Расчет и конструирование оборудования для внепечной обработки и разливки стали
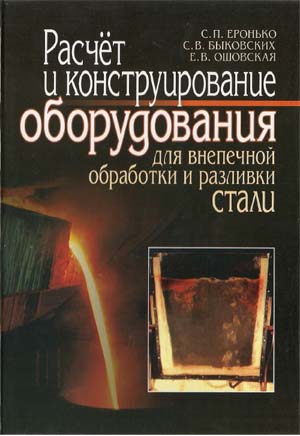
Еронько С.П., Быковских С.В., Ошовская Е.В.
Киев, Техника, 2007 г.
1.1. Краткий анализ современных способов внепечного воздействия на жидкую сталь
Многообразие разработанных и внедренных в производство способов внепечной обработки выплавляемой стали требует внесения изменений в и классификацию.
К методам внепечной обработки стали может быть отнесен всякий способ воздействия на расплав, прямо или косвенно обеспечивающий изменениеего физических или химических параметров, положительно влияющих на качество металла на любой стадии технологического процесса с момента начала его выпуска из плавильного агрегата до момента окончания разливки.
Рис.1. Классификация способов внепечной обработки стали
Существующие способы внеагрегатного воздействия на сталь в зависимости и от поставленных целей условно можно разделить на пять групп . К первой группе относятся способы обработки вакуумом, предназначенные для снижения содержания газов в металле. Способы дегазациистали постоянно совершенствуются и развиваются. В настоящее время получили распространение способы ковшового, порционного, циркуляционного, и струйного вакуумирования.
При ковшовом рафинировании разливочный ковш с жидкой сталью устанавливается в вакуумную камеру, в которой создается разрежение, способствующее удалению газов из расплава. Для интенсификации процесса дегазации во время вакуумирования металл продувают аргоном через пористую пробку, установленную в днище ковша. Схема установки ковшового рафинирования показана на рис. 2, а.
Рис. 2. Схемы основных способов вакуумирования стали:
а - ковшового; б - порционного; в - пульсационного; г - циркуляционного; д - струйного; е - непрерывного при разливке стали на МНЛЗ
Процесс порционного вакуумирования осуществляют в разливочном ковше с использованием вакуумной камеры, в которую через погружной патрубок засасывается порция металла, после чего камера периодически поднимается с таким расчетом, чтобы нижний конец патрубка оставался ниже уровня стали, как это показано на рис. 2, б. Затем металл сливается В ковш, а в камеру засасывается очередная порция жидкой стали, подвергаемая обработке.
К одной из разновидностей порционного вакуумирования может быть отнесен разработанный в Японии метод пульсационного перемешивания, схематично представленный на рис. 2, в. Осуществляется поочередное включение и отключение подачи аргона в полость погружаемой в жидкую сталь огнеупорной трубы и вакуумного насоса, обеспечивающего откачку из нее газа с интенсивностью примерно 10 м3/мин. При этом жидкий металл в полости трубы, а следовательно, и в ковше начинает интенсивно пульсировать, в результате чего повышается степень его рафинирования [50].
Для реализации процесса циркуляционного вакуумирования камеру снабжают двумя погружаемыми патрубками. По одному из них в момент создания разрежения в камеру подается аргон, поэтому плотность металла, находящегося в данном патрубке, снижается, что способствует подъему стали в полость трубы, где происходит ее дегазация. Затем по сливному патрубку обработанная сталь возвращается в разливочный ковш, вследствие чего возбуждается циркуляция стали (рис. 2, г).
Струйное вакуумирование осуществляется в процессе перелива или разливки металла. При этом обработке вакуумом подвергается струя стали, переливаемой из ковша в ковш или из ковша в изложницу. В обоих случаях металлоприемник располагается в вакуумной камере (рис. 2, д).
Известно промышленное опробование метода непрерывного вакуумирования при разливке стали на МНЛЗ. Вакуумную дегазацию струи стали осуществляют в проточной камере, которую размещают между сталеразливочным и промежуточным ковшами (рис. 2, е). Этот метод позволяет одновременно осуществлять дегазацию и защиту стали от вторичного окисления, что следует отнести к его достоинствам.
Вторую группу составляют процессы, обеспечивающие интенсивное перемешивание жидкого металла в ковше за счет использования энергии сжатого газа, вводимого в расплав различными способами. Данный вид обработки стали применяют, в первую очередь, с целью усреднения ее температуры и химического состава перед последующей разливкой.
Наибольшее распространение на металлургических предприятиях получили способы перемешивания стали с помощью таких продувочных устройств, как погружаемые фурмы, пористые пробки, устанавливаемые в днище ковша, и приспособления, подающие газ через разливочный канал ковшового затвора [119].
Рис. 3. Способы перемешивания жидкой стали.
Указанные способы инжекции газа в расплав схематично показаны на рис. 3, а-в. Любой из представленных методов ввода рафинирующего газа имеет свои достоинства и недостатки, проявляющиеся в разной степени в зависимости от конкретных условий их применения: вместимости сталеразливочного ковша, конструкции устройств для дозированного выпуска металла, которыми оборудован ковш и т. д.
