны в кристаллизаторе, и малая толщина слоя расплавленного металла являются теми факторами, которые способствуют интенсификации процессов, протекающих в диффузионном режиме.
Важную роль первого этапа подтверждают экспериментальные .данные: рафинирование тугоплавких металлов от кислорода происходит в основном на стадии течения пленки [4151; при ЭЛП легированных сталей и хромоникелевых сплавов на торце заготовки удаляется на 70—80 % примесей цветных металлов, 40—50 % азота и меди [203, 242, 258].
Кроме большой приведенной поверхности реагирования фаз эффективное очищение металла на стадии пленочного течения обусловливается более высокими концентрациями вредных примесей и, соответственно, более высокой скоростью относительного их изменения. По мере приближения показателей загрязненности к какому-либо термодинамически обусловленному уровню добиться дальнейшего повышения чистоты металла значительно сложнее. Поэтому полагают [168]а что наиболее эффективными способами и конструкциями печей ЭЛП являются те, в которых в наибольшей мере используются преимущества рафинирования на стадии оплавления заготовки.
Роль третьего этапа рафинирования при ЭЛП менее значительна. Несмотря на то что поверхность расплава в кристаллизаторе имеет наибольший перегрев, а продолжительность пребывания металла в жидком состоянии достаточно велика, приведенные поверхности реагирования фаз в этой зоне и на оплавляющейся заготовке примерно одинаковы. Как отмечалось, повышение температуры не очень существенно сказывается на скорости физико-химических процессов, протекающих в диффузионном режиме. Поэтому реакции дегазации расплава и испарения многих вредных примесей осуществляются в кристаллизаторе с теми же скоростями, что и на первом этапе рафинирования [168, 428]. Усилить рафинирующий эффект можно лишь уменьшением производительности переплава, т. е. увеличением продолжительности выдержки расплава в кристаллизаторе. Практические результаты подтверждают этот вывод: чистота переплавленного металла действительно повышается с уменьшением скорости плавления заготовки и, соответственно, с повышением удельных затрат электроэнергии.
Однако такой путь достижения высоких металлургических показателей приводит и к негативным последствиям. Изменившиеся условия межфазного взаимодействия на поверхности металлической ванны интенсифицируют процессы, скорость которых ограничена химической стадией реакции. Как отмечалось, к таким процессам при ЭЛП относится в основном испарение. Поскольку подавляющее большинство элементов, испаряющихся в кинетическом режиме, является либо основой сплавов, либо легирующими компонентами, перегрев и длительная выдержка расплава наряду с удалением вредных примесей приводят к потерям металла (основы и легирующих элементов). Зависимость этих потерь от мощности электронно-лучевой пушки и удельных затрат электроэнергии практически линейная в широком диапазоне изменения этих параметров ЭЛП [168, 428, 491].
Выше перечислены основные отличия условий взаимодействия жидкого металла с разреженной газовой фазой при ВДП и ЭЛП и в общем показано, в какой мере эти изменения влияют на ход главных физико-химических процессов, обусловливающих рафинирование расплава при его вакуумировании. Охарактеризуем теперь подробнее особенности дистилляции и дегазации переплавляемого металла в условиях ЭЛП.
Высокие вакуум и температура, развитая реакционная поверхность и регулируемое время выдержки расплава обеспечивают большие возможности ЭЛП в деле очищения металлов от вредных цветных примесей. Испарение свинца, висмута, сурьмы, меди, олова, теллура, таллия, присутствующих в виде следов в сплавах на основе никеля, хрома, железа и с трудом удаляемых при ВДП, при ЭЛП происходит с наибольшей степенью полноты. Снижение концентрации этих элементов при однократном переплаве составляет в среднем не менее 60 % исходного содержания (табл. 68).
