Рафинирование металлов и сплавов методом электронно-лучевой плавки
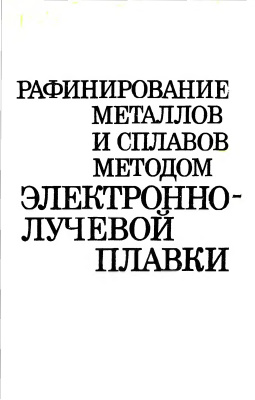
Тихоновский А.Л., Тур А.А.
Наукова думка, Киев, 1984 г.
Общим требованием к способам ЭЛП является обеспечение наиболее полного использования электронного луча как легко регулируемого и управляемого источника нагрева для рафинирования металлов и сплавов. Поэтому совершенствование технологии ЭЛП осуществляется непрерывно по мере создания более мощных и надежных пушек, блоков питания, вакуумных агрегатов и накоплением данных о физико-химических процессах вакуумного рафинирования.
В настоящее время наиболее широкое промышленное применение получила технологическая схема переплава твердой заготовки в кристаллизатор. В зависимости от типа и количества электронных пушек способы ЭЛП в кристаллизатор могут реализоваться по различным вариантам (см. рис. 1). Причем из представленных на рис. 1 вариантов только два первых принципиально отличаются от остальных, так как они реализованы с помощью электронных пушек без ускоряющего анода. При плавке пушками без ускоряющего анода (см. рис. 1, а) кольцевой катод располагается над верхним уровнем кристаллизатора, в котором формируется слиток. С помощью фокусирующих экранов электронные лучи делятся на две части: одна — для нагрева расходуемой (переплавляемой) заготовки, а вторая — для нагрева поверхности жидкой ванны в кристаллизаторе. Расходуемую заготовку опускают в зону плавки вертикально с помощью подающего механизма. Под влиянием бомбардировки ускоренными электронами осуществляются нагрев и плавление нижнего торца расходуемой заготовки, а расплавленный металл при этом стекает в водоохлаждаемый медный кристаллизатор, где создается жидкая ванна, подогреваемая отклоненной частью электронного луча. По мере сплавления расходуемой заготовки осуществляют вытягивание слитка со скоростью, обеспечивающей поддержание постоянного уровня жидкой ванны в кристаллизаторе. Основной недостаток этого способа плавки заключается в наличии ускоряющего электрического поля непосредственно у нагреваемой поверхности. Пары металлов, газы и брызги, образующиеся в этом пространстве, вызывают электрические разряды и изменяют тепловой режим плавки. Это приводит к возникновению непроплавов, слоистой химической и структурной неоднородности в слитке, некачественной поверхности. Поэтому качественные слитки часто получают двойным и даже тройным переплавом. Когда переплавляемая заготовка содержит значительное количество газообразных примесей, затрудняющих осуществление стабильного процесса плавки, применяют две электрически раздельные кольцевые пушки (см. рис. 1,6). При этом первая пушка плавит заготовку, а вторая поддерживает ванну в кристаллизаторе [1661. Подобное решение значительно усложняет электрическую схему питания пушек и не устраняет полностью отмеченных технологических недостатков.
Недолговечность службы катода, невозможность плавить одной и той же пушкой в кристаллизаторы разного диаметра и нестабильность технологического процесса плавки с помощью кольцевых пушек без ускоряющего анода послужили основой для изыскания новых, более приемлемых решений.
В ГДР под руководством М. Арденне разработана схема плавки с помощью одной вертикально расположенной аксиальной пушки, боковой подачи переплавляемой заготовки и развертки достаточно сфокусированного электронного луча по поверхности жидкой ванны в кристаллизаторе (см. рис. 1, е) [129].
Плавка с помощью нескольких аксиальных пушек, вертикальной подачей переплавляемой заготовки и электромагнитным отклонением лучей разработана западногерманской фирмой «Лейбольд— Гереус» (см. рис. 1, ж) [25, 140].
В ИЭС им. Е. О. Патона АН УССР разработан способ ЭЛП с помощью многопушечного радиального электроннолучевого нагревателя, вертикальной подачей переплавляемой заготовки со сканированием пучков по нагреваемой поверхности (см. рис. 1, з) [70, 72].
Американская фирма «Стауфер — Темескал» предложила способ плавки с помощью нескольких пушек с линейными лучами, отклоненными на 180° и более, и вертикальной подачей переплавляемой заготовки (см. рис. 1, и) [175]. Последние три способа (см. рис. 1, ж—и) переплава расходуемой заготовки, по-существу, равноценны. Различия их состоят только в применении разных систем электронных пушек.
