Ресурс пластичности металлов при обработке давлением
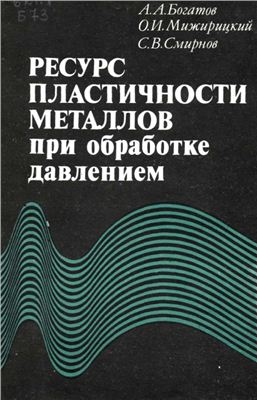
Богатов А.А.
Металлургия, 1984 г.
АППАРАТУРА ДЛЯ ИССЛЕДОВАНИЯ МЕХАНИЧЕСКИХ СВОЙСТВ ПОД ВЫСОКИМ ДАВЛЕНИЕМ
В последнее время стало очевидным, что изучение механических свойств в условиях, характерных для процессов ОМД, возможно только при использовании установок высокого давления. Значительный прогресс в создании аппаратуры высокого давления и методик изучения механических свойств был достигнут благодаря работам П.Бриджмена.
В СССР крупные работы в области создания установок высокого давления и исследования физико-механических свойств металлов были проведены под руководством Л.Ф.Верещагина и Б.И.Береснева [21]. Новые установки были созданы Х.Пью [50], Г .Д.Ушаковым [72], Ю.Г.Важен-цевым [73], В.И.Зайцевым [74] и др. Несколько конструкций универсальных испытательных машин с камерой высокого давления разработано авторами книги1 [46,75], на две из которых получены авторские свидетельства СССР.
Установки высокого давления для изучения механических свойств материалов различают по способам создания давления в испытательной камере и по конструкции устройств, предназначенных для осуществления нагружения. По первому признаку выделяют две группы установок.
К первой относятся установки с вынесенным независимым источником высокого давления (мультипликаторы, компрессоры, а при давлении до 200 МПа - насосы). В результате удается упростить конструкцию испытательной камеры и привода механизма для испытания образцов. Но в этом случае оказывается более громоздким и менее надежным блок высокого давления, так как увеличивается количество деталей, трубопроводов и соединений, находящихся под высоким давлением. Такие испытательные машины отличаются малой производительностью.
Ко второй группе относят установки "прямого действия", в которых испытательной камерой является контейнер, а давление создается перемещением плунжера от независимого привода, чаще всего гидроцилиндра. Преимуществами таких машин являются высокие производительность и надежность.
По второму признаку установки различаются конструкцией контейнера высокого давления или испытательной камеры, а также конструкцией привода механизма для нагружения образца. В большинстве испытательных машин применяют подвижные захваты образца, одновременно являющиеся плунжерами контейнера высокого давления. Недостатком такого типа установок является изменение давления в контейнере в процессе испытания образца. Поддерживать давление постоянным можно, используя более сложные конструкции испытательной камеры типа цилиндр—поршень—мультипликатор или цилиндр-поршень—поршень, разработанные Г.Д.Ушаковым [72]. В случае, когда плунжеры контейнера снабжены захватами и соединены с приводами источника высокого давления и механизма для испытания образца, существенно усложняется конструкция приводов и ухудшаются условия обслуживания установки, снижается ее производительность, затрудняется управление процессом испытания образца по заданной программе нагружения, ограничиваются возможности осуществления различных видов испытания образца (растяжение, кручение, осадка, выдавливание мембраны) в одной и той же испытательной камере.
Существенные преимущества имеют установки с испытательной камерой, в которой захваты расположены на нижнем плунжере и на контейнере [74, 75). В этом случае верхний плунжер будет соединен с приводом механизма, обеспечивающего создание давления в испытательной камере, а нижний плунжер и контейнер соединяют с приводами механизма испытания образца. Применение трех независимых приводов позволяет упростить условия эксплуатации установки, резко увеличить ее производительность и конструктивно обеспечить возможность программного нагружения образцов. Испытательные камеры отличаются по конструкции ) уплотнений на плунжерах и конструкции датчиков силы испытания и перемещения захватов образца.
Различают установки и по величине достигаемых параметров: давление и температура испытания. Более подробное описание конструкции установок высокого давления для изучения механических свойств металлов и их классификация приведены в работах [50, 72, 73].
Одной из основных задач совершенствования методик изучения механических свойств с помощью установок высокого давления является разработка стандартных методов испытания и создание стандартной испытательной машины с камерой высокого давления, в которой нагружение образца осуществляется при изменении давления в камере и перемещении захватов образца по заданной программе. Испытательная машина должна иметь микропроцессор для обработки экспериментальной информации и выдачи ее на печатающее устройство. На рис. 7 приведена кинематическая схема испытательной машины, соответствующая этим требованиям. Образец 9 закрепляют в захватах на контейнере 8 и нижнем плунжере 10, которые соединены с приводом перемещения контейнера 1 в осевом направлении образца и приводом вращения плунжера 11. Давление в контейнере создают перемещением верхнего плунжера 7 от гидроцилиндра 6 с гидронасосом 4.
Изменение давления в контейнере и перемещение захватов образца в соответствии с программой нагружения осуществляется с помощью числового программного устройства 17, управляющего работой реле давления 3 и приводов движения контейнера и нижнего плунжера 1 и 11. «Приводы могут быть электромеханические от двигателей постоянного тока 2, 16 с питанием от тиристоров 12, 14, как это изображено на схеме, или от гидродвигателей-гидронасосов (универсальных гидравлических регуляторов скорости). Гидроцилиндр 6 и приводы механизмов 1,.Поснащены датчиками состояния системы нагружения: датчиком давления 5 и тахогенераторами 13 и 15, с помощью которых осуществляется обратная связь с числовым программным устройством.
Испытательная машина оснащена специальными датчиками для измерения давления в испытательной камере 8, а также силовых и кинематических параметров нагружения образца в окружном и осевом напавлениях. Сигналы от датчиков поступают на систему аналог-код 19 и микропроцессор 18 для расчета и выдачи на печать параметров напряженного и деформированного состояний образца при испытании с последующей статистической обработкой экспериментальных данных для определения кривых упрочнения и диаграмм пластичности металла.