К альтернативным методам интенсификации массообменных процессов в ковшах следует отнести способы газлифтного и пульсационного перемешивания, разработанные сотрудниками Донецкого политехническогоинститута (ныне ДонНТУ) под руководством В. И. Мачикина.
Газлифтное перемешивание (рис. 3, г) основано на направленной циркуляции металла в специальной футерованной огнеупорным кирпичом
камере, снабженной всасывающим и сливным патрубками. При подаче газа во всасывающий патрубок, погруженный в жидкий металл, образуется газожидкостная смесь, кажущаяся плотность которой значительно меньше плотности расплава, в результате чего уровень двухфазной смеси в камере начинает подниматься. В момент достижения смесью уровня сливного отверстия в верхней части камеры, когда газометаллическая смесь начнет сливаться в ковш, происходит направленная циркуляция жидкого металла, способствующая снижению колебаний его химического состава и градиента температуры в объеме перемешиваемой ванны [49].
В отличие от зарубежного аналога разработанный в ДонНТУ способ пульсационного перемешивания, принципиальная схема которого показана на рис. 3, д, предусматривает заполнение полости огнеупорной трубы (колонны) расплавом и периодическое его вытеснение в глубь ковша нейтральным газом, подаваемым под избыточным давлением. Эффективность данного метода значительно повышается при обеспечении согласования собственных частот колебания металла в системе колонна-ковш и собственных частот упругих колебаний газометаллического столба [50, 87].
Указанные методы перемешивания жидкого металла успешно применяют и в сочетании с другими видами внепечной обработки, входящими в третью группу, которая объединяет способы рафинирования стали с помощью специально приготовленных шлакообразующих смесей, позволяющих снизить содержание в металле серы и кислорода [119].
В четвертую группу могут быть выделены способы обработки стали порошкообразными реагентами, вводимыми в металл с целью его дефосфорации, десульфурации, раскисления и легирования, а также науглероживания. Введение реагентов в металлическую ванну осуществляют вдуванием струей газа-носителя, "выстреливанием" капсул или подачей материала в виде проволоки.
Для осуществления технологии инжекционной обработки стали газопорошковыми смесями необходимы устройства, обеспечивающие дозирование, устойчивую транспортировку и ввод порошкообразных реагентов в жидкий металл. Наиболее целесообразно для этих целей использование погружных и донных фурм, посредством трубопроводов связанных с аэрационными питателями (рис. 4, а).
Рис. 4. Схема ввода порошкообразных реагентов в жидкую сталь при обработке в разливочном ковше
Поскольку многие порошкообразные материалы взрывоопасны, то при их использовании необходимо применение особых мер предосторожности. По этой причине для подачи в расплав высокоактивных порошков в настоящее время применяют либо специальные пневматические устройства, "выстреливающие" в металл капсулы в виде цилиндров массой до 0,8 кг, изготовленные из соответствующих материалов, либо начиненную ими стальную проволоку. Для ввода проволоки в расплав с расчетной скоростью разработаны трайб-аппараты, снабженные подающими роликами, вращаемыми электромеханическим или пневматическим приводом (рис. 4, б).
Пятая группа объединяет способы модифицирования, микролегирования и инокулирования стали, предполагающие дозированный ввод в нее лигатур или модификаторов во время разливки [25, 98, 148].
Подачу необходимых компонентов в изложницу или центровую Осуществляют с помощью стационарных установок, размещенных на разливочной площадке (рис. 5, а), либо с использованием навесных устройств, устанавливаемых на время разливки на корпус ковша как показанона рис. 5, б.
Наряду с рассмотренными способами воздействия на жидкий металл в настоящее время применяют такие дополнительные меры, как отсечка конечногошлака во время выпуска плавки и защита стали от вторичного окисленияв процессе разливки.
При наличии в ковше большого количества высокоокисленного шлака резко увеличиваются потери раскислителей и лигатур из-за их угара, но и растет интенсивность разрушения ''шлакового пояса" футеровки ковша. В связи с этим ведут поиск эффективных решений проблемы отсечки конечного шлака при выпуске стали из плавильных печей и конвертеров. С этой целью предложено использовать специальные конструкции желобов, отводящих шлак в чашу во время схода металла из мартеновской печи в разливочный ковш [102, 108], или отсечных элементов поплавкового типа, вводимых в ванну кислородного конвертера и блокирующих его выпускной канал при подходе к нему слоя шлакового расплава.
Заметное влияние на качественные показатели получаемой металлопродукции оказывают газогидродинамические явления, происходящие во время разливки при взаимодействии истекающей из ковша струи металла с окружающей атмосферой.
В настоящее время для устранения негативного воздействия кислорода воздуха на разливаемый металл применяют различные способы экранирования струи, включающие использование специальных огнеупорных труб или создание кольцевой газовой завесы [132].
Рис. 5. Устройства для подачи сыпучих материалов под струю разливаемой в изложницы стали: 1- ковш; 2 - центровая; 3 - дозатор