Промежуточное место занимают способы плавки с помощью кольцевых пушек с ускоряющим анодом (см. рис. 1, в—д). Первый способ (см. рис. 1,в) может иметь лишь ограниченное применение, так как не позволяет изменять конфигурацию зоны нагрева без замены пушки, что очень важно при переходе от одного кристаллизатора к другому. Второй способ (см. рис. 1, г) позволяет в некоторых ограниченных пределах изменять конфигурацию зоны нагрева с помощью электромагнитов, но он может применяться только в сочетании с боковой подачей заготовки. Компромиссное решение для пушек рассматриваемого типа реализовано в технологической схеме мегаваттной печи [981, где три кольцевые пушки с ускоряющим анодом установлены над кристаллизатором вокруг вертикально подаваемой заготовки (см. рис. I, 5).В этом случае конфигурацию зоны нагрева можно изменять наклоном отдельных пушек.
Применение пушек с ускоряющим анодом позволяет осуществить плавку в пространстве, свободном от электрического поля. Эта отличительная особенность наряду с раздельной от полости плавки откачкой из полости пушки (см. рис. 1, е) или объединенного пространства, в котором расположены пушки (см. рис. 1, ж, з),а также отклонение луча позволяет свести к минимуму возможность электрических разрядов в системе катод — анод в процессе плавки. Одновременно значительно увеличивается долговечность катодов, уменьшается вероятность прерывания процесса плавки при выходе из строя части пушек.
Стабилизация теплового режима при отсутствии высоковольтных разрядов увеличивает химическую и структурную однородность слитка, позволяет получить более качественную поверхность слитка и упрощает управление процессом плавки.
При сопоставлении технологических схем, приведенных на рис. 1, следует отметить некоторое их различие с точки зрения физико-химического воздействия на переплавляемый металл и в первую очередь на условия нагрева и величину реакционной поверхности жидкой фазы.
Как отмечалось, плавка с помощью одной аксиальной пушки и разверткой луча происходит в динамическом, периодически повторяющемся тепловом режиме, а условия плавки несколькими пушками, особенное недостаточно сфокусированными лучами, приближаются к стационарным [60, 61, 137, 1601.
При динамическом нагреве электронный луч определенного сечения и плотности энергии перемещается по поверхности жидкой ванны в соответствии с круговой, спиральной или более сложной разверткой. В этих условиях каждая точка поверхности жидкой ванны подвергается действию периодических тепловых импульсов, частота и длительность которых зависят от частоты и траектории развертки электронного пучка и от диаметра фокального пятна (следа луча на поверхности ванны).
При стационарных условиях нагрева пространственное положение электронного потока остается практически неизменным в процессе плавки. Электроны относительно равномерно бомбардируют поверхность ванны.
Для обеспечения наилучших условий рафинирования следует максимально развивать реакционную поверхность, создавая наиболее оптимальный перегрев металла. При динамическом нагреве с относительно небольшой скоростью движения луча по поверхности жидкой ванны могут возникнуть нерационально высокий перегрев в перемещающемся фокальном пятне и, как следствие, повышенные потери металла в результате испарения. Одновременно могут ухудшаться условия рафинирования вследствие уменьшения эффективной реакционной поверхности и нивелирующего эффекта в зоне фокального пятна.
Более развитая поверхность и более выгодные условия рафинирования создаются при вертикальной подаче переплавляемой заготовки по сравнению с горизонтальной. При вертикальной подаче оплавляемый торец расходуемой заготовки, как правило, принимает форму конуса и стекание металла происходит вдоль образующей конуса, что значительно увеличивает реакционную поверхность.
При плавке с помощью одной аксиальной пушки и горизонтальной или наклонной подачей переплавляемой заготовки на
поверхности жидкой ванны в кристаллизаторе образуется область с пониженной плотностью энергии — «энергетическая тень» от переплавляемой заготовки, которая отрицательно влияет на структурную и химическую однородность слитка.
Разновидностью технологических схем плавки в кристаллизатор является переплав сыпучей шихты (порошка, гранул, губки, стружки и т. п.), а также скрапа (отходов металлургического прокатного, прессового и кузнечного производства.
Переплав сыпучей шихты обычно применяется для получения компактного слитка, который затем подвергается повторному переплаву по одной из схем, показанных на рис. 1, или другими способами специальной электрометаллургии. В работе [142] отмечается, что способ компактирования скрапа в электр он но-лучевой печи позволяет получить высокие показатели. Например, при переработке титанового скрапа достигается производительность 10 000кг/(ч *м2) при удельном расходе электроэнергии 1,44 МДж/кг. Для стали соответствующие показатели равны 17 000кг/(ч *м2) и 1,08 МДж/кг.
