Раскисление и вакуумная обработка стали
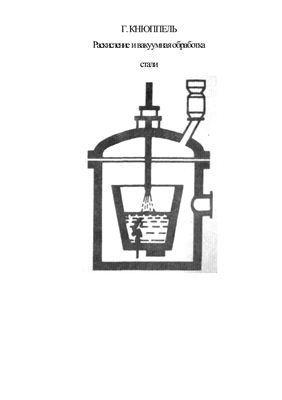
Кнюппель Г.
Металлургия, 1984 г.
Задачи вторичной металлургии можно сформулировать следующим образом.
1. Повышение чистоты стали по оксидным включениям за счет глубокого понижения концентрации растворенного в стали кислорода при раскислении углеродом под вакуумом; связывания растворенного кислорода при взаимодействии с равномерно распределенными в объеме металла раскислителями, при этом их надо вводить в такой последовательности, чтобы образовывались продукты раскисления, которые хорошо удаляются, а если они остаются в стали, то по возможности менее отрицательно влияют на свойства металла; облегчения коагуляции и удаления оксидов созданием интенсивных турбулентных потоков в расплаве.
2. Снижение содержания в стали водорода до пределов, "делающих сталь нефлокеночувствительной; это достигается путем вакуумирования с использованием мероприятий, способствующих усилению массообмена между металлом и газовой фазой.
3. Производство стали с очень низким содержанием углерода. Такая технология основывается на окислении углерода под вакуумом как без дополнительного подвода кислорода, так и с дополнительной продувкой металла кислородом. Этому же способствует продувка при атмосферном давлении расплавленной стали в конвертере смесями аргона и кислорода или водяного пара и кислорода,
4. Производство стали с суженными границами содержания элементов для стандартизации свойств стали различных плавок, а также для экономии легирующих элементов и раскислителей. Это становится возможным при присадке легирующих элементов и раскислителей во взвешенный после выпуска металл и тщательном его перемешивании; наиболее целесообразно присадку проводить в конце вакуумной обработки и под вакуумом, чтобы существенно уменьшить угар элементов.
5. Достижение однородности металла по температуре во всем объеме ковша за счет хорошего перемешивания.
6. Дополнительный подогрев металла для компенсации тепловых потерь за время внепечной обработки за счет электродугового подогрева, осуществляемого при пониженном или атмосферном давлении.
7. Достижение низких концентраций серы в стали. Это осуществляется вдуванием в металл в ковше карбида кальция, силикокальция или сплава магний-кальций, вдувания шлакообразующих смесей на основе извести при предварительном наведении покровного шлака; хороший эффект получают в том случае, если активность кислорода в металле и покровном шлаке будет очень низка. Кроме того, низкие содержания серы в стали можно получить, если металл покрыть достаточным количеством известкового шлака с низким содержанием оксидов железа и осуществить интенсивное перемешивание этих двух фаз.
8. Повышение производительности сталеплавильных агрегатов за счет сведения их функций к расплавлению металла.
9. Согласование производительности и длительности рабочего цикла установок внепечной обработки стали с таковыми показателями плавильных агрегатов за счет использования высокой удельной производительности и гибкости работы установок.
Пока еще не имеется какого-либо одного процесса внепечной обработки, который оказался бы пригодным для решения всех перечисленных, задач и который дал бы высокий экономический результат. Поэтому металлурги должны проанализировать и оценить, какие задачи в конкретных условиях производства стоят по повышению качества стали, какие затраты на повышение качества окупятся, чтобы выбрать подходящий способ внепечной обработки стали. Ниже будут подробно рассмотрены отдельные способы внепечной обработки, независимо от широты их применения, чтобы облегчить возможный выбор подходящих для данного цеха.
Наилучшей предпосылкой возможно более лучшего использования внепечных способов обработки стали являются точные знания металлургических и технических основ процессов и оборудования. Эти знания также необходимы для дальнейшего развития и совершенствования существующих процессов,
Данный способ разработан на заводах объединения "Bochumer Verein", Бохум, ФРГ (ныне эти заводы принадлежат фирме "Krupp Huttenwerke Bochum") [214]. В нем сталь, подлежащая вакуумной обработке, выпускается сперва в первый сталеразливочный ковш, позволяющий производить слив металла через дно. Из первого ковша струя стали перетекает через разреженное пространство во второй сталеразливочный ковш (метод называется "перелив из ковша в ковш") или в изложницу (метод называется "отливка слитков под вакуумом") — рис. 155.
Создание вакуума в вакуумной камере до начала перелива металла достигается тем, что впускное отверстие камеры перекрывается алюминиевым листом толщиной ~2 мм. Поэтому камера может быть уже откачена до начала перелива металла. При этом одновременно гарантируется устранение остатков влаги огнеупорной кладки сталеразливочного ковша или прибыльной надставки изложницы, которая могла бы в других условиях воспрепятствовать быстрому достижению необходимого для вакуумной обработки стали низкого давления. Жидкая сталь при переливе попадает сразу в пространство с предусмотренным низким давлением; поэтому мощность вакуумных насосов расходуется только на дегазацию стали, а не на одновременную откачку вакуумной камеры.