Сборник задач по технологии горячей и холодной прокатки стали и сплавов
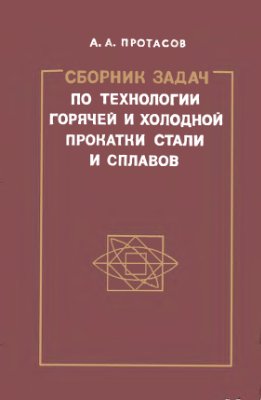
Протасов А.А.
Металлургия, 1972 г.
ОХЛАЖДЕНИЕ СТАЛИ
ОБЩИЕ СВЕДЕНИЯ
Режим охлаждения стали за период прокатки слитков или заготовок до конечного профиля и после прокатки годных изделий является одной из основных составных частей технологии прокатного производства.
Знание истинной температуры металла после каждого прохода имеет существенное значение для определения силовых уcловий процесса и проектирования средств и режимов охлаждения металла.
Теплотехнические инженерные расчеты производят по формулам, включающим значительное число допущений, поэтому результаты аналитических расчетов не всегда совпадают с практическими данными, полученными с помощью современной измерительной техники.
Например, давление металла на валок Ρ определяют методами, изложенными в работе А. Е. Гуревича и Е. С. Рокотяна [82], а температуру конца прокатки фиксируют с помощью саморегистрирующего прибора ФЭП (фотоэлектрический пирометр).
При выборе средств и режимов охлаждения прокатных изделий необходимо руководствоваться эпюрой распределения температурных напряжений по сечению тела (см. рис. 9 и 14). Однако следует отметить, что распределение напряжений по сечению охлаждаемого тела существенно
отличается от распределения напряжений при нагревании тела.
Если при нагревании тела в первый момент поверхностные слои его (см. рис. 9) подвергаются действию сжимающих напряжений (—), а середина — растягивающих (+), то при охлаждении — наоборот, т. е. поверхностные слои подвергаются действию растягивающих (+), а середина — сжимающих (—) напряжений. При дальнейшем охлаждении усадка наружных слоев металла почти прекращается, причем они становятся холодными и утрачивают пластичность, а середина продолжает еще остывать и сжиматься. Вследствие этого, картина напряжений изменяется: снаружи появляются сжимающие, а внутри растягивающие напряжения.
Схема изменения напряжений при охлаждении стали, по данным Шайля, приведена на рис. 125 [14]. Из нее следует, что при охлаждении стали, особенно высоколегированной малопластичной типа быстрорежущей марки Р19, начальный период охлаждения, когда поверхностные слои тела подвергаются действию растягивающих напряжений, считается опасным. В подобных сталях в этот период возникают поверхностные закалочные трещины. Для предотвращения их образования необходимо поддерживать минимальную разность температур между температурой поверхностного слоя и температурой окружающей среды. Первый период охлаждения стали является для средних слоев безопасным, так как они подвергаются действию сжимающих напряжений.
Для поверхностных слоев первый период опасен до момента изменения знака напряжений с плюса на минус. С этого момента охлаждения начинается второй период охлаждения, когда поверхностные слои сжимаются, а средние растягиваются. В этот период для стали типа быстрорежущей и хромоалюминиевой создаются условия, способствующие образованию прерывистых внутренних трещин, а в отдельных случаях — кольцевых трещин (рис. 126). В настоящее время критическую точку изменения знаков напряжений для каждой группы сталей определяют эмпирическим
методом, так как определение ее. аналитическим методом представляет значительные трудности.
По данным Ю. М. Чижикова [14] изменение знака напряжений происходит примерно при 300° С. Так, у стали мартенситно-ледебуритного класса опасность образования трещин возникает при температуре, несколько превышающей комнатную, и становится наибольшей после полного охлаждения, когда остаточные напряжения достигают своего максимума.
Закономерности изменения остаточных напряжений рассмотрены в трудах С. И. Губкина [32, 34].
У нелегированных сталей остаточные напряжения могут быть также высокими. Пример действия остаточных напряжений на прокатанные изделия при их охлаждении показан на рис. 127.
Если получающиеся внутренние остаточные напряжения достигают величины, превышающей предел прочности металла, то в нем могут образовываться внутренние микро- и макротрещины, а также трещины, выходящие наружу.
Иногда достаточно незначительного внешнего воздействия, чтобы появились трещины. Такими внешними незначительными воздействиями могут быть: толчок, встряхивание, нанесение царапин, местное изменение температуры, например, при зачистке стали абразивными кругами и др. Неоднородность металла, микропоры, газовые пузыри, неметаллические включения, крупные скопления карбидов также могут быть причиной появления поверхностных и внутренних трещин.
Известно, что нарушение сплошности тела является следствием действия растягивающих напряжений. Поэтому для уменьшения действия растягивающих напряжений при охлаждении стали рекомендуется изделия после прокатки охлаждать медленно до выравнивания температур поверхности и середины тела. Медленное охлаждение стали способствует также уменьшению структурных напряжений.
В ряде случаев, перечисленных ниже, прибегают к охлаждению металла в воде.
I. Когда предъявляются высокие требования к чистоте поверхности по окалине. Например, сутуночные полосы после выхода из стана при последнем проходе поступают в бассейн с водой. Таким способом охлаждают стали, в которых при любой скорости охлаждения не образуются никакие дефекты.
2. Когда необходимо получить сталь без цементитной (карбидной) сетки, например, ШХ15, У9—У12 и т. д. В этом случае металл охлаждают в воде до потемнения. После этого осуществляют самоотпуск.
В воде охлаждают преимущественно такие стали, которые даже при самой большой скорости охлаждения не склонны к образованию трещин и флокенов.
3. Когда требуется получить сталь с достаточно равномерной структурой, например листы из низкоуглеродистой стали, предназначенные для глубокой штамповки. При охлаждении листов в воде не выпадает свободный цементит и исключается образование неравномерной структуры. Если полосы сматывают в рулоны, то быстрое охлаждение производят до 700° С.
Особо чувствительные к термическим и другим напряжениям стали, например, быстрорежущая, после прокатки медленно охлаждают и затем не позже чем через сутки после охлаждения подвергают термической обработке (изотермическому отжигу). Только в этих случаях быстрорежущая сталь теряет склонность к трещинообразоваиию.
Все виды брака (закалочные трещины, внутренние концентрические или поперечные трещины, флокены, карбидная сетка) и причины их образования при охлаждении стали достаточно подробно рассмотрены в работе Ю. М. Чижикова [14].
В целях предупреждения образования всех видов брака при охлаждении стали применяют следующие способы охлаждения: 1) в малотеплопроводящих материалах (кизельгур, доменный шлак, песок, шлаковая вата, каменноугольная зола, мелкий гравий); 2) в термостатах; 3) в неотапливаемых колодцах; 4) в подогреваемых колодцах и печах; 5) в отапливаемых печах и колодцах; 6) в воде.
Большинство углеродистых и легированных сталей охлаждают непосредственно на воздухе. Охлаждение происходит на стеллажах, где изделия лежат в один ряд, или в пакетах и штабелях. Остывание стали на стеллажах идет значительно интенсивнее, чем в пакетах и штабелях.
При выборе режимов и средств охлаждения стали после прокатки необходимо знать следующие основные данные:
1) склонность стали к образованию флокенов, закалочных поверхностных и кольцевых внутренних трещин [14]
2) температуру конца прокатки стали;
3) критические точки фазовых превращений [83
4) физико-механические свойства металла при температурах конца прокатки [13], [12];
5) остаточные напряжения в металле после прокатки. Основные графики охлаждения стали после прокатки, используемые на производстве, представлены на рис. 128.