В соответствии с описанными термодинамическими и кинетическими закономерностями испарения показатели чистоты металла оказываются взаимосвязанными с режимом переплава и в общем улучшаются с увеличением температуры и продолжительности вакуумирования (рис. 110). Поскольку интенсивность испарения свинца и висмута ограничена скоростью их диффузии в пограничном слое металла, влияние изменения производительности ЭЛП на скорость их удаления оказывается существеннее, чем мощность облучения. Испарение меди и сурьмы, осуществляемое в переходном между диффузионным и кинетическим режиме, в большей мере зависит от температурного фактора. Также подвержена влиянию термодинамических и кинетических факторов интенсивность испарения других элементов.
О дистилляционных возможностях ЭЛП и влиянии режима переплава на интенсивность испарения какого-либо элемента можно судить по сопоставлению теоретических (1.39) констант скорости испарения с экспериментально полученными значениями коэффициента массопередачи [168, 592, 612]. Результаты такого сопоставления, например, для ЭЛП сплавов на основе железа приведены на рис. 111. Правая часть рисунка соответствует температурным условиям на стадии плавления заготовки (низкотемпературная зона рафинирования), левая — условиям на поверхности ванны (высокотемпературная зона). В данном случае в диффузионном режиме испаряются лишь свинец, марганец, медь и олово, причем лимитирующая роль диффузии усиливается на стадии ванны. Испарение большинства элементов ограничено скоростью десорбции. На поверхности оплавляемой заготовки испарение почти не имеет места, но интенсифицируется в высокотемпературной зоне. Константы испарения кремния, молибдена, ниобия, вольфрама располагаются ниже линии ванадия, т. е. эти элементы практически не испаряются из сплавов на основе железа.
Для сплавов на основе других металлов относительное положение соответствующих линий изменится, поскольку изменяется активность элементов в расплаве и, следовательно, движущая сила испарения. Тем не менее такое сопоставление позволяет сделать вывод о дистилляционных возможностях ЭЛП. Принципы сравнения при этом таковы: удаление элемента, константы скорости испарения которого меньше, обязательно сопровождается более интенсивным испарением компонентов, обладающих повышенными скоростями десорбции; удаление примесей, испарение которых ограничено процессом диффузии, можно усилить технологическими мероприятиями на первом этапе, а для интенсификации рафинирования расплава от элементов, испаряющихся в кинетическом режиме, полезны лишь снижение скорости переплава и повышение температуры ванны.
Испарение серы, очень вяло происходящее на первом этапе рафинирования, интенсифицируется с поверхности расплава в кристаллизаторе. Однако хром и железо имеют близкие к сере константы скорости испарения, а потенциальные возможности десорбции марганца значительно выше. Поэтому использование ЭЛП с целью десульфурации стали обязательно приведет к потерям легирующих элементов.
При оптимальных скоростях ЭЛП относительное снижение концентрации серы в низкоуглеродистых сталях и никельхромовых сплавах составляет 5—10 %, но увеличивается до 20—30 % с повышением содержания в сталях углерода и кремния, а также исходного содержания самой серы [31]. Рафинирование расплава от фосфора ограничено еще более низкими значениями констант скорости испарения. В зависимости от типа сплава ЭЛЛ может сопровождаться либо незначительным снижением концентрации фосфора, либо даже некоторым повышением его содержания в слитке, обусловленным потерями основы сплава и легирующих элементов. Однако в обоих случаях эти изменения не имеют практического значения в аспекте рафинирования. Поэтому полагают, что метод ЭЛП не предназначен для проведения десульфурации и дефосфорации, а требуемое низкое содержание серый фосфора в слитке, как и для ВДП, должно быть обеспечено еще на этапе выплавки металла для расходуемой заготовки.
Испарение легирующих элементов и основы сплава, сопровождающее его дистилляцию от вредных примесей,—негативная сторона рафинирования при ЭЛП. Хотя с этими нежелательными изменениями химического состава приходится мириться,, максимальные потери сплава на испарение ограничивают обычно величиной 3—5 %. Конденсат на кристаллизаторе и стенках камеры печи ЭЛП при переплаве сталей состоит преимущественно из марганца, хрома и железа.
В связи с интенсивным испарением марганца полагают [444] , что ЭЛП сталей, содержащих этот элемент в количестве более 0,4 % t нельзя признать целесообразным.
