Режимы резания металлов
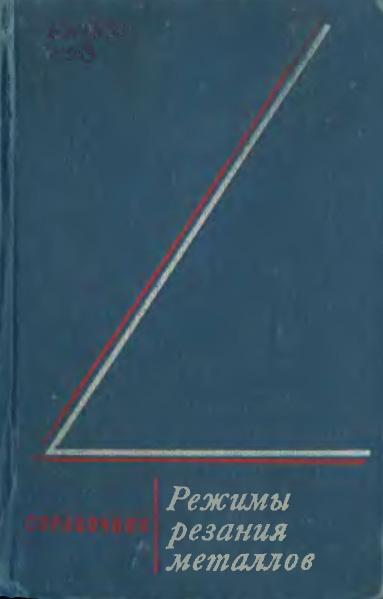
Под ред. Барановского.
Машиностроение, 1972 г.
Нормативы состоят из девяти разделов , каждый из которых включает указания по расчету и карты рекомендуемых режимов резания (подача, стойкость, скорость резания, мощность резания и др.) для наиболее распространенных в автомобилестроении операций.
I. Обработка на токарных станках.
II. Обработка на токарных одно- и многошпиндельных прутковых автоматах.
III. Фрезерование на одно- и многошпиндельных станках.
IV. Обработка на одношпиндельных сверлильных станках, а также на станках, имеющих одну или несколько многошпиндельных головок.
V. Протягивание отверстий и наружных поверхностей на горизонтально- и вертикально-протяжных станках.
VI. Зубообработка цилиндрических и конических зубчатых колес и шлицевых валов.
VII. Нарезание резьбы метчиками, резьбонарезными головками, фрезами и накатывание резьбы круглыми роликами и плоскими плашками.
VIII. Шлифование и абразивно-алмазная обработка, включая круглое врезное шлифование в центрах, бесцентровое шлифованиеметодом продольной подачи и врезания, внутреннее шлифование, плоское шлифование на станках с круглым столом, шлицешлифование, хоннигование и суперфиниширование.
IX. Чистовая Обработкаповерхностным пластическим деформированием.
Карты режимов резания являются едиными для одно- и многоинструментных работ, а указания для них1 даны раздельно, при этом для каждого вида работ, где применяется многоинструментная обработка, приводится несколько инструкций, расположенных в порядке усложнения наладок. Так, например, для токарных станков даны инструкции го одноинструментной и мпогоинструментной обработке на одношпиндельных станках, многоинструментной обработке на многошпиндельных полуавтоматах.
Кроме этих основных материалов, имеется 6 приложении, в которых приведены коэффициенты обрабатываемости сталей, рекомендации по обработке магниевых сплавов, металлокерамики и некоторые другие дополнительные данные по режимам резания (приложение I); рекомендации по выбору твердых сплавов и абразивных кругов, ряда параметров при зубообработке, протягивании и другие технологические рекомендации (приложение 2); некоторые справочные материалы, полезные технологу при назначении им режимов резания, такие как маркировки сталей, соотношение чисел твердости и др. (приложение 3); основные зависимости, принятые при составлении рекомендаций по скоростям резания (приложение 4); данные по применению ЭВМ для расчета режимов резания (приложение 5); примеры расчета режимов резания (приложение 6).
При обобщении и анализе данных производственной практики, помимо установления уровня режимов резания, выявилась также необходимость изменения некоторых принципиальных и методических положений по расчету режимов, являющихся основой нормативных материалов, выпущенных рядом организаций и отдельными авторами. Особенности нормативов кратко можно свести к следующему:
1. Принята не степенная зависимость стойкостиинструментов от скорости резания.
2. Значительное влияние жесткостисистемы станок—деталь—инструмент на подачу, которое, однако, не поддается количественному определению, и отсутствие данных о динамической жесткостистанков не позволили рекомендовать однозначные решения при назначении подач на токарных и фрезерных станках. В нормативах даны указания о назначении в этих случаях больших подач при жестких станках, деталях и оснастке. Однако эти указания носят качественный характер и приводят в известной мере к субъективным решениям при выборе в диапазоне рекомендуемых подач.
3. Одной из основных задач расчета режимов резания многоинструментных наладок является установление стойкостиинструментов многоинструментной наладки, обеспечивающих экономически рентабельный режим работы.