В настоящее время разрабатываются технологические схемы ЭЛП, позволяющие более полно использовать преимущества электронного луча как источника нагрева. Независимость нагрева от процесса плавления и возможность регулирования параметров нагрева в широких пределах позволяют С применением электронно-лучевых пушек создавать технологические схемы, в которых плавление, рафинирование и кристаллизация осуществляются раздельно. Это существенно расширяет технологические возможности ЭЛП.
На рис. б показаны варианты способа плавки с промежуточной емкостью. При плавке в соответствии с рис. 5, а, жидкий металл с переплавляемой заготовки поступает в водоохлаждаемую промежуточную емкость, а затем в кристаллизатор. Заданный температурный режим в промежуточной емкости и кристаллизаторе обеспечивают автономные пушки. С применением промежуточной емкости можно осуществить параллельную разливку металла в несколько кристаллизаторов (рис. 5, б) и легирование металла летучими элементами по ходу плавки (рис. 5, в), при этом в камере формирования слитка, в которой осуществляют присадку легирующего компонента, вакуум составляет 1,3 • 10-1 Па.
В США создан и опробован в промышленных условиях способ холодноподового электронно-лучевого рафинирования исходного жидкого металла (рис. 6) 1133, 135, 144]. Этот способ предусматривает рафинирование жидкого металла в процессе течения его по каскаду из пяти медных водоохлаждаемых желобов и формирование слитков в кристаллизаторе скольжения. Жидкое состояние и необходимый перегрев металла поддерживаются электронно-лучевыми пушками со сканирующим лучом.
Существующие способы ЭЛП в кристаллизатор и с применением промежуточной емкости весьма ограничены по производительности. Скорость вытягивания слитка из кристаллизатора, обеспечивающая получение высокой однородности его по химическому составу и структуре, зависит от интервала кристаллизации сплава и условий отвода тепла от фронта кристаллизации. Обычно для сложнолегированных сплавов при диаметре кристаллизатора более 0,2—0,3 м она составляет несколько миллиметров в минуту. Поэтому наряду с совершенствованием способа вертикального формирования слитка, осуществляемого в современных электронно-лучевых установках, в настоящее время предложены способы горизонтальной отливки слитков, расширяющие возможности ЭЛП по производительности оборудования и качеству получаемых слитков.
На рис. 7 показана установка для получения монолитных и многослойных литых слябов, разработанная в ИЭС им. Е. О. Патона АН УССР [86]. За счет увеличения площади зеркала жидкого металла при горизонтальной отливке можно достичь значительно большей производительности, чем при формировании слитков традиционным способом по методу полунепрерывной разливки жидкого металла.
Большим преимуществом горизонтальной отливки является получение слитков, которые могут поступать в прокатку, минуя обжимные станы. Причем слиток-сляб не требует механической обработки перед прокаткой, так как верх его имеет зеркальную поверхность, а низ при необходимости может быть оплавлен электронными пучками сразу же после сформирования слитка. Методом горизонтальной отливки можно получать заготовки различной формы и конфигурации (диски, кольца, фланцы, плиты), отличающиеся высокой чистотой, химической и структурной однородностью. Эти заготовки могут быть использованы в изделиях в литом или деформированном виде. Обычно горизонтальные слитки требуют значительно меньших обжатий для измельчения литой структуры, а прокат из них обладает небольшой анизотропией свойств как в продольном, так и в поперечном направлении.
Благодаря высокой производительности метод горизонтальной отливки слитков открывает неограниченные возможности
для формирования высококачественных слитков из исходного жидкого металла. При этом можно получать слитки большой массы с использованием нескольких порций жидкого металла. Наконец, этот метод позволяет получать новые конструкционные материалы (биметаллические, многослойные и армированные слитки) под последующую прокатку или для применения в изделиях в литом виде.
Электронно-лучевые источники нагрева применяются для гарнисажной плавки с последующим сливом жидкого металла в изложницу или фасонную форму (рис. 8) [118, 175]. Они имеют преимущества перед дуговым источником нагрева: можно более длительное время выдерживать расплав и перегревать его до более высокой температуры; нет необходимости изготавливать расходуемые электроды; меньше опасность прожигания гарнисажного тигля и более просто измерять температуру металла; можно осуществлять подогрев не только жидкой ванны, но и сливного носка и приемника формы при разливке и т. п.
В последнее время в СССР и за рубежом интенсивно разрабатывается новая электронно-лучевая технология производства конструкционных материалов, основанная на распылении в вакууме жидких сплавов и затвердевании их с большой скоростью в виде гранул или других частиц малых размеров с последующим компактированием в заготовки под деформацию и готовые детали. Перспективным направлением является также разработка способов ЭЛП для получения мерных заготовок под последующий профильный прокат (рис. 9) [76,104,118,175].