Потери легирующих элементов и испарение железа обусловливают одновременное относительное обогащение состава стали тугоплавкими компонентами и элементами с низкой упругостью пара (вольфрам, молибден, кремний, никель).
Понятно, что при заданном конечном составе стали содержание легирующих элементов в исходном материале должно быть соответствующим образом скорректировано. Большую помощь в деле получения сталей и сплавов прецизионного состава оказывают расчетные методы прогнозирования и оптимизации параметров процесса ЭЛП, в разработку которых существенный вклад внесли ученые ИЭС им. Е. О. Патона АН УССР [428].
Возможности дегазации металлов и сплавов при ЭЛП, как и рафинирования их от вредных примесей цветных металлов, также очень высоки. Удаление водорода из переплавляемых материалов не представляет проблем. Его остаточные концентрации независимо от исходного содержания обычно весьма малы и близки к значениям, термодинамически обусловленным для данного металла или сплава в конкретных режимах переплава.
Достигнуть низких содержаний азота в переплавленном металле сложнее. Очищение расплава от этого диффузионно менее подвиж-
ного элемента ограничено кинетическими особенностями процесса деазотации и оказывается зависимым от режимов ЭЛП. Общие закономерности удаления азота были описаны в параграфе 5 третьей главы. При переплавах с использованием расходуемого электрода или заготовки содержание азота как исходное, так и в переплавленном металле обычно не достигает тех минимальных значений, при которых режим деазотации переходит в кинетический. Поэтому на показатели рафинирования металла от азота большое влияние оказывают мероприятия, интенсифицирующие диффузионный этап мас- сообмена (увеличение приведенной поверхности реагирования).
На полноту удаления азота при вакуумных процессах переплава положительно влияют уменьшение производительности и повышение мощности. Поскольку ЭЛП присущи большие возможности регулирования продолжительности пребывания металла в жидком состоянии, а также более благоприятные кинетические условия массо- обмена на поверхности оплавляемой заготовки, при ЭЛП достигаются пониженные в сравнении с ВДП конечные концентрации азота в переплавленном металле (табл. 69). Причем некоторые исследователи полагают, что в случае ВДП первый этап рафинирования (заготовка) имеет второстепенное значение и азот выделяется преимущественно с поверхности ванны, а при ЭЛП на стадии заготовки удаляется примерно треть всего количества экстрагированного азота [168, 257].
Рафинирование металла от кислорода осуществляется при ЭЛП в общем по тем же механизмам, что и в ранее описанных методах производства высококачественных слитков. Сравнительно высокие вакуум и температура благоприятствуют диссоциации исходных неметаллических включений, восстановлению их углеродом, десорбции растворепного в расплаве кислорода в газопаровую фазу, в том числе и за счет ВУР, выделению не успевших диссоциировать НВ на поверхность металла и их последующей коагуляции с обособлением шлаковой фазы (параграфы 2, 3, 5 первой главы и параграф 5 третьей главы).
Термодинамические расчеты и результаты экспериментов показывают, что доля участия каждого из перечисленных процессов в повышении чистоты металла по оксидным НВ может быть различной и зависит от химического состава переплавляемого материала и режимов ЭЛП. Так, например, растворение гомогенных оксидных фаз кремния, марганца, алюминия, лимитируемое диффузией кислорода в жидком металле, происходит достаточно быстро и может иметь место уже на оплавляемом торце заготовки. Диссоциация термодинамически более устойчивых комплексных оксидов (типа алюминатов кальция) менее вероятна. Поэтому очищение комплексно-раскисленного переплавляемого металла или металла, имеющего сложный химический состав, в большей мере происходит путем механического выделения НВ на межфазную границу газ — металл как на стадии заготовки, так и из расплава в кристаллизаторе. Десорбция растворенного кислорода, маловероятная при переплаве сталей, интенсифицируется в случае производства чистых металлов,; например
никеля. Однако даже в этих условиях относительное количество удаленного кислорода за счет указанного процесса не превышает 10 % исходного содержания.